Introduction
고무의 마모 특성은 고무제품의 사용 수명에 직접적인 영향을 미치기 때문에 매우 중요한 특성 중 하나이며, 마찰 및 마모 조건에 노출되어 사용되는 타이어와 신발 등의 산업에서는 가장 중요한 요소 중의 하나로 인식되고 있다. 고무의 마모는 고무와 접촉면 사이에 작용하는 마찰력에 의해 고무가 떨어져 나가는 현상으로 고무의 종류, 접촉면의 거칠기 및 상태, 주변 환경의 온도, 습도 등 다양한 인자들에 따라 달라진다.1,2 이러한 마모특성 메커니즘을 규명하기 위해 Schallamach,3-5 Grosch,6,7 Gent,8-10 Thomas11,12 등에 의해 많은 연구가 진행되어왔다. 고무의 마모성능 평가 시험은 마찰 및 마모를 일으키는 도구로 칼날을 이용하는 칼날형, 연마석을 이용하는 아크론형 및 람본형, 그리고 탄화규소로 처리된 드럼을 이용하는 DIN형 등 다양한 실험방법들이 사용되고 있다.13 칼날형 마모시험기의 경우, 회전하는 고무시편에 칼날을 압착하여 마모를 유발시키며 손실된 고무량의 측정과10 손실된 높이를 측정하는 방법2이 있다. 이와 같은 칼날형 마모시험법은 고무와 마찰하면서 칼날의 날카로운 정도가 달라지기 때문에 평가결과의 재현성이 낮은 단점이 있다. 또한 고무의 종류에도 영향을 받는 것으로 알려져 있다.
본 연구에서는 마모가 진행되는 동안 가해지는 마찰에너지의 측정이 가능한 칼날형 마모시험기를 이용하여 3종류의 서로 다른 칼날재질인 steel (SB), Ti-coated tungsten carbide (TiB), 그리고 zirconia (ZB)로 제조된 칼날을 이용하여 대표적인 합성고무인 SBR과 BR 컴파운드의 마모특성을 평가하였다.
Experimental
Styrene-butadiene rubber (SBR)은 금호석유화학의 SOL 6361H (styrene 함량: 33 wt%, vinyl 함량: 58 wt%), butadiene rubber (BR)은 금호석유화학 KBR 01 (cis-1,4 함량: 96 wt% 이상)을 사용하였고, 가교제로는 황을 가교활성제로는 산화아연(ZnO)과 스테아르산(Stearic acid), 가교촉진제로는 N-tert-butyl benzothiazol-2 sulfenamide (NS)를 사용하였다. 추가적으로 산화방지제로는 poly(1,2-dihydro-2,2,4-trimethyl-quinoline) (RD)를 사용하였다. 마모 실험에 사용된 3종의 칼날로는 steel 칼날(Peace utility, Korea)과 Ti-coated tungsten carbide 칼날(BTL-3P, NT Cutter, Japan), 그리고 zirconia 칼날(sdf5, Ruifengli Blade Manufacturing Co. Ltd., China)이며, 각각 SB, TiB, ZB로 명명하였다.
밴버리 믹서(Banbury mixer, ㈜남양기업, Korea)를 이용하여 150°C, 50 rpm 조건에서 고무와 가교활성제, 산화방지제를 Table 1에 나타낸 함량에 따라 차례로 첨가하여 6분동안 혼련하였다. 이축밀(DS-1500R, WITHLAB Co. Ltd., Korea)을 이용하여 가교 촉진제와 가교제를 넣고 10분 동안 추가 혼련하여 최종 컴파운드를 제조하였다. 가교 레오미터를 이용하여 적정 가교시간을 측정하고, 유압식 프레스(CMV50H-15-CLPX, Carver, Inc., USA)를 이용하여 170°C, 25 ton으로 가압하여 가교시편을 제조하였다. 사용된 시편은 실린더 모양이며, 마모가 진행되는 동안 발생하는 마찰열의 방출을 원활하게 하기 위해 중앙이 비워진 형태로 제작하였다. 시편의 규격은 Figure 1에 나타내었다.
Ingredients | |||||
---|---|---|---|---|---|
Rubber (SBR, BR) | ZnO | Stearic acid | aRD | bNS | S |
100 | 3 | 1 | 1 | 1 | 2 |
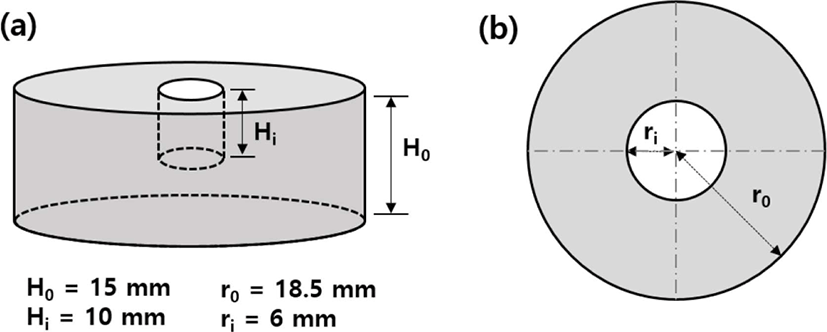
본 실험에 사용된 칼날형 마모시험기의 모식도를 Figure 2에 나타내었다. 칼날 연결 축에 추를 매달아 시편에 하중을 가해주고, 축을 일정한 속도로 회전시키면서 마모를 유발시키는 구조로 되어있다. 칼날의 회전속도는 10 rpm, 온도는 30°C, 하중은 0.5~2.5 kg 범위에서 마모실험을 진행하였다. 시편 표면에 일정한 마모패턴이 형성되고 토크 값이 일정하게 유지될 때까지 예비 마모를 진행한 후 본 마모실험을 진행하였다. 매 6,000회에 새로운 칼날로 교체하여 마모속도를 관찰하였다. 시편 표면에 가해지는 마찰 토크, M은 회전축에 부착된 토크센서를 통해 측정하였고, 마모가 진행되는 동안 마찰힘 F은 식 (1)을 통해 계산하였다(Figure 2).
여기서 rm은 시편의 평균 반경을 나타낸다. 평균마찰계수, μ와 마찰에너지, Wf은 각각 식 (2)와 (3)을 통해 구하였다.
여기서 N 은 시편에 가해준 수직하중을 나타낸다.
여기서 r0는 시편의 바깥쪽 반경, 그리고 ri 는 시편의 안쪽 반경을 나타낸다. 고무의 마모속도, Rh 는 마모가 진행됨에 따라 칼날이 앞으로 이동한 거리 L 을 회전수 n 으로 나누어 단위회전당 높이손실로 식 (4)와 같이 나타내었다.
Results and Discussion
칼날재질이 고무의 마모속도에 미치는 영향을 알아보기 위해 소재가 다른 steel (SB), Ti-coated tungten carbide (TiB), zirconia (ZB) 3종류의 칼날을 사용하였다(Figure 3). 칼날 단면을 FE-SEM으로 관찰한 결과를 Figure 4에 나타내었다. SB는 대칭구조로 나타났고, TiB와 ZB는 비대칭 구조로 나타났으며, 칼날의 각도는 약 30° 로 나타냈다. 따라서 본 연구에 사용된 3종류의 칼날의 초기 예리도(Sharpness)는 유사한 수준으로 칼날 예리도에 의한 고무의 마모속도의 영향은 크지 않을 것으로 판단되었다.
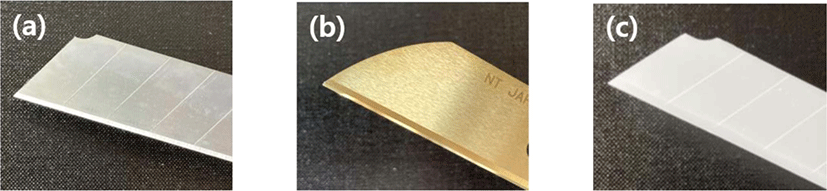
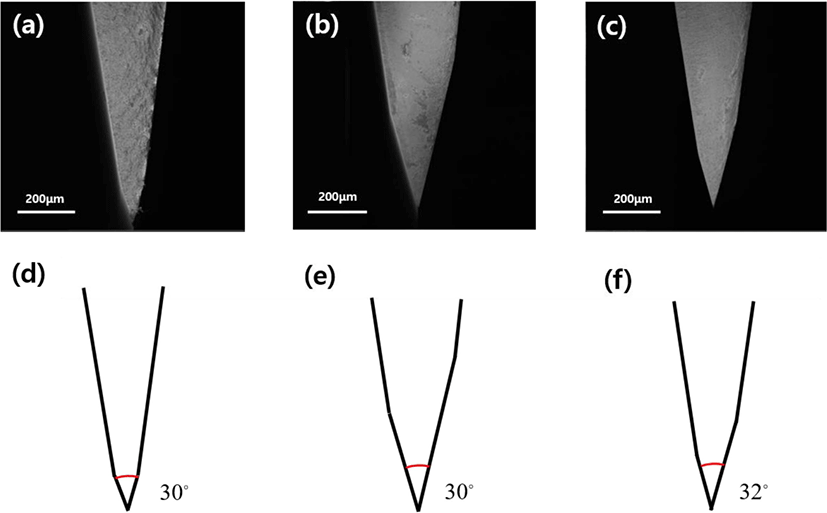
Figure 5에는 SBR 고무에 대한 회전수에 따른 마모된 길이(L)와 이를 회전수로 나눈 값으로 표현되는 마모속도(Rh)를 도시하였다. SB의 경우 회전수가 증가함에 따라 마모속도가 매우 급격하게 하락하는 결과를 보여주고 있고, 6,000회 이후에 새로운 칼날로 교체할 경우 다시 높은 마모속도로 회복한 후 다시 감소하는 경향을 보였다(Figure 5b). 반면 ZB의 경우 초기 마모속도가 둔화되는 정도가 현저히 감소하는 경향을 보였고(Figure 5f), TiB의 경우는 중간 정도의 경향을 보였다(Figure 5d). 이는 칼날의 재질에 따라서 상대 고무의 마모속도는 크게 영향을 받는 것을 의미한다. 이러한 영향을 보다 자세히 설명하기위해 3종류의 칼날을 마모 전후에 FE-SEM으로 관찰하여 Figure 6에 나타내었다. 3종류의 칼날의 초기 예리도는 2.3~2.6 μm로 유사하게 평가되었으나 SBR 고무에 6,000회 회전시킨 후, SB와 TiB의 경우 예리도가 약 2배 낮아진 결과를 보인 반면 ZB의 경우는 거의 초기 예리도를 유지하는 경향을 보이고 있다. 이러한 결과로 미루어 SB 및 TiB의 경우 회전수 증가에 따른 마모속도 하락은 칼날이 무뎌지기 때문에 기인된 것으로 해석된다. ZB의 경우는 SBR 고무에 의해 칼날의 예리도를 유지하는 것으로 나타났다. 이러한 결과는 마모진행동안 SBR 고무사슬이 절단되면서 발생하는 자유라디칼은 비교적 안정적이어서 다른 고무분자와의 반응대신 칼날과의 반응에 참여하기 때문에 나타난 경향의 차이로 해석된다.14 즉, SB와 TiB는 SBR 자유라디칼과의 산화반응이 용이하여 칼날의 예리도를 둔화시킨 반면, ZB의 경우 무기물이기 때문에 자유라디칼과의 반응이 어려우므로 초기 예리도를 유지할 수 있었을 것으로 판단된다.
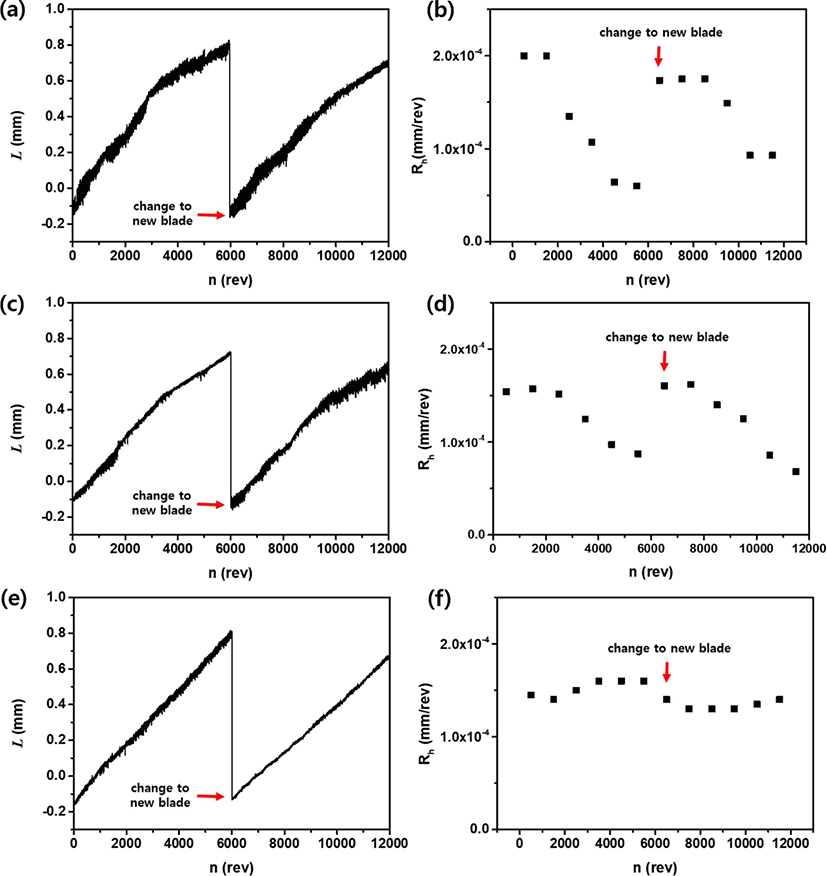
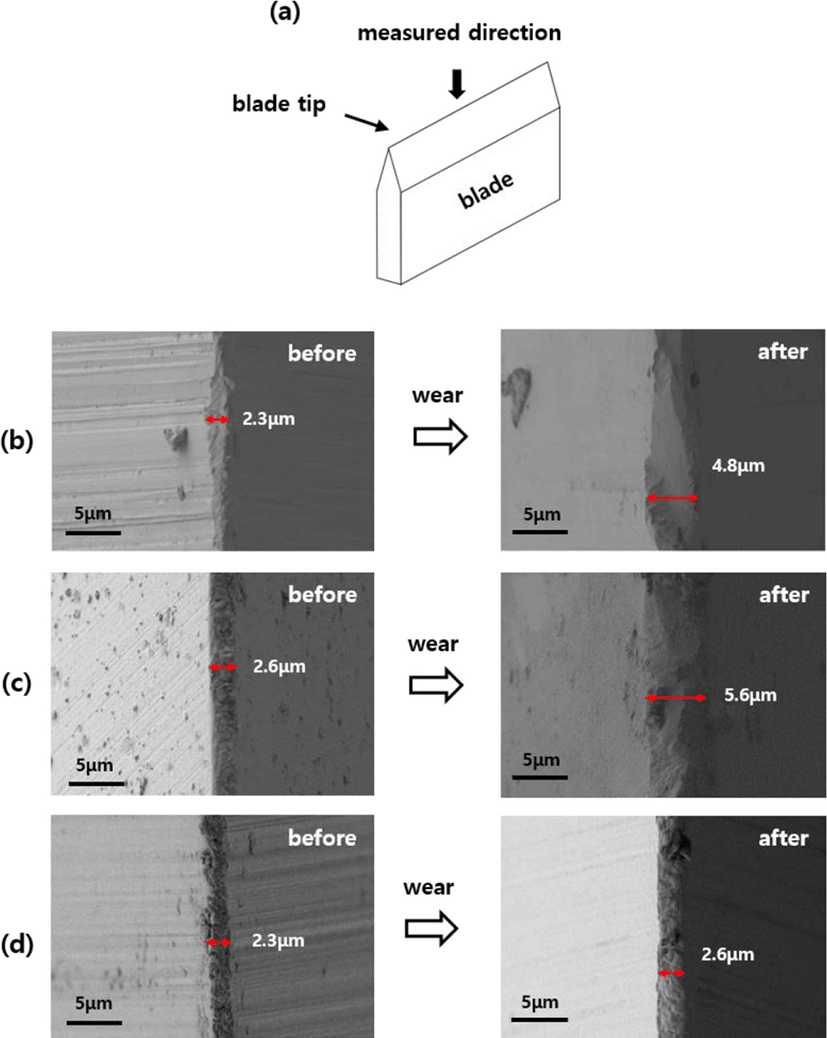
Figure 7과 8에는 BR 고무에 대한 3종류의 칼날재질의 영향을 나타내었다. SBR과는 매우 상이한 경향을 보였다. 즉, 회전수 증가에 따른 BR 고무의 마모속도가 칼날재질에 관계없이 거의 유사한 수준을 유지하는 것으로 나타났고, 마모 전후의 칼날 예리도에서도 초기 수준을 공히 유지하고 있었다. 이는 매우 흥미로운 결과인데 칼날의 예리도는 사용한 고무 종류에 따라서도 영향을 받는다는 것을 알 수 있다. BR의 경우 마모동안 발생하는 자유라디칼이 매우 불안정하여 바로 인접고무사슬과의 반응으로 추가적인 가교반응을 하는 것으로 알려져 있기 때문에 상대적으로 칼날과의 반응기회가 낮으므로 칼날의 예리도에 큰 영향을 주지 않는 것으로 판단된다.14 이러한 결과는 Figure 8에 나타난 마모 전후의 칼날 예리도를 통해서도 확인할 수 있다.
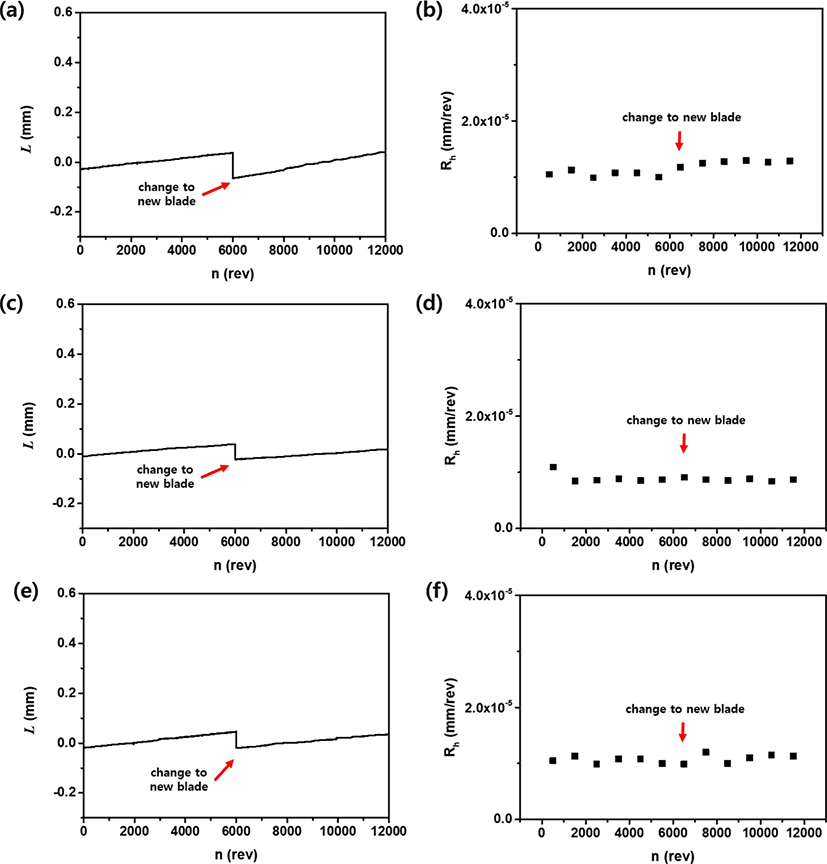
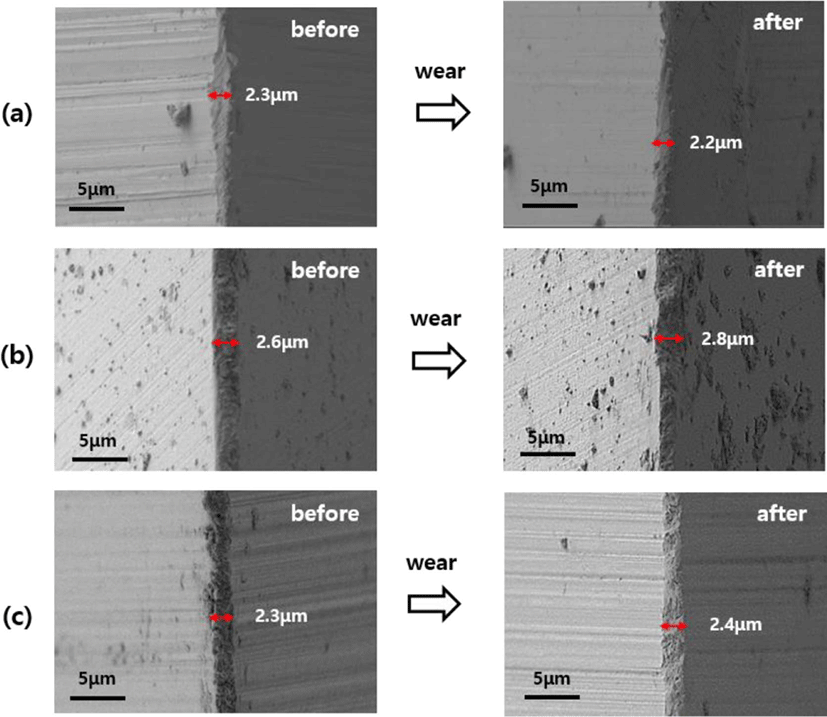
고무의 마모거동은 가해지는 하중에 따라 크게 영향을 받는 것으로 알려져 있다. 본 연구에서도 마모하중을 0.75~2.5 kg 변화시키면서 마모특성을 관찰하였으며 그 결과를 Figure 9-11에 도시하였다. 하중이 증가함에 따라 마찰토크는 증가하였고, 동일 하중에서는 BR보다 SBR이 더 큰 값을 나타냈다 (Figure 9). 한편 SBR의 경우는 칼날의 종류에 큰 영향을 나타내지 않았으나, BR의 경우 SB와 TiB가 ZB보다 높은 마찰토크 값을 보였다. 마찰계수의 경우 전체적으로 SBR이 BR보다 높은 마찰계수를 보였고, ZB가 SB와 TiB보다 대체로 낮은 마찰계수를 보였다. 전체적인 하중에 대한 경향은 하중증가에 따라 미세하게 마찰계수가 낮아지는 일반적인 경향을 보였다(Figure 10). 마모속도는 하중증가에 따라 증가하는 경향이 뚜렷하였고, SBR이 BR보다 급격한 증가경향을 보였다 (Figure 11). 동일 하중에서 SBR의 마모속도가 BR보다 크다는 것을 의미하는데 이는 Figure 9, 10에 나타낸 마찰토크와 마찰계수의 경향과 상응하는 결과로 마찰토크와 마찰계수가 클수록 마모속도가 크다는 일반적인 마모이론을 따르고 있음을 확인할 수 있다. 칼날재질에 대한 특별한 경향은 보이지 않았다. Figure 12에는 마모속도를 가해진 마찰에너지(Wf)의 로그-로그 함수로 도시하였다. SBR과 BR 공히 마찰에너지가 증가함에 따라 마모속도가 선형적으로 증가하는 결과를 보이고 있어 잘 알려진 Power-Law 마모관계식, Rh = k(Wf)n 을 따르는 것으로 나타났다.8,13 마찰일과 마모속도 그래프의 기울기는 마찰일에 대한 민감도를 나타내는 것으로 각 시편 이름 옆의 괄호 안에 계산하여 나타내었다. SBR이 전체적으로 BR보다 더 높은 기울기 값을 보였다. 한편 동일 마찰에너지 조건에서 ZB가 가장 높은 마모속도를 보이고 있는 경향도 확인할 수 있다. 따라서 단순하중 조건보다 마찰에너지 조건에서 고무의 마모거동을 비교하는 것이 보다 합리적인 방법이라고 판단된다.
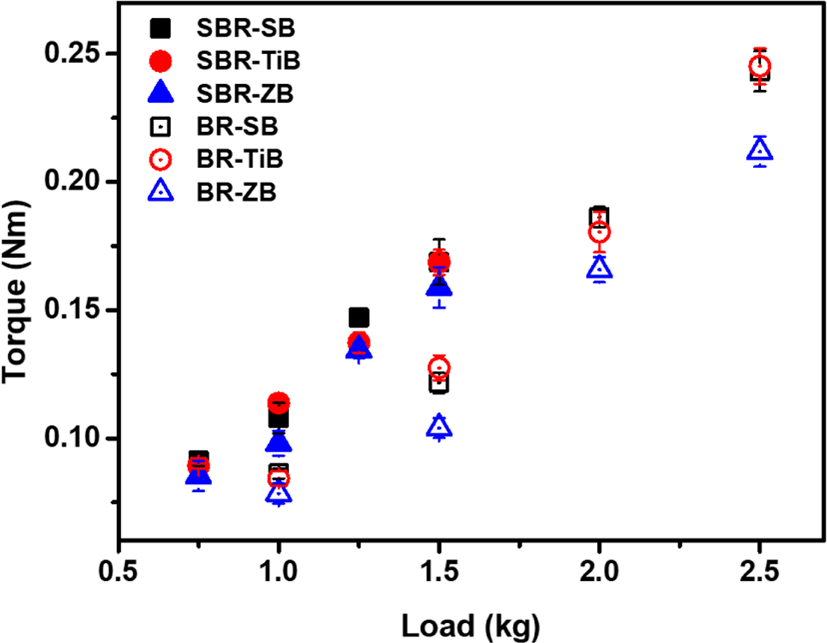
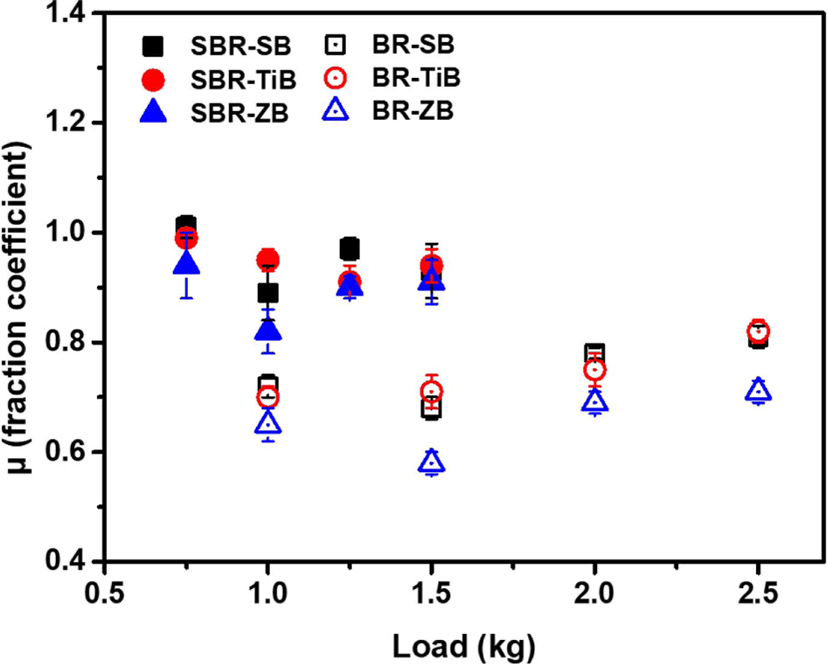
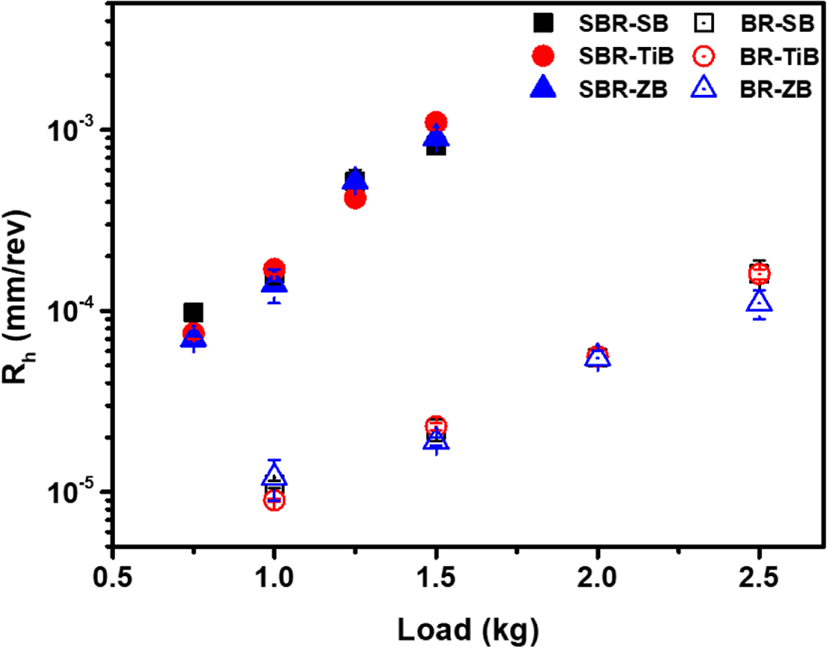
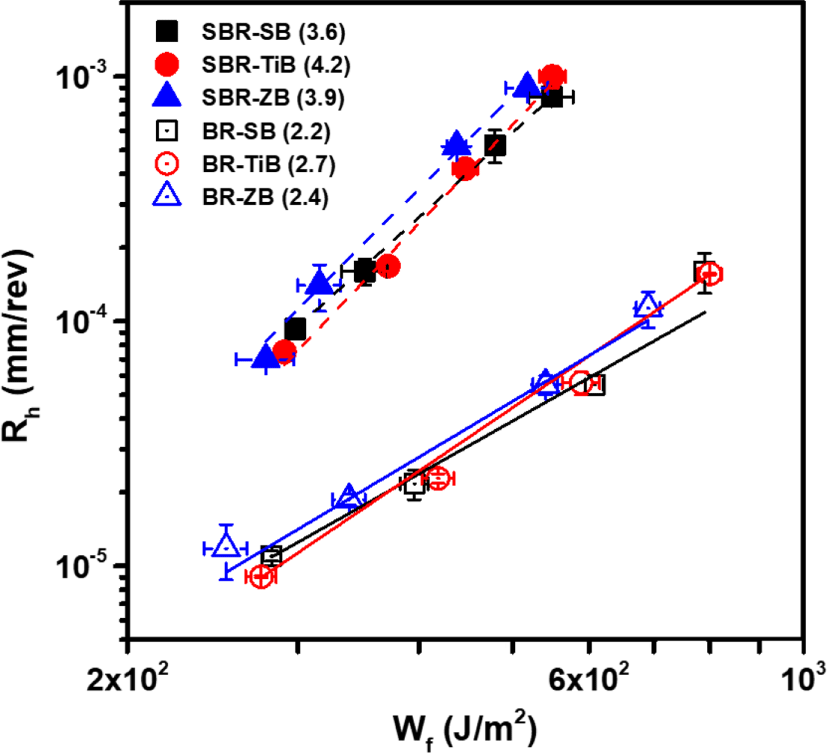
마모시편의 표면을 디지털 카메라로 촬영한 사진을 Figure 13에 나타냈다. 고무 표면을 칼날로 일정한 방향으로 마모시키면 마모방향과 수직한 방향으로 고무표면에 마모패턴이 형성되는데 이를 Schallamach 패턴이라고 한다.1 SBR의 경우, SB, TiB, ZB 공히 뚜렷한 Schallamach 패턴이 관찰되었으나 BR의 경우는 패턴대신 매우 고운 마모분말 형태의 입자가 떨어져 나오는 형태를 보였다. 이는 SBR과 BR의 마찰계수 차이에 의한 것으로 마찰계수가 큰 SBR은 칼날에 의한 패턴을 형성하며 마모가 진행되는 패턴마모 메커니즘이 일어났으나, 마찰계수가 낮은 BR은 고무 표면이 칼날의 긁힘에 의해 아주 작은 마모 입자를 형성하며 떨어져 나가는 절대마모가 일어난 것으로 판단된다.1
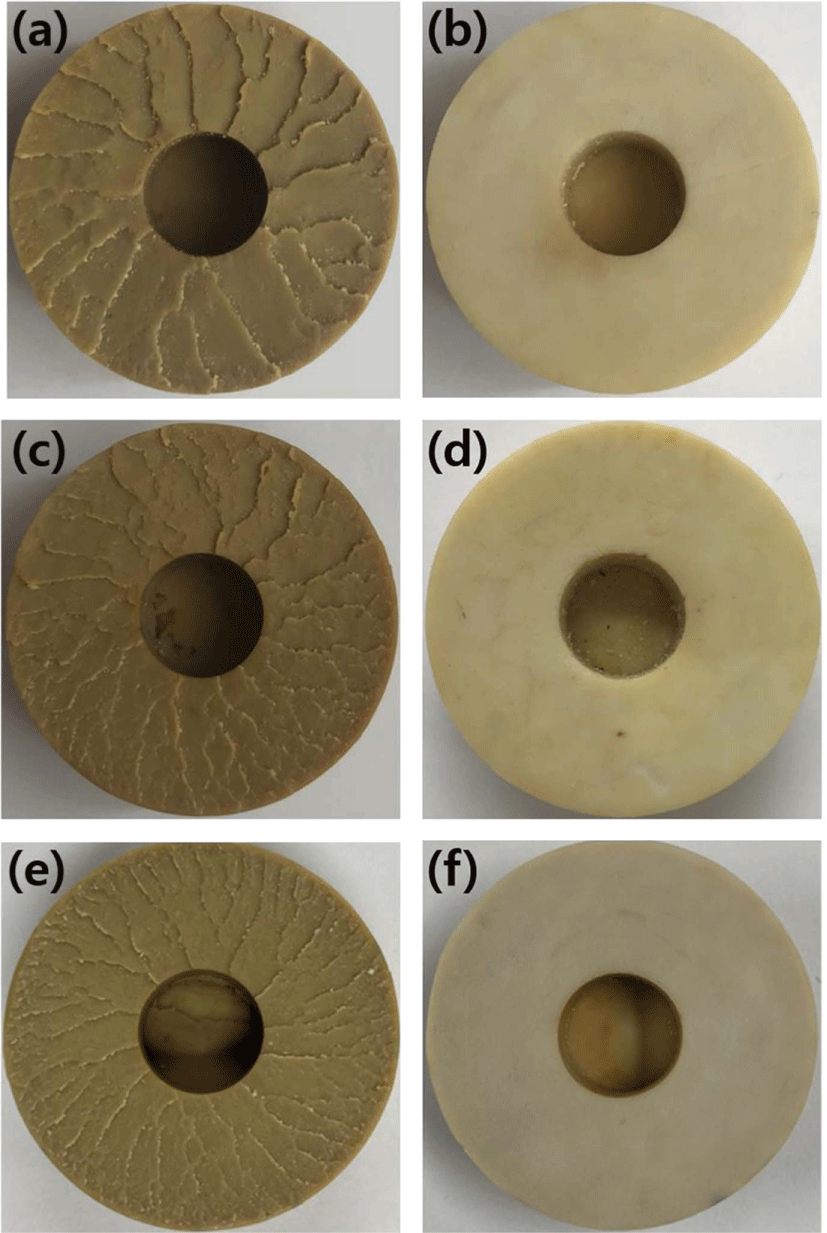
Conclusions
본 연구에서는 칼날형 마모시험기에 steel (SB), Ti-coated tungsten carbide (TiB) 및 zirconia (ZB) 칼날을 사용하여 SBR 및 BR의 마모거동을 조사하였다. 금속계인 SB와 TiB을 SBR 마모실험에 사용한 경우 SBR에 의해 칼날의 예리도가 저하되었지만 ZB의 경우는 비교적 일정한 칼날 예리도를 유지하였다. 한편 BR 고무의 경우는 칼날재질에 관계없이 칼날 예리도에는 큰 영향이 없었다. 따라서 고무의 마모평가에서 칼날의 재질과 고무의 종류는 반드시 고려되어야 할 것으로 판단된다.
하중에 따른 마모거동 조사결과 마찰토크, 마찰계수, 마모속도는 전반적으로 SBR이 BR보다 더 높은 경향을 나타냈다. 가해진 마찰에너지와 마모속도의 관계는 Power-Law, Rh = k(Wf)n 식을 따르는 것으로 확인되었다. SBR의 마모패턴은 Schallamach 마모 메커니즘을 따르고, BR의 마모는 고운 입자가 떨어져 나가면서 형성하는 절대마모 메커니즘을 따르는 것을 확인하였다.
본 연구를 통해 고무의 마모특성 측정에 있어서 칼날의 재질, 고무 종류 및 마찰에너지는 매우 중요한 요인으로 판단되며, SBR과 BR의 경우, 무기계인 zirconia 칼날이 가장 안정적인 마모특성 평가를 제공할 것으로 판단된다.