Introduction
해양 고무펜더의 주요 기능은 Figure 1에서 보는 바와 같이 선착장 부두에 설치되어 선박이 접안할 때 또는 계류장 파랑이나 바람으로 인해 동요할 때에 선체와 접안시설 사이의 충격력과 마찰력으로 인한 선체의 손상을 방지하기 위한 역할을 담당하고 있으며 주로 고무제품을 이용하고 있다. 고무펜더를 설계하고 생산할 때에 제조업체는 선체 및 도킹 선박에 작용하는 반력과 선박의 운동 에너지를 흡수 한 후의 변형 등 다양한 조건에 따른 고무펜더의 개발이 요구되고 있으며, 특히 고무펜더의 사용수명 및 교체주기를 예측하는 것은 선체의 안전 및 항구시설의 유지 관리에 매우 중요하다 하겠다. 하지만 지금까지 고무펜더의 사용수명에 관한 연구는 Terauchi1 등이 일본 주위의 항구에 설치된 고무펜더에 대해 사용된 기간에 따른 결함, 파손 등을 통해 V형 펜더의 수명은 10년에서 20년 정도임을 보고하였으며, 고무펜더 몸체의 결함을 측정하여 잔존수명을 평가하는 유지 관리 가이드 라인2이 출판 되었으나, 실제 교체 기록이나 사용기간에 대한 자료들은 보고되지 않은 실정이다. 따라서 본 연구에서는 해양 고무펜더의 내구성을 평가하기 위해 제품설계 및 개발단계에서부터 사용수명을 예측하고 평가하는 방법을 개발하여 SSP-300H와 HSP-300H 모델에 적용하여 사용수명을 예측하였다.
개발된 고무펜더의 사용수명 예측방법은 Figure 2에서와 같이 펜더에 사용되는 고무소재에 대한 물성시험을 통해 펜더 특성해석에 필요한 소재 물성을 구하고 이를 이용하여 펜더에 대한 유한요소 해석을 수행하여 하중과 변위와의 특성과 최대 변형률 발생부위와 크기를 파악한다. 또한 고무펜더가 반복하중에 의한 인장-압축변위를 재현할 수 있는 3차원 덤벨형 시편을 설계, 제작3하여 다양한 조건에서 피로시험을 수행하여 펜더에 적용되는 고무소재에 대한 변위와 피로수명과의 관계를 도출한 후 유한요소 해석을 통해 얻어진 3차원 덤벨형 시편의 변위와 변형률과의 관계를 이용하여 최대 변형률 함수의 피로수명 예측 모델을 도출한다.
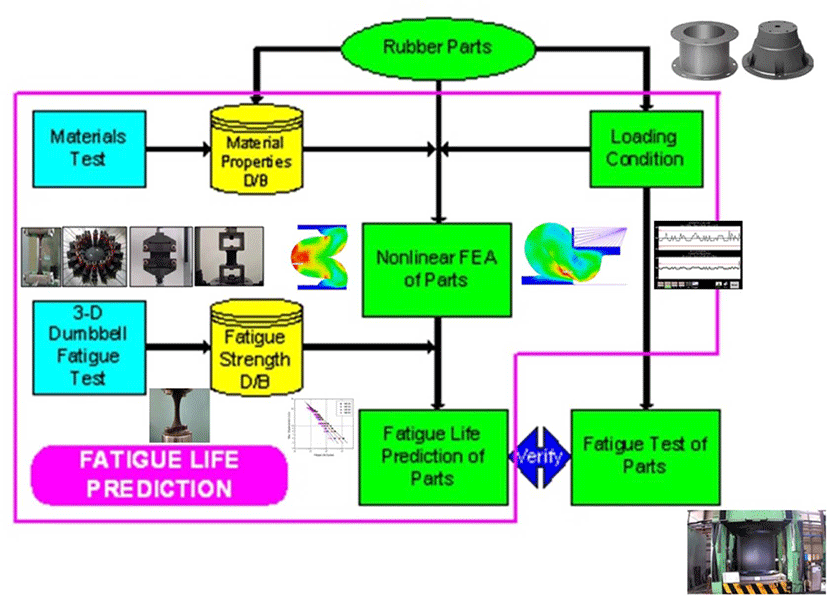
다음은 고무펜더 소재에 대한 수명예측 모델에 펜더 해석을 통해 구해진 최대 변형률을 적용하면 고무펜더의 사용수명을 예측할 수 있다. 이렇게 예측된 사용수명은 실제 고무펜더의 특성시험 및 피로시험을 통해 얻어진 수명과 비교하여 개발된 사용수명 예측방법의 타당성을 검증하게 된다.
Experimental
고무소재는 제조과정에서 배합성분 및 함량조건이 다양하고 재현성 확보가 어렵기 때문에 아직까지 표준화된 물성이 자리 잡지 못하고 있다. 대부분의 고무부품들은 반복하 중과 환경적인 노화4에 의해 피로손상 누적으로 수명을 다하게 되므로 고무소재의 물성을 정확하게 파악하기 위해서는 여러 가지 하중상태 및 환경조건에서 물성시험이 수행되어야 한다. 또한, 고무부품의 유한요소 해석에 필수적인 물성은 그 값의 변화에 따라 해석결과에 큰 차이를 나타내게 되어 해석의 수렴성 및 결과의 정확성에도 크게 영향을 미치게 되므로 고무부품의 보다 정확한 해석결과를 얻기 위해서는 제품과 동일한 성분 및 조건으로 제작된 시편에 대한 물성시험을 통한 물성 확보가 필수적이다 하겠다. 이러한 고무소재의 물성은 수치적으로 변형률 에너지함수(Strain energy function)의 계수 값으로 표현되는데 이 계수 값들은 여러 가지 다른 하중 상태에서의 물성시험을 통하여 구해진 응력과 변형률 데이터를 변형률 에너지함수로부터 유도된 응력-변형률 곡선으로 피팅하여 시험 값과 계산 값의 차이를 최소화함으로써 결정된다.5
고무소재의 물성을 구하기 위한 시험으로는 먼저 시험에 적절한 시편을 제작한 후 경도를 측정하여 시편간의 오차가 최소화 되도록 한 다음에 시험온도와 시험속도 등 시험조건을 설정하여 물성시험을 실시한 후 시험을 통해 얻어진 데이터를 분석하여 고무소재의 물성을 결정하였다. 고무소재의 물성을 보다 정확하게 결정하기 위해서는 단축인장, 단축압축, 순수전단 또는 단순전단, 등 이축인장시험 등 여러 가지 다른 하중 상태에서의 시험을 통하여 물성을 확보하는 것이 필요하나, 본 연구에서는 해양 고무 펜더에 사용되는 고무소재에 대해 Figure 3과 같이 단축 인장시편과 원형 형태의 등 이축 인장시편을 방사형으로 신장시켜 이축 응력과 이축 변형률을 측정할 수 있는 시험장치를 이용하여 상온에서 시험속도 300 mm/min로 변형률 25%, 50%, 75, 100%에서 5회 반복시험을 수행하였다. Figure 4에서와 같이 반복횟수와 변형률이 증가할수록 응력이 완화되는 뮬린스 효과(Mullins effect)와 히스테리시스(Hysteresis) 특성6이 나타났으며 시험을 통해 얻어진 응력과 변형률 데이터를 각 변형률에서 안정화된 마지막 응력-변형률 선도를 탄성이론을 통해 원점으로 이동시킨 결과를 Figure 5에 나타내었다.
단축 인장시험과 등 이축인장시험을 통해 얻어진 응력-변형률 데이터를 변형률 에너지함수로 구해진 응력-변형률의 관계식을 이용하여 Table 1과 같이 변형률 범위에 따른 무니-리블린(Mooney-Rivlin) 2항과 오그덴(Ogden) 3항의 비선형 재료상수를 결정하여 고무펜더 특성해석의 물성으로 활용하였다.7
고무소재의 피로수명을 평가하기 위하여 종래의 덤벨형 시편을 이용할 경우에는 시편 피로시험과 부품 피로시험 결과와의 상관성 유지가 어렵기 때문에 본 연구에서는 고무 펜더의 반복하중에 의한 최대 인장변형률을 재현할 수 있는 시편을 제작하여 피로시험을 수행하여 고무 펜더의 내구수명을 평가하는데 이용하였다. 피로시편의 형상은 Figure 6(a)에서와 같이 양단에 금속편을 가황하여 접착시킨 3차원 덤벨형으로 반복하중에 의한 이완이 발생되지 않고 인장과 압축변형이 가능하며 변형에 의한 변형률 분포가 비교적 완만하게 설계되었으며 최대 인장변형률 발생부위가 어떠한 변형에도 일정하게 발생되도록 중심부 형상은 타원형 단면으로 하였다. 피로시편에 발생하는 최대 변형률을 구하기 위해 유한요소 해석을 수행하였다. 3차원 모델로 유한요소 모형화 하였으며 고무물성은 변형률 범위에 따른 물성시험을 통해 구 해진 비선형 재료상수를 이용하였다. Figure 6(b)는 피로시편의 최대 변형률 발생 부위에서 변위와 변형률(Von Mises strain)과의 관계를 나타낸 것으로 고무소재의 피로수명을 예측하는데 활용하였다.
Results and Discussion
고무펜더의 사용수명을 예측하기 위해서는 펜더에 사용되는 소재의 피로수명선도가 있어야 하기 때문에 3차원 피로시편을 이용하여 진폭, 최대변위, 평균변위 등을 변화시키면서 다양한 시험조건에서 피로시험을 수행하여 Figure 7(a)에서와 같이 최대 인장변위와 피로수명과의 관계선도를 나타내면 진폭과 평균변위에 상관없이 인장변위가 클수록 피로수명은 감소함을 알 수 있었다. 따라서 최대 인장변위를 피로손상변수로 하면 시험조건에 상관없이 피로수명 선도를 잘 표현할 수 있었다.
3차원 덤벨형 시편에 대한 피로시험 결과를 이용하여 구해진 최대 인장변위와 피로수명과의 선도를 3차원 덤벨형 시편에 대한 유한요소 해석으로 구해진 최대 인장변위와 변형률과의 관계를 이용하여 Figure 7(b)와 같이 최대 변형률과 피로수명과의 관계선도로도 잘 표현할 수 있음을 알 수 있었다. 따라서 취약부위에서 발생되는 최대 변형률을 피로손상 변수로 하여 펜더용 고무소재에 대해 식 (1)과 같이 피로수명 예측식을 도출하였다.
여기서, εMax strain : Von-Mise strain
3차원 덤벨형 시편을 통해 펜더용 고무소재의 예측된 피로수명 예측식을 이용하여 펜더의 사용수명을 평가하기 위해 Figure 8과 같이 SSP-300H와 HSP-300H 타입의 고무 펜더에 대한 유한요소 해석을 수행하여 하중과 변형 특성을 파악하였다. 고무물성은 변형률 범위에 따른 물성시험을 통해 구 해진 비선형 재료상수를 이용하였으며 금속판의 물성으로 탄성계수 210 GPa, 포아슨 비는 0.3으로 하였다.
Figure 9에서와 같이 SSP-300H에 대한 하중과 변형 특성은 펜더 특성에 가장 중요한 25% 변형에서는 해석과 시험 결과가 거의 일치하였으며 전체적인 하중-변형 양상은 시험이 해석보다 약간 높은 경향을 나타내었으나 유한요소 해석을 통해 고무 펜더의 특성을 미리 파악할 수 있어 펜더 설계 및 제품개발에 유용하게 활용될 수 있으리라 기대된다.8
Figure 10은 고무펜더의 최대 변형률 발생하는 부위를 나타낸 것으로 SSP-300H은 펜더 중앙부의 바깥쪽에서, HSP-300H는 펜더 아래쪽 내면에서 발생하였으며, 최대 변형률 발생 부위에서의 변형률은 Figure 11에서와 같이 SSP-300H는 50% 변형에서 0.911의 Von-Mises 변형률이 발생하였으며, HSP-300H는 70% 변형에서 1.556으로 나타났다.
3차원 피로시편에 대한 피로시험을 통해 도출된 펜더의 피로수명 예측식인 식 (1)에 각 타입의 특성해석을 통해 파악된 최대 변형률 값을 적용하면 Figure 12에서와 같이 SSP-300H의 사용수명은 약 46,000회, HSP-300H는 약 11,357회로 예측되어 통상 고무 펜더의 사용수명인 3,650회(1회/일 × 10년) 보다 긴 수명을 나타내었다. 향 후 실제 고무펜더에 대한 피로시험을 수행하여 예측된 사용수명의 타당성을 검증할 예정 이다.
Conclusions
본 연구에서는 해양 고무 펜더에 적용되는 고무소재에 대해 특성해석에 필요한 비선형 재료상수 결정을 위한 시험을 통해 기본물성 및 해석물성을 확보하였으며 고무 펜더용 소재의 피로시편에 대한 반복 피로내구시험을 통해 설계 및 개발 초기단계에서 짧은 기간에 비교적 정확하게 고무 펜더의 사용수명을 예측할 수 있는 방법을 개발하여 다음과 같은 결론을 얻었다.
(1) 해양 고무펜더에 사용되는 고무소재에 대해 단축 인장시험과 등 이축인장시험을 통해 얻어진 응력-변형률 데이터를 이용하여 변형률 25%, 50%, 75%, 100%에 대한 무니-리블린(Mooney-Rivlin) 2항과 오그덴(Ogden) 3항의 비선형 재료상수를 도출하였다.
(2) 고무소재 비선형 재료상수를 이용하여 펜더의 하중-변형 특성해석은 25% 변형에서는 해석과 시험 결과가 거의 일치하여 해석을 통해 펜더의 특성을 미리 파악할 수 있어 펜더 설계 및 제품개발에 유용하게 활용될 수 있으리라 기대 된다.
(3) 3차원 덤벨형 시편에 대해 다양한 시험조건에서 피로시험을 수행하여 최대인장 변위를 피로손상 변수로 하는 피로수명 예측 식을 도출하였으며 최대인장 변위가 클수록 피로수명은 감소하였다.
(4) 고무 펜더의 취약부위에 발생되는 최대 변형률을 적용하여 SSP-300H 및 HSP-300H 펜더에 대한 사용수명으로 SSP-300H는 약 46,000회, HSP-300H는 약 11,357회로 예측되어 통상 고무 펜더의 사용수명인 3,650회 보다 긴 사용수명을 나타내었다.
(5) 본 연구를 통해 개발된 고무 펜더 사용수명 예측 방법을 활용하면 짧은 시간에 비 교적 정확하게 펜더에 대한 사용수명 예측이 가능하여 제품의 평가기준 및 품질 안정성 확보에 기여하리라 기대된다.