Introduction
In the rubber industry, blending different types of rubber has become a standard approach to leveraging the advantages of various materials while compensating for their individual limitations.1-3 By combining rubbers, manufacturers aim to improve mechanical properties, enhance processability, and impart specific desired characteristics to meet diverse application needs.4-6 Among the rubbers widely used in such blends is ethylene-propylene-diene monomer (EPDM), which is recognized for its outstanding mechanical properties and broad processing temperature range.7,8 EPDM, a saturated rubber polymer, exhibits excellent resistance to aging, ozone, ultraviolet (UV) radiation, oxidation, and various chemicals,9-11 making it a material of choice for applications such as automotive profiles, window gaskets, roof sheets, wastewater seals, electrical cables, and wires.12-14 However, despite its many advantages, EPDM has certain limitations compared to IIR, including relatively high gas permeability and inferior shock absorption capabilities.15
To address these shortcomings, EPDM is often blended with other rubbers, such as isobutylene-isoprene rubber (IIR).16,17 IIR, also known as butyl rubber, is characterized by its excellent heat resistance and superior shock absorption properties.18,19 Despite these benefits, IIR is rarely used as a standalone rubber due to its challenging processing requirements and comparatively poor mechanical properties.20 Instead, it is typically blended with other rubbers to enhance specific characteristics, such as damping properties and durability.21 Incorporating IIR into EPDM formulations can potentially improve the shock absorption capacity of the resulting composites, making them more effective in applications requiring enhanced anti-vibration characteristics, such as automotive tires and suspension components. These anti-vibration properties are particularly important for improving vehicle ride comfort by reducing the transmission of road vibrations to the vehicle body.22
In addition to rubber blending, the incorporation of fillers, such as carbon black (CB), plays a crucial role in optimizing the mechanical and damping properties of rubber composites.2,23 CB is one of the most extensively used fillers in the rubber industry due to its ability to provide high hardness, elasticity, and improved durability. When used in rubber composites, CB enhances the mechanical strength, abrasion resistance, and processability, making it indispensable for applications in sealing, vibration damping, and various transport-related uses.23-26 In the present study, CB was utilized as a filler to maximize the anti-vibration effects and enhance the overall mechanical properties of EPDM/IIR composites.
The vulcanization process, or the cross-linking of rubber molecules, is another critical factor in determining the properties of rubber composites. Curing agents, such as sulfur (S) and peroxide, are commonly employed to facilitate cross-linking.8,21,27 Sulfur vulcanization, a traditional method, improves the abrasion resistance of rubber by forming sulfursulfur (S-S) cross-links between the rubber molecules, which are relatively unstable at high temperatures.28-31 Alternatively, peroxide curing forms more stable carbon-carbon (C-C) cross-links, providing enhanced thermal stability and heat resistance to the rubber.24,30 The choice of curing agent can significantly impact the final properties of the rubber composite, including its mechanical performance and thermal aging characteristics.
This study investigates the effects of two commonly used curing agents, sulfur and peroxide, on the damping and mechanical properties of EPDM/IIR composites. By evaluating the effects of these curing agents on mechanical properties, thermal stability, and anti-vibration characteristics of the rubber blends, this research aims to provide insights into optimizing the formulation of rubber composites for applications demanding superior mechanical performance and vibration damping properties.
Experimental
Ethylene propylene diene monomer (EPDM; KEP 330) was purchased from Kumho Polychem Co. (South Korea), and butyl rubber (EXXON (TM) butyl rubber), also known as isobutylene isoprene rubber (IIR) was purchased from ExxonMobil Co. (South Korea). Carbon black (CB; FEF) with a diameter of 40-48 nm was purchased from TSR Co. (South Korea). Zinc oxide (ZnO), stearic acid (SA), sulfur, and 2,2-dibenzothiazole disulfide (DM), CZ were purchased from Puyang Willing Chemical Co. (China). Toluene was purchased from BNOChem Co. (South Korea), Peroxide was purchased from Shin-Etsu Chemical
EPDM and IIR were initially blended through mastication using an open two-roll mill until achieving a uniform mixture. Subsequently, 5 parts per hundred rubber (phr) of ZnO and 2 phr of SA were integrated into the EPDM/IIR rubber blend and compounded for 20 minutes. This blend is commonly termed the ‘carbon master batch (CMB)’. Subsequently, 0.6 phr of DM, 1.5 phr of CZ, 1.5 to 3 phr of sulfur, and 0.5 to 3 phr of peroxide were added to the CMB, leading to the formation of the final rubber compound known as the ‘final master batch (FMB)’. Table 1 provides a comprehensive list of recipes for these rubber compounds.
The rheological properties of the rubber were evaluated using a rubber rheometer (DRM-100, Deakyung Engineering Co., South Korea) at 160°C, by measuring the time needed for the torque to reach 90% of its maximum during curing (T90). An average of three measurements was taken for each sample.
The Mooney viscosity of the rubber samples was determined with a Mooney viscometer (DWV-200C, Deakyung Engineering Co., South Korea) at 125°C for 4 min. Prior to measurement, each sample was pre-heated at 125°C for 1 min to stabilize. The final value for each sample was the average of two measurements.
To evaluate the crosslink density, samples (ca. 1 mg) were immersed in toluene for 24 h. The weight of the dried samples was recorded. The average crosslink density for each sample was calculated from three measurements.
Uniaxial tensile testing followed the ISO 37 protocol, using a universal testing machine (UTM; DUT-500CM, Daekyung Engineering Co., South Korea). The test specimen had a cross-section of 15 mm × 4 mm and a gauge length of 40 mm. The elongation was performed at a crosshead speed of 500 mm/min under a 5 kN load cell at ambient temperature. The average value was calculated using five specimens.
The rebound resilience of the samples was measured using a ball rebound tester (H090, UTS International Co., China) following the ISO 4662 standard. Prior to testing, specimens were maintained at room temperature for 24 h. A ball was dropped onto each sample, and the rebound height was measured. The mean value for each sample was calculated from five measurements.
Compression set tests followed ISO 815 guidelines. The specimens were placed in a cylindrical mold measuring 12.5 mm (± 0.5 mm) × 9 mm and compressed at 125°C for 22 h. After compression, the specimens were removed and allowed to recover for 30 minutes. The final dimensions, particularly the height, were recorded. The average value was calculated from four specimens.
Results and Discussions
When EPDM and IIR were cured individually with sulfur (S), the tensile strength and elongation at break of IIR were higher than those of EPDM. This indicates that IIR exhibits superior mechanical properties under sulfur curing. As shown in Figure 2b, EPDM/IIR blends cured with S and carbon black (CB) at 30 parts per hundred rubber (phr), a compound containing 1.5 phr of S (the same amount used for curing both EPDM and IIR individually) displayed intermediate tensile strength values between those of EPDM and IIR. However, when the S content was increased to 3 phr in the blend, the tensile strength reduced. This suggests that a lower sulfur content of 1.5 phr achieved more effective curing in the EPDM/IIR blend compared to 3 phr.
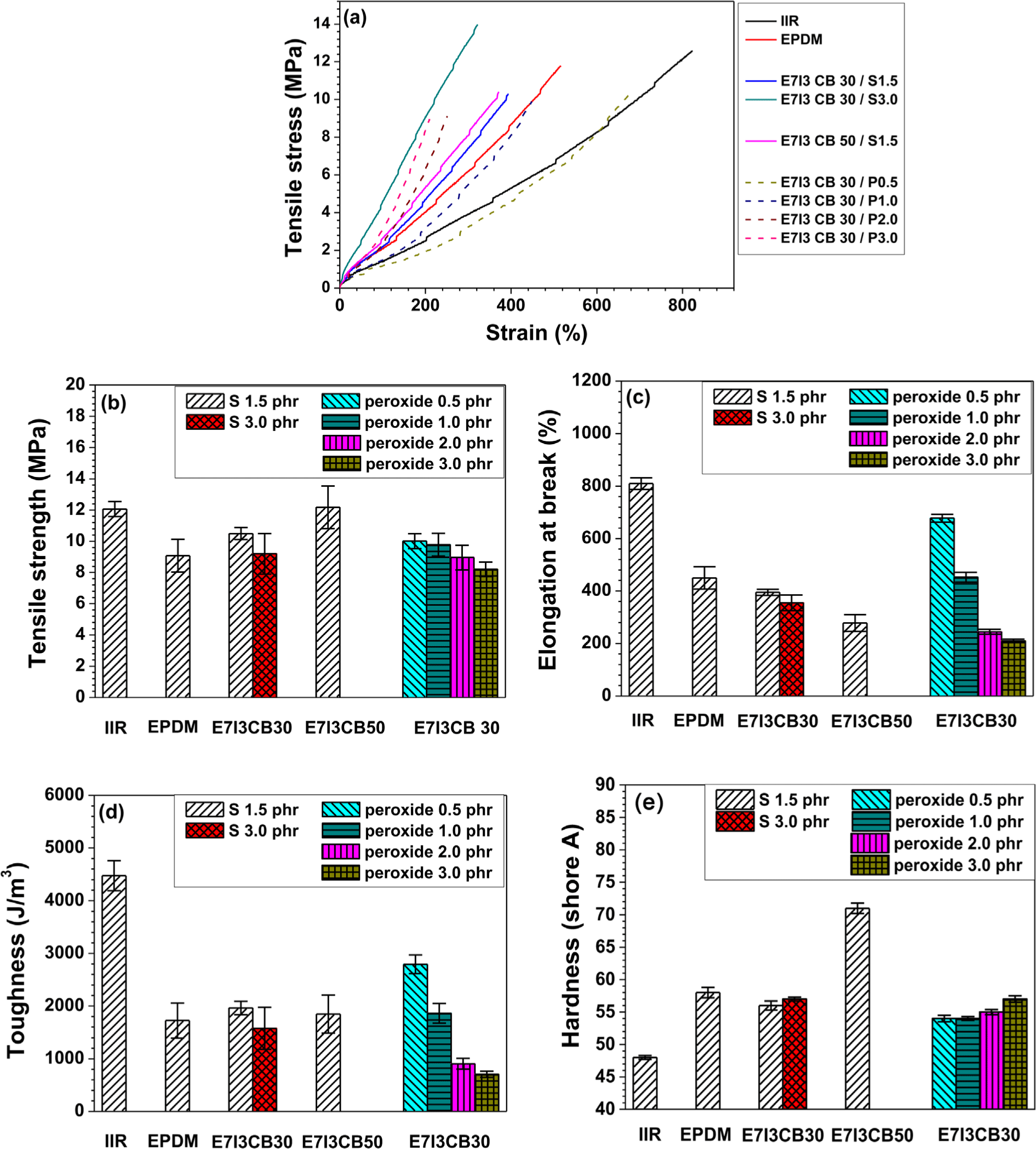
In addition, under the same S content, the tensile strength characteristics corresponded to the proportion of each rubber component in the blend. However, as shown in Figure 3c, in terms of elongation at break, the blend showed values nearly identical to those of the EPDM cured alone, indicating that the elongation at break was dominated by the properties of EPDM.
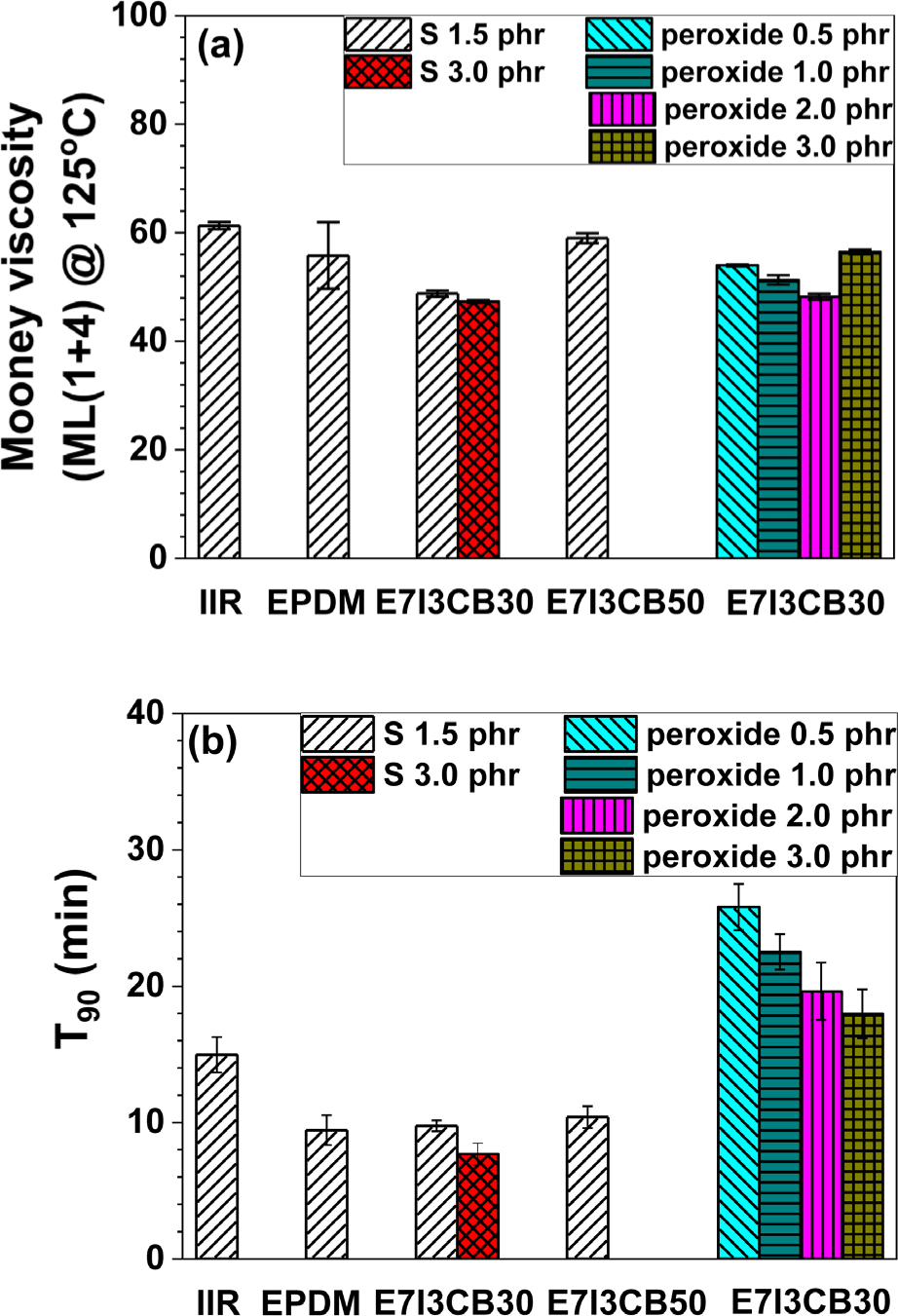
In the blend with an increased CB content of 50 phr, the tensile strength improved as a function of CB content. However, this enhancement in tensile strength was accompanied by a decrease in elongation at break. For the blends cured with peroxide, the tensile strength was similar to that of blends cured with S. However, as the peroxide content increased from 0.5 phr to 3 phr, the tensile strength decreased. Similarly, the elongation at break also showed a declining trend with increasing peroxide content, suggesting that the high tensile strength and elongation at break were achieved at a peroxide content of 0.5 phr.
In terms of toughness, the highest values were observed in the IIR cured alone with sulfur, which exhibited superior tensile strength and elongation at break. The blend containing 0.5 phr of peroxide demonstrated the second highest toughness, effectively compensating for the deficiencies in the properties of EPDM. Regarding hardness, the EPDM cured alone with sulfur exhibited higher hardness than the IIR cured alone with sulfur. In the blend containing 30 phr of CB, the hardness was similar to that of the sulfur-cured EPDM alone, whereas the blend with 50 phr of CB showed a significant increase in hardness. This suggests that, in the sulfur-cured EPDM/IIR blends, the hardness increased with increasing CB concentration, indicating the influence of CB content on hardness. In contrast, no significant changes in hardness were observed with varying peroxide content in the peroxide-cured compounds.
Figure 3 presents the curing and rheological properties of individual S-cured EPDM and IIR, as well as EPDM/IIR blends with varying curing agents and concentrations. In Figure 3a, the viscosity of the uncured rubber was measured using a Mooney viscosity test. Figure 3b shows T90, the time required to reach 90% of the maximum torque, using a rheometer.
For the blends using S and 30 phr of CB, the Mooney viscosity decreased compared to the individual S-cured EPDM and IIR. This indicates that the Mooney viscosity was reduced when EPDM and IIR were blended. In the blend where the CB content increased to 50 phr, the Mooney viscosity increased compared to the blend with 30 phr of CB, demonstrating that higher CB content led to the increased viscosity.
The T90 values for different sulfur and CB contents were similar to those observed for individual S-cured EPDM. In the formulations using peroxide as a curing agent, there was no significant change in Mooney viscosity; however, a considerable increase in curing time (T90) was observed. Peroxide curing typically occurs at higher temperatures than sulfur curing, resulting in longer T90 measurements at the same temperature. This suggests that rubber compounds cured with peroxide may exhibit greater thermal stability, but they may also require longer curing times. In the formulations using both S and peroxide, a common trend was observed: as the T90 values decreased with increasing curing agent loading. This indicates that higher concentrations of curing agents accelerated the curing process.
The swelling test was utilized to determine the degree of curing in rubber composites. Generally, a lower swelling weight ratio in a swelling test indicates a lower degree of swelling, which suggests a more compactly cured rubber with a higher degree of curing. The results in Figure 4(a) and Figure 4(b) are primarily divided into sulfur (S) curing and peroxide curing. Due to the differences in the curing structures of each blend, a direct or absolute comparison between S curing and peroxide curing is not feasible. Therefore, the analysis was conducted separately for each curing agent, focusing on the rubber composition and the content of the curing agent.
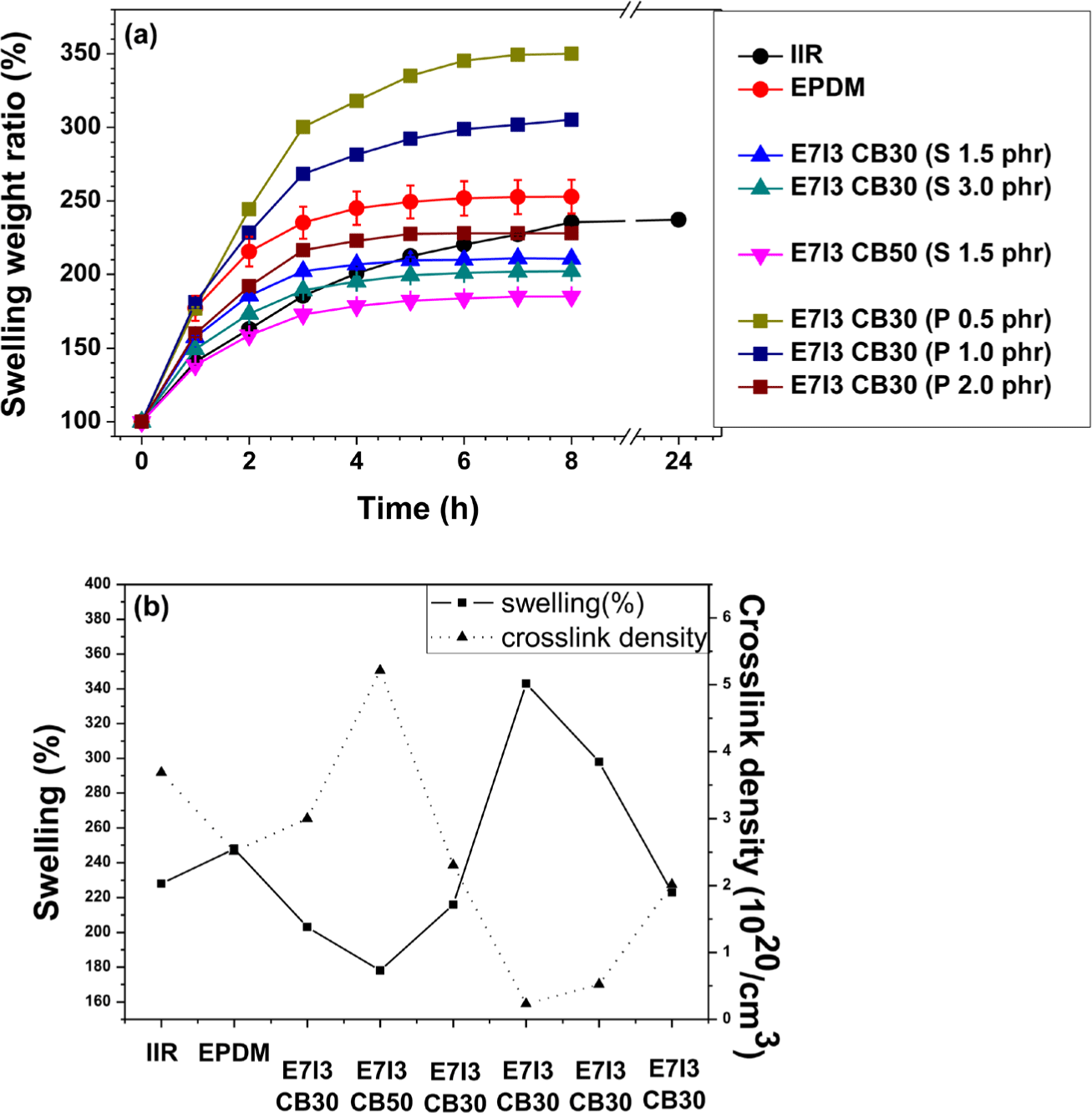
The swelling test results showed a common trend for both S-curing and peroxide-curing: the degree of curing increased with increasing content of the curing agent. In addition, in the formulations where EPDM and IIR were blended, the degree of curing was higher than that of the individual S-cured EPDM and IIR. This suggests good compatibility between EPDM and IIR in the blend.
In addition, the crosslink density of each composite was calculated using the following equations.
The crosslink density ve, defined as the number of elastically active network chains per unit volume for a perfect network, is given by the equation:
The average molecular weight between crosslinks (Mc) according to the Flory-Rehner relationship is expressed as:
Here, vs is the molar volume of the solvent (106.3 cm3/mol for toluene), and vr is the volume fraction of the swollen rubber, defined by:
where Q is the mass of solvent absorbed per unit mass of rubber hydrocarbon, calculated as:
In this equation, W is the weight of the sample after immersion in the solvent for 8 h, and Wd is the weight of the sample after 30 days following the swelling test. The density of the polymer (ρp) is calculated using the equation:
where Wa is the weight of the sample in air, Ws is the weight of the sample in water, and ρwater is the density of water. The Flory-Huggins interaction parameter (χ) is defined as:
Here, δs is the solubility parameter of the solvent (18.3 MPa0.5 for toluene), and δr is the solubility parameter of the polymer (δEPDM = 16.6 MPa0.5 and δIIR = 14.7 MPa0.5). R is the gas constant (8.3144598 J/mol·K), and T is the test temperature (room temperature).
The crosslink density of each composite exhibited an inverse relationship with swelling (%); higher crosslink density indicates a higher degree of curing. Consistent with the swelling results, the increase in the content of both S and peroxide curing agents corresponded to an increase in the degree of curing.
The compression set and rebound resilience of rubber and their composites were evaluated under different conditions: the compression set reflected the behavior of the material under heat and pressure, while rebound resilience is related to impact loading. The compression set measures the irreversible deformation experienced by an elastomer when exposed to a defined compression, duration, and temperature. In contrast, rebound resilience measures the percentage of kinetic energy recovered by the rubber material after impact.
These parameters are influenced by factors such as the type of elastomer, specific composition, and test temperature.
The rebound resilience of S-cured EPDM was higher than that of S-cured IIR, indicating that EPDM has superior elasticity compared to IIR but lower vibration-damping properties. In S-cured blends, the rebound resilience values were intermediate between those of the individually S-cured EPDM and IIR, confirming that blending IIR with EPDM successfully imparted the desired vibration-damping properties to EPDM, which originally lacked these characteristics. In blends cured with peroxide, rebound resilience increased as a function of peroxide content, demonstrating that higher peroxide content enhances elasticity. However, vibration-damping properties decreased with increasing peroxide content, with the optimal damping properties observed at a peroxide content of 0.5 phr.
The compression set (CS) test measures the degree to which an elastomer returns to its original shape after being subjected to temperature and compression. A higher CS value indicates less ability to recover its original shape. When comparing the S-cured EPDM and S-cured IIR individually to the S-cured EPDM/IIR blend, the blend showed intermediate CS value between the cases of S-cured EPDM and IIR. As the S content increased from 1.5 phr to 3 phr, the CS value decreased, showing better recovery properties at 3 phr of S. However, increasing the CB content to 50 phr resulted in an increased CS value. This suggests that as the concentration of the filler increased, the rubber portion decreased, thereby reducing the recovery capacity.
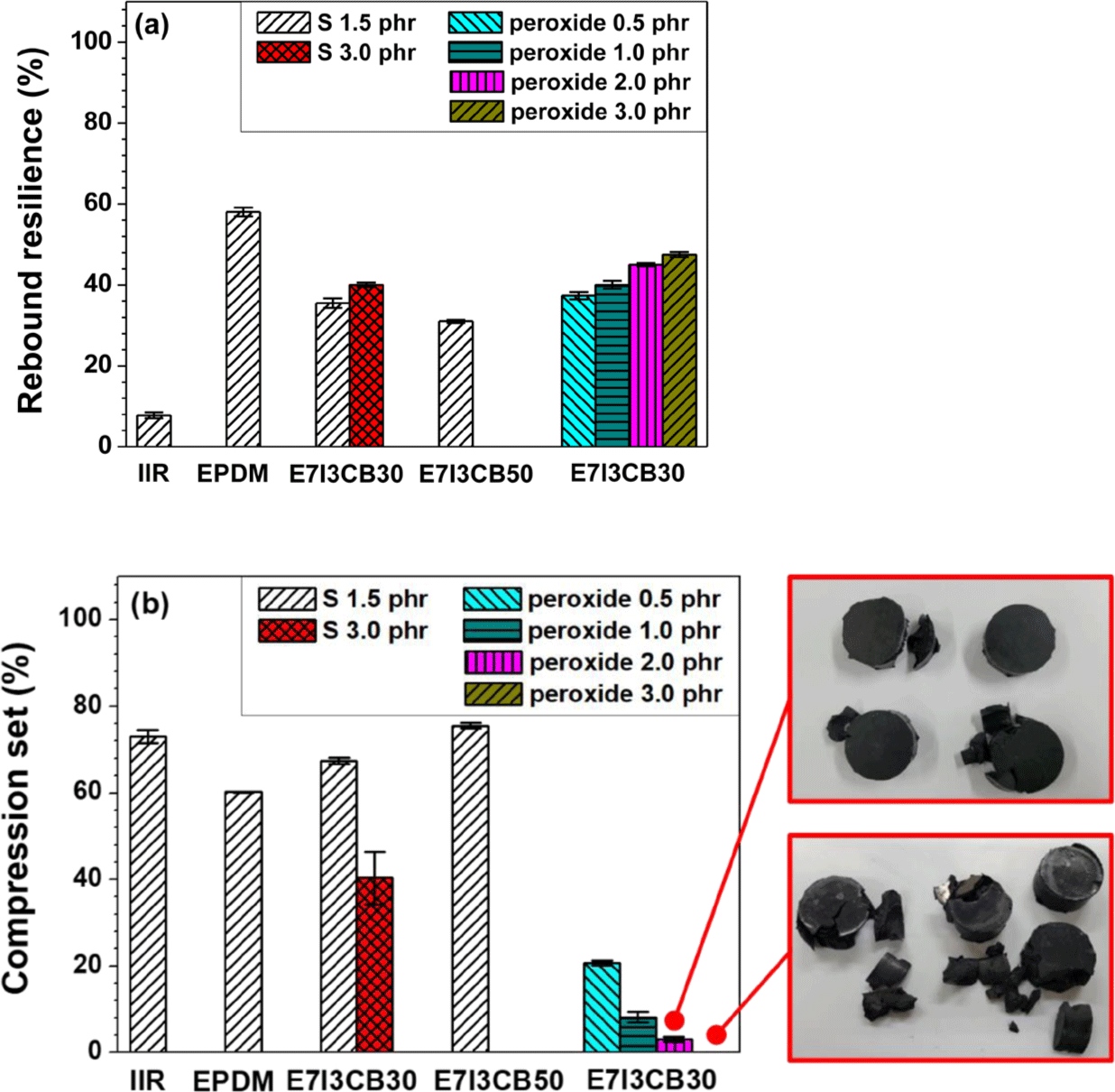
The results for the peroxide-cured blends showed very low CS values, indicating that these blends have superior recovery properties under heat and pressure compared to those cured with sulfur, suggesting greater resistance to thermal and pressure conditions. In addition, as the peroxide content increased from 0.5 phr to 3 phr, the CS value decreased; however, most of the CS specimens at 2 phr and 3 phr showed significant damage, making it difficult to produce reliable CS samples. This can be attributed to the increased crosslink density with higher peroxide content, as indicated by the swelling test results, leading to specimen failure due to excessive crosslinking.
The tensile strength specimens were exposed to the environment (at 100°C for 48 h) for thermal aging test, after which the tensile strength was remeasured. For the formulations cured with sulfur (S), a significant reduction in both tensile strength and elongation at break was observed after the thermal aging test. In contrast, for the blends cured with peroxide, a decrease in tensile strength and elongation was noted only in the blend containing 0.5 phr of peroxide, while almost no reduction in properties was observed in the other peroxide-cured formulations.
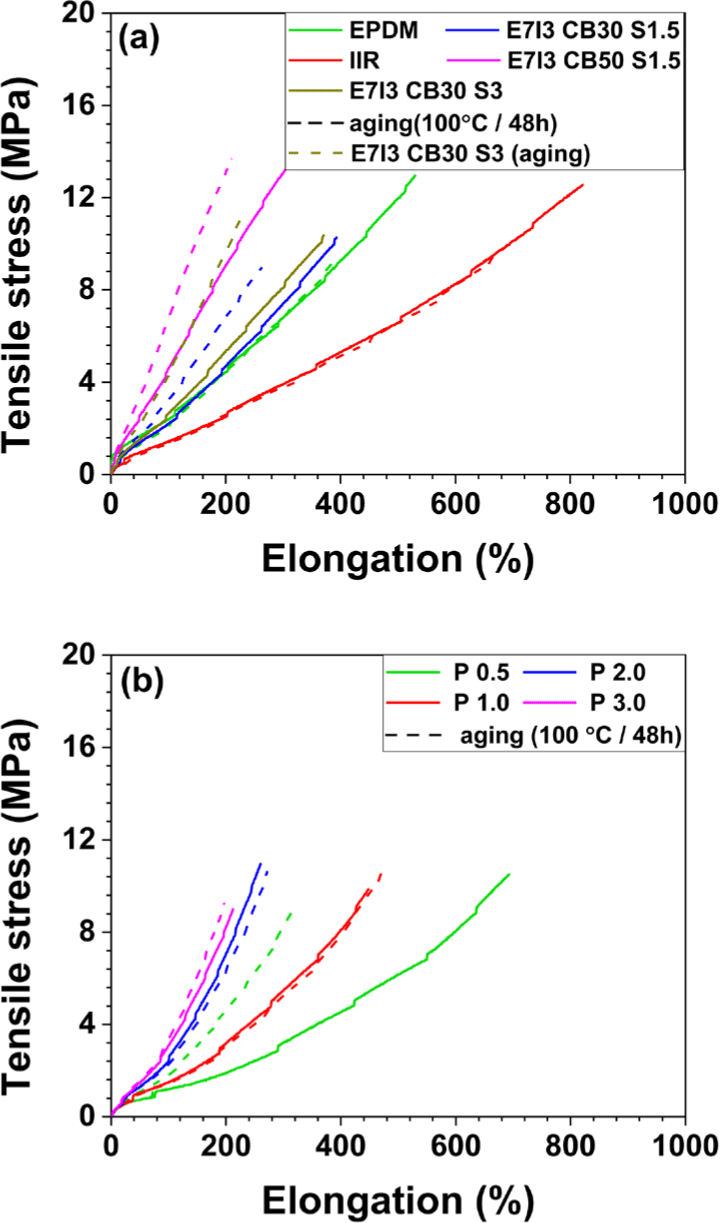
These results indicate that the carbon-carbon (C-C) bonds formed during peroxide curing were more thermally stable than the sulfur-sulfur (S-S) crosslinks created during S curing. This demonstrates that the EPDM/IIR blends cured with peroxide possess superior resistance to thermal aging compared to those cured with sulfur.
Conclusion
This study demonstrated that blending EPDM with IIR and incorporating different curing agents into the blend can effectively enhance the mechanical, damping, and thermal properties of rubber composites. The results showed that the addition of IIR to EPDM improved the shock absorption and anti-vibration characteristics of the resulting composites, while the incorporation of CB into the blend further optimized their mechanical performance. Among the two curing agents evaluated, S and peroxide, the peroxide-cured blends exhibited superior thermal stability and resistance to aging, primarily due to the formation of more stable C–C crosslinks. These peroxide-cured blends also maintained desirable mechanical properties, such as elasticity and tensile strength, especially at a peroxide content of 0.5 phr, which was found to provide the optimal balance between elasticity and anti-vibration properties. In contrast, sulfur curing resulted in higher tensile strength but demonstrated less stability under thermal aging conditions due to the relatively unstable S–S crosslinks. Overall, the findings of this study provide valuable insights into optimizing the formulation of rubber composites by selecting appropriate curing agents and their concentrations. The study highlights the potential of using peroxide curing to achieve enhanced thermal and mechanical performance, making it a promising approach for developing rubber materials suitable for applications that require superior durability and vibration damping properties. This research contributes to the advancement of rubber composite technology for various industrial applications, particularly in the automotive and construction sectors.