Introduction
Tire wear particles (TWPs), emitted by the non-exhaust sources of a vehicle, are generated by the friction between tires and road surface.1-5 TWPs are commonly surrounded by mineral particles from the road and hence, are referred to as tire-road wear particles (TRWPs).3-9 Once released into the environment, TRWPs can be deposited along the roadside, disintegrated into small pieces that remain suspended in the air, or transported to the aquatic environment through road runoff.10-13
Quantitative analysis of TWPs in environmental samples is primarily conducted through pyrolysis by analyzing rubber components.13-18 The polymer composition of TWP varies depending on the tire manufacturer and application, which is a crucial consideration in the quantification of TWP in environmental matrices.14,15,19 If the temperature during pyrolysis-based quantitative analysis is not applied uniformly to the entire sample, some parts of the sample may undergo incomplete decomposition, while some parts may undergo excess decomposition. Therefore, a calibration curve prepared using an accurate amount of sample is essential for precise quantification. For quantifying TWPs in environmental samples, many studies, along with the International Organization for Standardization (ISO) documents, have suggested the use of deuterated polymers as an internal standard.12,13,19-21 However, deuterated chemicals are too expensive, and alternative internal standards must be developed. An internal standard must meet the following criteria: (1) it must not change during the analysis process; (2) it must not be a substance present in the sample; (3) it must be clearly separated from the analyte; and (4) it must not react with the components in the sample during the analysis.
The contribution of TWPs in PM2.5 or road dust is less than 5%,14,20,22-25 and the amount of sample used for pyrolysis analysis is usually up to 0.5 mg.26-28 The rubber content in TWPs is generally ~50%.3,9,29 Since the rubber content in the samples for pyrolysis analysis is less than 20 μg, an internal standard that is suitable for quantifying up to 20 μg is required. The primary rubber of a truck-bus tire tread is natural rubber (NR), while that of a passenger car tire tread is styrene-butadiene rubber, along with some NR. Therefore, we used NR for selecting a new internal standard.2,10,30-32
Experimental
SMR CV 60 was employed as NR and toluene was purchaed from J. T. Baker (USA). Poly(4-methylstyrene) (PMS) was purchaed from Sigma-aldrich (Germany). An NR and PMS solution were prepared by dissolving in toluene. An NR particle sample was prepared as follows: (1) an NR solution was dropped onto a slide glass, (2) the solvent was evaporated in a convection oven at 70°C for 30 min, and (3) a solid NR particle was obtained by gathering the dried NR with a knife. The initial NR solution of 10.0 mg mL-1 was prepared by dissolving SMR CV 60 in toluene. This NR solution was diluted to 2.0 and 0.40 mg mL-1. NR samples of 10.0 and 20.0 μg were obatined using the 2.0 mg mL-1 NR solution of 5.0 and 10.0 μL, respectively, while those of 2.0 and 5.0 μg were obatined using the 0.40 mg mL-1 NR solution of 5.0 and 12.5 μL, respectively. A PMS solution was prepared at 0.6 mg mL-1, and 5.0 μL of this solution, corresponding to 3.0 μg PMS, was used as an internal standard. All analyses were perforemd in quadruplicate.
A furnace type pyrolyzer of a pyroprobe 2000 system with a CDS 1500 interface (Chemical Data System Analytical Inc., USA) was used. A furnace type pyrolyzer uses a quartz tube for sampling. The sample preparation process was as follows: (1) insert glass wool into the one end part of the quartz tube, (2) put the rubber sample at the center of the quartz tube, (3) insert glass wool at the center of the quartz tube, (4) put a PMS solution into the glass wool at the center of the quartz tube, (5) insert glass wool at the other end part of the quartz tube, and (6) evaporate the solution in a convection oven at 70°C for 10 min. The sample was preheated at 250°C for 15 s and pyrolyzed at 590°C for 10 s under helium (He) atmosphere.
An Agilent 6890 GC (Agilent Technology Inc., USA) equipped with an Agilent 5973 MSD (Agilent Technology Inc., USA) was used. DB-5MS (30 m × 0.32 mm, film thickness 0.25 μm, Agilent Technology Inc., USA) was used. The sample inlet temperature was 250°C, the split ratio was 1:15, and helium (1.8 mL min-1) was used as the carrier gas. The GC oven temperature programming was as follows: 30°C (held for 3 min) to 160°C at a rate of 8 °C min-1 (held for 1 min), and then to 250°C at a rate of 10 °C min-1 (held for 3 min). The interface temperature of GC to MS was 250°C.
The electron ionization (70 eV) was used to ionize the pyrolysis products. The MS source temperature was 230°C.
Results and Discussion
Figure 1 shows Py-GC/MS chromatograms of NR and PMS. The main pyrolysis products of the polymers are monomer and dimers. The primary pyrolysis products of NR, isoprene and dipentene, were detected at 1.35 and 10.18 min, respectively. The monomer of PMS, 4-methylstyrene, was observed at 9.55 min. The dimer species of PMS, namely, 1,3-bis(4-methylphenyl) propane, 2,4-bis(4-methylphenyl) butene, and 2,4-bis(4-methylphenyl) penta-1,4-diene, were observed at 24.09, 24.84, and 26.31 min, respectively. The peak areas decreased in the order 4-methylstyrene > 2,4-bis(4-methylphenyl) butene > 1,3-bis(4-methylphenyl) propane > 2,4-bis(4-methylphenyl) penta-1,4-diene.
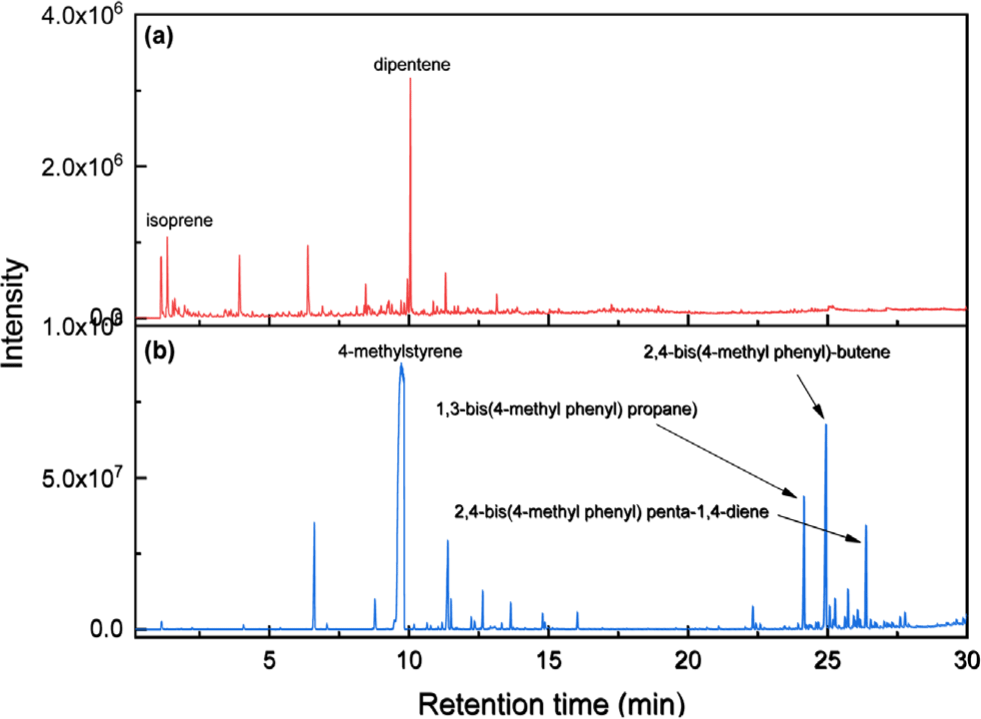
The formation mechanisms of the pyrolysis products from PMS are described in Schemes 1-3. The C-C bond in a PMS chain is thermally dissociated, leading to the formation of ~CH · and ~·CH~ radicals (Scheme 1). The radicals easily rearrange with the next C-C single bond to form the monomer of PMS (4-methylstyrene). Accordingly, the most abundant pyrolysis product of PMS is 4-methylstyrene because its formation is thermodynamically favorable.
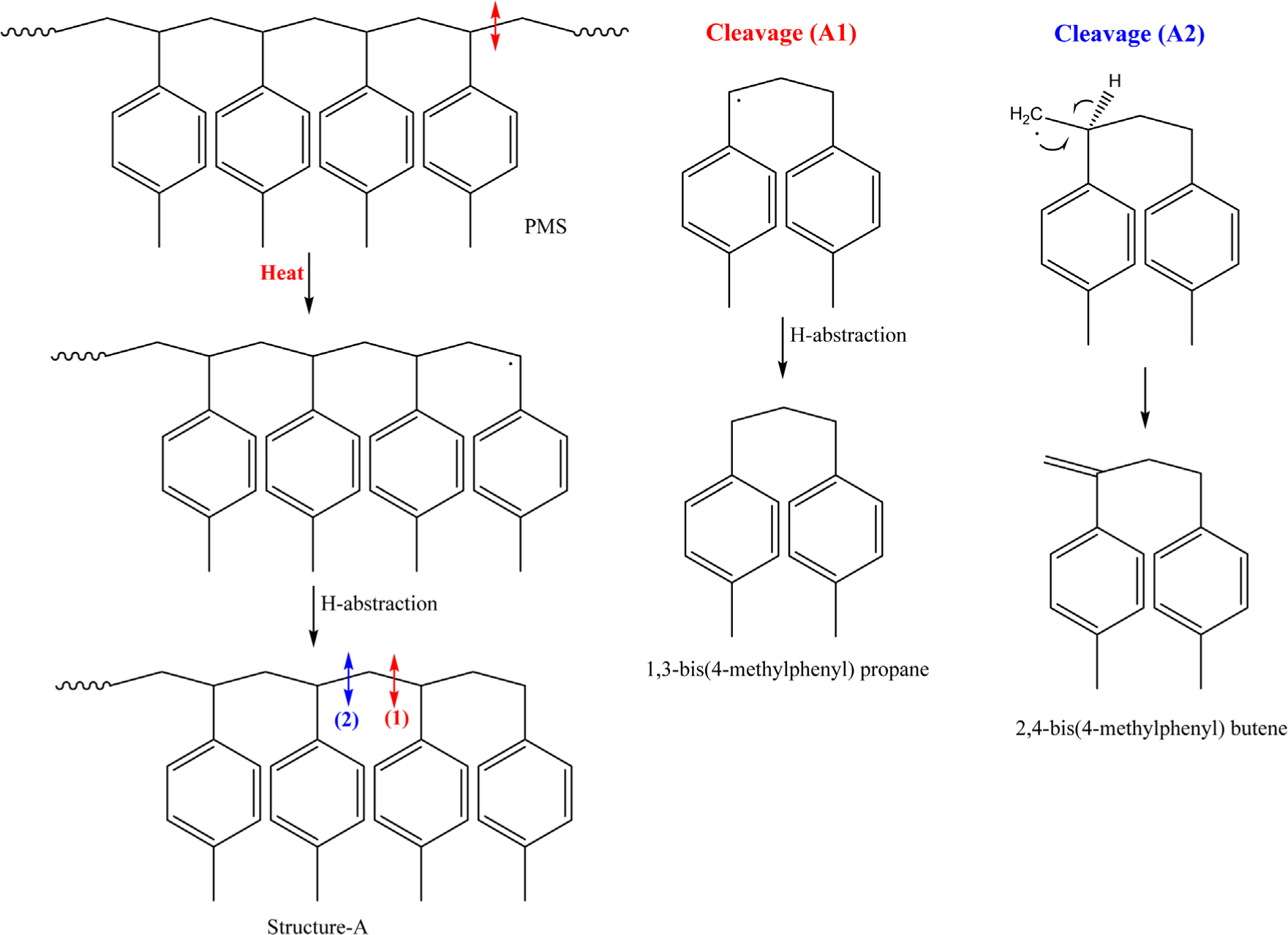
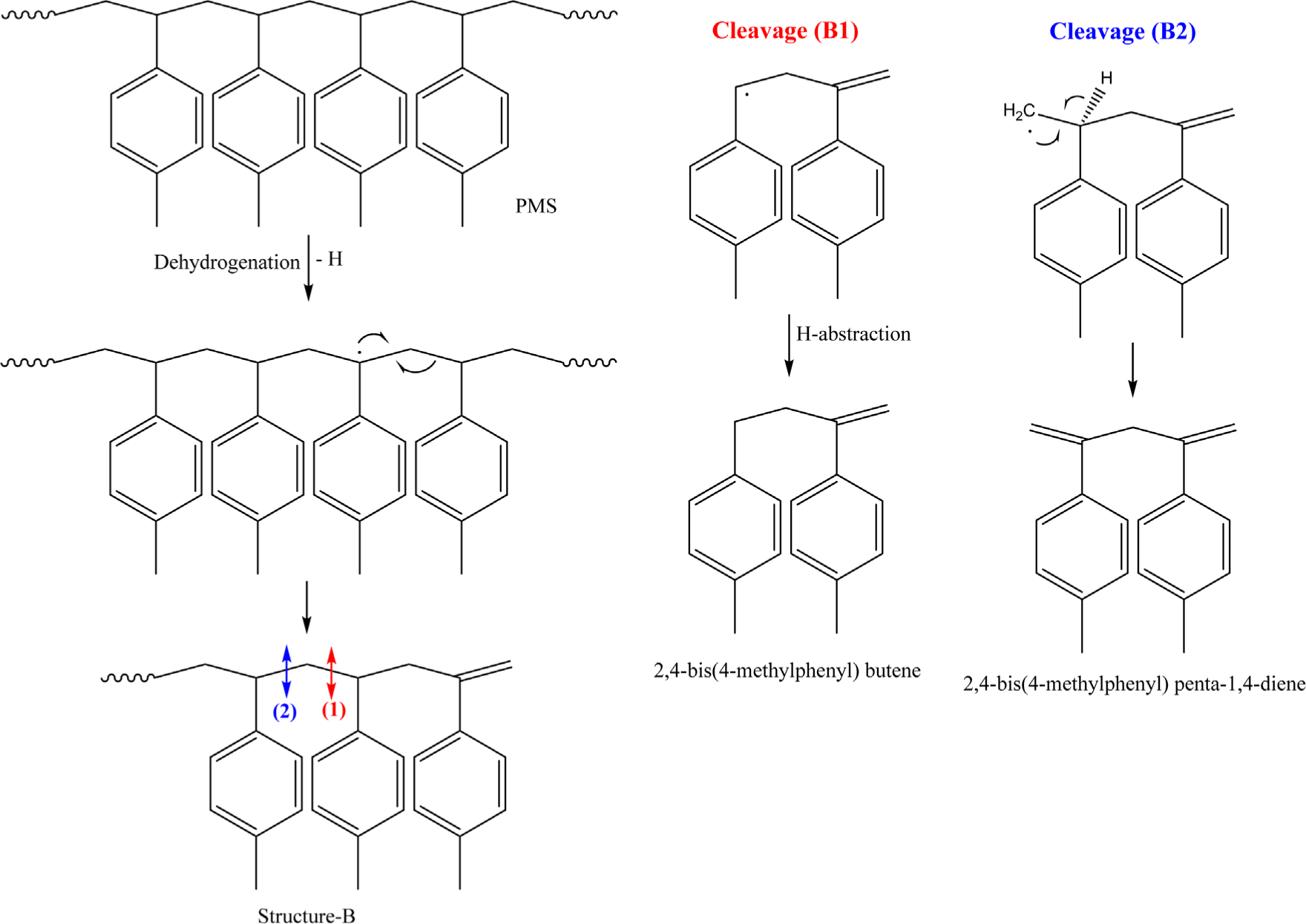
The dimeric pyrolysis products (1,3-bis(4-methylphenyl) propane, 2,4-bis(4-methylphenyl) butene), and 2,4-bis(4-methylphenyl) penta-1,4-diene) can be formed through the secondary C-C bond cleavages as shown in Schemes 2 and 3. When the ~°CH~ radical is formed from PMS by the primary C-C bond cleavage (Scheme 2), the end adopts a structure with an alkane backbone (~CH2~), Structure-A, by hydrogen abstraction. After the secondary C-C bond cleavage in Structure-A, two radicals with dimer are formed. 1,3-Bis(4-methylphenyl) propane is produced through Cleavage (A1) and hydrogen abstraction, while 2,4-bis(4-methylphenyl) butene is generated through Cleavage (A2) and a subsequent rearrangement.
If a radical formed by pyrolysis abstracts a hydrogen atom from the backbone of PMS, a new radical is generated at the PMS chain (Scheme 3). The new radical is probably formed at ~CH~ and not at ~CH2~, considering the radical stability. It is easily rearranged with the next C-C single bond to form an end with an alkene structure, Structure-B. After the secondary C-C bond cleavage in Structure-B, two radicals with dimer are formed. 2,4-Bis(4-methylphenyl) butene is produced through Cleavage (B1) and hydrogen abstraction, while bis(4-methylphenyl) penta-1,4-diene is generated through Cleavage (B2) and a subsequent rearrangement. 2,4-Bis(4-methylphenyl) butene is formed from both Structure-A and Structure-B. The higher abundance of 2,4-bis(4-methylphenyl) butene compared to those of 1,3-bis(4-methylphenyl) propane and bis(4-methylphenyl) penta-1,4-diene can be explained by the two reactions to generate 2,4-bis(4-methylphenyl) butene.
Figure 2 presents the Py-GC/MS chromatogram of the mixture of NR and PMS. The peaks of the pyrolysis products of PMS did not overlap with those of NR. Additionally, no new pyrolysis products were detected. Therefore, PMS can be employed as an internal standard.
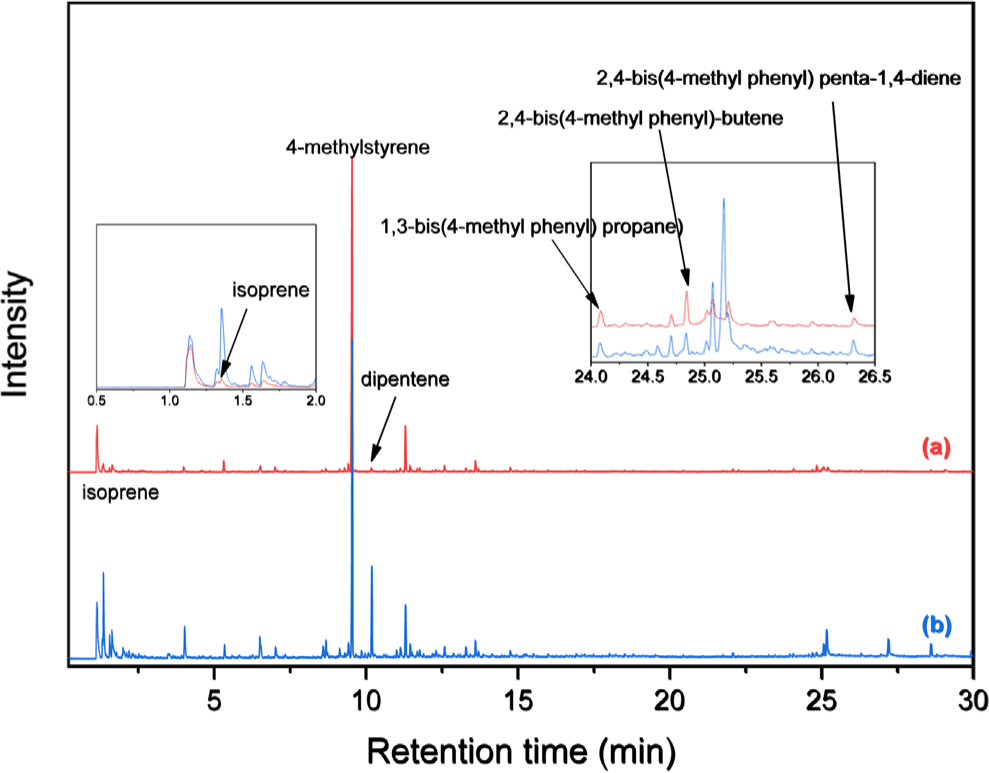
Figure 3 shows the calibration curves for quantifying NR using the peak areas of isoprene and dipentene. The correlation coefficients (R2) for the calibration curves were 0.992 and 0.934, respectively. Although the calibration curve of isoprene exhibited good correlation, an internal standard may be necessary to eliminate potential errors such as variations in instrument performance during analysis.
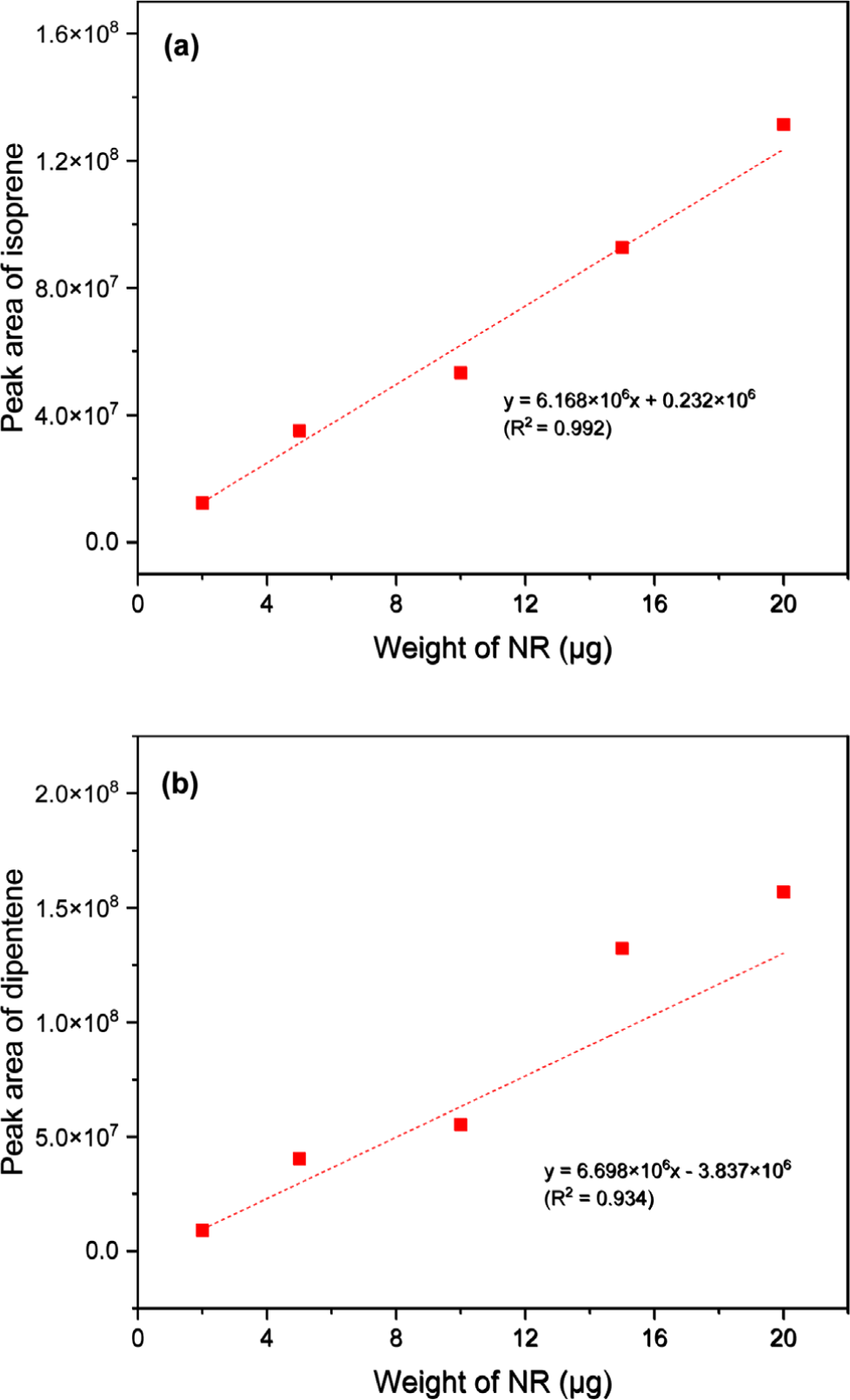
Figure 4 presents the calibration curves constructed using the peak intensity ratios of the pyrolysis products of NR and 4-methylstyrene (monomeric pyrolysis product of PMS). While the calibration curve of isoprene showed poor correlation (R2 = 0.976), the calibration curve of dipentene showed improved correlation (R2 = 0.988) compared to that of NR alone. The three calibration curves of the dimeric pyrolysis products of PMS showed higher correlation than those of isoprene and dipentene (Figures 5, 6, and 7 for bis(4-methylphenyl) propane, 2,4-bis(4-methylphenyl) butene, and 2,4-bis(4-methylphenyl) penta-1,4-diene, respectively). The R2 values for isoprene and the dimeric species of PMS were 0.998, 0.999, and 0.999 for bis(4-methylphenyl) propane, 2,4-bis(4-methylphenyl) butene, and 2,4-bis(4-methylphenyl) penta-1,4-diene, respectively. The R2 values for dipentene and the dimeric species of PMS were 0.986, 0.994, and 0.994, respectively.
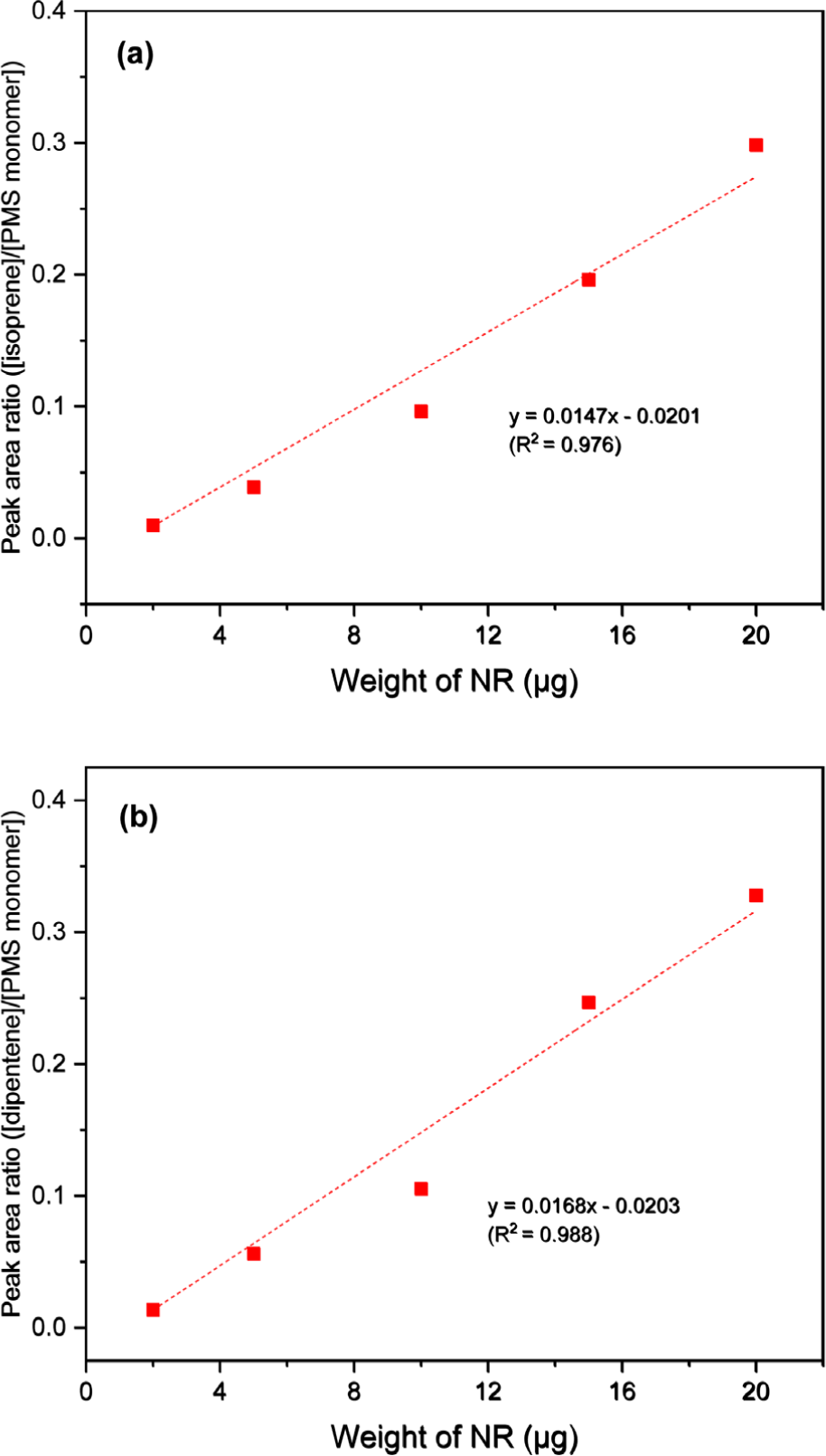
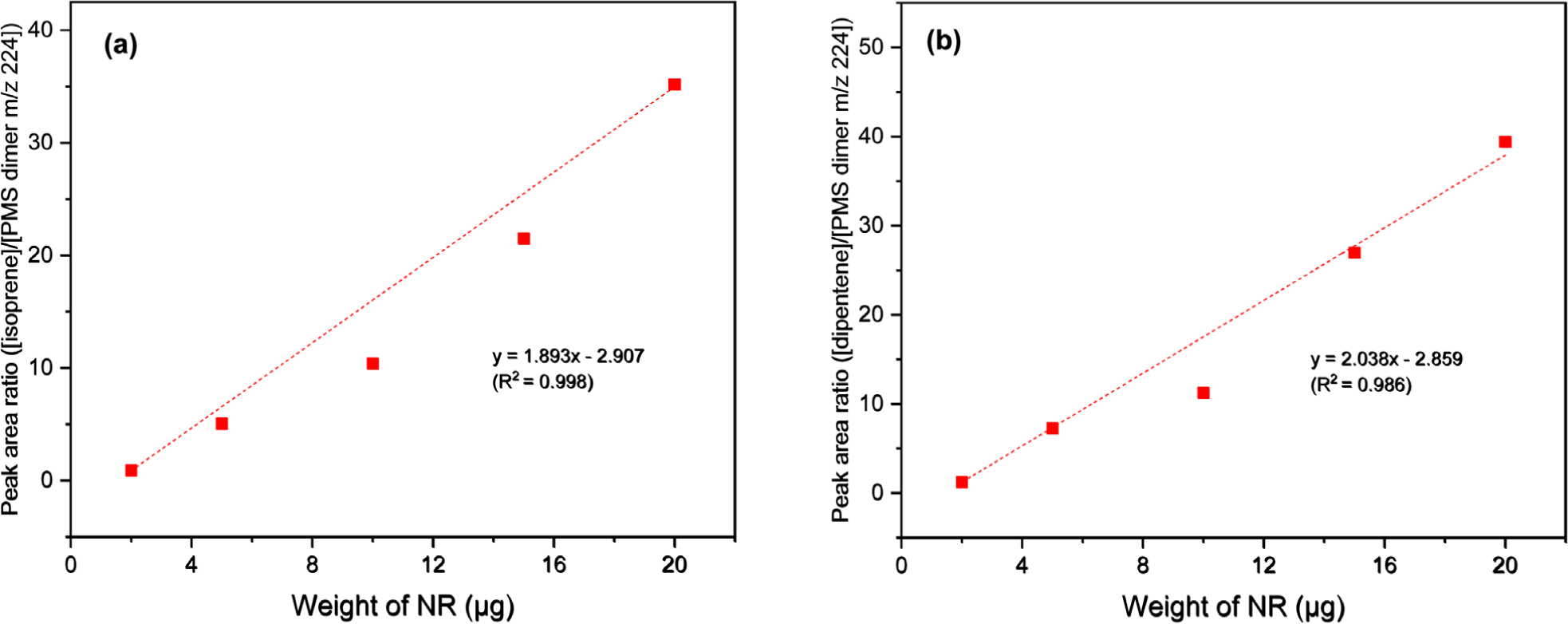
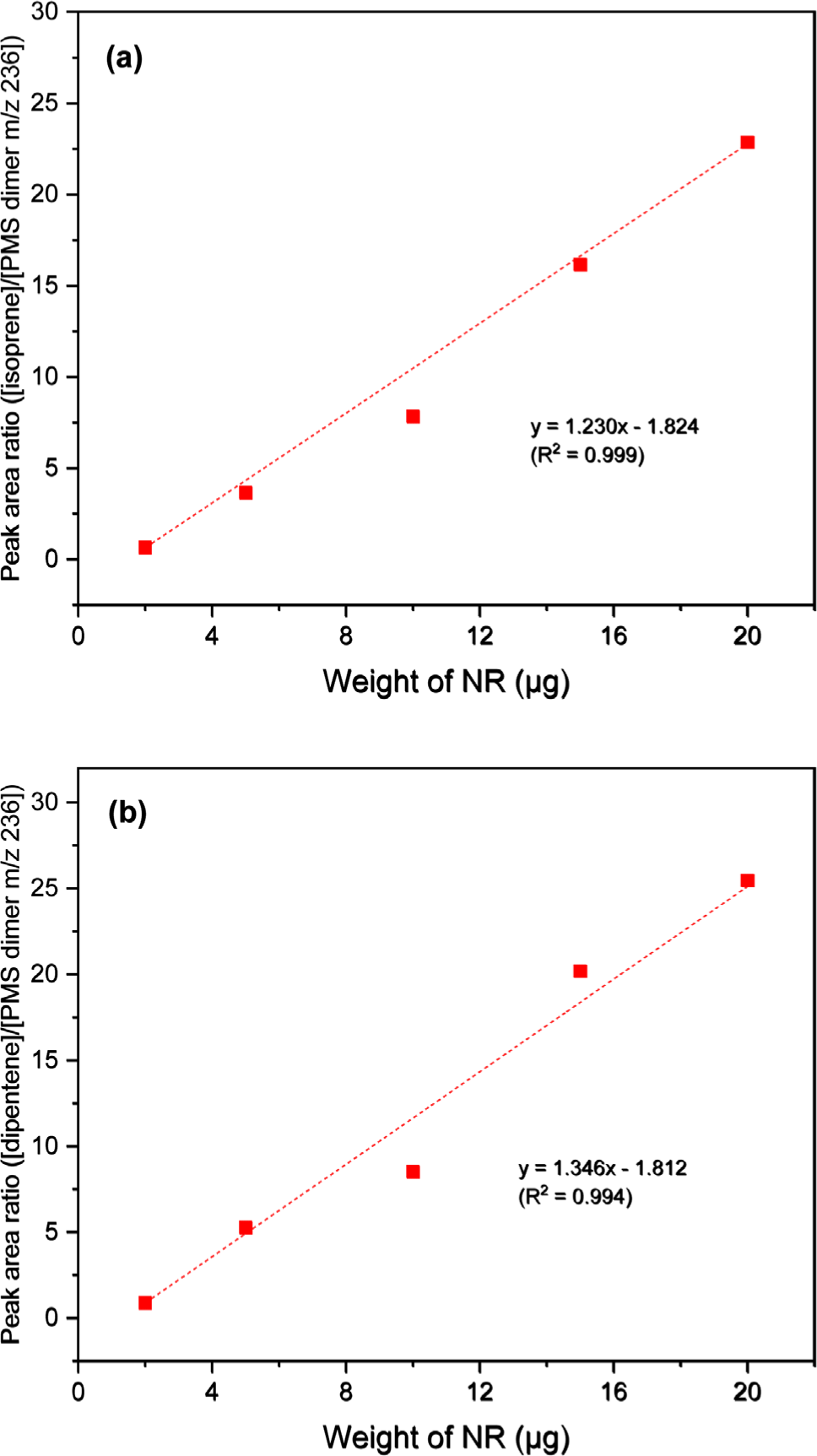
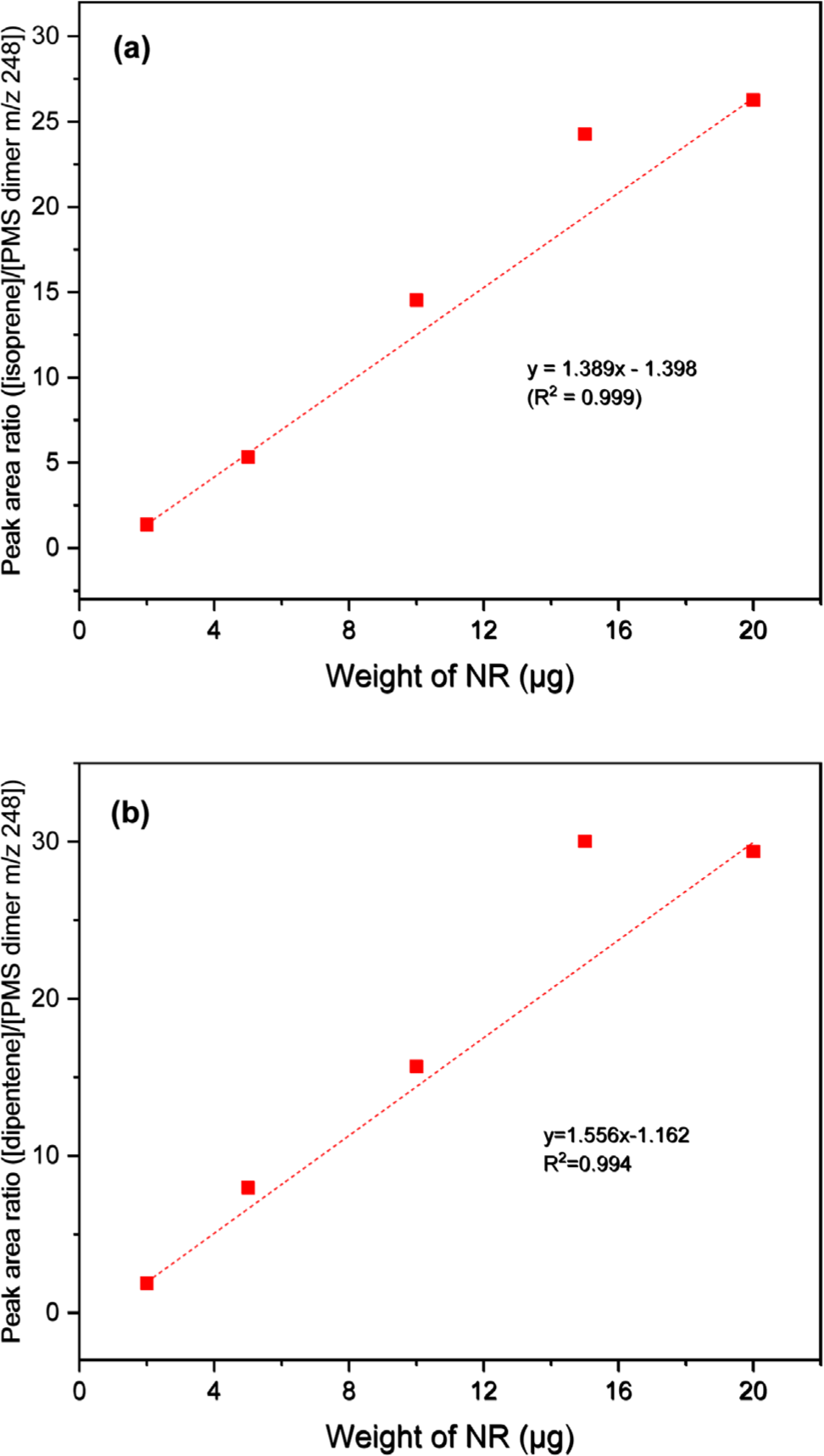
The correlations for the calibration curves of 2,4-bis(4-methylphenyl) butene and 2,4-bis(4-methylphenyl) penta-1,4-diene were better than that of bis(4-methylphenyl) propane. The results suggest that the use of the dimeric pyrolysis products of PMS for constructing calibration curves can improve the R2 values for both isoprene and dipentene. Among the three dimeric pyrolysis products of PMS, using 2,4-bis(4-methylphenyl) butene for constructing the calibration curves will be more appropriate than using bis(4-methylphenyl) propane and 2,4-bis(4-methylphenyl) penta-1,4-diene because 2,4-bis(4-methylphenyl) butene is more abundant and has a higher correlation coefficient of the calibration curve than the other two pyrolysis products.
Conclusions
PMS was proposed as a novel internal standard for quantifying TWP in environmental samples. The principal pyrolysis products of PMS were 4-methylsyrene, 1,3-bis(4-methylphenyl) propane, 2,4-bis(4-methylphenyl) butene, and 2,4-bis(4-methylphenyl) penta-1,4-diene. The peaks of these products did not overlap with those of the major pyrolysis products of NR, such as isoprene and dipentene. Therefore, PMS can be used as an internal standard for quantifying NR components. Upon examining the calibration curve indicators using the monomeric and dimeric species of PMS, it was found that the correlation of the calibration curve improved using the dimeric pyrolysis products of PMS. In particular, the linearity of the calibration curves of 2,4-bis(4-methylphenyl) butene and 2,4-bis(4-methylphenyl) penta-1,4-diene was significantly improved. 2,4-Bis(4-methylphenyl) butene was better than 2,4-bis(4-methylphenyl) penta-1,4-diene because of its relatively higher abundance.