Introduction
The increasing traffic in urban areas has led to increased amounts of air pollutants, automotive industry is conducting research to reduce the generation of particulate matter.1 In the automobile, particulate matter emissions are largely classified into exhaust and non-exhaust emissions. Although various sources of particulate matter contribute to air pollution, the exhaust gases produced by internal combustion engines are one of the main causes of air pollution.2 However, due to the recent strengthening of environmental regulations and the development of electric vehicles, the amount of particulate matter emitted through exhaust is significantly decreasing. Consequently, this has led to a relatively increase in the proportion of particulate matter emission produced from non-exhaust sources, such as break wear particles, tire wear particles, and road surface wear.3,4 Michelin in France reported that 0.17% and 2.2% of tire wear corresponds to particulate matter in the form of PM2.5 and PM10, respectively,5 wherein PM10 represents particles with a diameter of ≤ 10 μm, and PM2.5 represents particles with a diameter of ≤ 2.5 μm. However, despite the low emission of particulate matter from tire wear, the tire industry is continuously conducting efforts to reduce particulate matter emissions in response to the increased emissions resulting from the heavy loading of electric vehicles.6-9
The tires used by automobile are classified as passenger car radial (PCR) tires, light truck radial (LTR) tires, or TBR tires. Among them, TBR tires require a superior wear resistance and fuel efficiency compared to other tires due to their heavy loads and long-distance driving requirements. Thus, NR is used as a base rubber in TBR tire because of its excellent mechanical properties and superior cut & chip properties.10 BR exhibits a low glass transition temperature (Tg) and high elasticity. Additionally, BR has a lower coefficient of friction than NR,11 leading to a reduced friction on rough surfaces.12 Thus, BR is blended to improve wear resistance of compound, and BR/NR blends are commonly used in TBR tires. Furthermore, CB, which exhibits a good affinity with NR and has excellent reinforcement properties, is commonly used as a filler.
Hysteresis loss in rubber occurs due to the random thermal motion at the chain ends, and this ultimately leads to a reduced fuel efficiency in tires.13 However, through the introduction of the functional group corresponding with fillers at the ends of the chains, it is possible to restrict the molecular motion at chain ends to significantly reduce hysteresis loss. Moreover, it can improve the filler dispersion by enhancing filler–rubber interaction, resulting not only in reduced rolling resistance, but also in improved wear resistance. Previous researches have focused on improving the filler dispersion and reducing hysteresis loss at the chain ends by introducing functional groups. Functionalization enhances the interaction between the filler and the rubber, and improve the fuel efficiency.14,15
Thus, in this study, functionalized lithium BR (F-LiBR) with modified chain ends is added to the NR/BR blend compound commonly used in TBR tire treads. Through this, the effect of introducing the functional group can react with CB into BR is investigated with the aim of improving the CB dispersion, enhancing the compound performance, and reducing the generation of particulate matter.
Experimental
NR (Standard Vietnamese Rubber SVR-10, dirty content =0.1 wt%), NdBR-60 (Neodymium-based butadiene rubber, Mooney viscosity (ML1+4, 100°C); 63 MU; Kumho Petro- chemical Co., Daejeon, Korea) and F-LiBR (KBR-810, Mooney viscosity (ML1+4, 100°C); 64 MU; Kumho Petrochemical Co., Daejeon, Korea) were used as the base rubber. The filler was CB (OCI-C, IA: 174 g/kg, OAN: 123 cc/100 g, OCI Company Ltd., Seoul, Korea). TDAE oil (Kukdong Oil & Chemicals Co., Yangsan, Korea) was used as a processing aid. Zinc oxide and stearic acid (Sigma-Aldrich Corp., Seoul, Korea) were used as crosslinking activators. N-(1,3-dimethybutyl)-N′-phenyl-phenylenediamine (6PPD, Kumho Petrochemical Co., Daejeon, Korea) and 2,2,4-trimethyl-1,2-dihydroquinoline (TMQ, Sinopec corp., Beijing, China) were used as antioxidants. Sulfur (Daejung Chemicals & Metals Co., Siheung, Korea) was used as a crosslinking agent, and N-tert-butyl-2-benzothiazyl sulfonamide (TBBS, Shandong Yanggu Huatai Chemical Co., Ltd., Liaocheng, China) was used as the curing activator. N-(Cyclohexylthio) phthalimide (PVI, Shandong Yanggu Huatai Chemical Co., Ltd., Liaocheng, China) was used as the pre-vulcanization inhibitor.
The average molecular weight and molecular weight distribution were measured by gel permeation chromatography (GPC, Shimadzu, Kyoto, Japan). The GPC system consisted of a solvent delivery unit, a reflective index detector, and three Styragel columns: HT 6E (10 μm, 7.8 mm × 300 mm), HMW 7 (15-20 μm, 7.8 mm × 300 mm), and HMW 6E (15-20 μm, 7.8 mm × 300 mm). The molecular weight was calibrated using polybutadiene standards (Kit Poly(1,3-butadiene) number average molecular weight standards, WAT035709, Waters Corp., Eschborn, Germany).
Nuclear magnetic resonance (NMR) spectroscopy (Varian, Unity Plus 300 spectrometer, Garden State Scientific, Morristown, NJ, USA) was used to measure the microstructure of the BR (i.e., the vinyl, cis, and trans contents). BR sample was dissolved in a 5 mm NMR tube at a concentration of 15 mg/mL using deuterochloroform (CDCl3, Cambridge Isotope Laboratories, Inc., Andover, MA, USA) as the solvent.
The glass transition temperature (Tg) was determined using a differential scanning calorimeter (DSC-Q10, TA Instruments, New Castle, DE, USA). The sample curves (were obtained by heating the sample 3-6 mg sample per measurement) from -100°C to 100°C at a heating rate of 10°C/min under a nitrogen atmosphere.
To assess the degree of filler network formation in the uncured compound, a strain sweep test (0.28%-40%) was conducted at 60°C using a rubber process analyzer (RPA 2000, Alpha Technologies, Hudson, Ohio, USA). As the strain increases, the filler network is destroyed and the storage modulus (G′) decreases. Therefore, ΔG′ (G′@0.28% − G′@40%) represents the extent of filler–filler interaction, and can be used to assess the degree of filler dispersion within the rubber matrix; this is referred to as the Payne effect.16
Mooney viscosity, a measure of the processability of a compound, was determined using a Mooney rotatory viscometer (Vluchem IND Co., Seoul, Korea). According to the ASTM D1646 conditions, the large rotor (diameter = 38.10 ± 0.03 mm, thickness = 5.54 ± 0.03 mm) was preheated for 1 min, and then operated at 2 rpm for 4 min at 100°C to carry out the measurements.
Cure characteristics of the compound were measured for 30 min at a temperature of 150°C, a vibration angle of ± 1° and 100 rpm using a moving die rheometer (MDR, RLR-3-rotorless rheometer, Toyoseiki, Tokyo, Japan). This experiment was carried out to determine the minimum torque value (Tmin), maximum torque value (Tmax), and optimum cure time (t90) of the compound. Subsequently, vulcanizates were manufactured in a press heated to 150°C using the optimum cure time.
Vulcanizates were cut into dimensions of 10 mm (length) × 10 mm (width) × 2 mm (thickness) and their weights were measured. The samples were then stored in tetrahydrofuran (THF, 99%, Samchun Chemical Co., Seoul, Korea) and n-hexane (95%, Samchun Chemical Co., Seoul, Korea) at 25°C for 2 d each to remove any organic additives present in the specimens. After subjecting the specimens to drying at 25°C for 1 d, their weights were measured, and the mass fraction of extracted organic additives was calculated. The sample was subsequently swollen in toluene at 25°C for 1 d, and its weight was measured once again. The crosslink density was calculated using the final specimen weight and the following Flory–Rehner equation, as follows:17
where ν is the crosslink density of the vulcanizate (mol/g), Mc is the average molecular weight between crosslink points (g/mol), Vr is the volume fraction of rubber in the swollen gel at equilibrium, Vs is the molar volume of the solvent (cm3/ mol), ρr is the density of the rubber sample (g/cm3), and χ is the polymer–solvent interaction parameter.
The mechanical properties (e.g., tensile modulus and elongation at break) of the vulcanizates were measured using a universal testing machine (UTM, KSU-05M-C, KSU Co., Ansan, Korea). The measurements were conducted on dumbbell-shaped specimens with dimensions of 100 mm (length) × 25 mm (width) at a speed of 500 mm/min. Samples were fabricated according to the ATSM D 412 standard.
The abrasion resistance was measured according to ISO 4649 using a Deutsche Industrie Normen (DIN) abrasion tester. The specimens were adapted into cylindrical shapes (diameter = 16 mm, thickness = 8 mm) and attached to the surface of an abrasive sheet on a rotating drum at a rotation speed of 40 rpm. A load of 5 N was applied to each specimen, and the reduced mass was measured after rubbing it for 40 s.
To determine the viscoelastic characteristics of the vulcanizates, tan δ values were measured using a strain-controlled rheometer (ARES-G2, TA Instrument, New Castle, USA). For this purpose, a temperature sweep was performed from −60°C to 60°C at a strain of 0.5% and a frequency of 10 Hz.
Measurement of the particulate matter generated during tire tread specimen wear was performed using an aerodynamic particle sizer (APS, TSI 3321, USA) to determine the mass concentration. The schematic representation of the test apparatus is presented in Figure 1. The specimen was subjected to a vertical load of 20 N while in contact with a sandpaper belt (80 grit), which was rotated at a speed of 20 m/min to impart wear on the specimen. A filtered air supply (TSI 3074B, USA) was used to deliver clean and dry air into the chamber at a flow rate of 5 L/min (flow meter, TSI 5300, USA). Subsequently, the generated particles ranging in size from 0.37 to 20 μm were measured using APS.
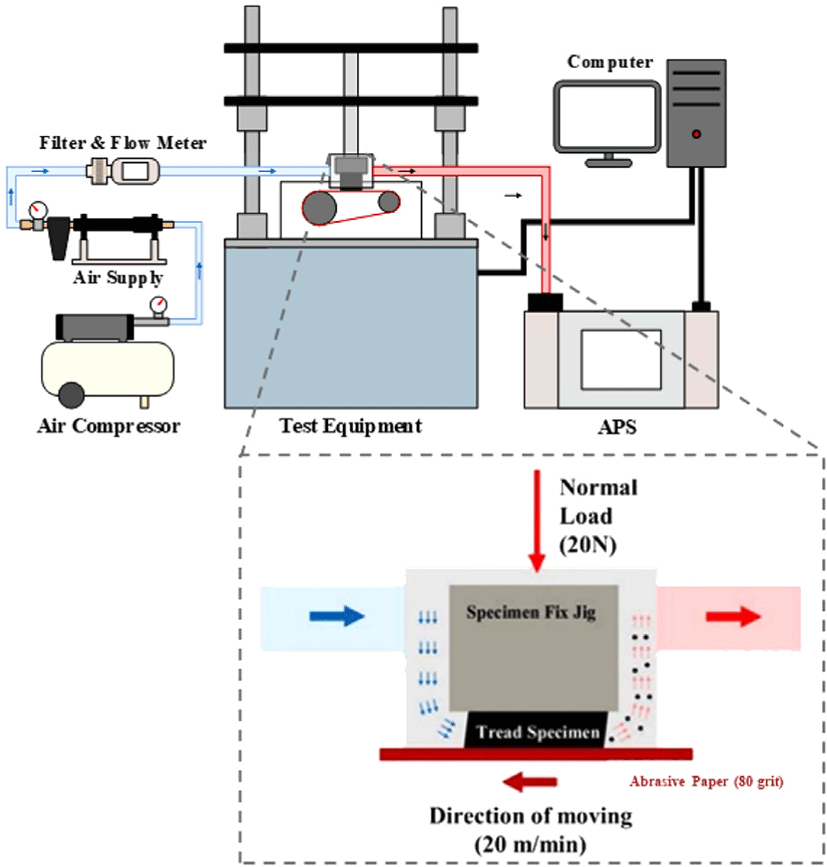
The compounds were manufactured by replacing NdBR with F-LiBR at concentrations of 10, 20 and 30 phr to investigate the effect of the F-LiBR content on the properties and degree of particulate matter generation of NR/BR/CB compound. The formulations of the various specimens are listed in Table 1. All compounds were manufactured using an internal kneader (300 cc, MIRAESI Company, Gwangju, Korea) with the fill factor set at 80% of the mixer capacity. In the first stage of mixing (Table 2), the temperature was started at 80°C and controlled dump temperature up to 150°C, and mixing was carried out for 330 s. In the second mixing step (Table 2), blending was carried out at 60°C for 150 s. Subsequently, the compound was converted into a sheet using a two-roll mill. The MDR instrument was then employed to cure each compound at 150°C for the optimum cure time. Then, the vulcanizates were produced using a hydraulic press at 150°C using the optimum cure time.
Results and Discussion
BR synthesized using the Ziegler–Natta (ZN) catalyst has a high cis content,18 while NdBR synthesized using a neodymium catalyst exhibits a cis content of ≥ 97%. During anionic polymerization, the addition of a polar solvent enhances the reaction rate and activate the anions to grow as chain ends.19 However, the ZN catalyst tends to exhibit a reduced catalytic activity in polar environments.20 To address this issue, a polar solvent was introduced into a lithium catalyst to replace the ZN catalyst and yield the F-LiBR. BR was subsequently analyzed by DSC, GPC, and NMR, as outlined in Table 3. More specifically, GPC analysis revealed that NdBR and F-LiBR possess weight average molecular weights (Mw) of 600,000 and 446,000 (g/mol) respectively, as well as molecular weight distributions of 3.83 and 1.07. In the 1H NMR spectra, the 1,4-addition structure of butadiene is represented by resonance peaks at 5.3-5.5 ppm, while the 1,2-addition (vinyl) structure is represented by resonance peaks at 5.5-5.6 and 4.8-5.0 ppm. Using the ratio of these peak areas, it was possible to calculate the vinyl content of prepared BR samples. In the 13C NMR spectrum, peaks corresponding to the cis structure of butadiene are present at 27-28 ppm, while peaks corresponding to the trans structure are present at 32-33 ppm. It was therefore possible to calculate the cis and trans contents of the BR specimens using the peak area ratios. As a result, NdBR exhibited a high cis content of 97.4%. In contrast, F-LiBR exhibited a high vinyl content (i.e., 16% cf., 1% for NdBR). Furthermore, DSC analysis revealed that the introduction of a polar solvent led to increased vinyl contents in F-LiBR, which in turn lead to a higher Tg value of -91°C (cf., -105°C for NdBR).
Payne effect measurement of compounds is presented in Figure 2 and Table 4. As indicated, compounds prepared with F-LiBR, which has functional group can react with CB, exhibited enhanced interaction with CB compared to the NdBR system, resulting in lower ΔG′ values. Furthermore, upon increasing the F-LiBR contents, the filler dispersion in the compound improved, resulting in a much lower ΔG′ value. The value of G’ in the high strain region, which is the point at which the filler network is destroyed, is influenced by factors such as the filler–rubber interaction, the rubber network, and the hydrodynamic effect.10 It was found that the incorporation of F-LiBR led to enhanced filler–rubber interaction, thereby resulting in a high G′ value at strain 40%.
The cure characteristics obtained using MDR and Mooney viscosity, a measure of compound processability, are presented in Figure 3 and Table 5. The compounds with F-LiBR exhibited higher Mooney viscosity due to increased interaction with CB during mixing,21 as compared to compound with NdBR.
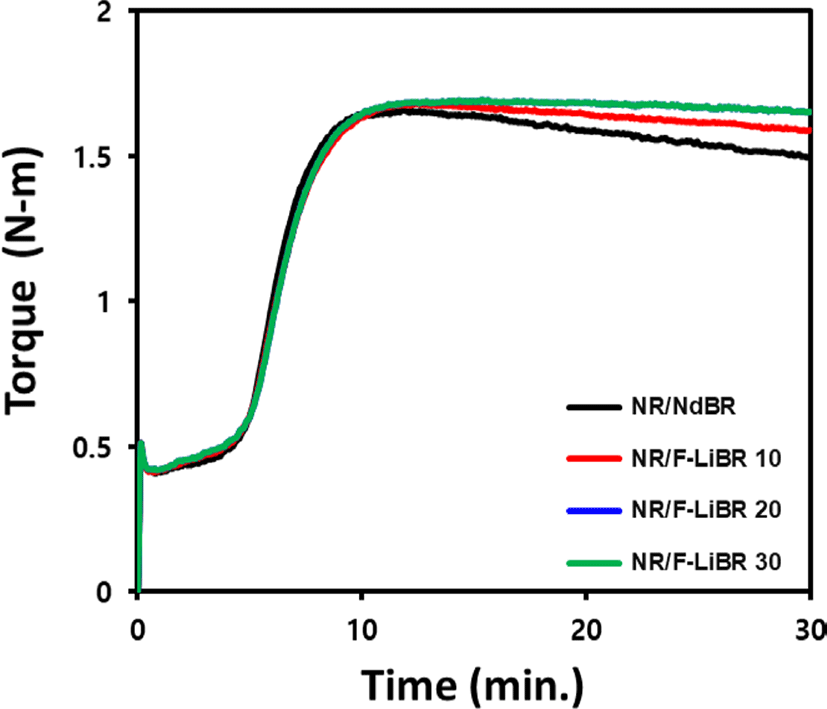
Compared to NR, BR is known for its superior resistance to the reversion, which causes a decrease in torque during the vulcanization process. In such systems, higher trans and vinyl contents lead to greater thermal stability.22 Thus, NdBR, with a cis content of > 97%, exhibits a lower thermal stability than F-LiBR, leading to a significant reversion as the cure time increases.
The crosslink density, mechanical properties, and DIN abrasion loss of the compounds are presented in Figure 9. and Table 6. Sulfur is known to form crosslink with allylic position of the rubber.23 Thus, the high vinyl content of F-LiBR result in a lower number of allylic positions compared to NdBR, leading to a lower crosslink density in NR/F-LiBR compounds.
The tensile modulus is a measure of the stiffness of rubber and tends to increase with higher crosslink density.24 Thus, due to the higher vinyl contents of NR/F-LiBR compounds, this led to a lower crosslink density than NR/ NdBR compound, along with a lower M300% value (tensile modulus at 300% elongation). Upon increasing the contents of F-LiBR, the crosslink density decreased further, thereby reducing the M300% value.
In DIN abrasion tests, the degree of abrasion loss is reduced when the rubber has a lower Tg and a higher molecular weight of base rubber.25,26 As mentioned above, F-LiBR has a higher vinyl content than NdBR and exhibits a higher Tg; this has a disadvantage on its wear resistance properties. Thus, NR/NdBR compound exhibited superior abrasion resistance compared to NR/F-LiBR compounds, and the abrasion resistance of the NR/F-LiBR compounds decreased as the F-LiBR content increased.
When a tire rotates under the applied load of a vehicle, all parts of the tire undergo deformation and recovery, resulting in energy loss. This phenomenon is referred to as hysteresis loss. At 60°C the tan δ represents the rolling resistance of a tire, wherein a lower value indicates a superior fuel efficiency.10 Furthermore, the loss modulus (G′′) at 0°C is an indicator of the wet grip performance, with higher values indicating superior performances.27
Tan δ values under a temperature sweep with a 0.5% strain were measured, as presented in Figure 5 and Table 7. This enhanced filler dispersion led to a decrease in the effective filler volume fraction, leading to a lower G′′ value.28 As a result, NR/F-LiBR compounds exhibited an improved filler dispersion and lower G′′ at 0°C upon increasing the degree of substitution.
Compound | Unit | NR/NdBR | NR/F-LiBR 10 | NR/F-LiBR 20 | NR/F-LiBR 30 |
---|---|---|---|---|---|
G′′ at 0°C | MPa | 1.81 | 1.69 | 1.73 | 1.49 |
Tan δ at 60°C | - | 1.115 | 1.115 | 1.115 | 1.112 |
Improvement of the compounds filler dispersion reduces the degree of hysteresis loss caused by destruction and reformation of the filler network, leading to lower tan δ values.29 Although F-LiBR substitution at levels of 10 and 20 phr had a negligible effect on the fuel efficiency due to offset between the influence of the filler dispersion improvement and the reducing crosslink density, substitution at 30 phr improved the filler dispersion, along with an lower tan δ at 60°C.
The measurement results of particulate matter generated by abrasion of compound are presented in Figure 6 and Table 8. As reported previously, the amount of generated particulate matter is highly correlated with the filler dispersion and abrasion resistance of a rubber.8 Previous studies have confirmed that the crack propagation inhibition of BR and the stress distribution relaxation effect within the NR matrix are effective in reducing particulate matter generation.30 As a result, the excellent filler dispersion of NR/F-LiBR compounds, enhanced by improved filler-rubber interaction and properties of BR, resulted in the generation of lower amounts of particulate matter compared to that recorded for the NR/NdBR compound. However, upon increasing the F-LiBR substitution content from 10 to 30 phr, the degree of particulate matter generation increased. This was related to the reduced wear resistance of the more highly substituted F-LiBR.
Compound | Unit | NR/NdBR | NR/F-LiBR 10 | NR/F-LiBR 20 | NR/F-LiBR 30 |
---|---|---|---|---|---|
PM2.5 | mg/m3 | 0.09 | 0.04 | 0.06 | 0.07 |
PM10 | mg/m3 | 0.12 | 0.04 | 0.09 | 0.09 |
Conclusion
In this study, F-LiBR was prepared by introducing CB corresponding functional groups at the rubber chain ends. Subsequently, the effect of these functional groups on the physical properties and particulate matter generation characteristics of the compound was evaluated. It was found that NR/F-LiBR compounds exhibited enhanced interaction with CB compared to NR/NdBR compound, resulting in an excellent filler dispersion. However, the incorporation of F-LiBR had a disadvantage on the mechanical properties and abrasion resistance because of its high vinyl content compared to NdBR. Importantly, the introduction of F-LiBR resulted in an improved filler dispersion, which was advantageous in terms of the rolling resistance when a substitution degree of 30 phr was employed. The enhanced filler dispersion of NR/F-LiBR compounds also led to the reduced generation of particulate matter. Through this study, it was confirmed that the introduction of F-LiBR improves filler dispersion in CB filled compounds, leading to enhancement in fuel efficiency and reduction in particulate matter. This study presents the research results on the technology of reducing particulate matters through the introduction of BR with modified chain ends in TBR tire tread.