Introduction
Since Dow first manufactured foamed polystyrene boards by extrusion in 1944, foamed polymers have been used in various materials such as lightweight materials (materials with low foam density), insulation materials, and shock absorbing materials. Recently, demand for a new foamed polymer material continues in emerging fields such as electric vehicle applications. In general, when a chemical blowing agent is mixed with a solid polymer and the mixture is heated while maintaining pressure, the polymer fluidizes and the blowing agent releases gas through a chemical reaction. This gas forms bubbles or cells in the fluid polymer, and when the mixture formed with cells is injected into a mold and solidified by cooling, a polymer foam having a cell structure is obtained. Since different blowing agents release gas at different temperatures, the choice of blowing agent depends on processing conditions, polymer type, desired cell size, blowing agent cost and environmental impact. There are many publications on various techniques and applications using various blowing agents and foaming methods for different polymers.1-4 Polyamide polymers are engineering plastics and are widely used in various industrial fields that require excellent high strength, light weight, and wear resistance.5,6 In particular, since aliphatic polyamide such as Nylon 6 is thermoplastic and can be easily molded, it is mainly used in various applications such as mechanical parts, automobile/aircraft parts, clothing and sports goods, electrical/electronic parts, and home appliances. In particular, weight reduction is very important when they are used for automobile/aircraft materials and special parts. Wang et al.7 manufactured porous Nylon 6 material using a facial solution-foaming strategy method in which a foaming agent that reacts with formic acid generates CO2 gas to induce phase separation of the polymer. However, in general, polyamide polymers have a high melting point and are not easy to process by foaming. Therefore, in this study, Nylon 6 was foamed using a chemical foaming agents (p-toluenesulfonyl semicarbazide (PTSS) and 5-phenyltetrazole (5-PT)) at various concentrations. The foam density and the weight reduction of Nylon 6 was studied to investigate the effects of each foaming agent. In general, crystalline resins such as polypropylene and Nylon are known to improve toughness and transparency/gloss by increasing crystallinity during cooling and solidification in a molten state by an added nucleating agent. It is also known that the nucleating agent serves to shorten the cooling time during molding by increasing the crystallization rate.8 In this study, the effect of the content of the additive Talc, which acts as a nucleating agent,8 on the density and % weight reduction of Ny-lon 6 foam was also studied.
Experimental
Material: Nylon 6 (KN111, Kolong Plastic Co., LTD) was dried and used. Blowing agents p-toluenesulfonyl semicarbazide (PTSS, KUM YANG CO., LTD, Korea) and 5-phenyltetrazole (5-PT, KUM YANG CO., LTD, Korea) were used as they were supplied by the manufacturer. Talc (KC5000, Particle size: 3.5±0.5 μm, KOCH Co., LTD, KOREA) was used as a nucleating agent without purification. A custom-made kneader (horizontal twin screw closed type kneader) was used to prepare the mixing and foaming samples.
Results and Discussion
In order to find the appropriate temperature for melting the Nylon 6 resin, the resin was melted in a kneader preheated at 230°C, 240°C, and 250°C for 4 minutes, which was sufficient to observe its melting or discoloration. Then, a foaming agent was added, mixed, and then taken out and cooled. The appearance of the mixture is shown in Figure 1. In the sample obtained at 230°C, it was found that the melt was not sufficiently melted under this experimental condition, and in the case of 250°C, discoloration occurred. However, it was found that the sample obtained at 240°C was a well-melted and mixed. Therefore, in this experiment, all samples were melted and mixed at the optimum temperature of 240°C for 4 minutes to prepare foamed Nylon 6 samples. Because of the high processing temperature (230-260°C) of Nylon 6, PTSS with the high decomposition temperature of 229-235°C and 5-PT with that of 234-245°C were used as blowing agents in this study. However, the amount of gas generated by PTSS is 150-160 ml/g and that of 5-PT is 180-210 ml/g, so 5-PT generates more gas than PTSS.
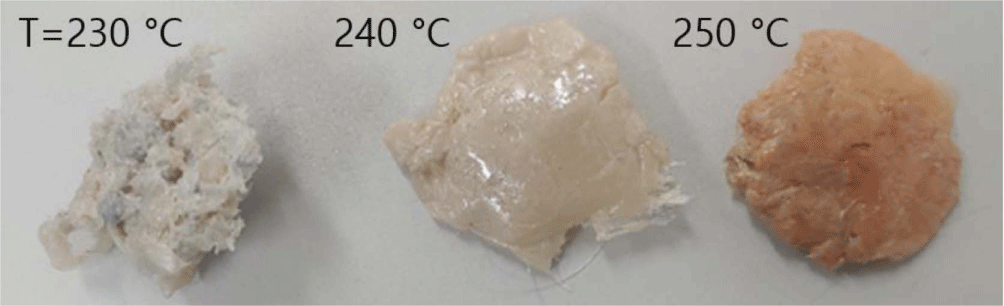
Table 1 shows the density and weight reduction rate (%) of Nylon foam according to the type and content of the foaming agent. Figure 2 show the effect of the foaming agent content (phr) on the foam density g/cm3, and Figure 3 show the weight loss rate (%) of the foam according to the foaming agent content of PTSS and 5-PT. As the content of both blowing agents increased, the density of Nylon 6 foam decreased and the rate of weight reduction increased. However, in the case of the foaming agent PTSS, the density of the foam decreased almost linearly, and the density of the foam was 0.71 g/cm3 at 10 phr, and the weight reduction rate was 37.7%. On the other hand, in the case of 5-PT, as the content of the foaming agent increased up to 2 phr, the density of the foam rapidly decreased, and it was found that the density of the foam gradually decreased above 2 phr. In the case of 5-PT, the density of the foam was 0.73 g/cm3 at the foaming agent content of 1.5 phr, and the weight reduction rate reached 36.0%. In addition, when the foaming agent content was 2 phr, the density of the foam was 0.55 g/cm3 and the weight reduction rate was 51.8%, showing a very large change. That shows that the foaming performance of 5-PT 1.5 phr is high enough to be almost comparable to the foaming performance of PTSS 10 phr. Of course, it would be necessary to adjust the required density and weight reduction rate in consideration of the required physical properties of each material, but as a result of simply comparing the foaming properties of the two foaming agents, it was found that 5PT has significantly better foaming performance than PTSS. This is partly due to the fact that 5-PT produces a slightly higher amount of gas per unit gram and the processing conditions was more favorable to 5-PT foaming.
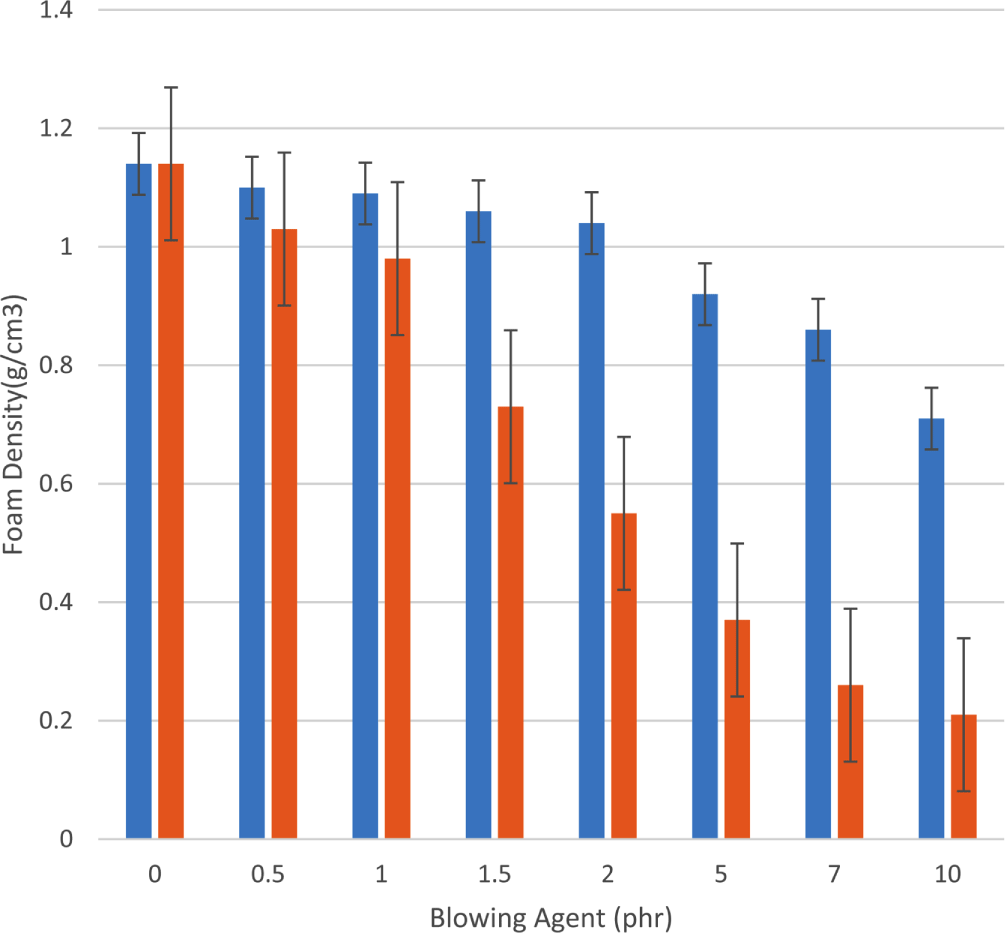
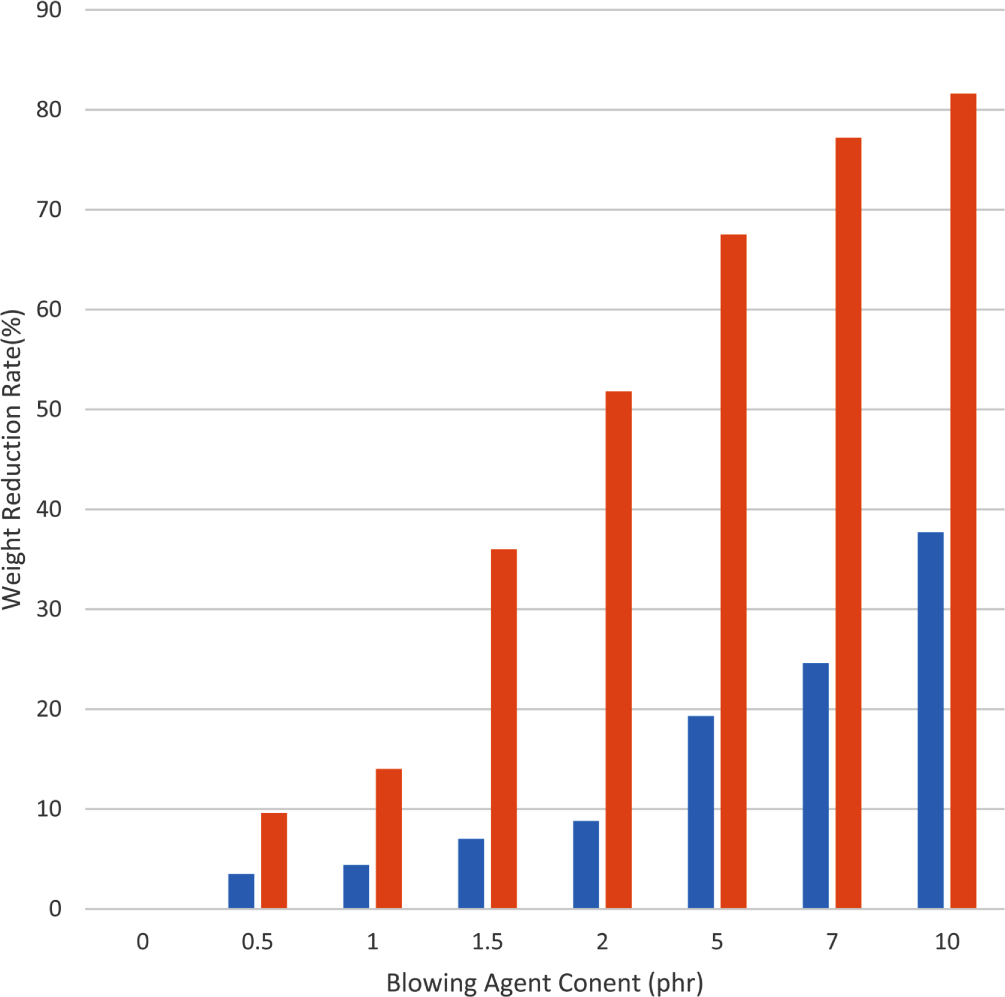
In the case of injection and extrusion of linear polymers such as polypropylene and polyamide, it has been reported that various physical properties such as abrasion and deformation resistance can be improved by increasing the crystallization rate by using various nucleating agents such as Talc.8 However, it was very difficult to find a study showing the effect of the nucleating agent on the foaming properties (density and weight reduction rate of foam). Therefore, in this study, in order to investigate the effect of the nucleating agent on the foaming of polyamide Nylon 6, foam samples of NFt1.5 and NFt2.0 were prepared where the talc concentration of the nucleating agent was changed from 0.1 to 0.4 phr. Changes in the density and weight reduction rate of the foam are shown in Figure 4 and Figure 5, respectively. From the increase in density and the decrease in weight loss rate (%), it was found that the foam forming ability was lowered when a nucleating agent was used compared to the sample without using a nucleating agent. However, in both samples, it was found that when the concentration of the nucleating agent Talc was 0.2 phr or higher, a constant foaming characteristic was exhibited almost regardless of the content of the nucleating agent. It is presumed that the cause of the deterioration in foaming due to the use of the nucleating agent is that the nucleating agent increases the crystallization rate of polyamide, thereby interfering with foaming. Also, from the fact that the rate of change in foaming is almost nonexistent at a Talc concentration of 0.2 phr or more, it can be assumed that 0.2 phr is a sufficient content to act as a nucleating agent.
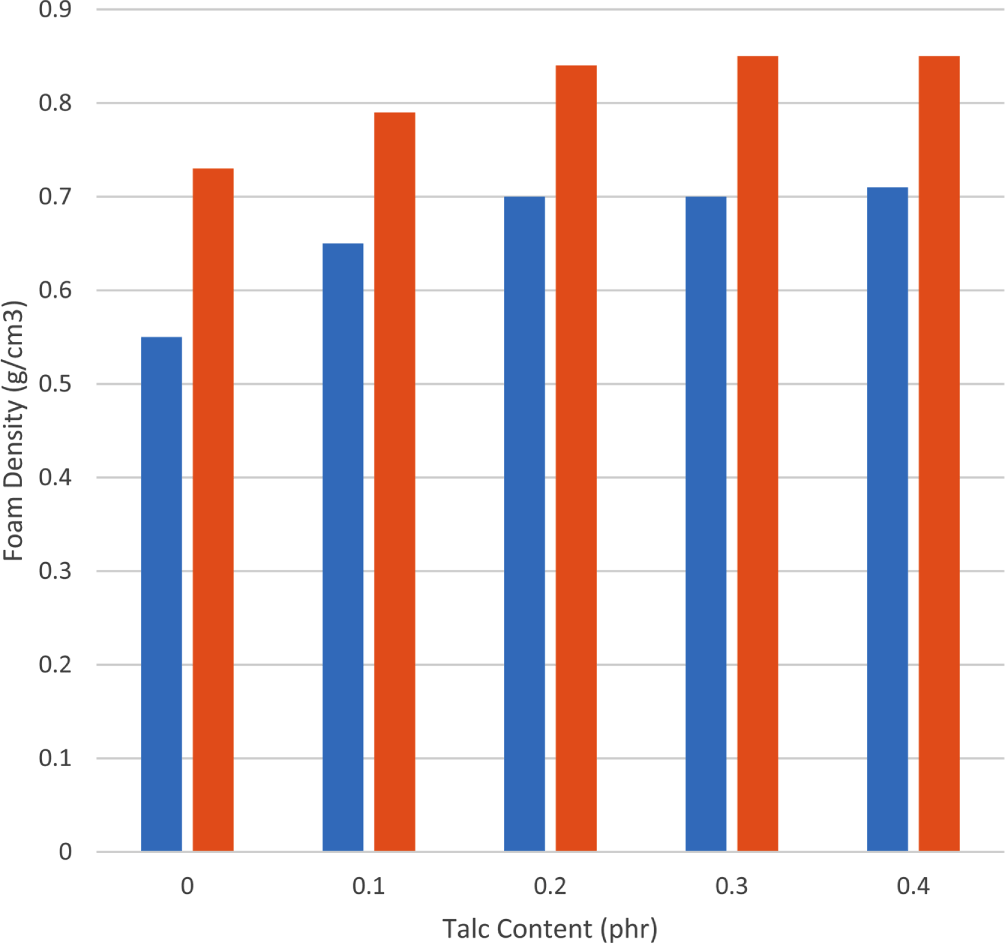
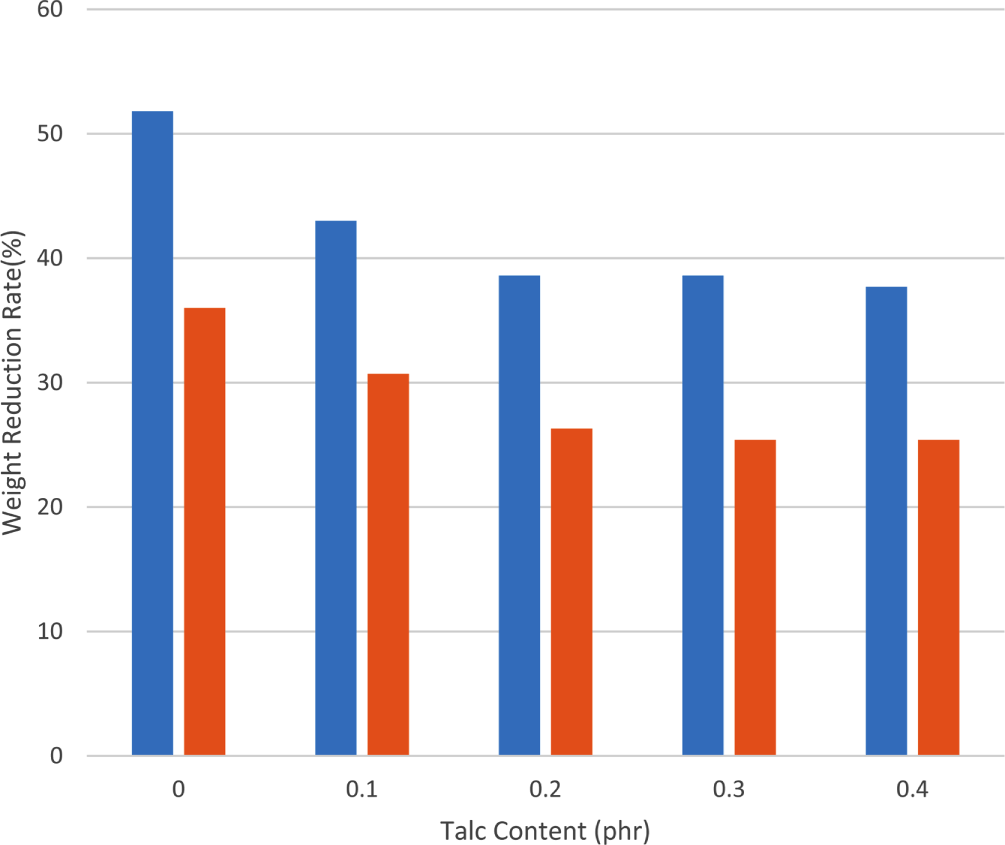
In the foam, the gas phase exists in the cells in the foamed resin. If these cells are connected, it is called an open-cell structure, and if they are independently distributed, it is called a closed-cell structure. Figure 6 shows SEM images of representative samples (NFt1.5 sample and NFt2.0 sample). In Figure 6, Nylon 6 foam has a closed cell structure, and the cell size varies from 20 μm to 120 μm, and the average cell size is about 60 μm. The cell distribution of the sample (NFt2.0) with a high blowing agent content was slightly higher than that of NFt1.5.
Conclusions
Nylon 6 resin was foamed using high-temperature blowing agents PTSS and 5-PT (0-10 phr) without any other additives, and the effect of the blowing agent content on the foaming characteristics (density and weight reduction rate) of the foam was investigated. It was found that the blowing agent 5-PT exhibited better foaming performance than PTSS In the case of 5-PT, when the blowing agent content was 10 phr, the density of the foam was very low at 0.21 g/cm3, and the weight reduction rate was about 82%. In the case of 5-PT, it was found that as the content of the blowing agent increased up to 2 phr, the density of the foam rapidly decreased, and at more than 2 phr, the density of the foam gradually decreased. It was found that the sample with a blowing agent content of 2.0 phr had a foam density of 0.55 g/cm3 and a weight reduction rate of about 52%, indicating excellent foam formation. In addition, the effect of adding nucleating agent Talc content (0.1, 0.2, 0.3 and 0.4 phr) to the samples (NFT1.5 and NFT2.0) on the foaming properties was investigated. It was found that the nucleating agent reduced the foaming properties. Engineering polymers with reduced weight are required for the applications such as automobiles and aircraft parts. This study shows 5-PT can be a good candidate as a blowing agent to effectively reduce the weight of Nylon 6 material.