Introduction
Dynamic damper has been developed to reduce vibration and noise generated from automobile. The vibration and noise are generated mainly by automobile engine and road unevenness. Thus, a dynamic damper is used to improve feeling of riding at engine room, muffler, and steering wheel where the reduction of vibration is most necessary in an automobile.
The stiffness and degree of deformation should be considered as a material of dynamic damper because it reduces vibration with opposing power against moving matter. Therefore, the dynamic damper should show a function with minimum deformation and has initial damping property to minimize repulsion force.1 The dynamic damper consists of mass part and rubber spring and it is used to improve vibrational property in specific frequency range. In design of conventional steel dynamic damper used in automobile, rubber material is used for damping property and steel is used as a proper mass. Thus, the size of damper is increased and the design of damper is restricted because in some cases the mounting space of damper is small and not simple. In addition, the adhesion between rubber spring and mass part of dynamic damper is one of the factors affecting the performance of steel dynamic damper. If the proper adhesion is not ensured, the dynamic damper cannot reduce the vibration of large frequency resulting from resonance of main structure due to the difference in inherent frequency of main structure.
An elastomer is a proper material in the area that requires damping property. As a typical viscoelastic material, the elastic part of elastomer shows a 150 times greater energy storage property than that of steel, while a viscous part transfers kinetic energy to heat plays a role of vibration absorption.2-4 But the density of elastomer should be comparable to that of steel dynamic damper in order to substitute the conventional steel dynamic damper used in engine room or muffler of automobile. However, it is impossible to obtain the correspond density to steel dynamic damper using elastomer. The only way to obtain high density corresponds to steel dynamic damper is to attain high loading technology of filler having high density.
In this study, a tungsten powder was used as a filler to obtain ultra high density elastomer through high loading of it. However, the matrix rubber could not be cured by conventional vulcanizing system due to the high loading of filler.5 Thus, the problem can be solved by the chemical modification of matrix rubber for proper vulcanizing system. The particle size and structure of filler are also important factors to obtain high loading of filler. Although there are many studies about the mechanical properties of particulate composite,6-8 the main concern of the studies is about the effect of filler particle size and structure on the mechanical properties of composites.
The high loading technology of filler will be introduced in this study. From this, the ultra high density elastomer is introduced for substitution of the conventional steel dynamic damper. By using ultra high density elastomer, the freedom of damper design would be greatly improved due to improvement of damping property as well as reduction of damper size.
Experimental
The basic matrix for ultra high density elastomer is chloroprene rubber (CR, Denco Co., SHOPRENE®). Maleic an-hydride (MAH, Samchun Chem., Korea) was used for mechanochemical modification of CR using internal mixer. The MAH grafted CR (MAH-g-CR) was prepared throughout the modification reactions. The various amounts of MAH were mixed into CR after mastication of CR. The controlling factors for mixing process were the amounts of MAH and mixing temperature. After preparing MAH-g-CR, 50 mol% epoxidized natural rubber (ENR50, Malaysian Rubber Producers Research Association) was blended for curing of MAH-g-CR, which is called the self-curable rubber blend system in this study. Tungsten powder (Korea Tungsten) was used as a filler to get ultra high density elastomeric material. The average particle size and density of tungsten were 8.9 μm and 19.3 g/cm3, respectively. The basic rubber compounding was performed using 12 inches two roll mill. The rubber compounds were stored at room temperature for 24 hours. The ingredients are listed in Table 1.
Material | Source | phr |
---|---|---|
CR | DENKO | 100 |
ZnO | Han-Il Chemical | 10 |
Stearic Acid | Dong-San C&G | 1 |
Tungsten Powder | Korea Tungsten | 0, 150, 450, 750, 900 |
In order to attain self-curable rubber blend system, the mechanochemical modification of CR was performed by internal mixer. After mastication of CR the modification reaction was done for 2 minutes at 60 rpm. The amount of MAH varied from 2 to 14 phr and mixing temperatures were controlled by 80, 100, 120, 135 and 150°C. The optimum grafting condition of MAH was examined.
In this study, the mechanochemical modification by internal mixer only utilize shearing action and heat was called dynamic maleation. By comparing weight of specimen before and after soxhlet, the efficiency of modification reaction was examined. This could be done by measuring gel fraction according to equation (1). The gel fraction was obtained by measuring the weight before and after soxhlet maleated CR (MAH-g-CR).
w0; weight of specimen before soxhlet
w; weight of specimen after soxhlet
Blending of MAH-g-CR and ENR was performed by two roll mill and the tungsten powder was also incorporated during blending. The cure characteristics of rubber compound such as scorch time (ts2) and 90% cure time (t90) were measured by rubber rheometer (DaeKyung Engineering, Korea) at 180°C.
The optimum way to obtain ultra high density elastomeric material would be by using filler control technique. In this study, the tungsten powder is pretreated by ball mill (J-PM1-S, JISCO) to break the aggregates of filler. The density of MAH-g-CR/ENR containing tungsten powder was measured by gravimeter (Precisa, 202A SCS-DT) at room temperature. The density of MAH-g-CR/ENR containing 60 vol.% of tungsten powder was 7.57 g/cm3. The tensile test performed at the condition of 20 mm gauge length, 500 mm/min crosshead speed, and 24°C. The rebound resilience was measured by rebound resilience tester (Kunwha Engineering, Korea) using cylindrical specimen according to KSMISO 4662. The rebound resilience was measured by reading the rebound height of steel ball after dropping it onto the specimen at specified height. The loss energy, which cannot be restored, had been dissipated as heat and it was called hysteresis. The ratio of initial drop height and rebound height was recorded as tan δ.
Results and Discussion
The curing characteristics and physical properties of CR matrix containing up to 60 vol.% of tungsten powder were examined in previous study.9 According to the results, increase in loading amounts of tungsten powder resulted in an unstable curing characteristic and a reduction of physical property. This occurred because ZnO used as a curing agent for CR is absorbed at aggregates of tungsten powder which in turn affected the curing reaction of CR. Also, the dispersion of ZnO becomes difficult because the portion of matrix decreases with increasing filler loading. This problem can be solved by the chemical modification of CR matix.10-14
In this study, the mechanochemical modification of CR by internal mixer using shearing action and heat was done instead of general photochemical modification by UV, which is surface modification. Maleic anhydride (MAH) was used as a reactive monomer and the process was called dynamic maleation. From this process, the succinic anhydride (SAH) grafted onto CR and called to MAH-g-CR. As shown in Scheme 1,14 the MAH excited by shear force and heat of internal mixer grafted onto the main chain of CR in the form of SAH or succinic acid (SA). The efficiency of grafting was examined by the gel fraction analysis. The results according to the mixing temperature are shown in Figure 1. The optimum gel fraction was obtained at 100°C as the same as previous results9 that used photochemical modification of CR. It was thought that the unreacted monomer was removed by solvent during soxhlet at 80°C and the self-reacted MAH was removed over mixing temperature of 120°C. Similar results can be obtained in the case of MAH content. As shown in Figure 2, the optimum gel fraction could be obtained at 10 phr of MAH. Therefore, it was concluded that the optimum modification condition of dynamic maleation was 10 phr of MAH and mixing temperature of 100°C.
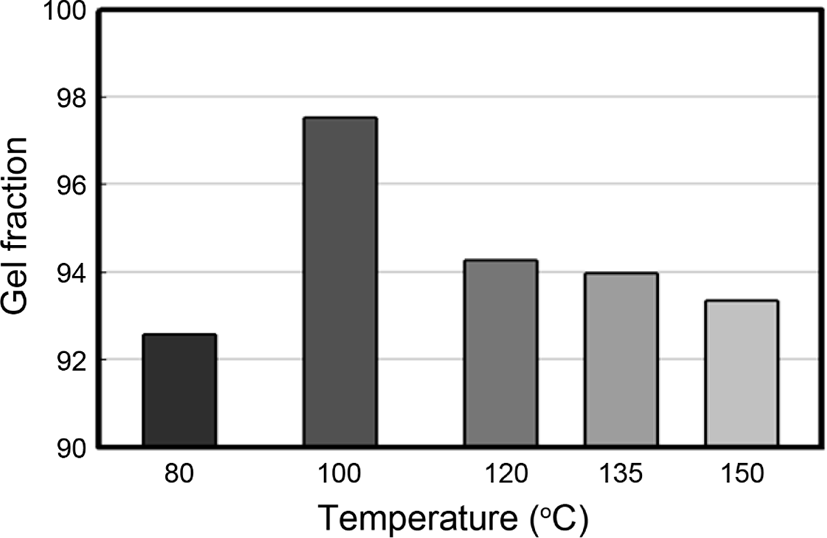
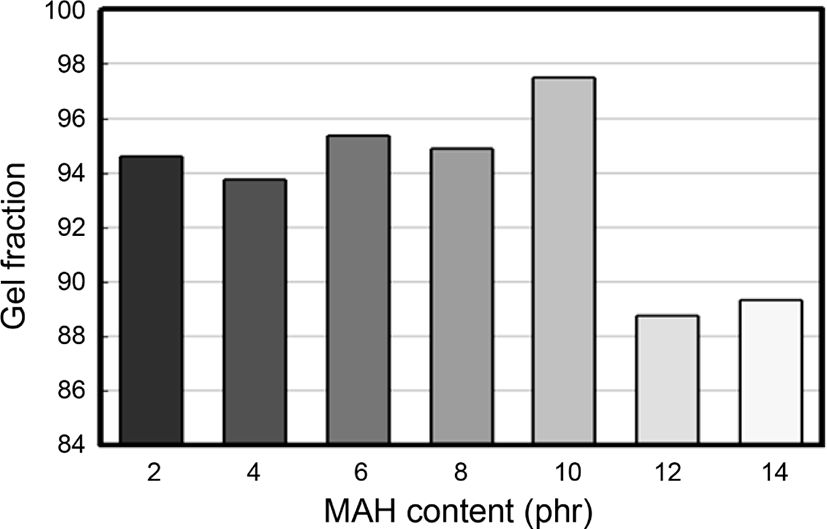
As mentioned in previous study,9 the CR compound containing high loading of tungsten powder showed inconsistent cure behavior due to poor dispersion of curing agent and adsorption of curing agent onto tungsten powder. Therefore, the new curing system is required for modified CR (MAH-g-CR) by dynamic maleation process. In this study, the epoxidized natural rubber (ENR) is used as a reactive blend for self-curable rubber blend system, which can be vulcanized without using a curing agent. The reaction mechanism is shown in Scheme 2.15 As shown in Scheme 2, the curing reaction takes place without a curing agent by the ring opening reaction of SAH grafted on MAH-g-CR and epoxide ring of ENR with heat and pressure of internal mixer.
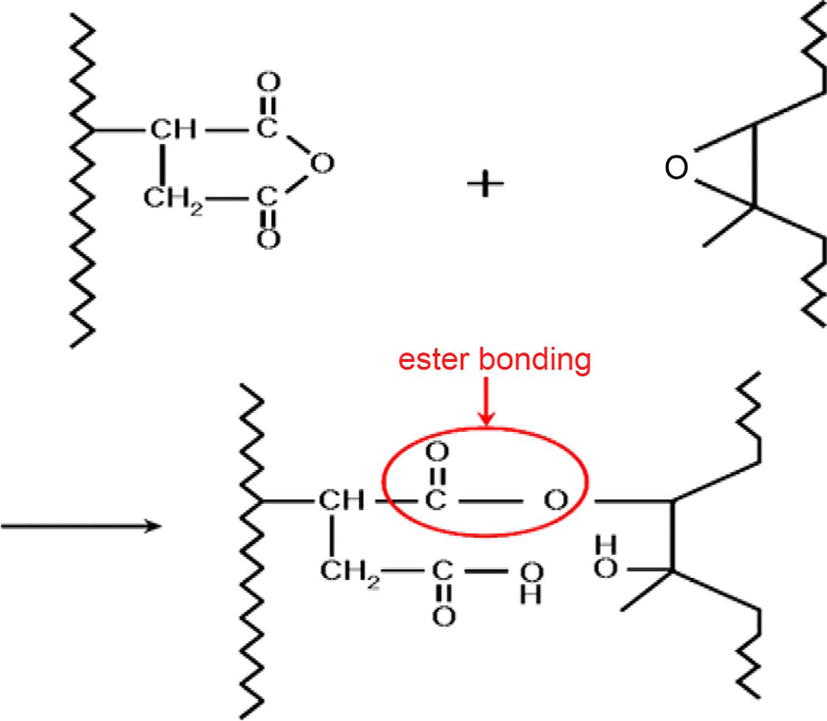
The curing characteristics of MAH-g-CR compound with the amounts of ENR are examined and the results are listed in Table 2. The curing temperature was adjusted to 180°C to speed up the curing rate. The maximum and minimum torque increased with increasing ENR contents and the difference between maximum and minimum torques also increased with the ENR contents as shown in Table 2. The cure rate index passed through the maximum at 30 wt.% of ENR content. It was thought that the curing rate became decrease if ENR contents increased over 30 wt.% because unreacted epoxy group of ENR reacted with the portion of CR in which SAH was not grafted. Therefore, it is thought that the 30 wt.% blending of ENR is optimum blending amount because it can provide proper scorch time and fast curing time.
The curing characteristics of MAH-g-CR compound containing 30 wt.% of ENR with the amounts of tungsten powder were examined and the results are listed in Table 3. As shown in Table 3, CRI decreased with the addition of tungsten powder due to decrease of the total amounts of rubber matrix. However, CRI increased with increasing the loading amounts of tungsten powder, while the ts2 did not change greatly as shown in Table 3. Thus, the premature curing problem is no longer considering factor caused by increase of thermal conductivity with incorporation of tungsten powder. The phenomena of increase of CRI with the amounts of tungsten powder is desirable thing in terms of manufacturing dynamic damper by self-curable rubber blend system.
The tensile strength of CR vulcanizate decreased with the addition of tungsten powder according to the previous re-sults.9 The reason is why the agglomeration of tungsten powder resulted from decrease of relative CR matrix portion by increasing tungsten loading rates. Also, improper curing of CR by poor dispersion of ZnO, used as a curing agent for CR, was an another factor affecting tensile strength of CR vulcanizate. In addition to above reasons, the weak interfacial adhesion between CR matrix and tungsten powder would be a factor affecting mechanical property of CR vulcanizate.
The self-curable rubber blend system was proposed in this study in order to solve the problem of decrease of mechanical properties of CR vulcanizate by incorporating the tungsten powder. The tensile property of MAH-g-CR/ENR blend by self-curable rubber blend system with the amounts of tungsten powder is shown in Figure 3. In contrast with the previous results, the tensile strength of MAH-g-CR/ENR matrix increased with increasing the contents of tungsten powder, while the elongation decreased slightly with the contents of tungsten powder. The MAH-g-CR/ENR matrix was vulcanized by ester bonding without using curing agent and accelerator. It was thought that the curing reaction of MAH-g-CR/ENR was proceeded constantly via ester bonding when the small difference of tensile strength with the contents of tungsten powder was considered. Thus, it was found that this system would be a stable curing system for high loading of tungsten powder. The elongation at break decreased slightly by increasing the content of tungsten powder. The reason could be attributed to the decrease of elastomeric matrix, increase of contact area between matrix and filler, and moving restriction of rubber chain occuluded at void space of filler aggregates.
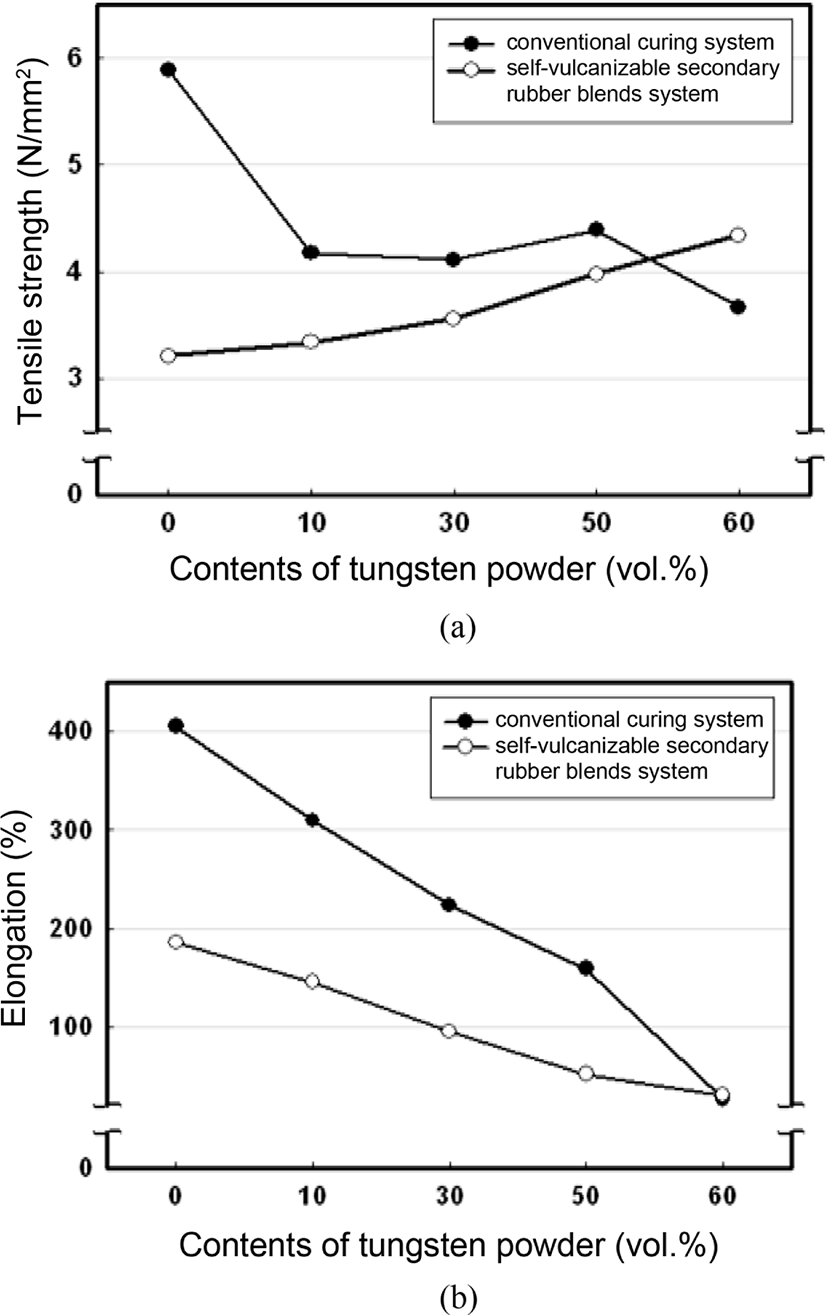
The damping property of MAH-g-CR/ENR system with the content of tungsten powder was measured and shown in Figure 4. The viscoelastic property of elastomeric matrix would be changed by the addition of filler. As shown in Figure 4, the resilience of MAH-g-CR/ENR matrix decreased with the contents of tungsten powder, while the tan δ increased. If the loading amount of tungsten powder is increased, the rubber fraction of system is decreased. Also, the resilience will be decreased as the occuluded rubber occuluded into void space of tungsten particles is increased and motion of rubber chain occuluded into void space is restricted. Both systems of the conventional cure system and MAH-g-CR/ENR system showed initial damping properties. But the MAH-g-CR/ENR system showed increase of modulus as well as initial damping property with the amounts of tungsten powder. As mentioned before, the damper should minimize rebound force with maintaining the minimum deformation about applied impact. From this point of view, the MAH-g-CR/ENR system will be used substituting material for steel dynamic damper because it has initial damping property as well as stiffness.
Conclusion
The self-curable rubber blend system was studied to obtain ultra high density elastomer using tungsten powder as substitution for steel dynamic damper. The mechanochemical modification of CR using MAH by internal mixer was performed and the optimum modification conditions were 10 phr of MAH and 100°C of mixing temperature. The MAH modified CR was cured by ENR and the optimum amounts of ENR was 30 wt.%. The self-curable rubber blend system showed stable cure behavior even though the tungsten powder was loaded up to 60 vol.%, which showed density of 7.57 g/cm3. Also, the MAH-g-CR/ENR system showed better damping property than that of conventional cure system. The substitution for steel dynamic damper will be possible because the density of the MAH-g-CR/ENR containing 60 vol.% of tungsten powder was close to the density of steel. If the high loading over 60 vol.% of tungsten powder throughout the study of filler geometry control is possible, the degree of design freedom of damper will be improved and the adhesion problem between steel and rubber will be solved because steel is not needed for dynamic damper.