Introduction
Lithium-ion batteries (LIBs) have become indispensable in modern energy-storage applications, playing a pivotal role in the widespread adoption of electric vehicles (EVs), renewable-energy integration, and portable electronic devices.1,2 Their high-energy density, long-cycle life, and reliability make LIBs a cornerstone of sustainable energy solutions. However, the rapid expansion of LIB production has also raised critical concerns regarding environmental sustainability, energy consumption, and cost-effectiveness. As global demand for LIBs continues to surge, addressing these challenges has become paramount for the advancement of next-generation battery-manufacturing technologies.3,4
Conventional LIB manufacturing predominantly relies on wet-processing methods, in which active materials, conductive additives, and polymer binders are dispersed in an organic solvent such as N-methyl-2-pyrrolidone (NMP) to form a slurry. This slurry is coated onto a metal current collector and then dried to remove the solvent, calendered to adjust the electrode thickness, and slit to the desired dimensions. A final vacuum-drying step eliminates any residual solvents.5,6 Polyvinylidene fluoride (PVDF) is commonly used as a binder in wet processing, requiring NMP as a solvent. Because NMP is toxic, solvent recovery is essential to mitigate environmental and health risks.7,8 Furthermore, coating, drying, and solvent-recovery stages collectively account for nearly 50% of the total energy consumption in electrode manufacturing, escalating both cost and carbon footprint.9-12 In addition, wet processing often encounters difficulties in achieving uniform, thick-electrode structures, leading to defects such as cracking and delamination that hinder electrochemical performance and mechanical stability.13
Researchers have been exploring alternative manufacturing approaches to address these challenges. One promising solution is dry-electrode manufacturing, which eliminates solvent use and significantly reduces energy consumption.8,14 By bypassing the solvent-evaporation and recovery stages, the dry process simplifies production, lowers costs, and mitigates environmental impact. Moreover, it facilitates the fabrication of thick electrodes, which are critical for achieving high-energy-density LIBs. As a result, dry-electrode technology has garnered substantial attention as a next-generation battery-manufacturing method.8,15,16
Recent advancements in dry-electrode technology— exemplified by Tesla’s adoption of Maxwell Technologies’ dry-battery electrode (DBE) process—have demonstrated the feasibility of large-scale implementation.17,18 Major battery manufacturers, including Samsung SDI, LG Energy Solution, and SK On, are also exploring dry-electrode fabrication to strengthen their market competitiveness.19,20 Key innovations such as roll-to-roll coating, hot-pressing, and PTFE-binder fibrillation have significantly improved material uniformity, mechanical stability, and scalability. In turn, the production of high-energy-density electrodes has become more viable, marking a major step forward in LIB technology. Despite its potential, dry-electrode technology faces several challenges before it can achieve widespread commercialization. Issues such as binder optimization, material homogeneity, and large-scale process adaptation remain key barriers. Continued research and development are needed to refine the dry process and establish its viability for mass production.
This review provides a comprehensive analysis of dry-electrode manufacturing, examining fundamental principles, recent technological advancements, and practical applications. By comparing the dry process with conventional wet processing, the review highlights the economic, environmental, and technical advantages of solvent-free electrode fabrication. Current limitations and prospective research directions are also outlined, offering insights into the future trajectory of dry-electrode technology in LIB production. Ultimately, this study underscores the transformative potential of dry-electrode manufacturing in creating sustainable energy-storage solutions and meeting growing global demand for high-performance LIBs.
Background and Motivation
Figure 1 compares a conventional battery-manufacturing process (wet) with a dry process. Wet processing involves dispersing active materials, conductive additives, and polymer binders into an organic solvent (e.g., NMP). This mixture forms a homogeneous slurry, which is coated onto metallic current collectors—commonly aluminum for cathodes and copper for anodes. After coating, the electrodes undergo drying to evaporate the solvent, followed by calendering to adjust thickness and enhance mechanical integrity. Slitting tailors the electrode dimensions, and final vacuum drying completes the fabrication process.
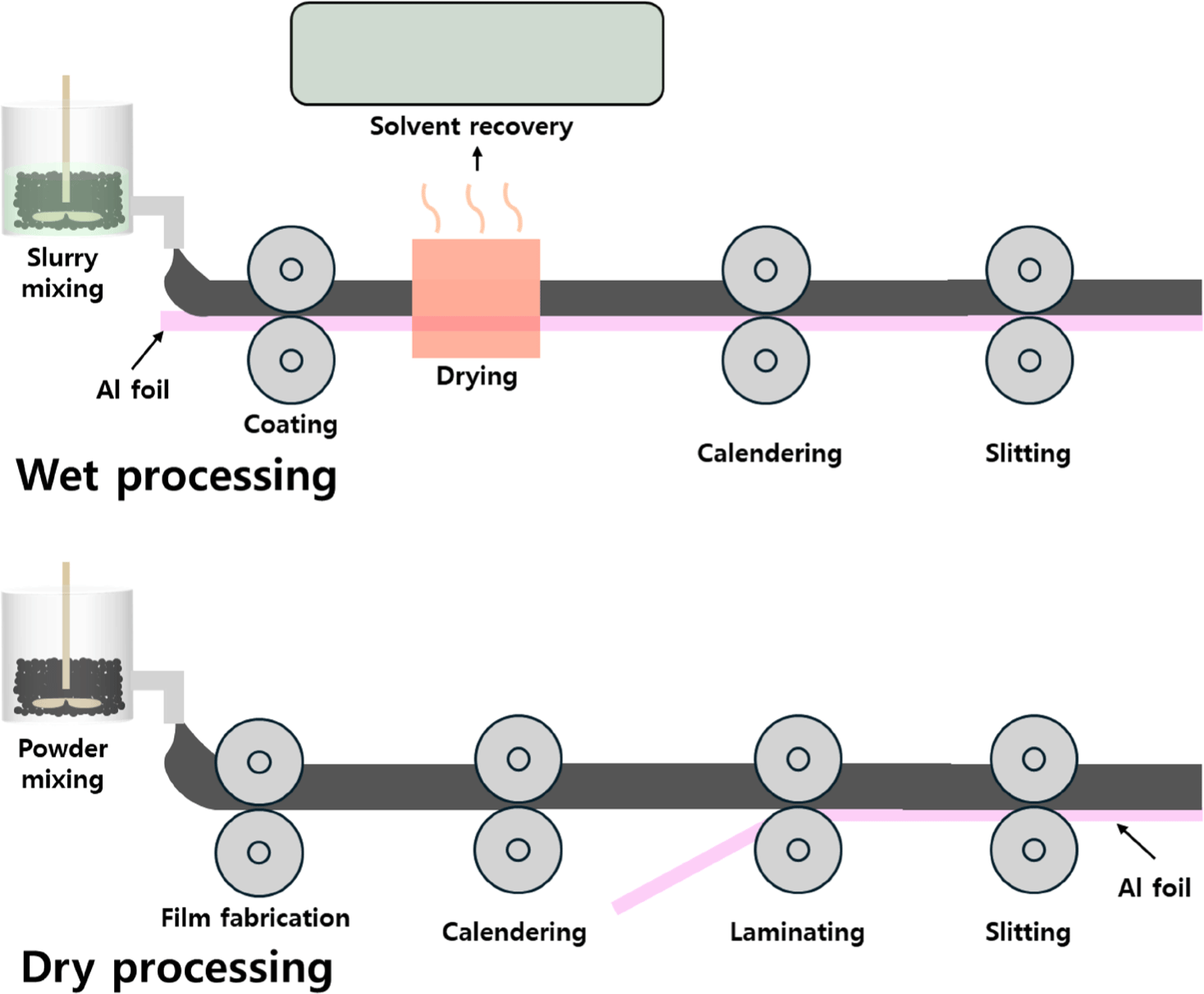
Because NMP is toxic, an extensive solvent-recovery system is necessary to reduce environmental and health risks.21,22 Furthermore, coating, drying, and solvent-recovery steps represent roughly half of the total energy consumption in electrode fabrication, contributing to high costs and increased carbon emissions.23-25 Wet processing also struggles with thick-electrode manufacturing: during drying, the electrode can shrink and crack, yielding poor mechanical properties and uneven material distribution. These defects degrade electrochemical performance and limit the scalability of high-energy-density LIBs.15,16,26
Dry-electrode manufacturing eliminates solvent use entirely. This solvent-free approach mixes active materials, conductive additives, and binders in solid-state form, followed by dry-coating or pressing methods to form electrodes. By removing the need for energy-intensive drying and solvent recovery, dry-electrode technology lowers energy consumption and operational costs.27-29
A chief advantage of dry processing is the ability to circumvent the shrinkage and cracking issues in thick electrodes. With no solvent to evaporate, the electrode structure remains more stable, and mechanical integrity is improved, particularly important for high-energy-density applications.14,15,30,31 In addition, PTFE serves as a solvent-free binder, thus avoiding the toxicity associated with NMP while simplifying manufacturing complexity and reducing costs.26,28 Dry-electrode production therefore emerges as a scalable, cost-effective, and eco-friendly innovation that helps meet global sustainability targets.
Types of Dry Electrode Manufacturing Processes
Electrostatic-spray deposition relies on electrostatic forces to coat current collectors with charged, dry-powder particles composed of active materials, conductive additives, and binders. The grounded substrate attracts these particles, which form a uniform layer without using solvents— substantially lowering energy consumption and production costs. Precise control over thickness and material distribution is another benefit. Compared to conventional wet coating, electrostatic-spray deposition often requires less binder and fewer conductive additives while maintaining comparable electrochemical performance.27,32,33 For example, Pan et al. demonstrated an LCO electrode fabricated via electrostatic spraying that achieved 77% capacity retention after 100 cycles at 0.3C, using only 1 wt% total binder and conductive additives.27 However, scaling up remains challenging: ensuring uniform powder deposition, precise thickness control, and integration into existing manufacturing lines must be addressed for large-scale adoption.
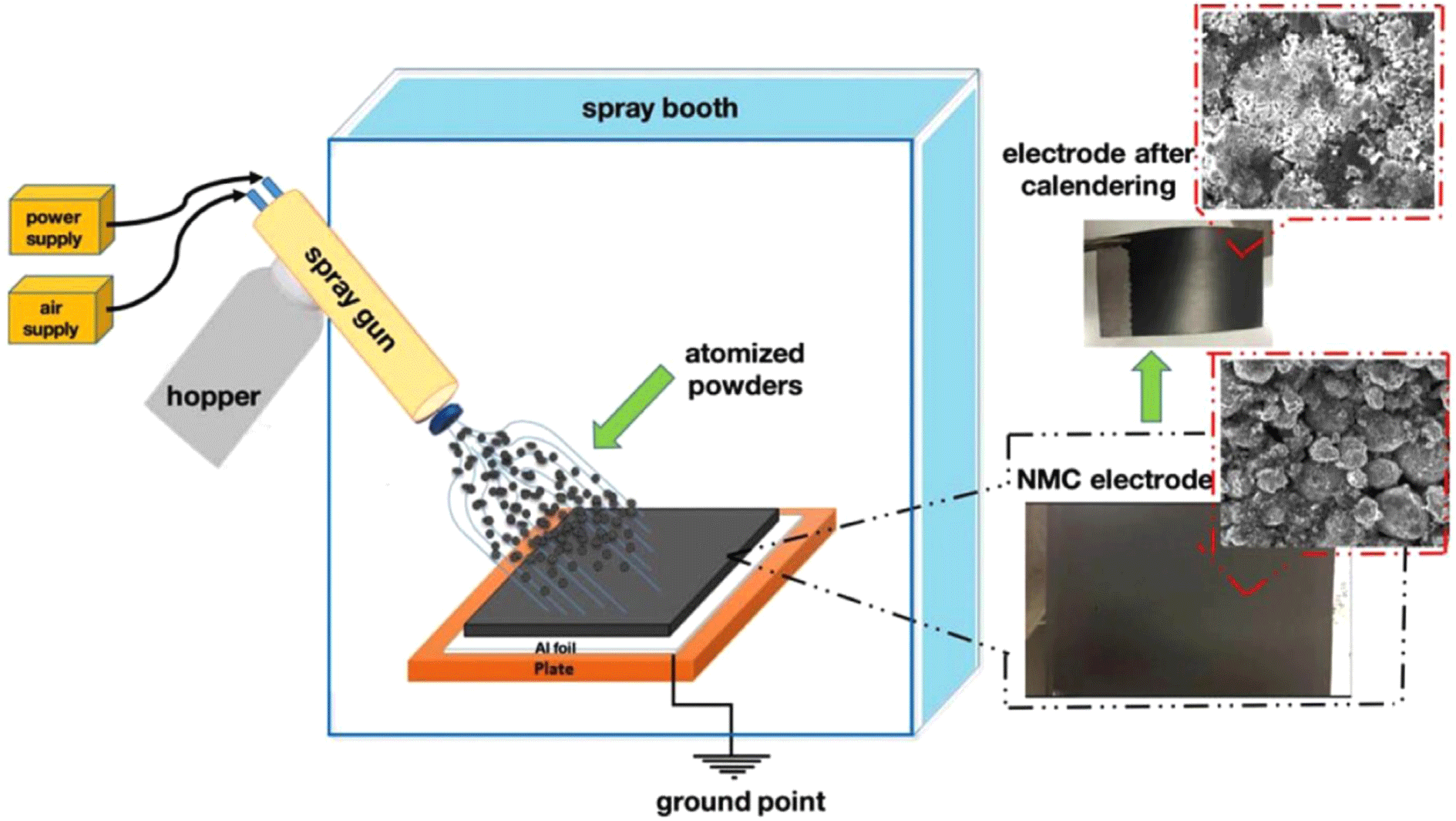
Pressing-based fabrication produces electrodes by compressing dry powders under high temperature and pressure. This approach triggers phase transitions in polymers, enabling the formation of thick films with high-energy density. Typically, the dry-powder mixture—consisting of active materials, conductive additives, and binder—is first heated and then compressed to form a dense film.8,34 Park et al. showed that pressing-based NCM712 electrodes achieved an area capacity of 17.6 mAh/cm2, demonstrating the method’s promise.8 Advantages include precise control over temperature and pressure, which broadens binder compatibility and speeds production. However, industrial scaling poses challenges: pressing can demand high pressures, and designs remain polymer-dependent. Material homogeneity and particle-size distribution also require careful management to ensure consistent electrochemical performance.
Extrusion adapts injection-molding concepts to dry-elect-rode manufacturing. Active materials, conductive additives, and binders are mixed and heated to form a continuous film, with thermoplastic polymers facilitating uniform blending.36 Passerini et al. demonstrated extrusion-based fabrication of LTO and LFO cathodes, achieving area capacities over 13 mAh/cm2.37 Further steps such as calendering, lamination, debinding, and sintering produce a porous structure that enhances electrochemical performance. Extrusion supports high-energy-density electrodes for materials like LFP, LTO, and NCM. Nevertheless, it often demands higher binder usage, longer processing times, and post-processing at elevated temperatures, all of which can slow commercialization.35-37 Precise control over particle size, temperature, and residence time is also critical to avoid nonuniform distribution and to preserve optimal electrochemical properties. Even so, extrusion enables the construction of tailored electrode architectures with controlled porosity, making it a noteworthy candidate for future dry-electrode technologies.
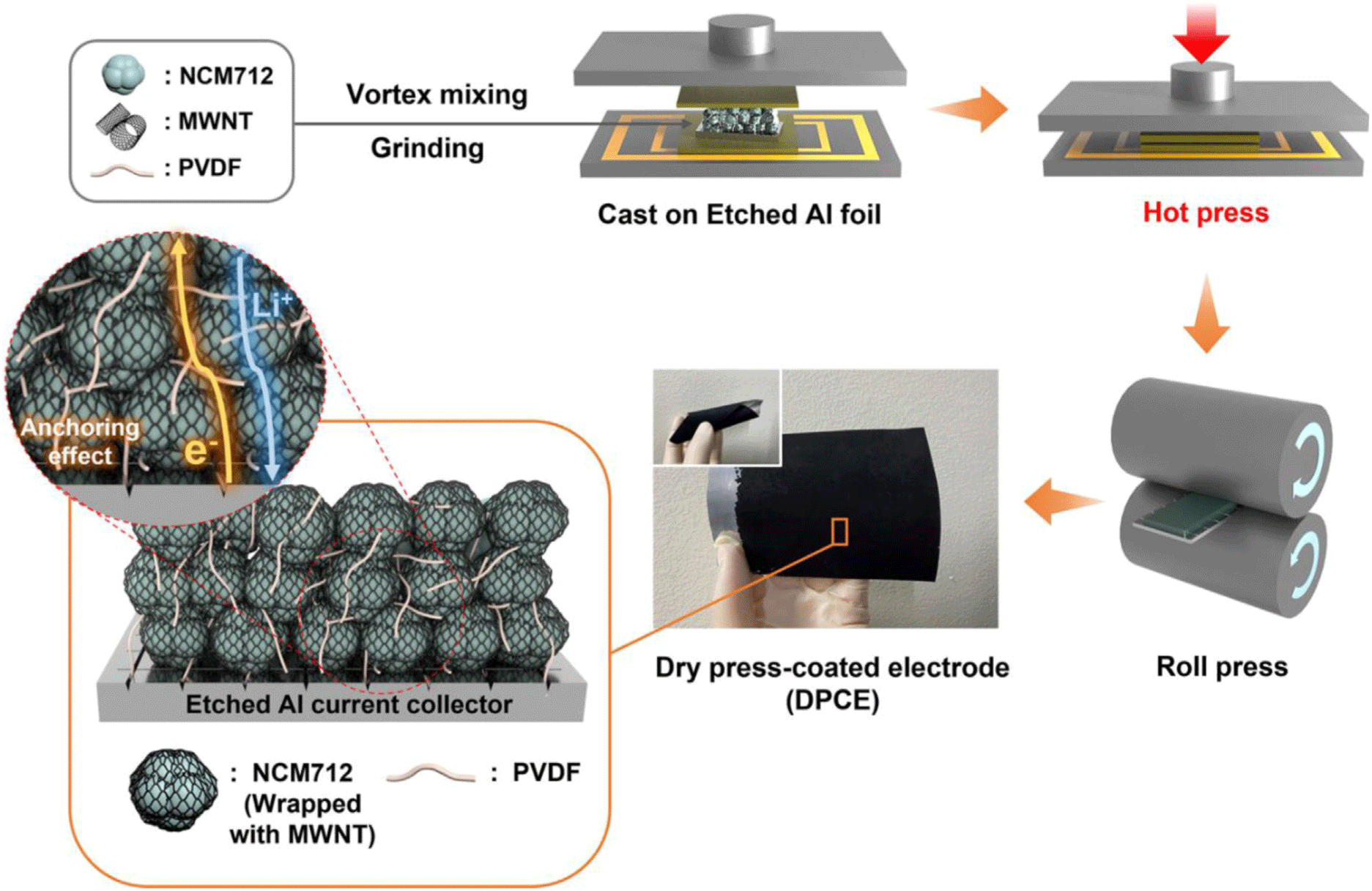
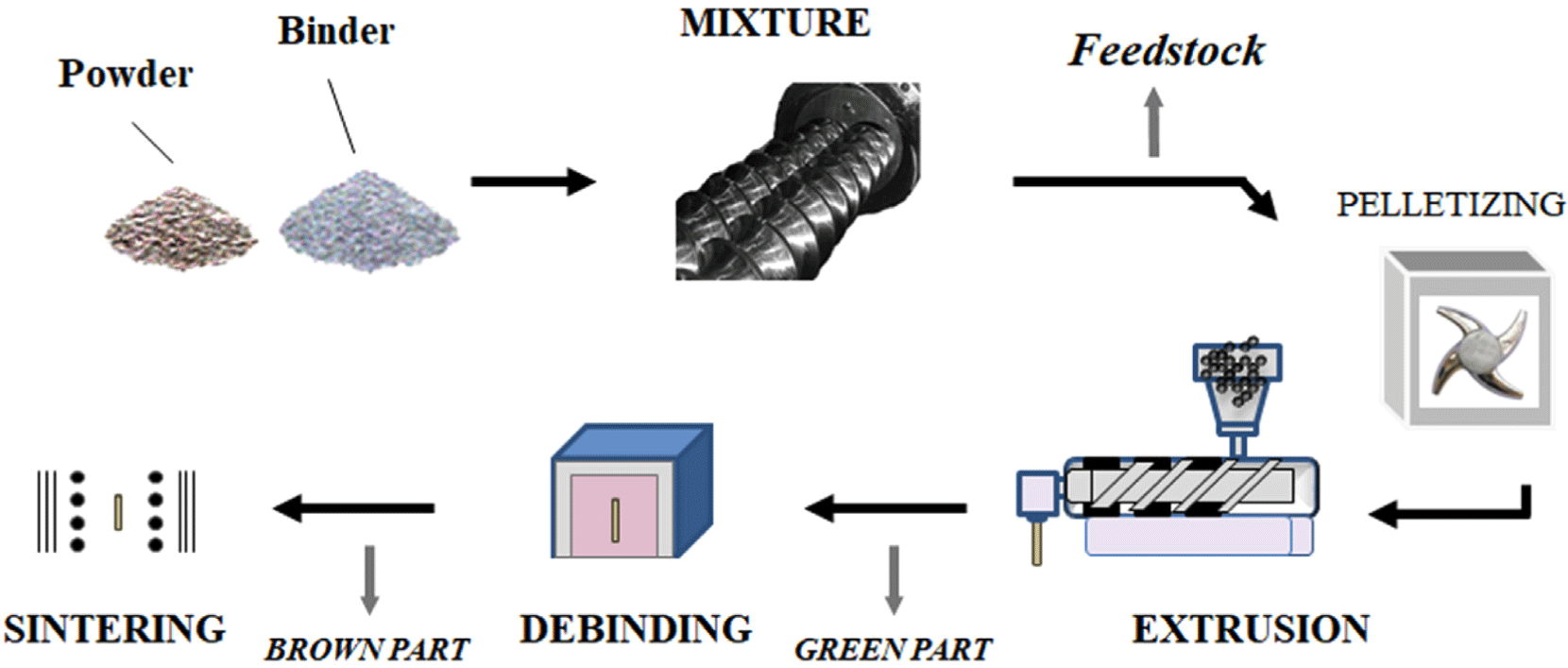
Roll-mill processing is the most widely implemented dry-electrode fabrication method, using shear mixing and rolling to produce uniform electrode films—even at high thicknesses. High-shear forces between rotating rollers thoroughly disperse dry powders, forming continuous electrode films with excellent uniformity.14,26,28 Its compatibility with large-scale, roll-to-roll manufacturing makes roll-mill processing particularly attractive. For instance, Maxwell-Tesla uses a two-roll milling-based dry-coating process to create free-standing electrode films at scale, while Fraunhofer IWS has developed a multi-roll system that integrates compaction and lamination to reduce costs.17,18,38
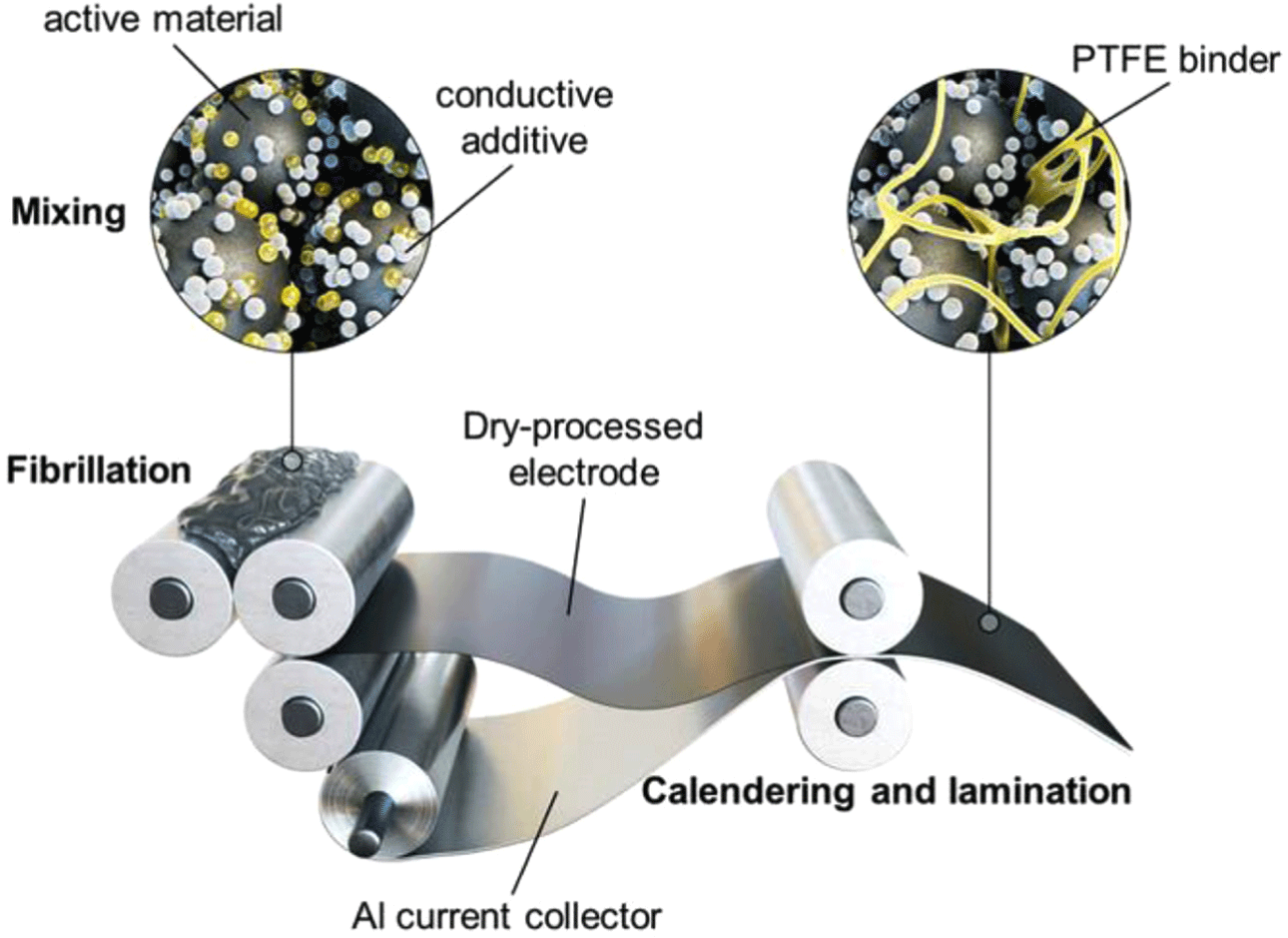
PTFE acts as the main binder in roll-mill processing. Under shear stress, PTFE forms fibrous networks that improve mechanical integrity and flexibility. However, the magnitude of shear forces depends on particle-size distribution; inadequate control risks film defects (e.g., cracks, edge deformation, or delamination).39 Although PTFE-based formulations are popular, alternative binders with enhanced processability, and sustainability are actively under study. Despite these challenges, roll-mill processing remains a dominant technique for solvent-free electrode manufacturing, offering scalable and efficient pathways to next-generation battery electrodes.
Microstructure and PTFE Fibrillation
Among the four dry electrode manufacturing techniques, roll mill processing is the most widely adopted method, primarily utilizing PTFE as a binder. PTFE is well-suited for dry processing due to its high thermal resistance, chemical stability, and electrochemical durability. Unlike conventional slurry-cast electrodes that often exhibit "moss-like" PVDF morphologies, solvent-free electrodes demonstrate a hierarchical PTFE fibril network, which spans tens of active material particles and facilitates improved ionic and electronic conductivity by ensuring open pores and uniform material distribution.40
To effectively incorporate PTFE in dry electrodes, fibrillation is a crucial step. The unique polymer structure of PTFE consists of a carbon backbone bonded with four fluorine atoms per monomer unit, forming strong C-F bonds that allow PTFE to extend into a fibrous framework. This structural characteristic results in low van der Waals interactions and weak intermolecular stacking, making PTFE highly susceptible to fibrillation under shear forces. During processing, PTFE particles deform and interconnect, forming an entangled network that enhances mechanical integrity and material cohesion.39-41
During shear mixing, rough surface particles interlock with PTFE crystallites, providing anchoring points for fibrillation. Initial fibrils, often a few microns in diameter, extend as particles slide past each other under shear forces. As the mixing process continues, secondary and tertiary fibrils emerge, forming a branch-like morphology that improves electrode uniformity. This hierarchical fibril structure effectively links active material particles and conductive additives, reinforcing both mechanical strength and electrical conductivity.39-41
Figure 6 illustrates the PTFE fibrillation process through schematic representation and SEM imaging.40 Initially, large PTFE particles deform and adhere to the active material surface. At this stage, primary fibrillation occurs, forming small fiber bundles. As shear force continues to be applied, secondary fibrillation takes place, where additional PTFE strands extend from the initial fibers, connecting surrounding active material particles. This multi-step fibrillation mechanism enhances electrode robustness and improves contact between active materials and conductive agents, ultimately contributing to superior electrochemical performance.40,41
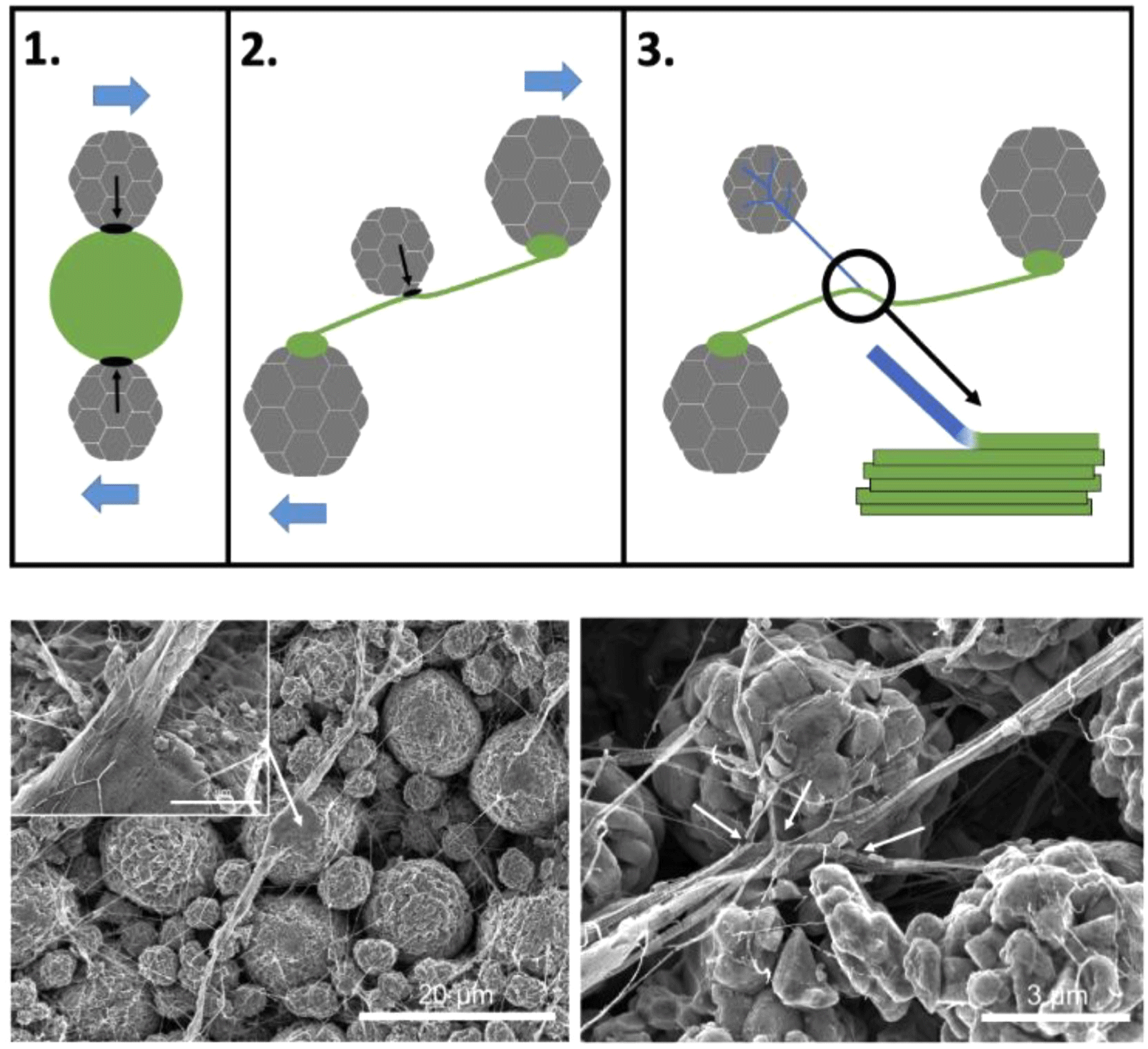
Temperature plays a significant role in optimizing PTFE fibrillation. As temperature increases, the kinetic energy of PTFE molecules rises, altering the polymer chain structure and reducing bond strength. This transition facilitates fibrillation by making PTFE more deformable.42,43
Dynamic MechanicalAnalysis (DMA) data reveals a plateau region in the storage modulus between 60-110°C, indicating that PTFE maintains a stable fibrillar structure within this temperature range. In this phase, lamellar PTFE structures transition into fibrillar networks, improving mechanical stability and adhesion to active material particles. However, beyond 110°C, the storage modulus begins to decrease, correlating with PTFE’s glass transition temperature (Tg) of ~118°C. At temperatures exceeding Tg, PTFE exhibits fluid-like properties, leading to molecular rearrangement and film formation rather than fibrillation. Figure 7 presents the DMA analysis of PTFE, demonstrating how the fibrillation process is optimized within specific temperature ranges. This analysis underscores the importance of carefully controlling processing temperatures to ensure stable PTFE network formation while preventing excessive molecular mobility that may compromise electrode integrity.39
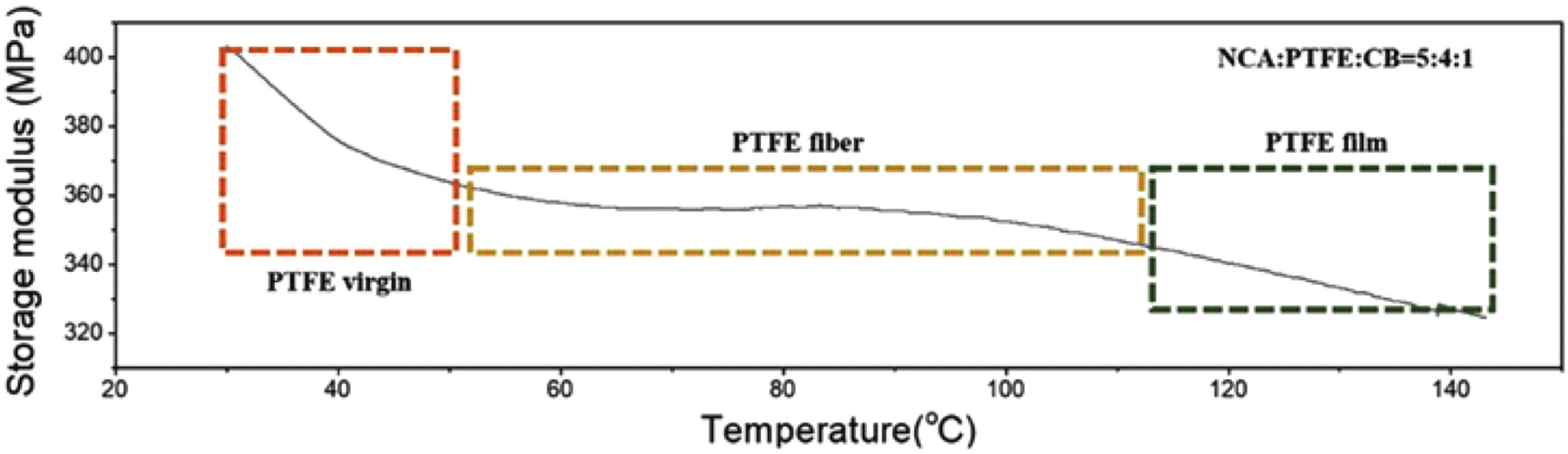
-
Mechanical Integrity: The interconnected fibrils enhance electrode durability and flexibility.
-
Electrochemical Performance: Uniform fibril distribution minimizes resistance and facilitates ion transport.
-
Scalability: PTFE fibrillation supports roll-to-roll manufacturing for industrial-scale production.
Applications of Dry Electrode Technology
Dry electrode technology has emerged as a transformative approach in LIB manufacturing, offering significant advantages over conventional methods. Its versatility and scalability have driven advancements across multiple application areas, from enhancing energy density to supporting next-generation battery systems.
One of the primary applications of dry electrode technology is its ability to produce thick electrodes, which are critical for achieving high energy densities. By eliminating the solvent-drying step inherent in wet processes, dry manufacturing minimizes issues such as binder migration and structural defects, including cracking and delamination. This ensures uniform material distribution and mechanical integrity, even in electrodes with high active material loadings. For example, roll mill processes enable the fabrication of thick cathodes exceeding 100 μm in thickness while maintaining consistent porosity and ionic pathways. This results in superior charge transport and electrochemical performance. These characteristics make dry-manufactured thick electrodes particularly valuable for EV and grid-scale energy storage systems, where achieving high energy density is essential.8,15,39
Dry electrode technology’s compatibility with all-solid-state batteries (ASSBs) marks another significant advancement. ASSBs, which use solid electrolytes instead of liquid ones, require electrode fabrication methods that minimize porosity and ensure intimate contact between the electrolyte and active materials. Dry processes, such as hot pressing and roll mill techniques, effectively meet these demands by producing dense, uniform films that enhance solid-solid interfaces and reduce interfacial resistance. Furthermore, the absence of solvents eliminates chemical incompatibility issues commonly encountered in conventional wet processes.37,44,45 These advantages position dry electrode manufacturing as a crucial enabler for the commercialization of ASSBs, which offer enhanced safety and energy density compared to traditional LIBs.
In addition to performance improvements, dry electrode technology significantly enhances the environmental sustainability of LIB manufacturing. By eliminating the use of toxic solvents such as NMP, dry processes reduce hazardous emissions and the energy consumption associated with solvent recovery and drying stages. This aligns with global sustainability goals and regulatory pressures to lower the carbon footprint of battery production. Moreover, the streamlined workflow of dry processes minimizes material waste and reduces operational costs, making dry electrode technology an economically and environmentally favorable solution for large-scale battery manufacturing.27,46,47
Challenges and Limitations
Dry electrode manufacturing has attracted considerable attention for its potential to eliminate solvent use, reduce energy consumption, and cut production costs in lithium-ion battery (LIB) fabrication. Nevertheless, several issues currently hinder large-scale industrial adoption. One of the foremost challenges is material stability, particularly concerning polytetrafluoroethylene (PTFE), which is frequently employed as a binder due to its excellent mechanical and electrochemical resilience. Despite these advantages, PTFE’s low lowest unoccupied molecular orbital (LUMO) level makes it prone to decomposition during lithiation, causing reduced initial coulombic efficiency (ICE) and diminished cycle life. Although electrolyte additives such as fluoroethylene carbonate (FEC) can form a protective solid electrolyte interphase (SEI) to mitigate this degradation, further research is needed to ensure compatibility across diverse electrode chemistries.48,49
Another significant limitation involves scalability and uniformity in high-volume production settings. Roll-to-roll processing, often used for solvent-free electrode fabrication, requires precise control over parameters such as roller speed, temperature, and pressure to maintain consistent fibrillation. Any fluctuation in these parameters can lead to defects—particularly in thick electrodes designed to achieve higher energy density. Moreover, the absence of solvent-based processing can make it more challenging to regulate pore structures and ionic pathways. Balancing mechanical integrity with efficient ion transport thus becomes a key hurdle.50,51
A further concern is the classification of PTFE as part of the broader per- and polyfluoroalkyl substances (PFAS) family, which has been subject to growing regulatory scrutiny due to potential environmental persistence. While PTFE offers excellent mechanical stability and fibrillation properties, ongoing discussions about PFAS usage and disposal may lead to stricter regulations or even phased bans in certain regions.52-53 In response, researchers are actively investigating fluorine-free or partially fluorinated polymers that can mimic the fibrillation behavior of PTFE without carrying the same environmental liabilities. Examples include modified polyethylene-based binders, cellulose-derived polymers, or advanced co-polymers engineered for shear-induced fibrillation.54-56 Although these alternatives show promise in initial laboratory-scale trials, achieving the same level of mechanical robustness and electrode longevity as PTFE remains a significant challenge. Further research must address how these new binders interact with active materials, how they behave under repeated cycling, and whether they can be cost-effectively scaled up.
Additionally, integrating dry electrode processes with emerging materials such as silicon anodes and lithium metal adds another layer of complexity. These high-capacity materials can undergo considerable volume changes during cycling, making them susceptible to cracking and loss of active material. Dry manufacturing must be tailored to accommodate these behaviors through specialized binders and conductive additives.57-59 Finally, although dry processing is likely to reduce operational and energy costs over time, specialized equipment—such as high-shear mixers, precision roll mills with multi-zone temperature control, and advanced tension-monitoring systems—requires substantial initial investment. This can deter smaller manufacturers from adopting the technology and underscores the importance of cost-effective engineering solutions.
In summary, the current challenges facing dry electrode manufacturing revolve around PTFE stability, roll-to-roll uniformity, thick electrode design, PFAS-related regulatory concerns, and integration with emerging high-performance battery materials. Addressing these challenges through materials research, process optimization, and cost-effective equipment design will be vital for the broader implementation of this promising approach.
Outlook
Dry electrode technology holds significant promise for revolutionizing lithium-ion battery manufacturing. Ongoing innovations in binder materials aim to replace or complement PTFE with polymers that are more sustainable, less chemically reactive, and still capable of fibrillation under shear forces. Such developments could expand the scope of solvent-free processes to include a broader range of electrode chemistries, while aligning with increasingly stringent environmental regulations.
From a process engineering perspective, refining roll-to-roll manufacturing parameters remains crucial for industrial scalability. Digital monitoring, real-time feedback systems, and advanced modeling tools can enhance fibrillation consistency, minimize defects, and boost throughput. In parallel, continued progress in automation promises to streamline quality control and reduce operational overhead across large-scale production lines.
Beyond conventional Li-ion batteries, dry fabrication methods show strong potential for next-generation energy storage technologies. In particular, all-solid-state batteries (ASSBs)—which rely on dense, uniform electrodes—could benefit significantly from solvent-free manufacturing, as it avoids many of the solvent-induced issues that degrade solid electrolytes. Moreover, high-capacity materials such as silicon or lithium metal may be more easily integrated through dry processes, where controlled powder mixing and fibrillation can help manage volume expansion and interface compatibility.
Industry interest in this area is already evident. Tesla’s adoption of Maxwell Technologies’ dry electrode process in 4680 cells illustrates how large-scale implementation can reduce production costs, increase energy density, and lower environmental impact. As researchers explore greener binder alternatives to address PFAS-related concerns, and as roll-to-roll systems become more robust through advanced sensors and multi-zone control, rapid growth in the adoption of dry electrode manufacturing across the battery sector seems likely.
In conclusion, dry electrode manufacturing embodies a transformative leap in lithium-ion battery production by delivering a solvent-free approach that is inherently more sustainable, energy-efficient, and scalable. While important questions regarding binder compatibility, process optimization, PFAS regulations, and equipment investment remain, ongoing research and cross-industry collaboration are poised to resolve outstanding issues. If these efforts are successful, dry electrode technology could redefine the future of battery manufacturing, paving the way for cleaner, more cost-effective, and higher-performance energy storage systems.