Introduction
Since the 1990s, portable mining equipment has been widely used due to the mechanization of coal equipment. Because portable equipment is supplied with electricity through high-voltage cables, these cables play a lifeline in the electric distribution system of mining equipment. Even in today’s mining equipment, which has been technically advanced compared to the past, the role of high-voltage cables to supply electricity is very important. The mining cable consists of a polymer insulating layer surrounding each conductor to prevent current leakage and a jacket covering all the conductors finally. Mining equipment used in the coal mining and mineral mining industries works in harsh environments with sharp stones or other obstacles and dangerous environments with flammable material such as coal and methane gas. If the cable’s jacket is damaged in such a dangerous environment, the insulation performance cannot be achieved, so coal powder or combustible dust accumulated on the cable surface can be ignited by electric sparks or fire sparks, causing a major accident. In particular, since the jacket of the mining cable is always exposed to harsh physical deformation such as bending, friction, compression, and elongation, it is necessary to secure various mechanical properties including tear strength of the jacket material to maintain the durability of the jacket.1,2
In this study, silica filled chloroprene rubber (CR) compound, which are mainly used as cable jacket materials for mining, were prepared by melt mixing method with three different types of silica, having same particle size and different structure. Cure characteristic, mechanical properties and tear strength of CR compound according to the type and content of silica were investigated. Tear strength was evaluated using two standard test method of ASTM D470 and DIN VDE 0472-613, and the findings were compared.
Experimental
Chloroprene rubber (CR, DCR-42A, Mooney viscosity: 35.0-55.0 MU) of Denka Company Limited was used. Three different types of silica having same particle size and different structure was used as reinforcing fillers, they include: VN3 (ULTRASIL VN3, Evonik), Z175 (Zeosil 175, Solvay), and U7000 (ULTRASIL 7000GR, Evonik). The particle size and structure of the silica fillers were determined based on N2 adsorption (m2/g) and dibutyl phthalate (DBP) absorption (ml/100g), respectively. Table 1 show the N2 adsorption and DBP absorption for the three types of silica used in this study. And MnO served as the curing agent, while Si-69 was used as the silane coupling agent. The other compounding ingredients were zinc oxide (ZnO), 2,2'-Benzothiazyl disulfide (DM), Ethylene Thiourea (NA-22) and paraffin wax.
Silica type | VN3 | Z175 | U7000 |
---|---|---|---|
N2 (m2/g) | 161 | 165 | 167 |
DBP (ml/100g) | 182 | 207 | 250 |
Table 2 shows the recipe for the CR rubber compounds. The mixing of CR was carried out in a Banbury mixer (NamYang Enterprise Co. Ltd., Korea) for 30 seconds at 60°C. Silica, Si-69 and paraffin wax were sequentially added and mixed for 12 minutes. The curing agent, accelerator (ZnO, N-22) and DM were blended into master batches using a two roll mill (DS-1500R, WITHLAB Co. Ltd., Korea) for 20 minutes. The cure time (T90) was determined using a cure rheometer (Oscillating rheometer, ODR, AlphaTechnology, UK) at 170°C, and the rubber specimens were finally cured using a hydraulic press (CMV50H-15-CLPX, Carver, Inc., USA) at 170°C on pressure of 25 tons for T90. The cured rubber specimens were cut into standard sizes and dimensions for further characterizations.
3. Characterization
To confirm the cure characteristics of CR compounds, it was carried out according to the ASTM D2084 test method using a cure rheometer at 170°C. The maximum torque (MH), minimum torque (ML), the difference between MH and ML (ΔM), TS2 (min), T90 (min) and CRI (Cure rate index, 100/ (t90-ts2)) were determined from the cure curves.
Hardness measurements were made 10 times for one specimen based on ASTM D2240-97 using a Shore A-type hardness meter (Asker, Kobunshi Keiki Co., Ltd), and the average value was calculated.
Tensile properties were measured according to ASTM D412 using a Universal Testing Machines (LLOYD Instrument). Dumbbell shaped specimens were prepared from the molded sheets of the samples. The experiment was carried out at a cross-head speed of 500 mm/min at room temperature. Six samples have been taken for each compound, and the average value was reported. Tensile strength, modulus and elongation at break determined from the stress-strain curve.
Tear strength (Gc) was measured by two standard test methods, ASTM D470 and DIN VDE 0472-613, and a schematic representation of the test methods are shown in Figure 1. In the ASTM D470 and DIN VDE 0472-613 test method, a pre-cut was applied to the center of the specimen to induce the progression of crack. The tear strength (Gc) measured from the ASTM D470 method was calculated through the highest tearing force (F) is divided by the sample thickness (t), Gc = F/t.
In the case of DIN VDE 0472-613 test method, a cotton cloth strip was attached on both sides of the samples by the compression molding to prevent elongation and a cross-head speed was changed to 5 mm/min. The crack route was resetup by using a knife, when the crack has followed a non-linear route during the tearing of samples. The graph of measured tearing force was formed saw-tooth shape and an average of tear force (F) was calculated using maximum and minimum values of saw-tooth. The tear strength (Gc) was calculated through an average tearing force (F) is divided by the sample thickness (t), Gc = 2F/t.
Results and Discussion
Figure 2 shows the cure characteristics according to silica type and content, and is summarized in Table 3. The optimum cure time (T90) increased and CRI decreased as the silica content increased, due to the silanol group on the surface of silica. Cure accelerator was adsorbed by silanol group resulting in reduced the effective accelerator effect.3 The difference between the minimum torque ML value and the maximum torque MH value (ΔM) showed a tendency to increase with increasing silica content.
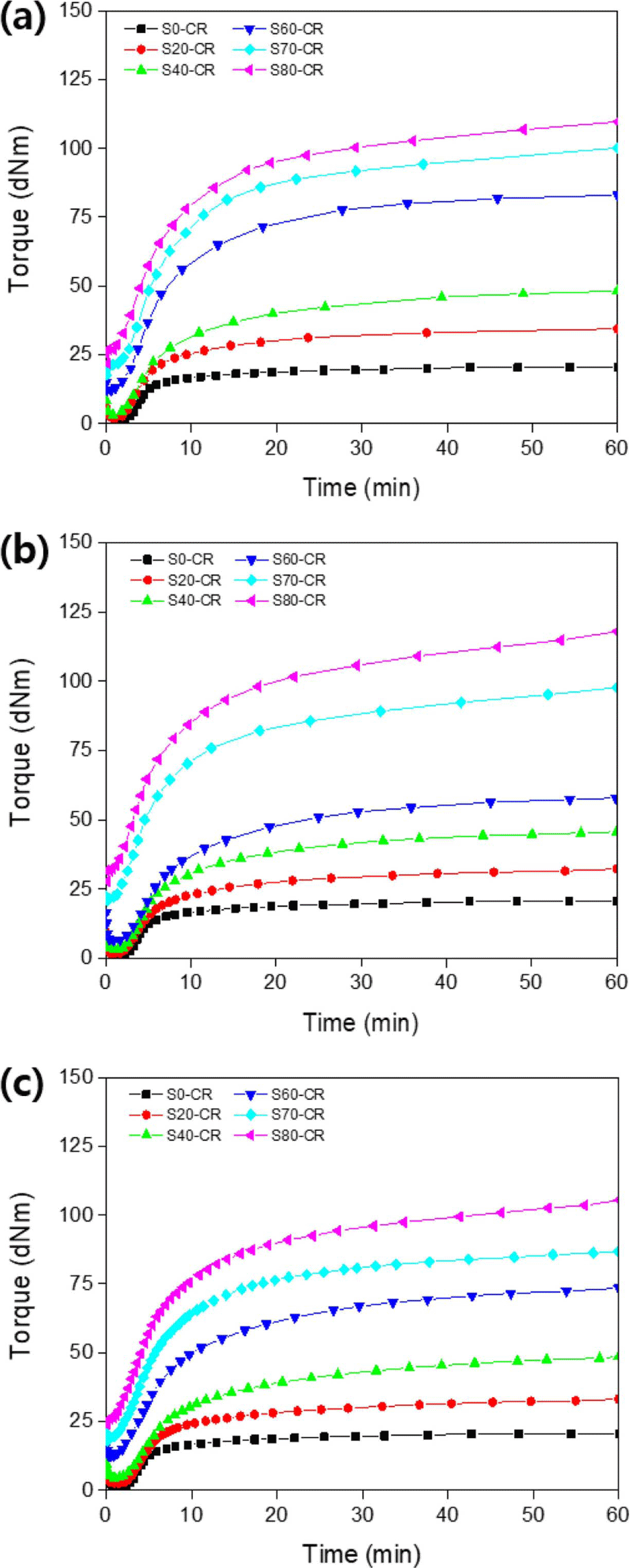
To confirm the silica reinforcing effect using crosslinking properties, the reinforcing factor (αf) was defined4,5 as shown in Equation (1).
Here, Mi, M∞ is minimum and maximum torque of the filled rubber compounds, , is minimum and maximum torque of the un-filled rubber compounds, and ωf, ωr is filler and polymer mass in the compounds, respectively.
Reinforcing factor of three types of silica was shown in Figure 3. As the silica content increased, the αf value increased and it showed a rapid increase at 20 phr of silica content, especially. The highly surface energy of polar silica surface causes a secondary structure and it seems that resulting in increase the value of αf. That is, it can be regarded as the Payne effect indicated filler-filler interaction.6-9 Secondary structural bonds are known to be strong enough not to be easily destroyed by the oscillating shear strain of the rheometer.10-12 The αf values of the three types of silica were similar at the same content, i.e., considering the experimental error, there was no difference of the reinforcement effect according to the degree of structural development of silica.
Hardness, 10% modulus, tensile strength, and elongation at break according to silica type and content are shown in Figure 4. As the content of silica increased, hardness and modulus increased, while elongation at break decreased. In the case of tensile strength, it showed a typical behavior that increases as the silica content increases and then decreases after reaching the maximum value. Especially, U7000, which has a high structural development, showed the best reinforcing effect. It seems to be due to the increase in the formation of bound rubber between the rubber and silica result from the high structural development of U7000.
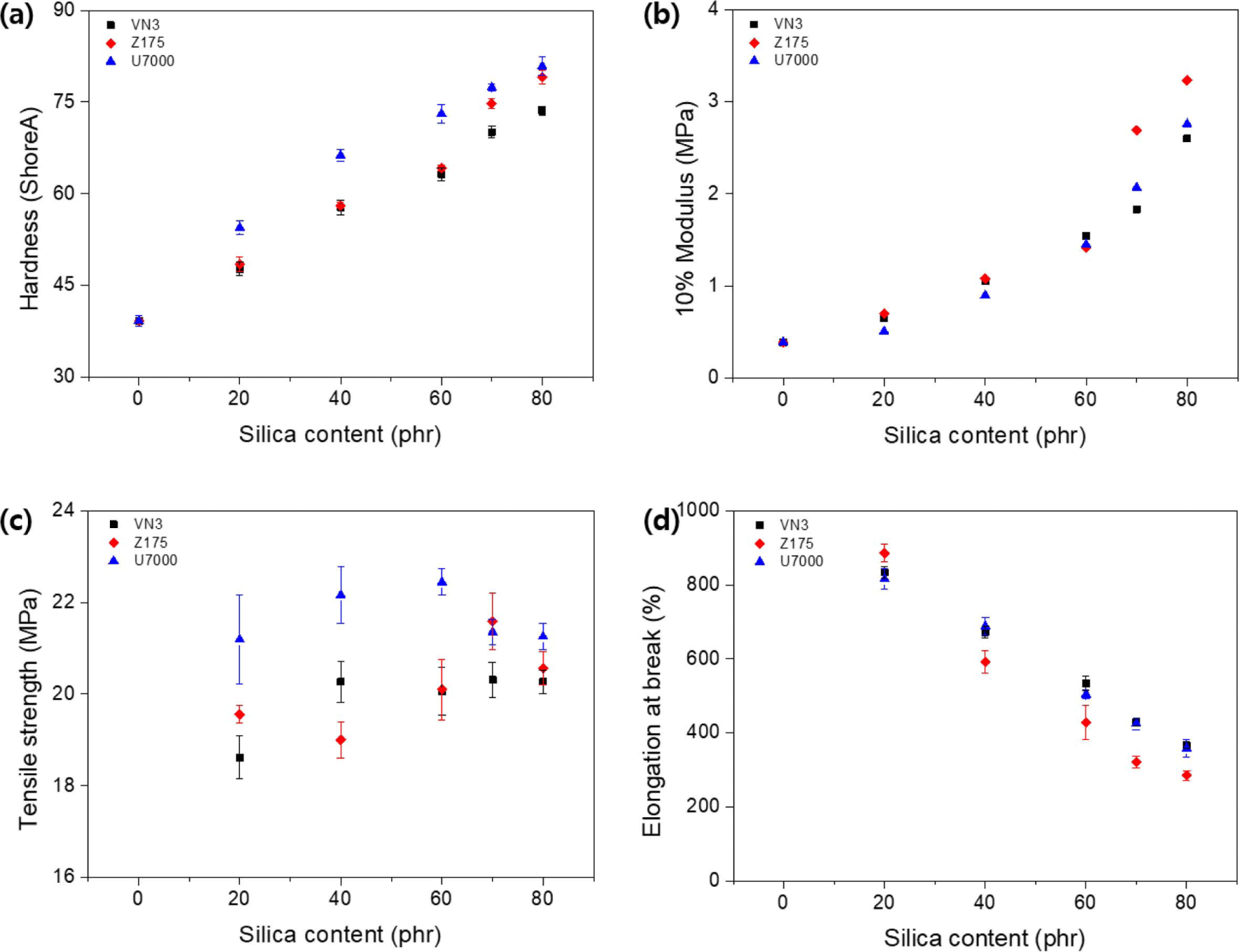
The reinforcing effect of filler can be predicted by various predictive equation model that represent the modulus ratio (Ef/Eu) of unfilled rubber and filled rubber as a function of the volume fraction (Φ) of the filler. Smallwood-Einstein,13 Guth-Gold14 and Thomas7 equation model were represented in equation (1), (2) and (3), respectively, and reinforcing behavior for 10% modulus of silica filled CR compounds was compared with that equations (Figure 5).
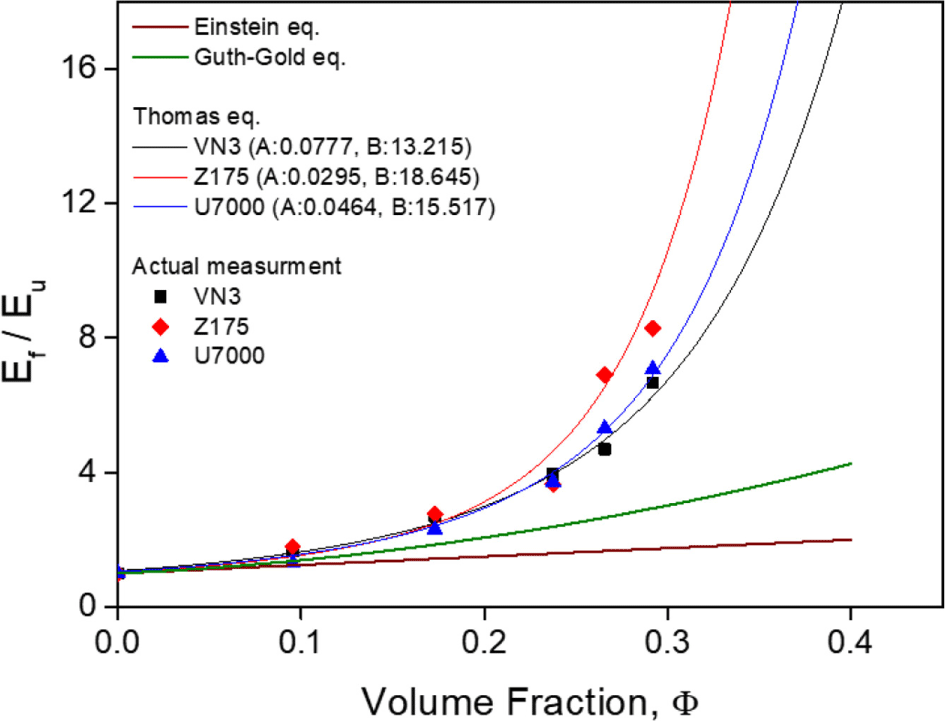
Here, Ef is 10% modulus of silica filled rubber compound, Eu is 10% modulus of unfilled rubber compound and Φ is volume fraction of silica. Reinforcing behavior of silica filled CR compound according to silica type and content showed the best fit with Thomas equation, which is more effective at high filler content. The modulus of Z175 and U7000 having a high structural development were slightly increase than VN3. Therefore, it seems that the degree of structure development of silica affects the modulus of the CR compound.
The tear strength of CR compound evaluated by the standard test method of ASTM D470 and DIN VDE 0472-613 are shown in Figures 6 (a) and 6 (b), respectively. As the silica content increased, the tearing force (N) and the tear strength (Gc) measured based on ASTM D470 and DIN VDE 0472-613 standard. The tear strength, measured using ASTM D470 standard method, increased with increasing silica contents until 70 phr, and U7000 having a high structural development showed higher improvement of the tear strength compared to Z175 and VN3 (Figure 6-a). In the case of ASTM D470 standard method, 7 N/mm of tear strength is generally required to be applied to the jacket material of mining cables.15 To achieve this requirement level of tear strength for CR compound, 40 phr of U7000 is required, while 50-60 phr for Z175 and VN3. The tear strength, evaluated by DIN VDE 0472-613 standard method, increased as the silica content increased, but it decreased above 60 phr of silica content. Especially, tear strength of Z175 filled CR compound rapidly decreased to a level similar to that of the unfilled CR compound at 80 phr. In the case of DIN VDE 0472-613 standard method, 30 N/mm of tear strength is generally required to be applied to the jacket material of mining cables.15 To satisfied this level of requirement for silica filled CR compound, 20 phr of silica content is required regardless of the type of silica.
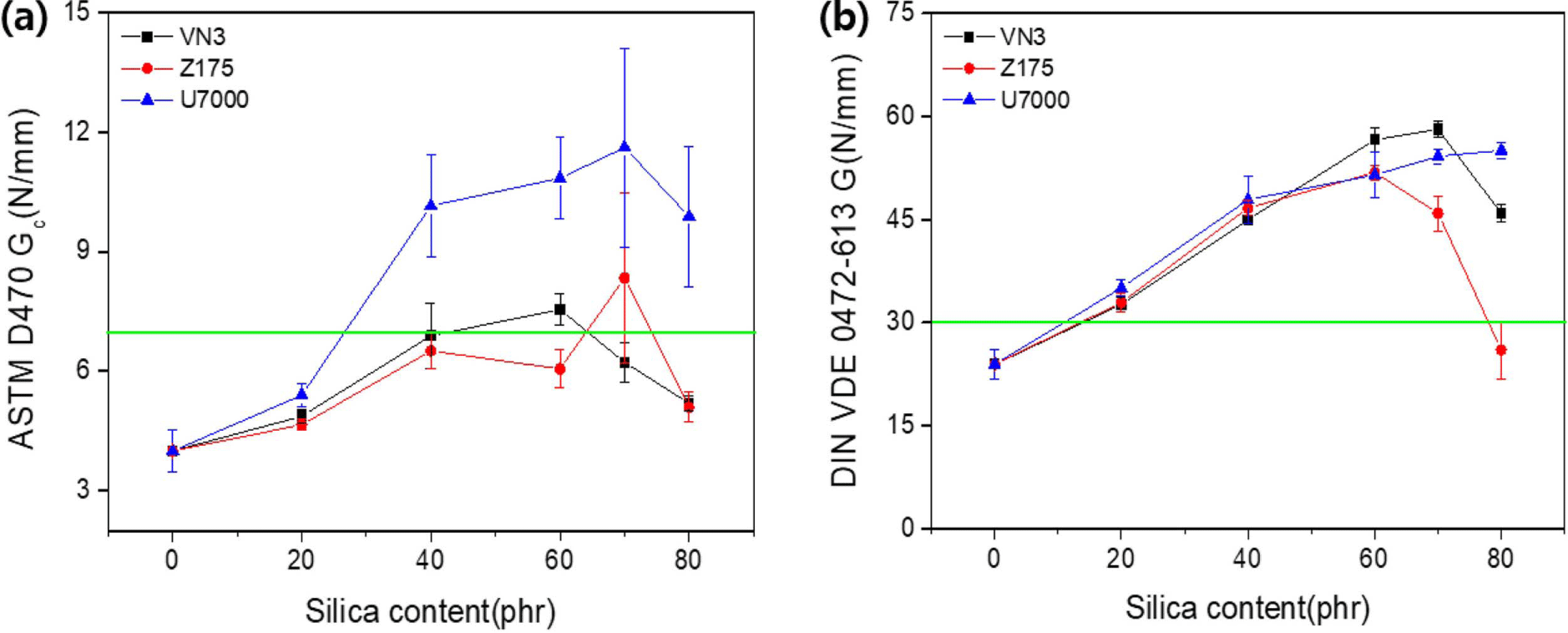
It is important to confirm the correlation between ASTM D470 and DIN VDE 0472-613 standard test method, because a considerable difference between the tear strength evaluated by these two standard test methods was observed. Figure 7 shows the correlation between the tear strength obtained by ASTM D470 and DIN VDE 0472-613 standard test method, which named as Gc (ASTM) and Gc (DIN), respectively. It was observed that a linear relationship with a coefficient of determination (R2) value of 0.88 between Gc (ASTM) and Gc (DIN), as shown in equation (5).
Considering the equation used in each experimental method, it was expected that Gc(= 2F/t, DIN) would be twice as high as Gc(= 2F/t, ASTM), but it showed a difference of about 5 times according to the correlation analysis. The requirement level of tear strength to be applied to the jacket material of mining cables is 7 N/mm for ASTM D470 and 30 N/mm for DIN VDE 0472-613, indicating a 4.3 times difference quite similar to the correlation of tear strength investigated in this study.
Conclusions
In this study, to confirm the effect of the type and content of silica on the mechanical and tear properties of CR compound, silica filled CR compound were prepared with three different types of silica having same particle size and different structure. Cure characteristic, mechanical properties and tear strength of CR compound according to the type and content of silica were investigated. Tear strength was evaluated using two standard test method of ASTM D470 and DIN VDE 0472-613. The crosslinking density (ΔM) and the reinforcing factor (αf) defined using cure characteristics increased with increasing silica content, due to a secondary structure formed by the filler-filler interaction of silica. Whereas, cure rate decreased as the silica content increased because cure accelerator was adsorbed by silanol group of silica surface. Hardness, tensile strength and modulus of the CR compound increased depending on the silica content and high structural development. It was confirmed that reinforcing behavior of silica filled CR compound according to silica type and content showed the best fit with Thomas equation that represent the modulus ratio (Ef/Eu) of unfilled rubber and filled rubber as a function of the volume fraction (Φ) of the filler. Tear strength increased as the silica content increased regardless of the test method. In the case of ASTM D470 standard method, U7000 having a high structural development showed higher improvement of the tear strength compared to Z175 and VN3, while there was no considerable difference of tear strength according to the degree of structural development of silica for DIN VDE 0472-613 standard method. It was found that tear strength obtained by ASTM D470 and DIN VDE 0472-613 standard test method showed a linear relationship with each other indicating a high correlation. The mechanical properties and tear strength of silica filled CR compound was improved as higher silica content and the silica structure became intricate. Therefore, it’s expect that CR compound filled with high content and high structural development of silica can be applied to the jacket material of mining cables used in a harsher environment.