Introduction
최근 고압 천연가스 및 수소를 이용하는 자동차 생산이 증대됨에 따라 안전하면서도 다량의 가스를 저장할 수 있는 고성능 압력용기에 대한 개발연구가 활발하다.1,2 고성능 압력용기는 수소 자동차의 연료탱크 뿐 만 아니라 미사일이나 로켓의 모터케이스 및 가스를 이용하는 다양한 산업현장에서 사용되고 있다. 폭발의 위험이 상존하기 때문에 고압을 견딜 수 있도록 강성과 강도 그리고 연비향상을 고려한 경량화의 방향으로 개발되고 있다.3 이를 위해 탄소섬유강화 복합소재가 활용되고있는데 원통형의 구조물에 보강섬유를 감아 제작하는 소위 필라멘트 와인딩 공법이 활용된다.4,5 필라멘트 와인딩 공법은 섬유를 구조물에 감기 직전에 수지에 함침 시킨 후 돌려 감는 습식 와인딩 공법과 수지를 섬유에 미리 함침시켜 제조한 토우 프리프레그(tow prepreg)를 돌려 감는 건식 와인딩 공법으로 분류된다. 건식 와인딩 공법은 토우 프리프레그를 제조하는 공정이 필요하므로 제조원가가 상승하는 단점은 있으나, 수지와 섬유의 체적비를 정밀하게 조절할 수 있기 때문에 보다 균일한 복합재의 성형이 가능하며, 습식 와인딩 공법에 적용되는 수지보다 기계적 물성, 내열성, 내화학성 등이 우수한 반고상(semi-solid)의 수지를 사용하므로 고성능 및 고신뢰성이 요구되는 고압 압력 용기 제조에 적합한 것으로 알려져있다.1,5,6 고성능 고압 용기에 사용되는 토우 프리프레그의 경우, 강한 압력을 견뎌야 하므로 고강도와 고신율을 만족할 수 있는 에폭시 수지에 탄소섬유를 함침시켜 제조한 토우 프리프레그가 사용된다. 고압용기의 경우 수지의 취성을 보완하기위해 여러가지 형태의 필러를 첨가하여 터프니스와 파단신장률을 향상시킴으로써 내충격성을 향상시키는 노력을 하고 있다. 일반적인 충격보강제로는 탄성을 지닌 고무계 필러로써 carboxyl-terminated butadiene acrylonitrile (CTBN)이 대표적인 충격보강제이다. 에폭시 수지에 고무 필러를 첨가하여 경화반응을 가하면 상분리에 의해 에폭시 연속상에 고무입자 분산상의 모폴로지가 형성되어서 결국 고무입자에 의한 충격성능 향상을 기할 수 있다.7-10 최근 고압용기에 대한 추가적인 성능요구가 대두되면서 기존 고무형태의 충격보강제로는 한계에 직면하게 되었다. 즉, 충격보강효과를 위해 보강제 함량을 증가시킬 경우 에폭시의 유리전이온도의 하락이 동반되어 고압용기의 치수안전성에 문제를 야기시키고 있다. 따라서 관련 분야에서는 고무형 충격보강제를 대체할 새로운 소재개발 연구가 진행되는 것으로 알려지고 있다.
본 연구에서는 카본계 나노필러인 나노다이아몬드(ND)와 카본나노튜브(CNT)의 충격보강 효과에 대해 조사하였고, 이를 상용화 충격보강제인 CTBN 및 블록공중합체 형태의 나노입자와 비교분석 하였다. 충격보강 효과는 경도, 인장특성, 굴곡강도, 충격강도를 측정하여 비교하였고, 터프닝 메커니즘분석을 위해 파단면의 모폴로지도 관찰하였다. ND필러의 경우 표면처리 영향분석을 위해 epoxidized hydroxy-terminated polybutadiene (EHTPB)로 표면을 처리한 후 보강효과를 분석하였다.
Experimental
에폭시 수지는 ㈜국도화학의 bisphenol A type인 YD-128을 사용하였으며, Table 1에 기본특성을 나타냈다. 경화제로는 아민계 경화제인 dicyadiamide (DICY, Alzchem, Germany), 경화촉진제로는 dichlorophenyl dimethylurea (DCMU, Alzchem, Germany)를 사용하였다. 충격보강제로는 고무계 필러인 carboxyl-terminated butadiene acrylonitrile (CTBN, Zibo Qilong Chemical Industry Co. Ltd., China), 블록공중합체 형태의 나노필러인 poly(methyl methacrylate)-b-poly(butyl acrylate)-b-poly(methyl methacrylate) (BA-b-MMA, Nanostrength® M52N, Arkema, France)을 사용하였다. 카본계 나노 필러로는 나노다이아몬드(ND, CNVISON, Korea)와 카본나노튜브(CNT, CM-95, Hanwha Chemical, Korea)를 사용하였다.
Grade | Chemical class | Physical form | EEWa (g/eq) | Viscosity | Specific gravity (20°C) |
---|---|---|---|---|---|
YD-128 | Bisphenol-A | Liquid | 184-190 | 11,500-13,500b | 1.17 |
표면처리효과분석을 위해 ND의 표면처리는 epoxidized hydroxyl-terminated polybutadiene (EHTPB, Zibo Qilong Chemical Industry Co. Ltd., China)를 사용하였고, 표면개질 나노다이아몬드를 TND로 명명하였다. 콘덴서가 연결된 둥근 플라스크에 ND와 EHTPB를 1:1중량비로 넣고, 아세톤 용매를 첨가하여 100°C 에서 2시간 동안 반응시킨 후, 원심분리기를 이용하여 아세톤으로 4~5회 세척하여 미 반응 EHTPB를 제거하였다. 세척한 반응 혼합물을 80°C 오븐에서 1시간 동안 건조하여 표면이 EHTPB로 개질 된 TND를 제조하였다.
에폭시 컴파운드는 Table 2에 나타낸 조성비에 따라 용융 혼합법을 이용하여 제조하였다. 에폭시 수지를 150°C, 150 rpm 조건에서 30분 동안 교반시킨 후, 필러를 첨가하여 필러 종류에 따라 Table 3의 조건으로 혼합하였다. 이후 경화제와 경화촉진제를 첨가하여 60°C, 150 rpm 조건에서 30분 동안 교반시킨 에폭시 혼합물을 판상형 몰드에 부은 후, 80°C의 진공오븐에 넣고 30분 동안 기포를 제거하였다. 기포가 제거된 에폭시 혼합물을 100°C 오븐에서 1시간 동안 1차 경화시킨 후, 125°C 오븐에서 1시간 30분 동안 2차 경화시켜 판상형 시편을 제조하였으며, 워터젯 절단기(BC WATERJET, Korea)를 이용하여 각 물성평가에 적합한 형태의 시편을 제작하였다.
Ingredients | Compounds | ||||
---|---|---|---|---|---|
1 | 2 | 3 | 4 | 5 | |
Epoxy resina | 100 | 100 | 100 | 100 | 100 |
CTBN | - | 1, 2, 5 | - | - | - |
BC | - | - | 1, 2, 5 | - | - |
ND or TNDb | - | - | - | 1, 2, 5 | - |
CNT | - | - | - | - | 0.5, 1 |
DICYc | 3 | 3 | 3 | 3 | 3 |
DCMUd | 2 | 2 | 2 | 2 | 2 |
Filler Type | Temperature (°C) | Stirring Speed (rpm) | Mixing Time (h) |
---|---|---|---|
CTBN | 150 | 150 | 4 |
BC | 150 | 150 | 2 |
ND or TNDa | 100 | 150 | 1 |
CNT | 100 | 150 | 1 |
표면처리를 통해 개질시킨 나노다이아몬드의 화학적 구조는 푸리에 변환 적외선 분광법(FT-IR, Spectrum 400 FT-IR, PerkinElmer Frontier, USA)을 통해 측정하였으며, 입자크기는 동적광산란(DLS, 90 Plus, Brookhaven Instruments, USA)을 사용하여 측정하였다.
인장특성은 ASTM D638-14규정에 따라 3.2 mm 두께의 덤벨형 시편을 제조한 후, 만능재료시험기(Instron 5969, Instron, USA)를 이용하여 5 mm/min의 속도로 측정하였으며, 인장강도 및 파단신장률을 구하였다.
굴곡강도는 ASTM D790-15 규정에 따라 127×12.7×3.2 mm 크기의 시편을 제조한 후, 만능재료시험기(Instron 5969, Instron, USA)를 이용하여 측정하였다.
충격강도 측정은 Izod형 충격 시험법으로 진행하였으며, ASTM D256-10 규정에 따라 노치가 적용된 63.5×6×12.7 mm크기의 시편을 사용하여 충격 시험기(HIT25P, Zwick Roell, Germany)를 이용하여 측정하였다.
Results and Discussion
나노다이아몬드는 표면에 있는 친수성 하이드록실기와 카르복실기 등의 관능기들로 인해 에폭시 수지와 상용성이 좋지 않으며, 입자들이 서로 응집되는 경향이 강하여 분산이 어려운 것으로 보고되고 있다.11 이를 개선하기 위해 EHTPB를 이용하여 표면을 개질시켰다. Figure 1에 미개질(ND) 및 개질(TND) 나노다이아몬드의 FT-IR 결과를 나타냈다. ND의 경우 표면에 있는 하이드록실기와 카르복실기의 -OH 특성을 나타내는 3,425 cm-1 영역의 피크가 크게 나타났으나, TND에서는 이 영역의 피크가 크게 감소하였고, 에스테르의 카르보닐기(C=O) 특성을 나타내는 1,716 cm-1 영역의 피크가 크게 나타났다. 또한, EHTPB의 에폭시 특성을 나타내는 910 cm-1 영역의 피크도 함께 관찰되었다. 이를 통해 ND 표면의 카르복실기와 EHTPB의 양쪽 말단에 있는 하이드록실기가 만나 에스테르화 반응을 통하여 표면개질이 이루어졌음을 확인하였다.
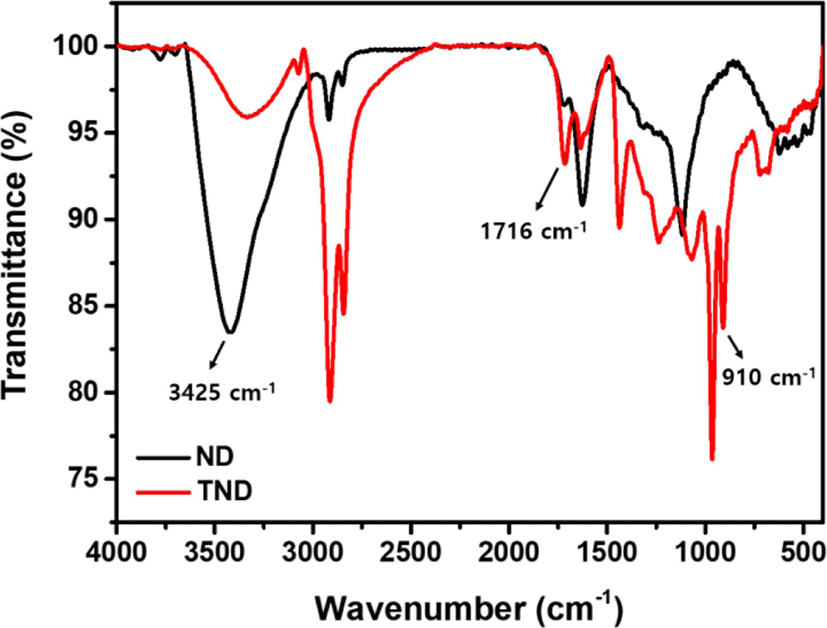
ND의 표면처리에 대해 추가적으로 확인하기위해 ND, TND 및 EHTPB의 TGA 열분해 거동을 조사하였고 그 결과를 Figure 2에 정리하였다. ND는 700°C에서 약 4%의 질량감소를 보이고 있어 열적으로 매우 안정된 것으로 나타났다. 반면 유기물인 EHTPB는 약 400°C에서 열분해가 시작되어 2%의 잔량만을 남기고 모두 열분해 되었다. TND의 경우는 400°C에서 표면에 존재하는 EHTPB의 분해로 약 33%의 질량 감소를 나타냈다. 이를 통해 약 31 wt%의 EHTPB가 TND 표면에 존재하는 것을 확인하였으며, 이는 ND의 표면개질이 성공적으로 이루어졌음을 나타낸다.
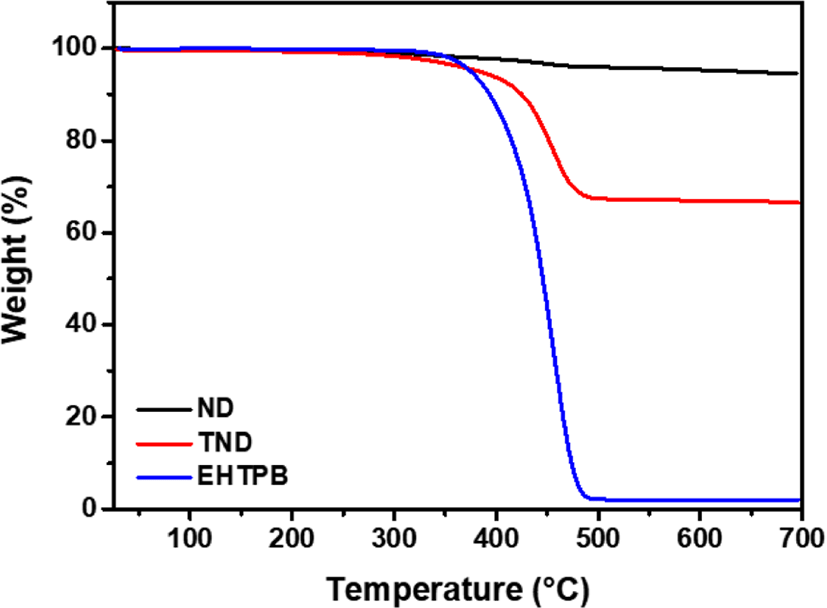
ND의 입자크기 분석을 위해 ND와 TND를 에탄올에 분산시킨 후, DLS 분석을 진행하였고 결과를 Figure 3에 나타냈다. ND의 입자크기는 1,793-1,867 nm로 나타났는데, 본 연구에 사용된 ND의 평균입자크기가 4-6 nm인점을 감안하면 ND 입자들이 서로 뭉쳐서 응집체를 이루고 있음을 알 수 있다. 반면 TND의 경우, 응집체의 크기가 238-328 nm로 크게 감소하였으며, 이는 EHTPB를 이용한 표면개질 방법이 ND 입자간 응집력을 크게 감소시키는 것으로 해석할 수 있다.
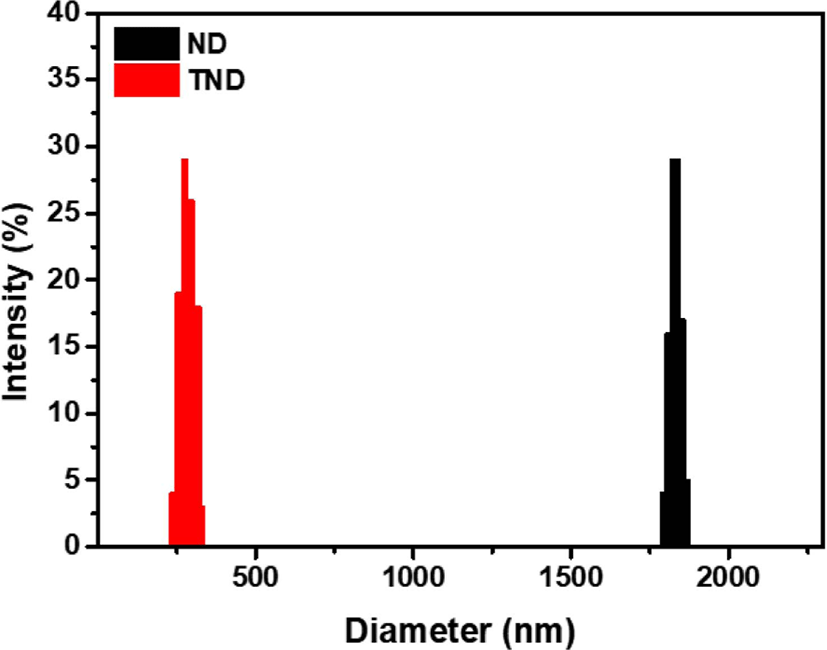
에폭시 컴파운드의 필러 종류 및 함량에 따른 인장강도 거동을 Figure 4에 나타내었다. 에폭시 컴파운드의 인장특성은 에폭시 수지와 필러의 상용성에 영향을 받기 때문에10 에폭시 수지와 상용성이 낮은 CTBN,10 ND,11 CNT12가 첨가된 컴파운드의 경우, 인장강도에 대한 필러의 보강효과가 나타나지 않았으며, 오히려 미세한 감소경향도 보였다. 또한, CTBN의 경우, 에폭시 매트릭스의 분자사슬에 작용하여 가교밀도를 감소시키는 역할을 하므로 이로 인한 물성저하 현상도 동반된 것으로 판단된다.13,14 그러나 CTBN의 함량이 5 phr로 증가하였을 때, 인장강도가 급격히 향상되는데 이는 CTBN 입자로 인한 터프닝 현상이 크게 증가하였기 때문으로 판단되며 이에 대한 추가내용은 다음에 나오는 충격강도 결과에서 설명하겠다. 반면 BA-b-MMA와 TND의 경우 에폭시 수지와 상용성이 좋은 MMA와 EHTPB를 각각 포함하고 있기 때문에 필러의 함량이 증가할수록 인장강도가 증가하는 경향을 나타냈다.
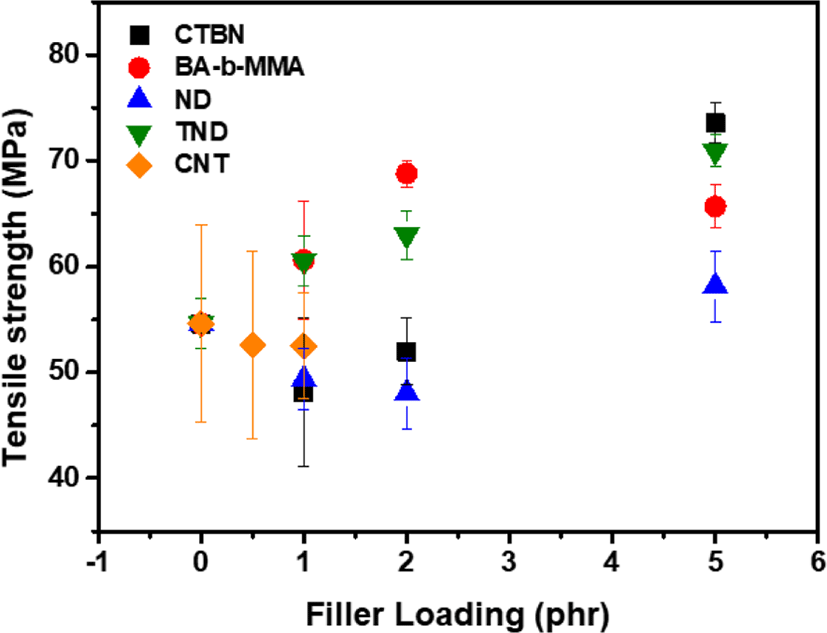
에폭시 컴파운드의 필러 종류 및 함량에 따른 파단신장률을 Figure 5에 나타냈다. 에폭시 컴파운드의 파단신장률은 고압 조건 하에서 충전과 방전이 반복적으로 발생되는 압력용기의 피로파괴 저항성에 영향을 주는 중요한 요인 중 하나이다. 파단신장률은 인장강도에서의 경향과 유사하게 나타났다. 인장강도와 파단신장률의 경우 필러 함량이 낮은 범위(~2 phr)에서는 BA-b-MMA와 TND, 높은 범위(~5 phr)에서는 CTBN의 보강효과가 가장 크게 나타났다.
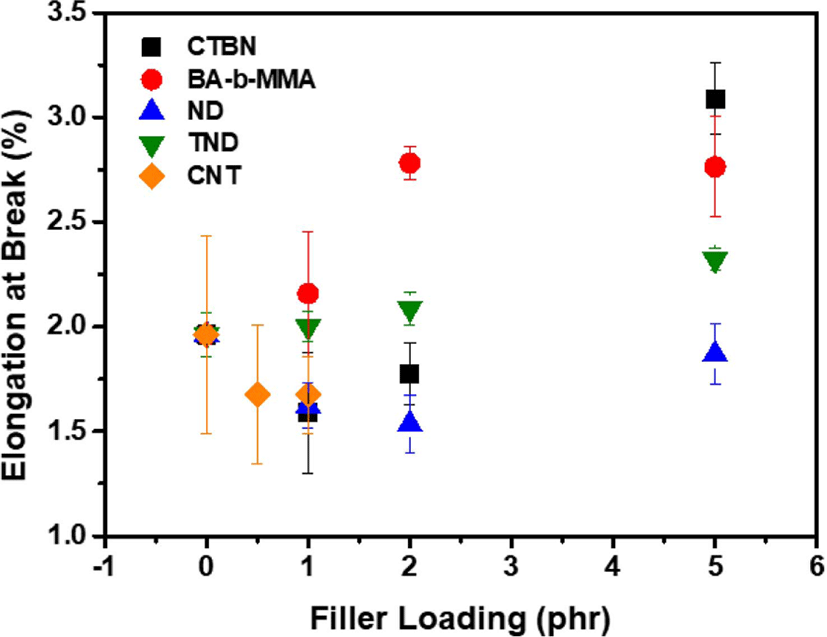
Figure 6은 에폭시 컴파운드의 필러 종류 및 함량에 따른 굴곡강도를 나타냈다. 전체적으로 CTBN과 ND의 경우 굴곡강도가 하락하는 경향을 보였다. BA-b-MMA의 경우 에폭시 수지 자체의 굴곡강도는 유지하였고, TND와 CNT의 경우만이 굴곡강도의 향상을 나타냈다. CNT의 경우 섬유형태이기 때문에 에폭시 수지에 분산된 CNT가 굴곡강성을 향상시킨 것으로 판단되며 TND의 경우 에폭시와 EHTPB와의 상호작용이 크기 때문에 굴곡 저항성이 향상된 것으로 판단된다.
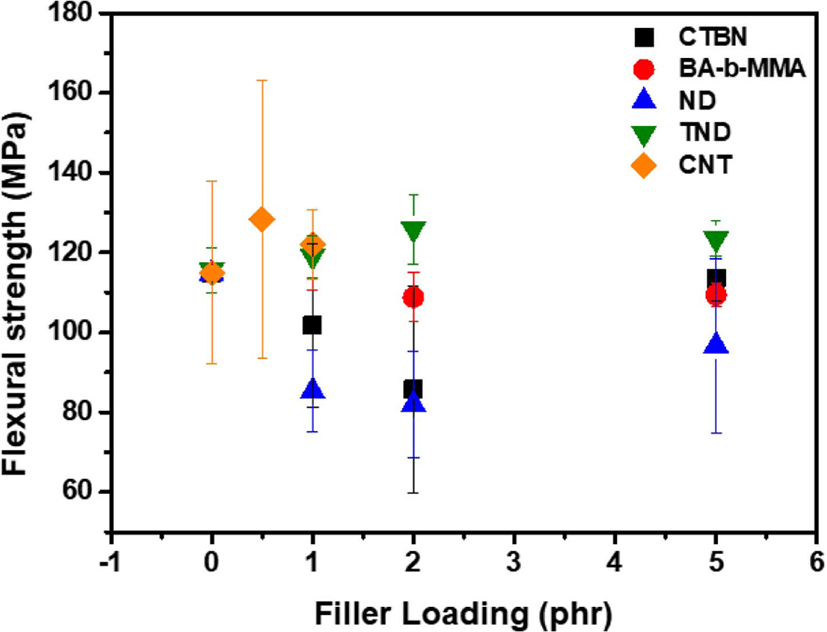
에폭시 컴파운드의 필러 종류 및 함량에 따른 충격강도 결과를 Figure 7에 나타냈다. CTBN으로 보강된 컴파운드의 충격강도는 1 phr에서 감소하였다가 필러 함량이 증가함에 따라 증가하였다. CNT의 경우 0.5 phr에서 최대치를 보인 후 감소하였으며, ND의 경우 1 phr에서 증가를 보인 후 다시 하락하는 경향을 보였다. BA-b-MMA와 TND의 경우 2 phr에서 최대치를 보인 후 하락하는 경향을 보였다. 즉, 필러 함량 증가에 따라 충격강도가 증가를 보인 후 감소하는 경향이 모든 필러에서 관찰되었다. 최대 충격강도 값을 기준으로 CNT > TND > ND > CTBN > BA-b-MMA 순으로 나타났다. 전체적으로 카본계 나노입자인 CNT와 ND가 에폭시 수지의 내충격성 향상에는 효과적인 것으로 평가된다.
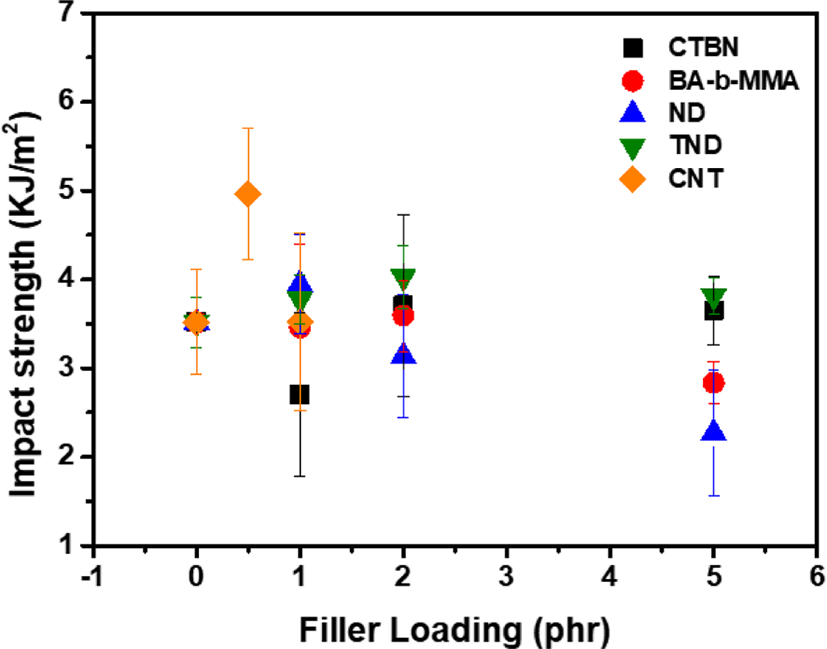
에폭시 컴파운드의 필러 종류 및 함량에 따른 경도 결과를 Figure 8에 나타냈다. 전반적으로 CTBN은 경도 특성에 크게 영향을 미치지 않은 것으로 나타났다. 반면 나노 필러의 함량증가에 따라 선형적인 경도 증가를 보였는데 가장 효과적인 필러는 TND로 평가되었다. BA-b-MMA, CNT, 그리고 ND의 경우는 유사한 보강효과를 나타냈다.
에폭시 메트릭스 내에 분산된 각 필러의 형태 및 분산상태를 FE-SEM으로 관찰하였고, 그 결과를 Figure 9-13에 나타냈다. 순수 에폭시는 비교적 매끄러운 파단면을 보였다(Figure 9). 비교적 규칙적인 직선 형태의 균열이 하중 방향으로 배열되어 있는 전형적인 취성 파괴 특성을 보였다.15 에폭시 수지에 CTBN을 첨가한 경우 경화과정을 통해 에폭시의 분자량이 증가함에 따라 구성 엔트로피(configurational entropy)가 감소하면서 CTBN의 상분리가 일어난다.9 이로 인해 에폭시 매트릭스에 구형의 CTBN이 분산상으로 분포되어 있는 형태가 나타나며, Figure 10에서 이를 확인할 수 있다. 1 phr의 CTBN이 첨가되었을 때 크기가 작은 CTBN 입자가 형성되었으나 개수가 매우 적고, 이로 인한 터프닝 현상도 거의 나타나지 않았다. 그러나 필러 함량이 증가함에 따라 CTBN의 입자크기와 개수가 증가하면서 터프닝 효과도 증가하였다. 에폭시 매트릭스에서 균열이 전파되다가 CTBN 입자를 만나면 응력이 집중되면서 터프닝 현상이 나타나는데, CTBN 입자를 지나면서 균열 방향이 바뀌는 crack deflection과 CTBN 입자가 에폭시 매트릭스에서 떨어져 나가는 cavitation의 터프닝 메커니즘이 주로 관찰되었다. 또한 CTBN 입자가 떨어져 나가면서 cavitation 주변의 에폭시를 변형시키는 shear yielding 현상도 관찰되었다. 특히, CTBN이 5 phr 첨가된 컴파운드의 터프닝 거동이 눈에 띄게 증가하였으며, 이러한 터프닝 효과로 인해 5 phr에서 인장특성이 크게 향상되었고, 충격강도 또한 증가한 것으로 판단된다.
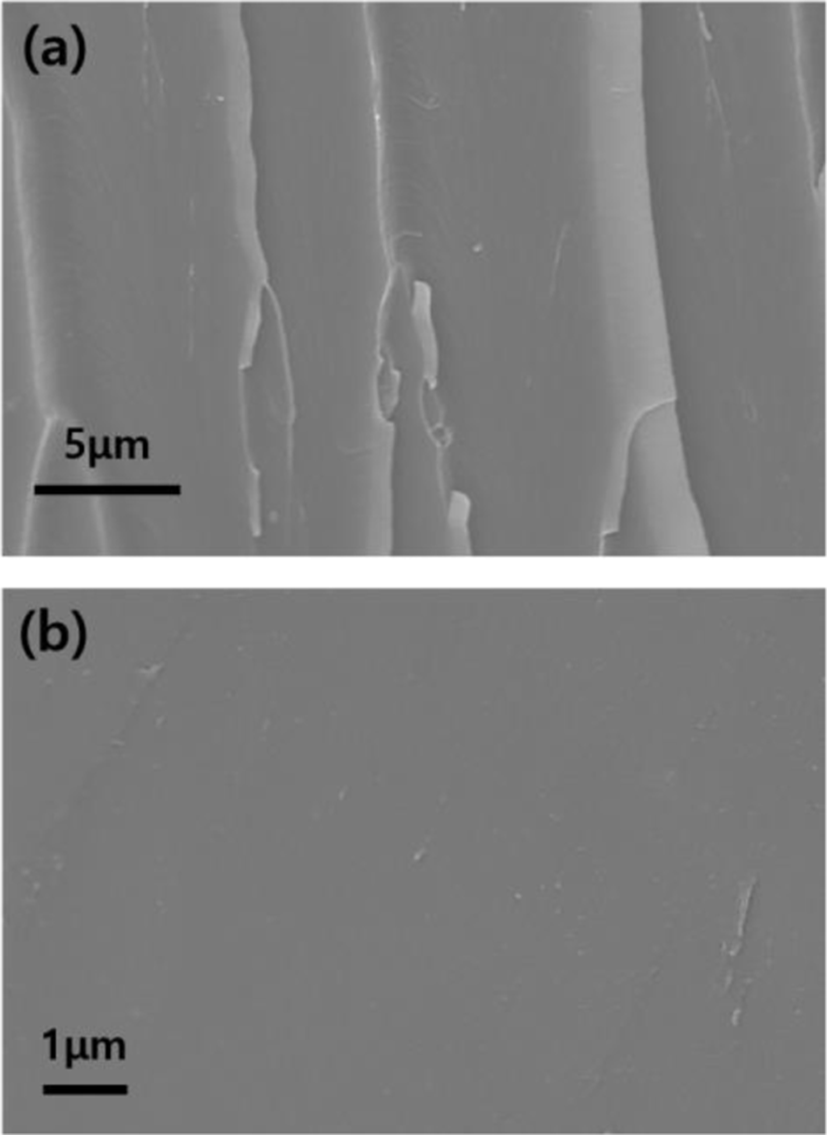
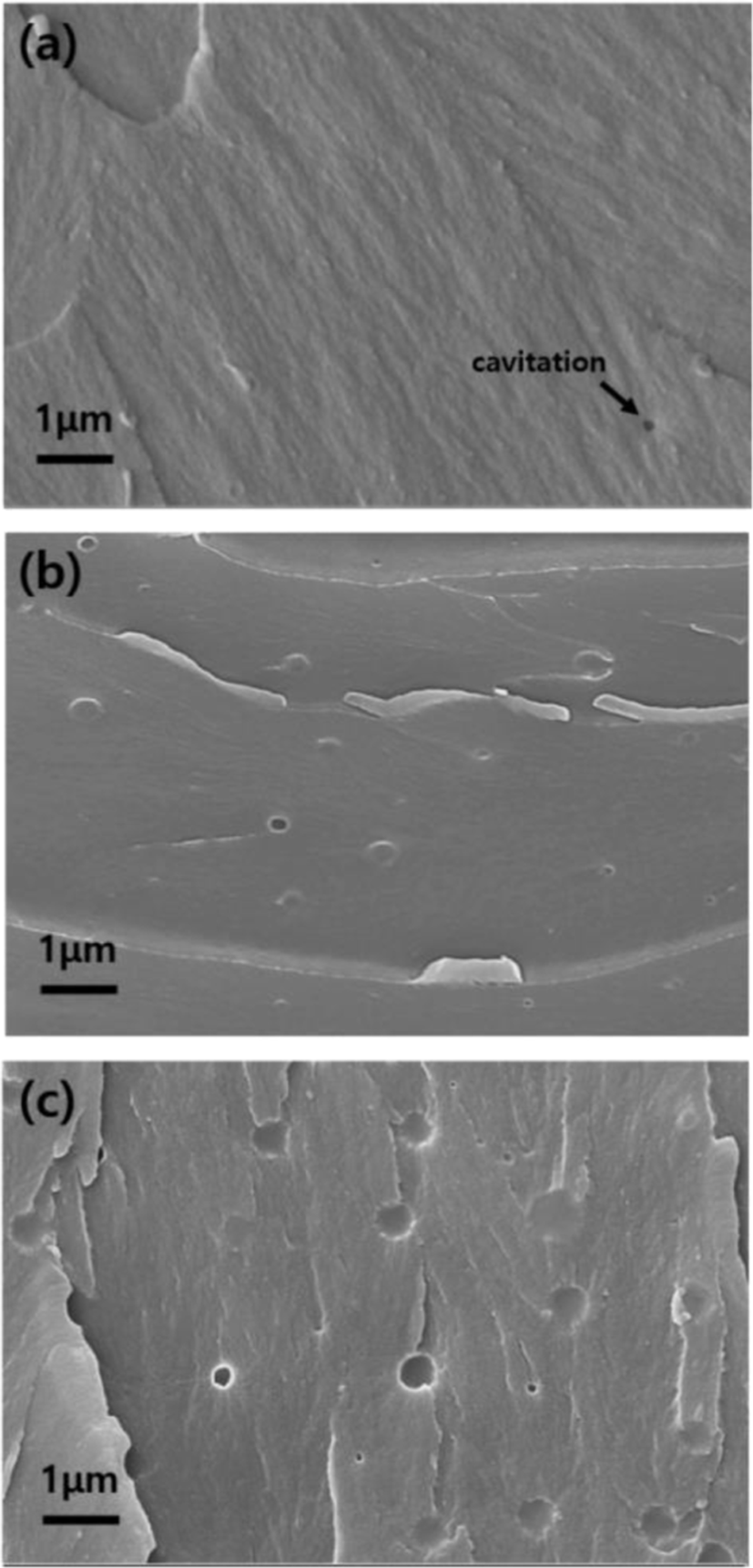
BA-b-MMA는 에폭시 수지에 혼합되지 않는 butyl acrylate (BA) 블록 양 말단에 에폭시 수지와 상용성이 좋은 methyl methacrylate (MMA) 블록이 위치해 있는 형태를 가지고 있으며, 에폭시와의 상용성 차이로 인해 MMA 블록이 BA 블록을 감싸고 있는 core-shell 형태로 자가조립하여 에폭시 매트릭스에 분산된다.16-18 CTBN과 마찬가지로 에폭시 수지의 경화과정에서 BA-b-MMA의 상분리가 일어나면서, Figure 11과 같이 에폭시 매트릭스에 구형의 BA-b-MMA 입자가 분산상으로 분포되어 모폴로지를 형성하고 있다. BA-b-MMA의 함량이 증가할수록 입자크기가 증가하였으며, CTBN과 같이 crack deflection, cavitation, shear yielding의 터프닝 메커니즘이 관찰되었다. 그러나 BA-b-MMA의 경우 CTBN과는 다르게 에폭시 수지와 결합력이 좋은 MMA가 BA 입자를 감싸고 있기 때문에 BA-b-MMA 입자가 에폭시 매트릭스에서 떨어져 나갈 때 MMA로 인한 shear yielding 현상이 cavitation 주변에 많이 나타났으며, cavitation 표면도 CTBN보다 거칠게 나타났다. 이로 인해 BA-b-MMA의 굴곡강도와 충격강도가 CTBN보다 더 큰 값을 보였으나, 5 phr과 같이 고함량에서는 BA-b-MMA 입자들이 더 큰 응집체를 형성하면서(Figure 11d) 순수 에폭시 수지보다 더 낮은 충격강도 값을 나타냈다. 크기가 큰 응집체들은 컴파운드의 조기파괴를 일으키는 시작점으로 작용하게 되고 이로 인해 충격강도가 저하된다.19
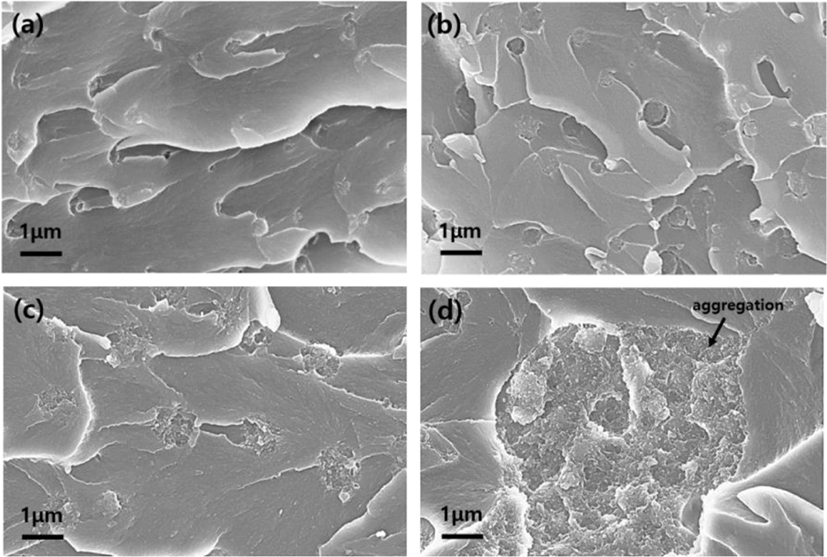
ND 및 TND로 보강된 에폭시 컴파운드의 파단면을 Figure 12에 나타냈다. ND의 경우(Figure 12a, 12b) shear yielding, crack deflection의 터프닝 메커니즘과 함께 ND 입자들의 응집현상이 관찰되었으며, 필러 함량이 증가함에 따라 더 많은 응집체들이 나타났다. 이로 인해 1 phr에서 증가하였던 충격강도가 점점 감소하는 경향을 보였다. 반면 TND의 경우(Figure 12c, 12d) 표면 개질로 인해 입자들의 응집력이 감소하고, 에폭시와 TND 사이의 상용성이 증가하면서 에폭시 매트릭스에 균일하게 분포되었으며, 응집현상 없이 shear yielding, crack deflection의 터프닝 메커니즘을 나타냈다. 이로 인해 TND의 함량이 증가함에 따라 에폭시 컴파운드의 굴곡강도와 충격강도가 증가하였다. TND 보강 컴파운드 보다 BA-b-MMA 보강 컴파운드의 파단면이 더 거칠고 더 많은 터프닝 현상이 관찰되지만, TND 필러 자체의 강성이 BA-b-MMA보다 훨씬 크기 때문에 TND의 굴곡 및 충격강도가 BA-b-MMA보다 더 큰 값을 나타내는 것으로 판단된다.
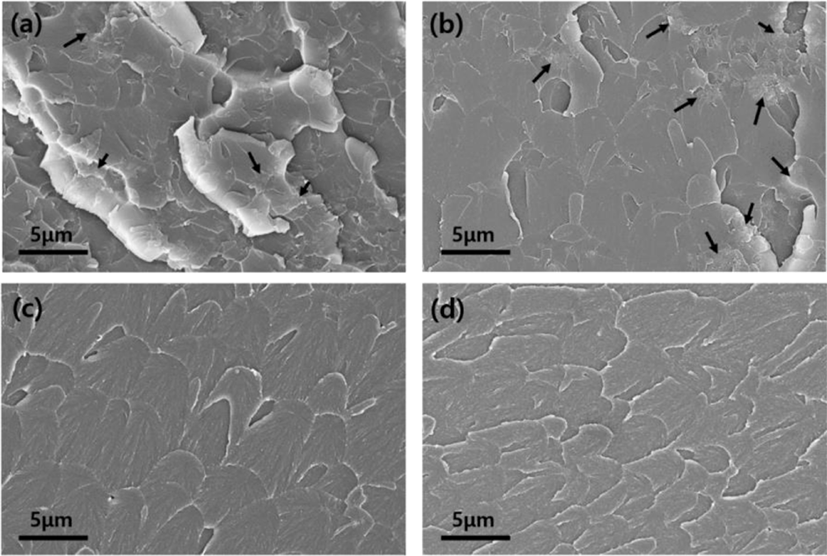
CNT로 보강된 에폭시 컴파운드의 파단면을 Figure 13에 나타냈다. 0.5 phr CNT 보강 컴파운드의 경우, 매우 소량의 CNT가 분산되어 있으며, CNT가 존재하지 않는 에폭시 매트릭스 부분이 많이 관찰되었다. 그러나 적은 양의 CNT로 crack deflection, crack bridging, cavitation의 터프닝 효과를 나타내면서 굴곡강도와 충격강도가 크게 증가하였다. CNT는 필러 자체의 강성이 높고, 종횡비가 매우 큰 섬유형태로 되어 있기 때문에20,21 적은 양으로도 다른 필러들보다 굴곡강도와 충격강도를 더 크게 향상시키는 것으로 판단된다. 그러나 에폭시와의 결합력이 좋지 않고, 반데르발스 힘에 의해 입자들이 응집하려는 경향이 크기 때문에21-23 CNT 함량이 증가함에 따라 큰 응집체를 형성하면서 균열의 개시점으로 작용하여 굴곡강도와 충격강도가 감소하였다.
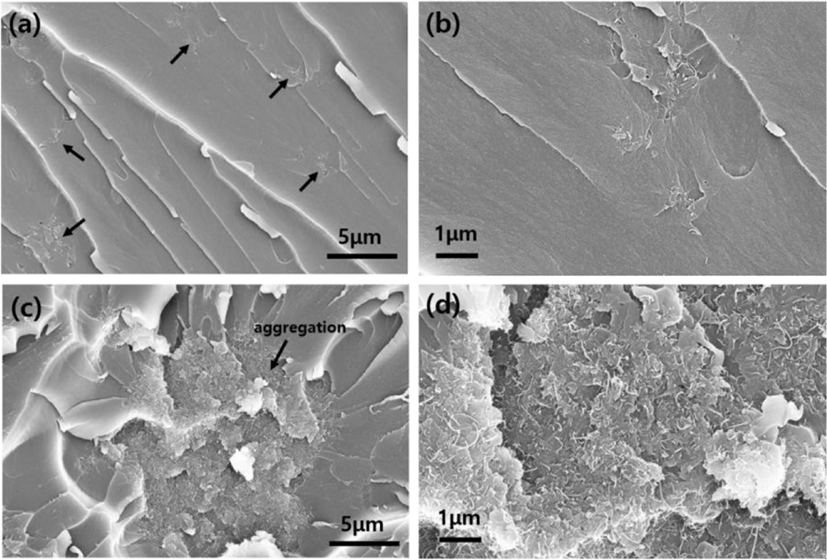
Conclusions
본 연구에서는 고성능 압력용기에 사용되는 토우프리프레그에 적합한 에폭시 수지의 충격보강성 향상을 위해 카본계 나노입자인 나노다이아몬드(ND 및 TND)와 카본나노튜브(CNT)를 적용하였고, 이를 블록공중합체 나노입자인 BA-b-MMA와 일반적인 고무계 충격보강제인 CTBN과 비교분석 하였다.
기존 CTBN으로 보강된 에폭시 컴파운드는 5 phr 이상의 필러 함량에서 높은 신율과 충격보강성을 나타내지만, 나노입자인 ND, TND, CNT 및 BA-b-MMA의 경우 2 phr 이하의 낮은 함량에서도 높은 강인성을 보였다. 특히, CNT는 0.5 phr의 함량으로 다른 필러들보다 뛰어난 강인성을 나타냈다. 그러나 에폭시 수지와 CNT의 결합력이 낮아 컴파운드의 파단신장률이 저하되는 모습을 보였다. 반면, BC와 TND 보강 컴파운드는 강인성과 파단신장률 모두 향상되었으며, 필러 자체의 강성이 높은 TND가 BA-b-MMA보다 더 큰 충격보강성과 파단신장률을 나타냈다. 따라서 고성능 압력 용기용 토우프리프레그의 에폭시 보강 시스템에 TND을 적용한다면, 적은 양으로 고효율을 나타낼 수 있을 것으로 판단된다.