Introduction
As the world intensifies its focus on climate change and environmental concerns, there is a growing interest in environmental regulations and the adoption of “eco-friendly” practices. Plastic, a fundamental material in our economy and daily lives, faces challenges associated with climate change and environmental impact resulting from excessive use and landfill disposal.1 The majority of frequently used synthetic polymers, such as polypropylene (PP), polyethylene (PE), polyethylene terephthalate (PET), and polyester (PS), are produced from petroleum-derived hydrocarbon monomers, which are made with high levels of greenhouse gas emissions.2 A promising solution to replace fossil fuel-based plastics, known for their contribution to global warming and environmental pollution, is the emergence of bio-based plastics.3 The term “bio-based” denotes materials or products derived (partly) from biomass.4 Biomass growth involves the consumption of CO2 through photosynthesis and its conversion back into biomass. Consequently, bioplastics offer the advantage of being eco-friendly with a lower carbon footprint compared to petroleum plastics, aligning with the concept of “carbon neutrality.”
Polyolefins for automobile parts are gaining significant attention in the automobile industry due to their superiority in processability, lightweight, and relatively low fuel consumption, and thus, their uses are increasing. Considering these perspectives, polyethylene (PE) and polypropylene (PP), which have a wide application range and low cost, are two common polyolefins that are widely used. Not only polyolefins, polyolefin-based composites and blends are also extensively used in bumpers and automotive interior trim.5-6 However, plastic manufacturing processes still suffer major challenges concerning environmental and energy issues.7 To tackle these challenges, bio-based plastic composites have emerged, nowadays.8 For instance, thanks to their reproducibility, low cost, high strength, and rigidity, poly(lactic acid)-based (PLA-based) composite materials are extensively researched and find their use in automotive applications. As PLA is derived from corn starch, it exhibits a huge potential to reduce the environmental impact of greenhouse gases.9-12 In addition, bio-polyethylene (bio-PE) is also a commercial bio-based plastic and finds suitable applications in food packaging, cosmetics, and automotive. Recently, researchers have been fabricating bio-based PE composites with fascinating mechanical, thermal, and aging properties.13-15 Nevertheless, the major components of automotive parts are PP-based, which are mainly petroleum-sourced. Very recently, bio-PP has been developed,13-16 but bio-PP-based composites are very rarely researched for automotive applications. The environmental issues associated with petroleum-based PP have prompted the exploration of bio-polypropylene (bio-PP) as a viable solution. Bio-PP can be derived from biological resources through subsequent polymerization, utilizing resources obtained from glucose by the butylene dehydration of bio-iso-butanol16. Despite its environmental benefits, the major drawback of bio-PP, similar to other bio-based plastics, is its high cost.17
Despite their superior functionality and economic concern, these bio-plastics still face similar environmental issues since the degradability of a polymer is reliant on its chemical structure. In this perspective, biocomposites are regarded as a viable alternative to both challenges. From the filler perspective, talc is an extensively used reinforcing agent in the PP matrix to enhance thermal, mechanical, and other physical properties.18-20 Talc has predominant hydrophobic surface chemistry, leading to poor wettability and dispersion in aqueous medium but a reduced dispersant request when used in the polymer matrix. Moreover, from the processing point of view, extrusion is a well-established method for efficiently producing polymer blends and composites.
In this study, the main objective was to produce bio-PP-based composites that optimize cost without compromising its mechanical properties. Thus, in this work, the extrusion process was employed to prepare different bio-PP composites with talc. To mitigate the cost of bio-PP and compare several properties, we considered two types of current PP, one of which had identical physical properties to bio-PP. Then, we prepared different polymeric blends and composites with current PP and bio-PP to demonstrate their thermal, mechanical, rheological, and morphological properties.
Materials and Methods
For the preparation of bio-PP-based composites, bio-PP (CirculenRenew C14 EP448T) was purchased from Lyondell Basell Industries. It has a density of 0.90 g/cm3, a melt flow rate, MFR (230°C, 2.16 kg) of 48 g/10 min. It is worth mentioning here that the bio-PP consists of a biomass content of 49%. The current PP, PP1 (Moplen EP448T), with the same grade, was purchased from the same organization. It has the same density and MFR of bio-PP. For the comparison with Moplen EP448T, another current PP, PP2 (CB5230), was purchased from Yuhwa Korea Petrochemical Ind., Seoul, Korea. It has a density of 0.91 g/cm3, MFR (230°C, 2.16 kg) of 30 g/10 min. Talc was used as a filler purchased from KOCH CO., Ltd., Seocheon, Korea.
First, bio-PP, talc, and two types of PP were dried overnight in an oven at 70°C before processing. Then, different blends of bio-PP and current PP were prepared by taking the bio-PP in specific amounts so that the biomass content in the blend becomes 5, 10, 20, 25, and 30 wt%. For the blend preparation, the dried polymers were premixed individually, and then, the polymer mixtures were compounded by a corotating twin screw extruder (BA-19, BauTek). The different proportions of bio-PP and current PP for the blends were taken as given in Table 1. On comparing physical properties, the PP1 and bio-PP of the same grade showed no significant difference, so talc was added to the commercially used PP2 to improve its properties. The recipe of the composites was followed, as shown in Table 2. To prepare the composites, a required amount of bio-PP was taken at a definite talc content so that the biomass content varies in 5, 20, and 30 wt%. The rotational speed of the screw was maintained at 240 rpm. The temperature from hopper to die was maintained at 170, 170, 170, 175, 175, 180, and 180°C. Then, the extruded blends and composites were cooled in a water bath and pelletized. After pelletization, the blends and composites were injection-molded by an injection-molding machine (WL-HV-80, Wonil Hydraulic). During molding, the temperature from hopper to nozzle was kept at 175, 210, 220, and 220°C. Finally, the molded samples were used for different characterizations.
Biomass content (wt%) | 5 | 10 | 20 | 25 | 30 |
---|---|---|---|---|---|
Bio-PP (wt%) | 10.2 | 20.4 | 41.0 | 51.0 | 61.2 |
PP1/PP2 (wt%) | 89.8 | 79.6 | 59.0 | 49.0 | 38.8 |
Characterizations
The thermogravimetric analysis (TGA) was performed using a TA Instruments TGA55 (New Castle, DE, USA) under a nitrogen atmosphere from room temperature to 600°C at a heating rate of 10°C/min. The differential scanning calorimetric (DSC) analysis was carried out by TA Instruments DSC Q20 (New Castle, DE, USA), under a nitrogen atmosphere at 10°C/min heating rate from 30 to 220°C. The melting temperature (Tm) was chosen as the inflection point from the heating curve. The crystallization temperature (Tc) was selected as the inflection point from the cooling curve.
The tensile properties were measured by Myungji Tech Tensometer 2000 (Yongsan, Korea) at a crosshead speed of 50 mm/min. The thickness of the specimens was kept at 3.2 ± 0.1 mm (ASTM D638 type 4).
The impact strength was measured by WITHLAB Co., Ltd., Izod Impact Tester WL2200D (Gunpo, Korea) at room temperature, notched (ASTM D256).
The specific gravity was measured by DPL Corp., DME-220E (Geumcheon, Koea) at room temperature (ASTM D792).
The MFI was obtained from WITHLAB Co., Ltd., Melt Flow Indexer WL1400 (Gunpo, Korea) at 230°C, 2.16 kg (ASTM D1238).
Results and Discussion
The thermal stability of a polymeric material is one of the most vital properties at elevated temperatures. It depends on the intrinsic properties of the samples as well as the interactions between the different macromolecules and nanomaterials. Typical thermogravimetric curves of neat bio-PP, PP1, and PP2 have been given in Figure 1a, Figure 1b and Figure 1c represent the TGA curves of the bio-PP/PP1 and bio-PP/PP2 blends, respectively. Figures 1d, e, and f represent the weight loss curve of the PP2-based bio-composites at different talc contents where the biomass contents are 5, 20, and 30 wt%, respectively. All the curves show one-step degradation, which is characteristic of the random radical scission mechanism of polyolefin’s degradation.21 Usually, the initial degradation temperature has been used to determine the thermal stability of the polymeric system. However, it is observed that for the bio-composites, the thermal stabilities remain unchanged after the addition of talc. This could be explained by the addition of the unorientation of talc in the composite system.22 However, the degradation temperature of pure PP and bio-PP composites is 410°C. DSC was studied to examine the possible changes in the melting and crystallization temperature of the bio-PP, PP1, PP2, and different blends and composites, as shown in Figure 2. Figure 2a shows the heating and cooling curves of different types of PP, displaying an indifferent melting and crystallization point for all the PP used. As shown in Figure 2b and 2c for the blends, the melting temperature remains unaltered at different biomass content. A slight decrease in melting temperature was observed when a specified amount of talc was introduced in the PP systems (Figure 2d-f). The decrement became quite prominent when the biomass content was 30 wt%. However, it is worth mentioning that adding filler does not noticeably influence the PP matrices, as reported elsewhere.23 Both pure PP (PP1 and PP2) and bio-PP composites have a melting point of 165°C. However, as the quantity of talc increased, the crystallization temperature also increased slightly. Generally, the molecular chains of polymer could crystallize by themselves through the self-nucleation effect or by foreign nucleating agents (heterogeneous crystallization). In this case, the increase in crystallization temperature is due to the faster crystallization of polymer chains upon cooling, where talc plays a role as a nucleating agent.
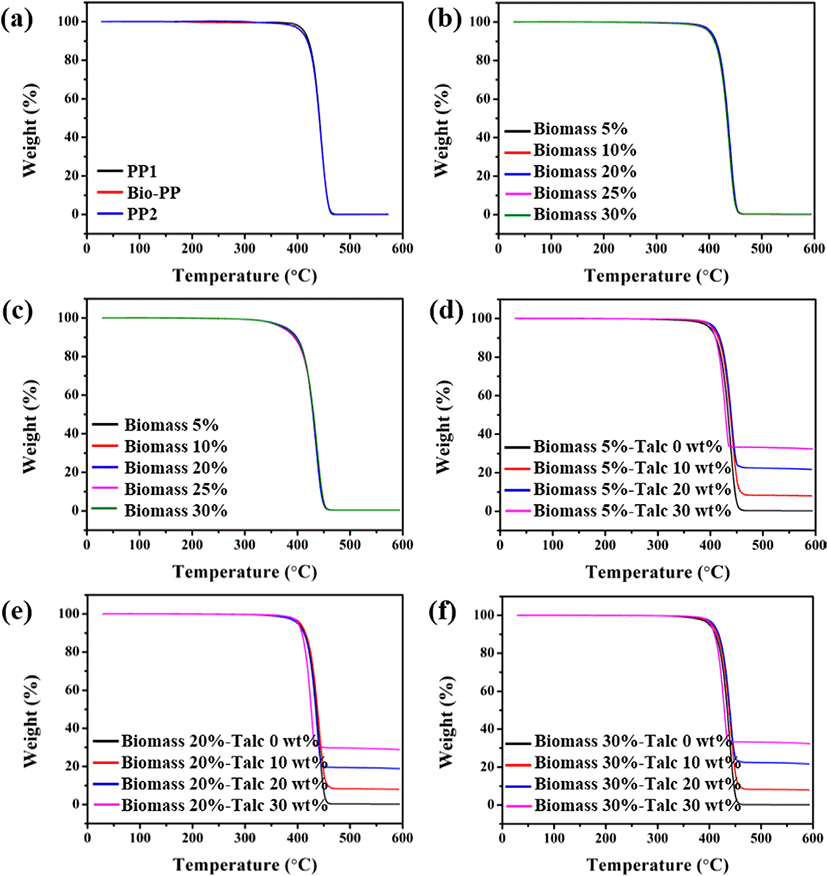
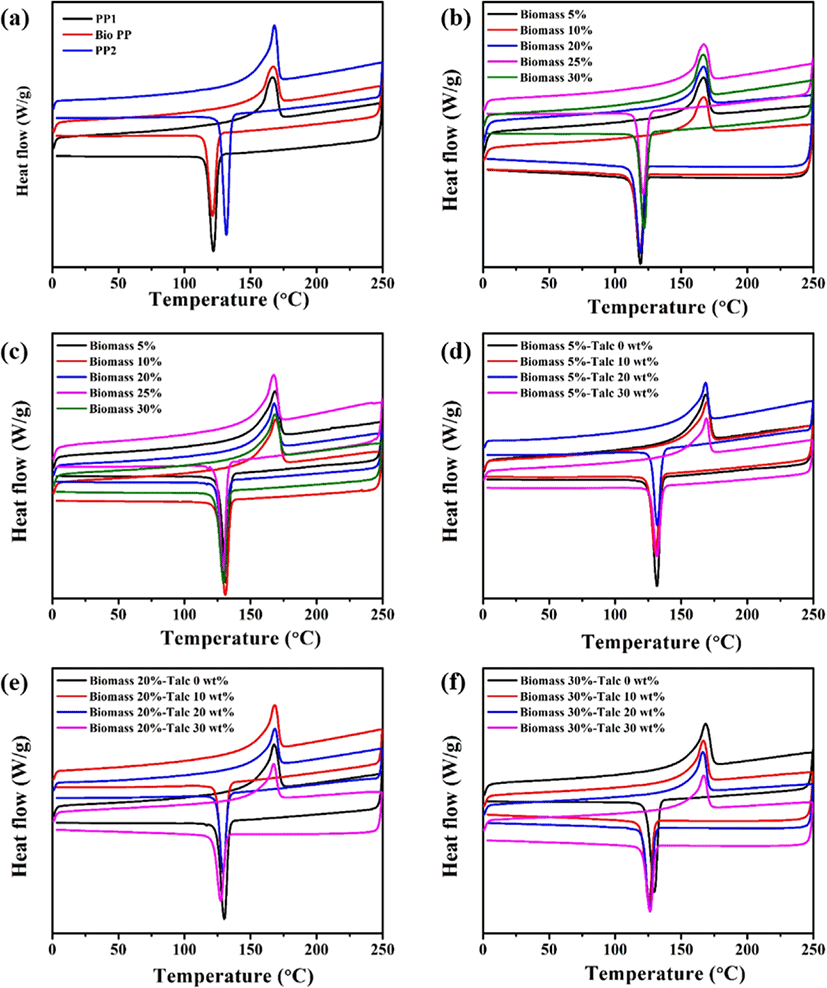
Tensile tests were performed to evaluate the mechanical properties of the bio-PP, PP1, PP2, their blends, and their composites with talc. Figure 3 displays the tensile strength, Young’s modulus, and elongation of the three types of pure PP. The bio-PP and PP1 show a similar tensile strength, Young’s modulus, and elongation at break, but the PP2 exhibited higher tensile strength and Young’s modulus but lower elongation of break than the other two types, as shown in Figure 3a-c. Figure 4a-c shows the mechanical properties of the prepared blends of PP1 and bio-PP. The mechanical properties of blends were expected to lead to similar mechanical properties like bio-PP and PP1, confirming that on mixing bio-PP with PP1, the mechanical properties did not deteriorate. Interestingly, for the blend of PP2 and bio-PP, the tensile strength remains almost constant, whereas Young’s modulus and elongation at break experienced a slight decrement and enhancement than the pure PP2, as observed from Figure 5a-c. The results prove that the blends were mixed well by the extrusion processing at five different biomass contents (5, 10, 20, 25, and 30%).
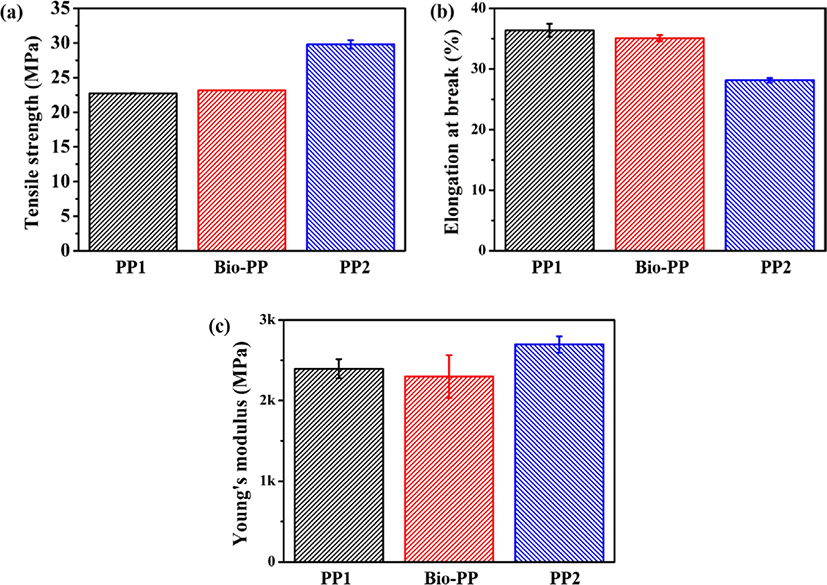
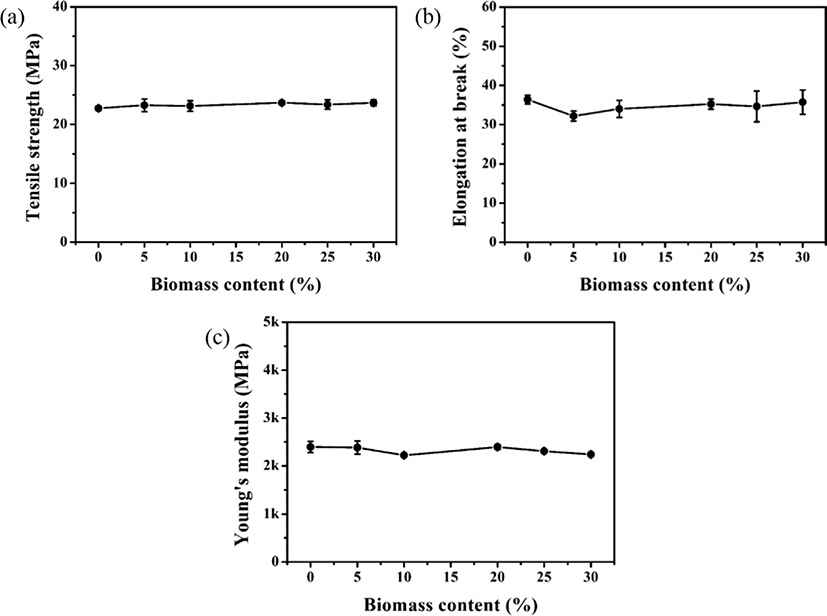
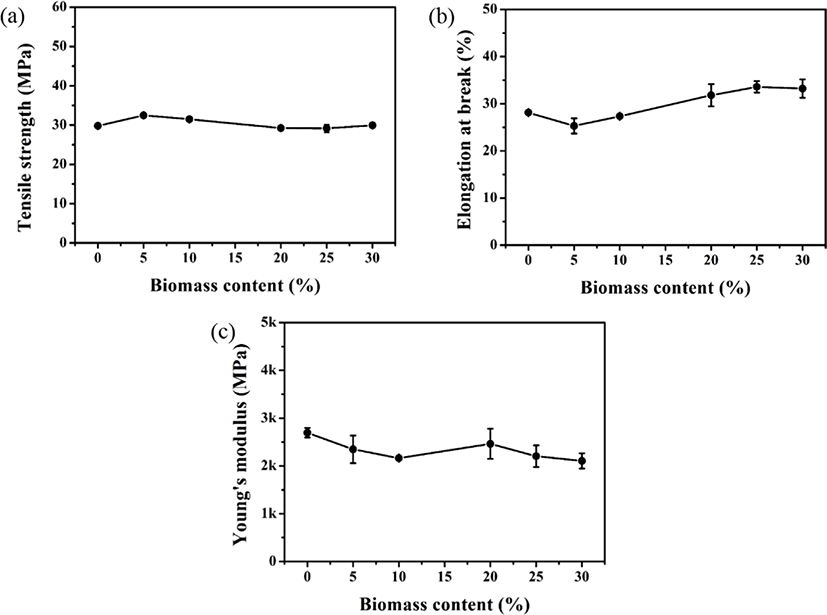
Figures 6a, b, and c show the mechanical properties of the PP2/bio-PP/talc composites with three different biomass contents (5, 20, and 30%) and three different talc contents (10, 20, and 30 wt%). In the case of 5 wt% biomass (Figure 6a), the tensile strength slightly decreased compared to PP2, but at 30 wt% talc, the composite with 5 and 20 wt% biomass exhibited similar values. However, it is worth mentioning that Young’s modulus sharply increased with the talc inclusion and reached a maximum of 10 wt% talc content. After 10 wt% talc content, Young’s modulus becomes constant for all the composites. Although the composites with 5 and 20 wt% biomass exhibited identical Young’s modulus, it decreased when the biomass content increased (30 wt%). The outcomes indicate that the included talc stiffens bio-PP to a lesser extent than PP2. With the variation in talc content, the elongation of break of bio-PP composites follows a decreasing manner. It is well established that when filler talc is used in the polymer matrix, the elongation at the break of composites is reduced to some extent due to its nucleating behavior.24,25 However, it was found that the composite with higher biomass content displayed better elongation properties.
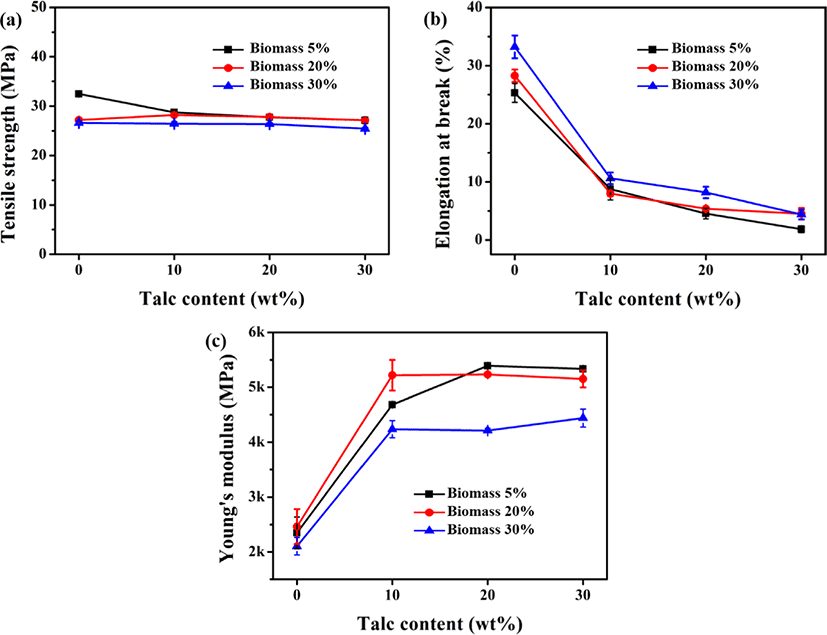
Impact strength is the ability of a material to resist cracking, fracture, or plastic deformation under sudden and intense shock. Understanding the impact behavior of materials is a critical piece of design information that drives material selection where the components are likely to suffer strong impulses. The notched impact strength of different PP, their blends, and composites at different biomass and talc contents are shown in Figure 7. The impact strength of three types of PP shows similar values of 1.5 kJ/m2, as can be seen in Figure 7a. In the case of blends, the impact strength of the PP1/bio-PP exhibited identical values irrespective of biomass content, whereas it was slightly increased for PP2/bio-PP blends with an increase in biomass amount, as depicted in Figure 7b and c, respectively. Interestingly, it was observed that the PP2/ bio-PP/talc composites with three different biomass contents (5, 20, 30%) and three different talc contents (10, 20, 30 wt%) displayed a similar value of the impact strength, as shown in Figure 7d. Generally, including talc in PP is known to increase the modulus while leading to a decreased impact strength.26-29 In our study, we found that there is no change in the impact strength (1.5 kJ/m2) after the addition of talc, with a similar report elsewhere.30 However, it is known to all that the impact strength directly correlates to the filler adhesion to the matrix; a better impact strength can be obtained at lower filler matrix adhesion.31 Thus, creating an identical number of cavities could be the possible reason for the identical impact strength of the composites at different talc loadings.18
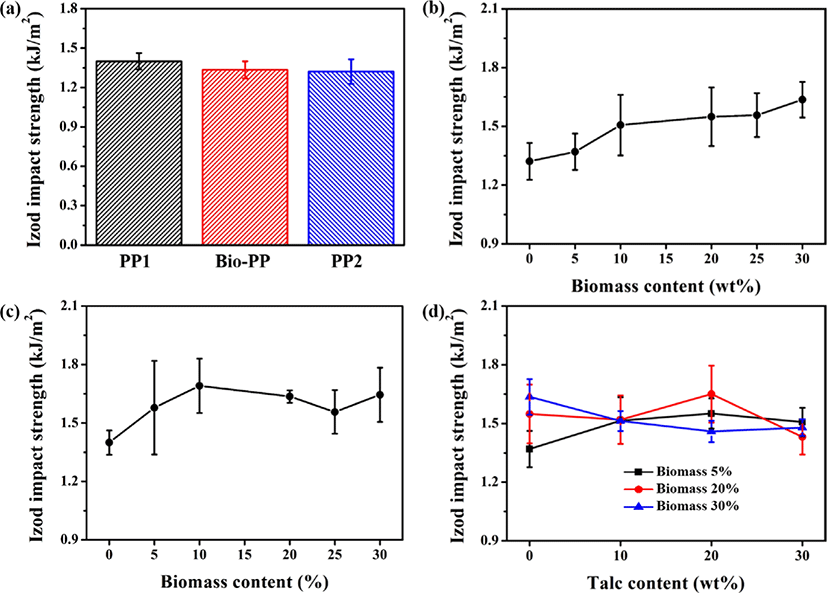
The processability of a polymeric system can be determined from the melt flow index of the system. Figures 8a, b, c, and d show the variation of MFI for different PP, PP1/bio-PP blends, PP2/bio-PP blends, and PP2/bio-PP/talc composites, respectively. For the three types of PP, the obtained MFI are 44.2, 45, and 31.6 g/10 min, as shown in Figure 8a. The MFI of PP1/bio-PP blends exhibited an identical MFI of 45 g/10 min, as shown in Figure 8b. This is due to the fact that the bio-PP and PP were of the same grade. However, the MFI of PP2/bio-PP blends was increased with an increase in biomass content, as shown in Figure 8c. This is because of the fact that the bio-PP has a higher MFI than the PP2. From Figure 8d, it is clear that the addition of talc led to a continuous decrease in the MFI of the composites.30 This is the result of the fact that the incorporation of talc hinders plastic flow and increases the viscosity of the polymer melt, leading to lower MFI.32
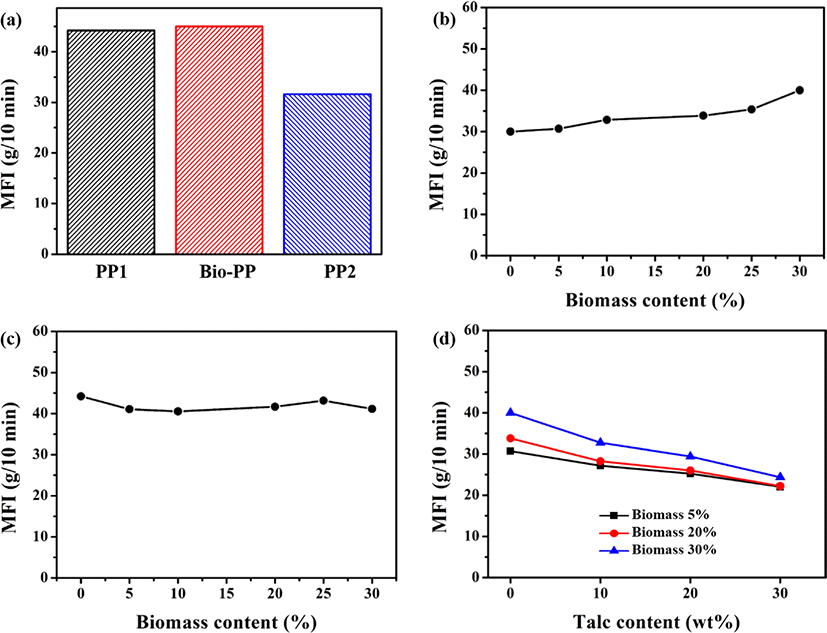
Shear viscosity is crucial for thermally developed flow complications where the temperature, pressure, and velocity in channels continually shift in the flow direction. The shear viscosity range from 0~20,000 s-1 was obtained at 220°C and is presented in a logarithmic plot as a function of shear rate, as shown in Figure 9. The shear viscosity of three different PPs is shown in Figure 9a. The PP2 has a lower MFI and higher shear viscosity, as the bio-PP and PP1 have higher MFI; thus, they display a lower shear viscosity. The PP1/ bio-PP blends exhibited identical shear viscosity at different biomass content, as shown in Figure 9b. In Figure 9c, for PP2/bio-PP, it is observed that as the biomass content increases, the shear viscosity decreases due to the rise in bio-PP content. The variation of shear viscosity with different shear rates of the composites has been provided in Figure 10a-c. The results show an increased shear viscosity with an increase in talc content. At the lower shear rate region, the shear viscosity of the composite with specific biomass shows an increment with an increase in talc content. Notably, the viscosity increases as the filler content increases owing to the fact that adding fillers to a polymer generally restricts molecular motion and creates a resistance in flowing.33 In contrast, we noticed a similar shear viscosity at a higher shear rate, leading to the promising processing of composites under similar conditions.
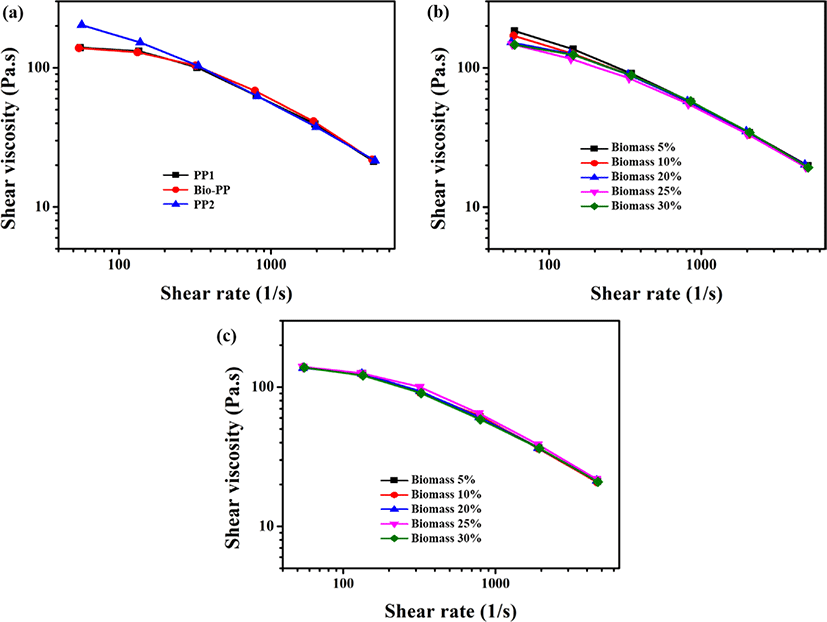
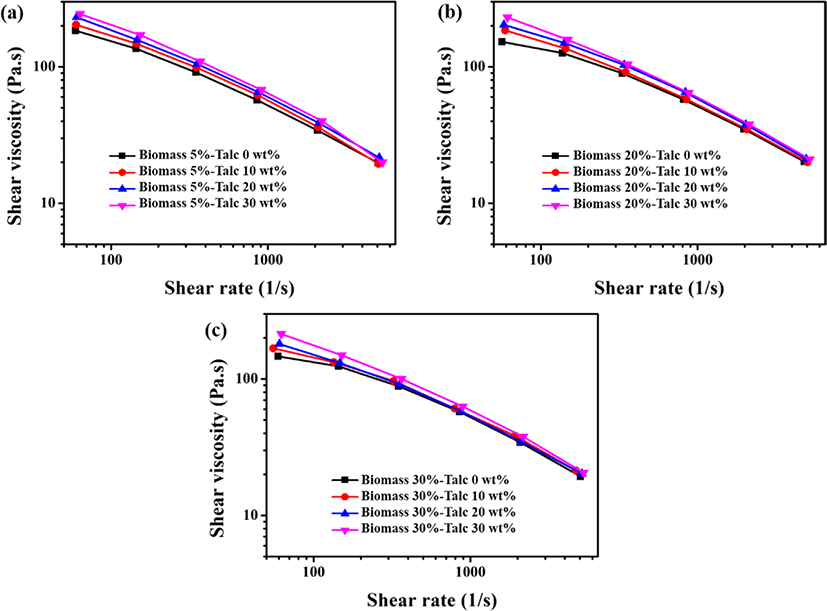
The increasing commercial interest underscores the potential of polymer nanocomposites to revolutionize automotive design, offering a compelling avenue for developing next-generation, high-performance vehicles. These innovative materials demonstrate remarkable mechanical strength and thermal stability improvements without compromising on specific gravity and maintaining optical clarity in certain instances. Polymer nanocomposites-derived components promise enhanced durability and performance and align with the industry’s pursuit of lightweight solutions crucial for fuel efficiency. The specific gravity of bio-PP composites has been provided in Table 3. Table 3 shows that the specific gravity of the bio-composite increases when the talc content is increased at a particular biomass content. This is due to the higher specific gravity of talc than PP, as biomass content does not influence the specific gravity of the composites. However, the maximum specific gravity of 1.16 was found for composite with 5% of biomass and 30% of talc.
Figure 11 illustrates the FESEM micrographs of three kinds of pure PP, their blends, and the prepared talc composites with PP2 at different loadings of talc. Plastic deformation is strongly evident in all the fractured surfaces of these studied specimens. Micrographs of pure PPs and blends (biomass content 20%) show a ductile break with elongated edges at the broken surface. The SEM micrographs of the composites imply the parallel orientation of talc particles, mostly uniform particle size distribution, and the absence of agglomeration.34 It is also evident that as the talc content increases, more talc can be seen rod-shaped on the fractured surface.35 The fractured surface of the composites is gradual and brittle in nature, which complies with the occurrence of fractures at the boundary of PP and talc. Furthermore, fewer cavities adjacent to the particles signify weak bonding between the filler and matrix at higher talc loading, leading to the sacrifice of the strength of the composites.
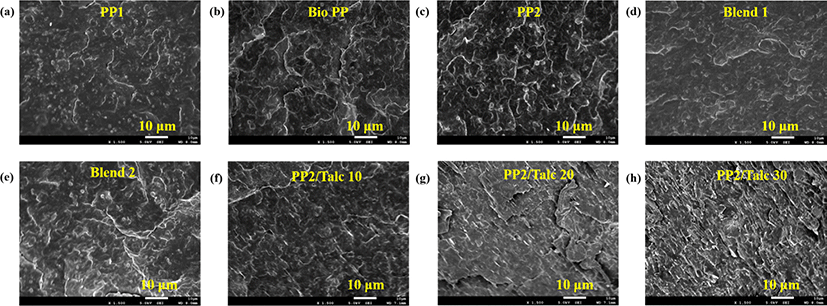
Conclusions
This work reports a comparative study of several prepared blends of bio-PP with current PP of similar and different grades and composites with talc via an extrusion process. The properties of blends showed that the physical properties were not significantly reduced compared to petroleum-based current PP, leading to a promising replacement of it by bio-PP. It was also observed that the tensile strength of the composites (PP2-based) did not show significant differences when biomass and talc contents were different. The moldability of the bio-PP composites is substantiated by comprehensive rheological property assessments. Therefore, it can be summarized that the fabricated bio-PP composites could be an alternative to current PP and current PP-based composites for sustainable automotive applications and so on.