Introduction
Hydroxyl-terminated polybutadiene (HTPB) is a telechelic polymer of butadiene, which is characterized by hydroxyl functional groups (–OH) at its chain ends, extensively employed in a wide range of applications such as automobile, aerospace, and coatings owing to its unique physical, mechanical, and chemical properties.1-10 It is mainly used as adhesives, coatings, and binders for solid propellant of rockets and missiles.11-18 HTPB is typically produced with a low molecular weight of about 1500~10000 g/mol affording the liquid state of polybutadiene (PB) and thus shows a low viscosity, low surface energy, excellent transparency, facile processability, and a low glass transition temperature (Tg ~ –80°C), leading to excellent low-temperature flexibility.1,10,19,20 In addition, the low polarity of HTPB provides excellent hydrolytic stability, low dielectric permittivity and loss, and corrosion resistance making it a promising material for high-voltage electrical insulation.7,9,21-23
HTPB is primarily produced by free radical polymerization of 1,3-butadiene using hydrogen peroxide as an initiator, which often yields characteristic contents of three structural configurations (1,4-cis ~ 20%, 1,4-trans ~ 60%, 1,2-vinyl ~ 20%) and the average number of hydroxyl functionality of 2.4 (Figure 1).6,24,25 It is worth noting that the microstructure of HTPB plays a major role in its physiochemical properties and processability.26 Increasing the 1,4-trans contents often contributes to higher tensile strength and lower elongation, whereas higher contents of the 1,4-cis unit afford higher low-temperature flexibility. Additionally, increased 1,2-vinyl contents lead to higher viscosity.27,28 HTPB can also be synthesized by anionic polymerization using a bidirectional radical anion initiator (e.g. lithium naphthalenide) or an initiator containing a protected hydroxyl group. It was reported that tert-butyl dimethyl siloxy dimethyl propyl lithium (Li)–naphthenate nickel (Ni)–boron trifluoride initiating system successfully afforded 95% of 1,4-cis contents for the preparation of HTPB.29 Furthermore, HTPB containing higher than 95% of 1,4-cis contents providing an extremely low Tg (~ –105°C) can be prepared by oxidative cleavage of high cis PB, constructed by metal-catalyzed coordination polymerization.29,30
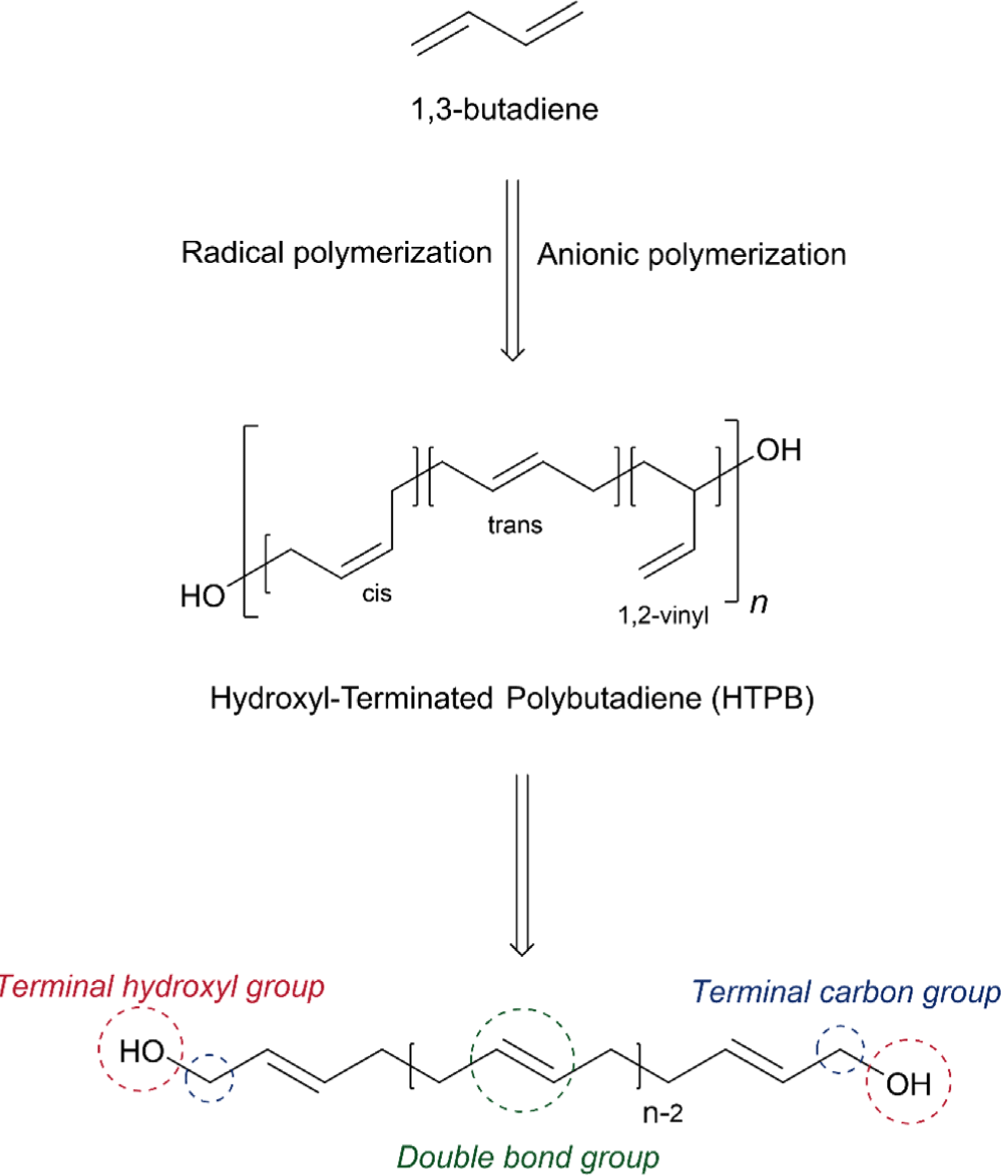
Due to the reactive terminal hydroxyl groups of HTPB, it is extensively used as a polyol in HTPB-based polyurethanes (HTPB-PUs). HTPB-PUs possess several remarkable properties, such as excellent chemical resistance, hydrolysis resistance, wear resistance, high viscoelasticity, low-temperature flexibility, and thermal stability.16,31 These attributes make HTPB-PUs ideal for a wide range of applications across different industries, including potting agents, electrical insulators, sealants, solid propellants, and explosives.5,9,10,16,28,32,33 Despite these advantages, HTPB-PUs may face concerns related to air and light-mediated oxidation during long-term applications. This susceptibility to oxidation is due to the presence of internal double bonds within the HTPB chain.10 However, the tendency toward oxidation can be mitigated by increasing the cross-link density in thermoset HTPB, leading to higher thermal stability.32 Furthermore, saturated HTPB (hydrogenated HTPB) can also be used as a polyol for HTPB-PU.19,34 By saturating the HTPB, the number of double bonds is reduced or eliminated, which further enhances the material’s resistance to oxidation and potentially improves its long-term stability and performance.35 Polyurethane (PU) chemistry, which involves the combination of a polyol, a crosslinker (e.g. isocyanates), and a chain extender (e.g. short-chain diols), offers a versatile approach to enhancing the stability of HTPB-PUs. This combination not only improves the thermal stability of HTPB-PUs but also allows for significant modifications in the mechanical, physical, and chemical properties of HTPB-PUs.9,15,33,36-38 By employing modified HTPBs, distinct cross-linkers, and varied chain extenders, the characteristics of HTPB-PUs can be precisely adjusted to meet specific application requirements. For instance, utilizing modified HTPB can introduce new functionalities or improve materials’ properties, such as increased oxidative stability, enhanced mechanical strength, or improved flexibility.39-41 Therefore, to maximize the potential of HTPB-PUs and enable the design of HTPB-PUs with tailored properties for various industrial applications, it is essential to develop post-polymerization modification methods for HTPB. This review will discuss the various post-polymerization modification methods for HTPB. For the sake of simplicity, the HTPB structures after post-polymerization modifications in this review were solely stated in trans configuration.
Discussion
Hydrogenated HTPB (HHTPB) is a specialized synthetic polymer created by hydrogenating HTPB to saturate its double bonds, thus enhancing its stability and mechanical properties for various high-performance applications.19,34 Since HTPB inherently contains ~46% internal double bonds, which are capable of reacting with air and light, long-term exposure to air and light can lead to degradation in mechanical properties.6,42 The synthesis of hydrogenated HTPB typically involves using transition metal catalysts such as palladium,26 nickel,43 or cobalt6,44,45 under controlled hydrogenation conditions (Figure 2), allowing for precise tuning of the polymer’s properties to meet specific application requirements. The resulting material’s reduced reactivity and enhanced stability not only improve safety during handling and processing but also extend the lifespan and reliability of products that incorporate hydrogenated HTPB.34 This process significantly improves HTPB’s oxidative and UV stability, making it ideal for use in demanding environments. For example, in aerospace applications, hydrogenated HTPB would serve as a binder in composite solid rocket propellants, providing improved mechanical properties and enhanced thermal and combustion stability, which contributes to greater propellant stability and performance. Additionally, hydrogenated HTPB can be utilized in protective coatings and adhesives where durability, chemical resistance, and flexibility are crucial, ensuring that the materials maintain their integrity under harsh conditions.
One of the most significant advancements in the field of HTPB is the development of epoxidized HTPB (EHTPB), which is suitable for use in coatings, adhesives, sealants, and composite materials across various industries, including automotive, aerospace, and electronics.46,47 Although HTPB has long been one of the most frequently utilized polymers as a binder in solid rocket propellants, it has a compatibility issue with a range of plasticizers and additives, especially with polar additives due to the non-polar characteristic of HTPB.46 This incompatibility poses significant challenges not only in propellant formulations but also in coatings, adhesives, and sealants where similar issues arise. The polar nature of additives or surfaces can lead to phase separation, reduced performance, and reduced adhesion. To address these compatibility issues, the epoxidation of the internal double bonds in HTPB can be an effective solution.46 Epoxidation introduces epoxy groups into the polymer chain, enhancing its chemical compatibility and improving its interaction with a broader range of materials. This modification enhances the polar nature of the polymer, allowing for better miscibility and stronger interaction when combined with polar materials. The enhanced compatibility and performance characteristics of epoxidized HTPB make it a valuable alternative in applications where traditional HTPB faces limitations. EHTPB can be typically prepared by peroxides (hydrogen peroxide or dioxiranes) or peroxy acids (e.g. m-CPBA) (Figure 3). In general, epoxidation with m-CPBA affords higher conversions than that with hydrogen peroxide.48 It was reported that a conversion of 77% was achieved with m-CPBA, while only a conversion of 6.9% with hydrogen peroxide/acetic acid and a conversion of ~60% with hydrogen peroxide with phase transfer catalysts.49-51 It is worth noting that the key to producing EHTPB is to precisely control the extent of epoxidation, which allows to balance the desired properties of EHTPB. In addition, three different structural configurations (1,4-cis, 1,4-trans, and 1,2-vinyl) toward epoxidation demonstrated distinct reactivity. It was reported that 1,4-cis configuration generally exhibits higher reactivity towards epoxidation owing to the favorable structure when the reagents approach syn-type addition, compared to 1,4-trans configuration.49,50,53 Surprisingly, 1,2-vinyl configuration showed almost no conversion for epoxidation. The low reactive 1,2-vinyl group can be converted to epoxide using dimethyl dioxirane (DMD) with Cu-based catalyst showing that a conversion of 84% was obtained with HTPB containing 1,2 vinyl contents of 60%.52 EHTPB exhibits enhanced characteristics on its own, but it is also regarded as an important precursor for the preparation of a modified HTPB with additional functions via a ring-opening reaction with functional nucleophiles.18
Nitrated HTPB (NHTPB) containing energetic groups such as nitrate ester (–ONO2) or nitro (–NO2) functional groups has been developed, especially for solid rocket propellant fields to provide additional energetic characteristics.54-56 Its development has enabled the formulation of high-performance rocket propellants capable of meeting stringent requirements in terms of energy output, stability, and combustion efficiency.56-59 The introduction of dinitrate ester functional groups was accomplished from EHTPB by utilizing N2O5 (Figure 4a).57,58 Although the extent of nitration could be controlled up to 90 % by increasing the stoichiometric amount of N2O5, it was found that a high degree of nitration over 50% led the NHTPB intractable during the synthesis. In addition, as the degree of nitration increased, the higher the Tg and the lower the thermal stability were obtained.57 It was found that the dinitrate ester of 10% demonstrated an optimized balance of energy output, mechanical properties, and miscibility with energetic plasticizers.58 However, precise control of epoxides and dinitrate esters addition is essential for effective synthesis because the preparation of the final product involves the epoxidation of HTPB followed by nitration.57 To simplify the nitration of HTPB while maintaining the characteristics of HTPB, nitro functional groups were installed directly on double bonds of HTPB without saturation by utilizing NaNO2 with I2, which generates the reactive species nitryl iodide (INO2) (Figure 4b).56,59-62 The insertion of the nitryl iodide into the double bonds followed by the elimination of HI afforded the nitro-functionalized HTPB.56 The optimized conditions afforded the resulting polymer functionalized with nitro group to a range of 12~15% at room temperature in 96 h. However, recent research revealed that the same conditions only afforded nitration of 3.2%, while nitration of 16% was achieved with 64 equivalents of NaNO2 and 24 equivalents of I2.62 The same group further studied to improve the synthetic methods utilizing N-iodosuccinimide (NIS), instead of I2 (Figure 4b). As a result, NaNO2 with NIS efficiently afforded nitro-functionalized HTPB containing nitro group of 6.7% at 60°C in 24 h.59 It was found that NHTPB with nitration of ~25% exhibited excellent mechanical properties in a wide range of temperatures, and the composite propellant with the resulting polymer demonstrated an increased combustion rate of up to 40% compared to that with HTPB.63
One of the most representative energetic binders for solid rocket propellants is glycidyl azide functionalized polyepichlorohydrin (PECH).64-68 This type of glycidyl azide polymer (GAP) exhibits desirable properties for energetic binders, such as high enthalpy of formation.69 The same structural design strategy has also been applied to HTPB modification. Azidated HTPB (AzHTPB, azide-functionalized HTPB) can be prepared by two main synthetic strategies: (i) bromination of HTPB with Br2 or KBrO3/KBr/H+ (in situ generation of Br2),31 followed by azidation with NaN3, and (ii) Mn(OAc)3 mediated azidation of HTPB in the presence of acetic acid and NaN3 (Figure 5).70 Although the second synthetic method is a more convenient single-step reaction and takes only a few minutes, it was revealed that the reaction showed inconsistent addition of azide due to the immiscibility of HTPB in acetic acid. The resulting polymer demonstrated that viscosity (11 Pa·s to soft gel) and Tg (–66°C~ –34°C) increased as the degree of azidation increased from 10% to 20%, owing to the polar interaction between polymer chains.31 In addition, the calculation results revealed that the enthalpy of formation of AzHTPB was found to be ~19,614 KJ mol-1, which is ~18,000 KJ mol-1 greater than that of HTPB having the same number of repeat units (1,540 KJ mol-1) and ~15,000 KJ mol-1 greater than that of PECH based GAP (4,825 KJ mol-1).71 This result strongly suggests that AzHTPB is one of the promising candidates for a binder of solid rocket propellants.
The simplicity, high efficiency, and regioselectivity of the thiol-ene click reaction make it an ideal method for the post-polymerization modification of HTPB.8 This reaction, which involves the addition of thiol groups to the double bonds in HTPB, proceeds under mild conditions and typically requires only a photoinitiator or a thermal initiator to drive the process (Figure 6).8,72,73 This allows for the rapid and clean modification of HTPB, introducing a wide range of functional groups. By utilizing thiol-ene chemistry, HTPB can be functionalized to enhance its properties, such as improving its compatibility with other materials, increasing its adhesive strength, or imparting additional chemical resistance.8 The versatility of the thiol-ene click reaction facilitates the precise tailoring of HTPB for specialized applications in coatings, adhesives, and advanced composites, expanding its utility and performance in various industrial sectors. It is worth noting that the reactivity of thiol insertion toward the three structural configurations of the double bonds is distinctive. The 1,2-vinyl groups are 10 times more reactive than the internal double bonds. Considering the fact that 1,2-vinyl groups are significantly more reactive than internal double bonds, the thiol-ene reaction allows for selective functionalization of HTPB, targeting these more reactive sites preferentially. This selective reactivity is advantageous to prepare modified HTPB while maintaining the intrinsic characteristics of HTPB, such as its flexibility, low glass transition temperature, and mechanical strength. By the selective modification of the more reactive sites, the thiol-ene reaction ensures that the bulk properties of the polymer are preserved while enhancing specific attributes required for particular applications. The orthogonality of the thiol-ene reaction to other chemical processes allows for further functionalization steps, enabling the development of multi-functional materials with tailored properties. For instance, after initial modification through the thiol-ene reaction, additional functional groups can be introduced to impart hydrophilicity or other desired characteristics, making the modified HTPB suitable for advanced applications. Recently, milder reaction conditions utilizing visible light-mediated transition metal catalysts have been developed. This method allows for even greater control over the thiol-ene click reaction, reducing the potential for side reactions and degradation of sensitive functional groups. Furthermore, it was found that this efficient method allowed the conversion of all the internal double bonds within 5 h.8 Even though the intrinsic properties of HTPB cannot remain intact using this method, new characteristics introduced through the thiol-ene reaction significantly enhance its utility for specialized applications. For example, THTPB with n-tetradecyl mercaptan exhibited extremely low Tg (–109.3°C), excellent hydrophobicity (contact angle of 137.2˚), and enhanced elongation at break, suggesting the applications in flexible thin films in low-temperature environments or hydrophobic coating. The use of visible light-mediated catalysts ensures a gentle yet efficient modification process, expanding the versatility of HTPB functionalization.73
The terminal hydroxyl group not only allows HTPB to engage in various applications, especially in polyurethane chemistry, but also provides a versatile foundation for further functional modifications that can tailor the polymer’s properties to specific needs. The versatility of terminal hydroxyl group modifications significantly enhances the uniqueness of HTPB, expanding its potential across a wide array of applications. For instance, terminal hydroxyl groups were converted to isocyanates affording isocyanate-terminated PB (ITPB) by end-capping with a diisocyanate reagent (Figure 7). This modification enables ITPB to react with various polyols, forming PUs that exhibit enhanced mechanical strength, elasticity, and chemical resistance, crucial for applications requiring durable elastomers. Moreover, this reactive functionality allows for further terminal modifications to epoxy-terminated or alkyne-terminated PB.14,74,75
In the tire industry, achieving compatibility between rubber and silica filler has been a persistent challenge. To improve this compatibility, the silane coupling agent TESPT (bis[3-(triethoxysilyl)propyl]tetrasulfide), commonly known as Si-69, is frequently used because it can chemically bond with both the rubber and the silica surface. Silane-terminated PB (SiTPB) represents a strategic advancement in addressing compatibility issues between rubber and silica fillers further (Figure 8). By integrating silane groups at the terminal positions of the PB chain, SiTPB can form more effective and durable interactions with rubber owing to the same chemical compositions.76,77 This enhancement not only improves the mechanical properties of the composite material but also optimizes processing characteristics, leading to tires with better performance metrics such as increased traction, reduced wear, and improved fuel efficiency.77 The use of SiTPB underscores the tire industry’s ongoing efforts to innovate materials that offer superior interaction with silica fillers, thereby enhancing the overall quality and durability of the final product.
Another interesting modification of the terminal hydroxyl group of HTPB is to prepare amine-terminated PB (ATPB). This transformation involves converting the terminal hydroxyl groups into amine groups,78 typically through a reaction of ITPB with amine-terminated small molecules,79 a reaction of tosyl-terminated PB with diamine reagents,80 or Michael addition with acrylonitrile followed by hydrogenation (Figure 9).81 ATPB offers enhanced reactivity compared to its hydroxyl-terminated counterpart due to the increased nucleophilicity of amine, leading to rapid curing time and making it particularly valuable in applications.81 For example, ATPB has been applied as a toughening agent for epoxy resin demonstrating increased critical stress intensity factor (KIC) and critical strain energy release rate (GIC) of the epoxy resin without the deterioration of the tensile strength of the matrix.78,80 In addition, tertiary ATPB for epoxy resin exhibited significant improvement in impact strength by 3.9 times.79 Interestingly, a reaction of ATPB with isocyanate leads to the formation of polyureas that exhibit exceptional mechanical properties including stronger intermolecular hydrogen bonding, compared to PUs.82,83
Terminal carbon group modification is a strategic approach that tailors the characteristics of HTPB without compromising its intrinsic physiochemical properties. The innovative approach to this functionalization involves the formation of a stable allyl anion at the terminal carbon of HTPB.28 This is achieved by treating the terminal hydroxyl groups with a strong base, typically sodium hydride (NaH), which effectively removes a hydrogen atom, thus generating the allyl anion (Figure 10).28,84 The presence of this anion is critical as it acts as a nucleophile in subsequent substitution reactions that facilitate the attachment of various functional groups to the polymer chain.21,28,84-88 One of the most compelling applications of this modification strategy is the attachment of energetic molecules such as 1-chloro-2,4-dinitrobenzene (DNCB) (Figure 11). This modification not only enhances the energy output of the resultant material but also maintains the original microstructure of HTPB, ensuring that key properties such as polymer flexibility and viscosity are preserved.28,85,89 Additionally, the terminal functionalization methodology is employed to attach biologically active molecules, for example, 2-chloro-4,6-bis(dimethylamino)-1,3,5-triazine (CBDT).84,86 This particular modification opens up new avenues for HTPB in the field of biomedicine, where it can be utilized in drug delivery systems or as a component in biocompatible materials.84 Please note that terminal carbon modifications of HTPB are well covered in the published article.88
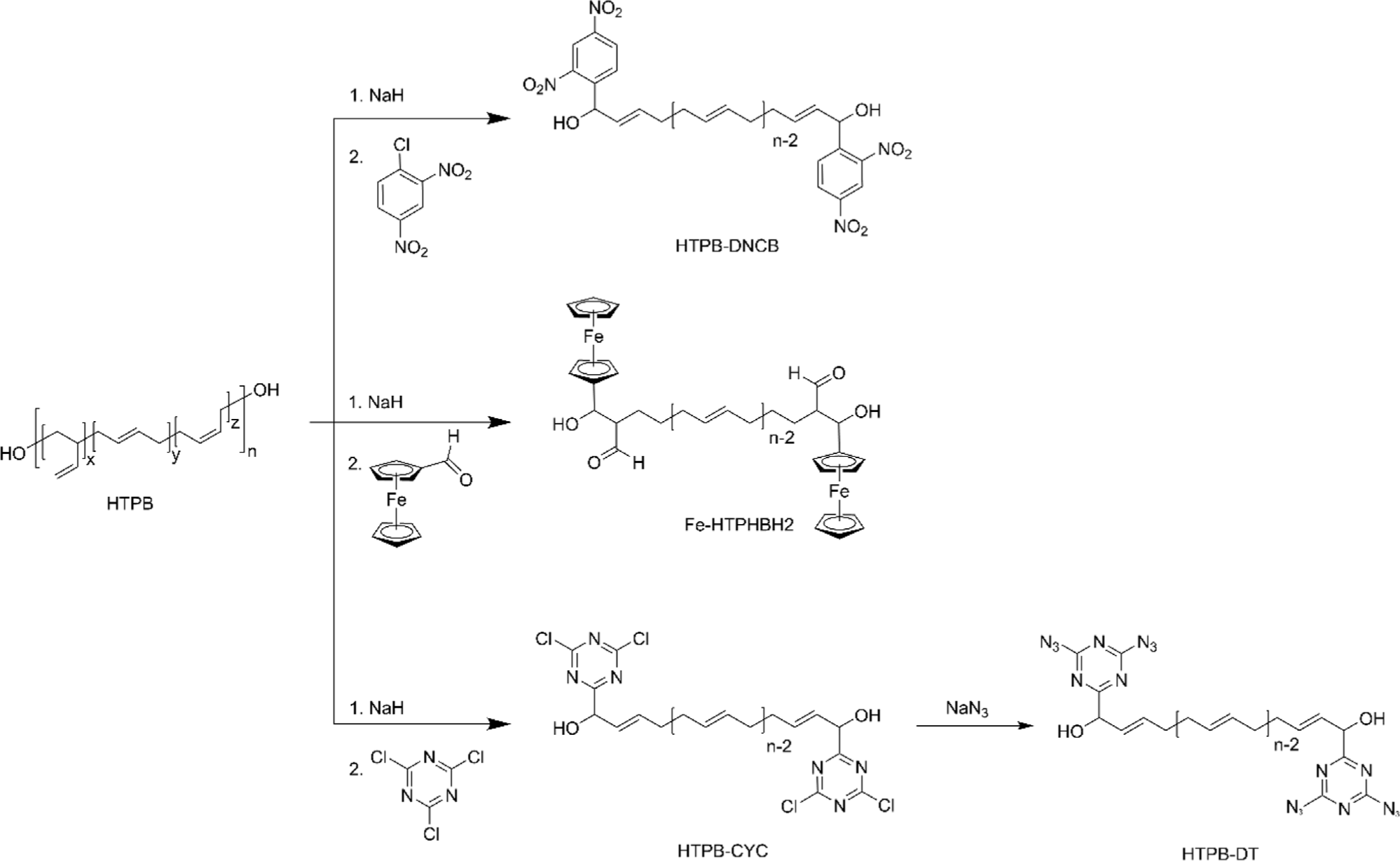
HTPB-based polyurethane networks exhibit indispensable roles in diverse applications. However, the inherent limitations associated with the non-reprocessability of traditional HTPB-based PUs contribute to environmental challenges and impede sustainable industrial advancements. Li et al.10 reported a groundbreaking study that developed recyclable HTPB-based PU vitrimer (HTPB-PUV) networks that incorporate a cross-linker with dynamic boronic ester bonds, facilitating reprocessing, self-healing, and shape memory abilities of the material. The innovative aspect of this study lies in the molecular design approach—utilizing a thiol-ene "click" reaction of the 1,2-vinyl group of HTPB with the cross-linker 2,2′-(1,4-phenylene)-bis[4-mercaptan-1,3,2-dioxaborolane] (BDB) (Figure 12).10 This method imparts dynamicity to the network through the dioxaborolane metathesis, allowing the rearrangement of the PU network topology.10,90 Characterization of the dynamic HTPB-PUV networks through dynamic mechanical analysis (DMA) and Fourier transform infrared (FTIR) spectroscopy demonstrated their superior thermostability. Notably, the dynamic boronic ester bonds allow for significant modification of the network topology, which is critical for the material’s unique reprocessing and self-healing capabilities.10 For instance, the polymer can be reprocessed multiple times without significant loss of mechanical properties, and self-healed samples nearly completely recover their integrity after damage. This behavior was further evidenced by experiments where pulverized samples were reprocessed through hot pressing, demonstrating similar mechanical properties to the original material, with even higher tensile strength. This result suggests the possibility that these materials will help advance sustainable practices in PU chemistry and engineering.
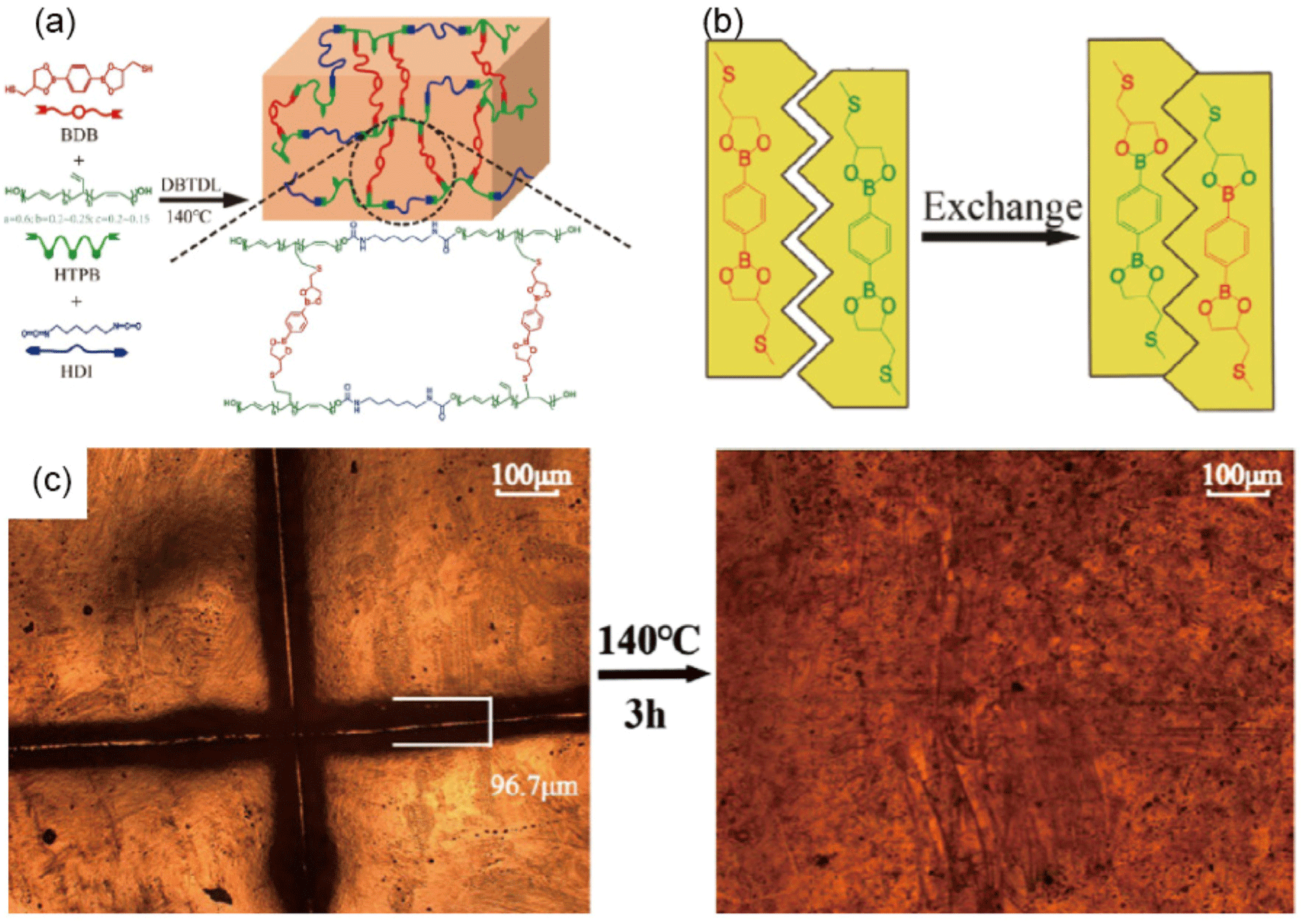
Another interesting study reported by Qin et al. is the preparation of flexible flame retardant based on PB.91 This was achieved by modifying epoxidized PB (EPB) with 9,10-dihydro-9-oxa-10-phosphaphenanthrene-10-oxide (DOPO), a well-known flame retardant, to produce DOPO-modified EPB (EPB–DOPO). The researchers carried out a two-step synthesis process, where the double bonds in PB were partially epoxidized to create reactive sites for subsequent DOPO attachment (Figure 13). The chemical structure of EPB–DOPO was characterized using 1H NMR and FT-IR spectroscopy, confirming the successful introduction of DOPO groups into the polymer’s backbone. Further analysis through thermogravimetric analysis (TGA) indicated good thermal stability of EPB–DOPO, which is crucial for maintaining integrity under high temperatures. The modified polymer also exhibited excellent flame retardancy, attributed to the presence of phosphorus in DOPO, which likely aids in capturing free radicals in the gas phase during combustion. Significantly, the EPB–DOPO maintained flexibility and toughness despite the incorporation of flame-retardant groups. This was evidenced by its Tg, which remained below –20°C even with the highest DOPO content.91 Although this study is not directly related to HTPB, it offers valuable insights into the broader realm of polybutadiene modifications, demonstrating the potential for enhancing material properties. Such methodologies could indeed be adapted for HTPB, suggesting a promising avenue for the development of HTPB-based materials with improved flame retardancy and thermal stability while maintaining its mechanical flexibility. By applying similar chemical strategies, researchers might enhance HTPB’s applicability in industries requiring robust, fire-resistant materials without sacrificing essential physical properties.

Conclusion
The exploration of post-polymerization modifications of HTPB illustrates a dynamic research area driven by the need to extend the utility of HTPB-based materials beyond their traditional applications. Through methods such as hydrogenation and epoxidation, researchers have successfully enhanced the chemical stability and functional adaptability of HTPB, thereby broadening its applicability in demanding environments. The hydrogenation of HTPB addresses its inherent susceptibility to oxidative degradation by saturating the double bonds within the polymer chain, significantly enhancing its oxidative stability and extending its lifespan under harsh conditions. Meanwhile, the introduction of epoxy groups through epoxidation has opened new avenues for HTPB by improving its compatibility with a range of polar additives, thus facilitating the creation of more complex material systems. Furthermore, these modifications have proven critical in maintaining the mechanical integrity and thermal stability of HTPB, ensuring that the modified polymers meet the stringent requirements of industries such as aerospace and automotive manufacturing. The ability to tailor the properties of HTPB through controlled chemical modifications also supports the development of specialized materials, including lightweight composites and high-performance coatings, which are vital for technological advancements. Looking ahead, the field of HTPB modification holds promising potential for developing innovative materials that contribute to sustainable practices and enhanced material performance. Continued research in this area is essential to uncover new chemical pathways that can further refine the properties of HTPB-based materials, supporting the growth of industries that rely on advanced polymeric solutions. As this research progresses, it is anticipated that the versatility and efficacy of HTPB will continue to expand, affirming its role as a cornerstone of modern polymer science and technology.