Introduction
고강도, 고강성 섬유로 알려진 아라미드(Aramid)직물과 UHMWPE(Ultra high-molecular weight polyethylene, 초고분자량 폴리에틸렌)직물 등은 높은 에너지 흡수 능력과 저중량, 유연성 등의 특성으로 인해 대표적인 방탄소재로 사용되고 있다. 최근 방탄소재는 우수한 방탄성능 뿐 만 아니라 기동성 및 착용성 등의 문제를 해결하기 위해 가볍고, 부피가 작으며 유연한 소재로의 개발이 요구되고 있다.1,2
방탄소재의 고속충돌에 의한 파단 메커니즘은 탄환의 운동에너지를 직물이 흡수 및 분산하면서 방호성능을 발휘하게 된다. 이 때 운동에너지는 서로 치밀하게 짜여진 섬유 조직체의 인장파괴, 압축, 응력전달, 층간분리, 층간전단 등의 형태로 흡수 및 분산된다.3-5 하지만 고속의 충격에 의한 탄환과 직물간의 상호작용은 직물을 구성하는 섬유의 특성, 구조, 적층수, 탄환의 형상, 충격 속도 등에 따라 직물의 파손 및 파괴가 매우 복잡하기 때문에 고속충격에 의한 변형 특성을 연구하기가 어려운 실정이다.6 지금까지 알려진 바와 같이 탄환의 질량과 속도가 운동에너지를 결정하며 이 운동에너지가 높을수록 충격에 의한 직물의 변형이 더 많이 발생한다. 수 십층으로 구성된 방탄소재는 탄환의 충격을 받으면 수직 및 수평방향으로 충격이 이동하면서 에너지를 분산하고 직물을 변형시킨다.7,8하지만 탄환의 속도가 일정한계를 넘어서면 탄환은 직물을 통과하게 된다. 따라서 방탄소재를 구성하고 있는 섬유 고유의 특성 이외에도 직물구조의 설계는 방탄성능 향상에 있어서 매우 중요한 요소이다. 아라미드나 UHMWPE와 같은 대표적인 방탄섬유는 평면방향으로는 강도 및 모듈러스가 매우 우수하지만, 그의 수직방향으로 가해지는 힘에는 매우 취약하다. 이러한 문제점을 해결하기 위해서 기존의 단순적층 형태의 복합직물에서 벗어나 직물의 층간 결합력을 높이기 위한 연구가 일부 진행되고 있으며, 복합직물 의 구성에서 적층순서, 층간의 마찰력, 층간접착 박리 등이 에너지 흡수에서 고려해야 할 요소이다.9-16
본 연구에서는 방탄 성능향상을 위해 복합직물 구성시 두께 방향 보강을 위한 다양한 방법을 제시하고자 하였다. 복합직물 구성을 위해 필름접착(Film bonding) 결합, 니들펀칭(Needle punching) 결합, 스티칭(Stitching) 결합 방법으로 복합 방탄직물을 제조하고 각 직물간의 충격 저항 및 흡수 특성에 대해 연구하였다.
Experimental
본 실험에서는 아라미드 직물과 UHMWPE 직물을 사용하여 복합 방탄직물을 제조하였다. 실험에 사용된 아라미드 직물은 파라(para) 아라미드 직물로 고강성 및 고강도 특성을 가지고 있다. 또한 UHMWPE 직물은 일반적으로 아라미드 섬유보다 가벼워 경량화 소재로 적합하며, 고강도 및 고탄성률을 지니고 있어 내충격성 또한 우수한 직물로 잘 알려져 있다. 복합 방탄직물 개발에 있어서 우수한 충격 저항성뿐만 아니라 경량화 또한 매우 중요한 요소 중의 하나로 면밀도 (Areal density)를 함께 고려해야 한다. 본 실험에 사용된 아라미드 직물은 면밀도 200 g/m2의 Dupont Kevlar이며, UHMWPE 직물은 면밀도 140 g/m2의 Dyneema이다.
본 실험에서는 결합방법에 따른 복합 방탄직물의 충격 저항 및 흡수 특성을 비교 분석하기 위해 필름접착, 니들펀칭, 스티칭 방법으로 시험편을 제조하였다.
필름접착 방법은 폴리우레탄 필름을 직물 사이에 삽입하여 프레스를 통해 압착하는 방식으로 이 때 아라미드 직물간의 접착은 135°C, UHMWPE 직물간의 접착은 115°C에서 실시하였으며, 프레스는 압력 40 ton으로 10 min간 실시하였다.
니들펀칭 방법은 각 직물과 아라미드 부직포를 함께 적층하여 결합하는 방식으로 적용하였다. 단일 하부 방향 니들펀칭 방식으로 아라미드 부직포가 상부에 위치하도록 하고 하부에 직물을 두어 아라미드 부직포 내의 단섬유가 니들 바브에 파지되어 직물로 이동하도록 하여 결합력을 높이고자 하였다. 부직포의 적층은 결합력의 향상뿐만 아니라 탄환의 충격이 가해졌을 때 충격을 흡수할 수 있는 완충재의 효과를 가져오기도 한다. 본 연구에서는 1.5de 아라미드 단섬유를 이용하여 제조한 니들펀칭 아라미드 부직포와 아라미드 직물 또는 UHMWPE 직물을 적층하고 m2당 10,000개의 니들로 구성되어 있는 장비를 이용하여 단위시간당 1000 strokes/min로 니들펀칭을 실시하였다. 이 때 결합력 향상을 위해 펀칭 횟수는 2회 실시하였으며, 니들펀칭 복합 방탄직물은 부직포의 완충효과를 위해 충격 실험시에는 부직포를 후면으로 배치하였다.
Codes | Combining method | Material |
---|---|---|
FA | Film bonding | Aramid |
FU | UHMWPE | |
NA | Needle punching | Aramid |
NU | UHMWPE | |
SA | Stitching | Aramid |
SU | UHMWPE |
스티칭에 의한 두께 방향의 보강은 공정이 용이하고 경제적인 방법으로 다양한 복합재의 제조에 적용이 되고 있는 방법이다. 스티칭에 의한 복합직물은 층간분리를 억제하고 충격에너지를 구조물에 고르게 분산시켜 줌으로써 내충격성을 향상시킨다. 또한 외부 충격시 스티칭에 의한 두께 방향의 보강섬유는 층간 분리에 보다 많은 에너지를 흡수하게 하여 손상영역의 확산을 제한하고 외부 충격 후 구조물의 잔여 강력을 크게 유지시켜준다. 스티칭시 고려해야 할 요건으로는 스티칭 형태, 실의 종류, 패턴, 밀도, 장력 등의 요소들이 있다.17 본 연구에서는 스티칭 패턴 및 밀도를 다르게 하여 구성하여 방탄성능에 미치는 영향에 대해 연구하고자 하였다. Sewing machine 을 사용하여 록(lock) 스티칭을 형성시켜 주는 방법으로 실시하였으며 스티칭은 케블라 실을 이용하여 1인치당 7스티칭이 되도록 하였다. 스티칭의 패턴 및 밀도에 대한 영향을 확인해보기 위해 아래의 Figure 2와 같이 총 7종의 스티칭 형태로 복합 방탄직물을 제조하였다.
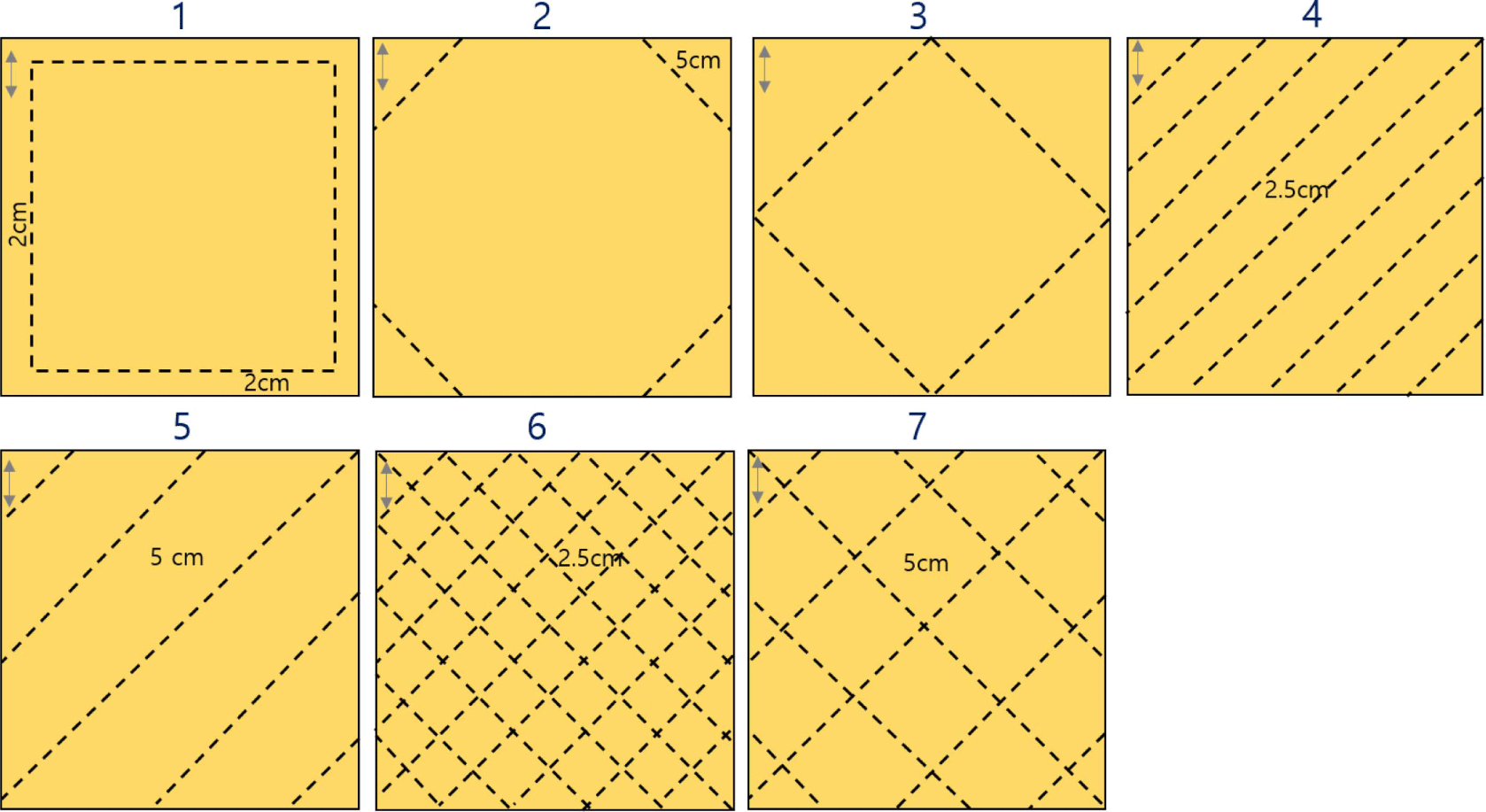
복합 방탄직물은 중량 및 두께 증가 대비 우수한 충격 저항성을 가지고 있어야 한다. 본 연구에서는 각각의 직물을 단순 적층했을 경우와 3가지 방법으로 결합했을 때의 중량 및 두께 변화를 측정하여 비교하였다. 직물의 변부는 시험편 제조시 원사가 일부 탈락되거나 프레스 작업시 불균일한 부분이 발생할 수 있기 때문에 변부를 제외하고 중심부에서 24×24 cm로 크기로 잘라 중량을 측정하였다. 또한 두께는 각 샘플마다 10부위를 측정하였으며, 니들펀칭 방식으로 결합된 시험편의 경우 부직포가 직물과는 달리 벌키하고 압력에 대한 저항성이 낮아 두께 측정의 오차가 클 수 있기 때문에 KES-FB3(Kawabata Evaluation System, Kato Tech, Japan)을 이용하여 초하중 0.5 gf/cm2 상태의 두께를 측정하였다.
전 세계적으로 방탄성능의 시험은 NIJ Standard 가 가장 많이 채택이 되며 국내에서는 해당 방탄시험이 허가된 기관이 한정적이다. 또한 방탄시험시 직물의 소요량이 상당하기 때문에 개발 중인 소재에 대한 방탄시험은 한계가 있다. 따라서 각 소재에 대한 상대적인 방탄성능을 평가하기 위해 KITECH에서 자체적으로 저속충격시험기를 제작하여 실험을 진행하였다. Figure 3과 Table 2는 본 연구에서 사용한 시험장비와 충격체의 형상과 규격을 나타내고 있다. 제작된 복합 방탄직물에 비교적 낮은 충격에너지를 가하기 위해서 충격체의 속도 및 질량을 가능한 최소화시켜야 한다. 본 연구에서는 실제 탄환과 유사한 형상의 발사체를 공압에 의해 순간적으로 발사하여 복합 방탄직물과 충돌 후, 직물 후면의 Backing material에 남긴 트라우마의 흔적을 측정하였다. 트라우마 깊이로 충격 흡수 정도를 판단하게 되며 이를 BFS(Backface Signature)라고 한다. BFS의 깊이가 낮을수록 방탄성능이 우수한 것으로 판단할 수 있다. 시험편은 발사체와 90도 방향에서 타격이 가해지도록 하였으며 충격시 시험편이 반발되며 충격을 분산 또는 흡수하지 않도록 양단 지지부를 밸크로 테이프로 고정시켰다. 테스트는 각 시험편마다 3회씩 실시하였으며 7 bar의 압력하에 진행되었다.
Equipment Specifications | Condition | |
---|---|---|
Projectile | Material | Tungsten |
Weight | 16.8 g | |
Diameter | 8.8 mm | |
Length | 21.95 mm | |
Distance from the muzzle of a gun to target | 115 mm | |
Pressure of projectile shot | 1~7 bar |
또한 복합 방탄직물의 충격 흡수 정도를 확인하기 위해 낙하충격 실험을 수행하였다. 본 연구에서 사용된 낙하충격시험 장치는 중량 낙하 방식으로 낙하충격체의 높이와 충격체 질량을 조절함으로써 다양한 충격에너지를 가할 수 있다. 마그네틱 홀더에 거치된 충격체를 자유낙하시켜 시험편에 충격을 가한 이후의 후면의 압력을 측정하는 방식으로 실험하였다. 본 연구에서는 복합 방탄직물에 직경 50 mm, 질량은 510 g의 구형의 발사체를 낙하높이 1500 mm로 낙하시켰으며, 이와 같은 조건을 통해서 7.5J의 충격에너지를 가할 수 있었다.
Results and Discussion
Figure 5는 결합에 따라 제조된 시험편의 중량과 두께를 측정하여 단순 적층시와 비교하여 증감을 나타낸 그래프이다. 비교 결과 3가지 결합방법 모두 중량은 증가하였으며, 아라미드 직물보다 UHMWPE 직물로 복합 방탄직물 제조시 중량 증가폭이 더 크게 확인되었다. UHMWPE 직물을 필름으로 접착한 경우 23%로 가장 큰 증가폭을 보인 반면 스티칭으로 결합한 경우 중량은 유의한 차이를 보이지 않았다. 두께는 필름으로 결합시 증가하였는데 고온에서 녹은 폴리우레탄 바인더가 직물 내부까지 침투하지 못하고 직물 표면에 바인더 층을 형성하며 두꺼워진 것으로 판단된다. 반면 니들펀칭의 경우 별도의 바인더 물질 없이 단섬유들이 물리적으로 결합되는 방식으로 부직포의 섬유가 니들 바브에 파지되어 직물쪽으로 이동되면서 벌키한 형태의 부직포가 압축되는 형태로 바뀌게 되어 단순적층시보다 두께가 큰 폭으로 감소한 것으로 볼 수 있다. 스티칭 방법은 결합 이후 두께에서도 유의한 차이를 보이지 않았다.
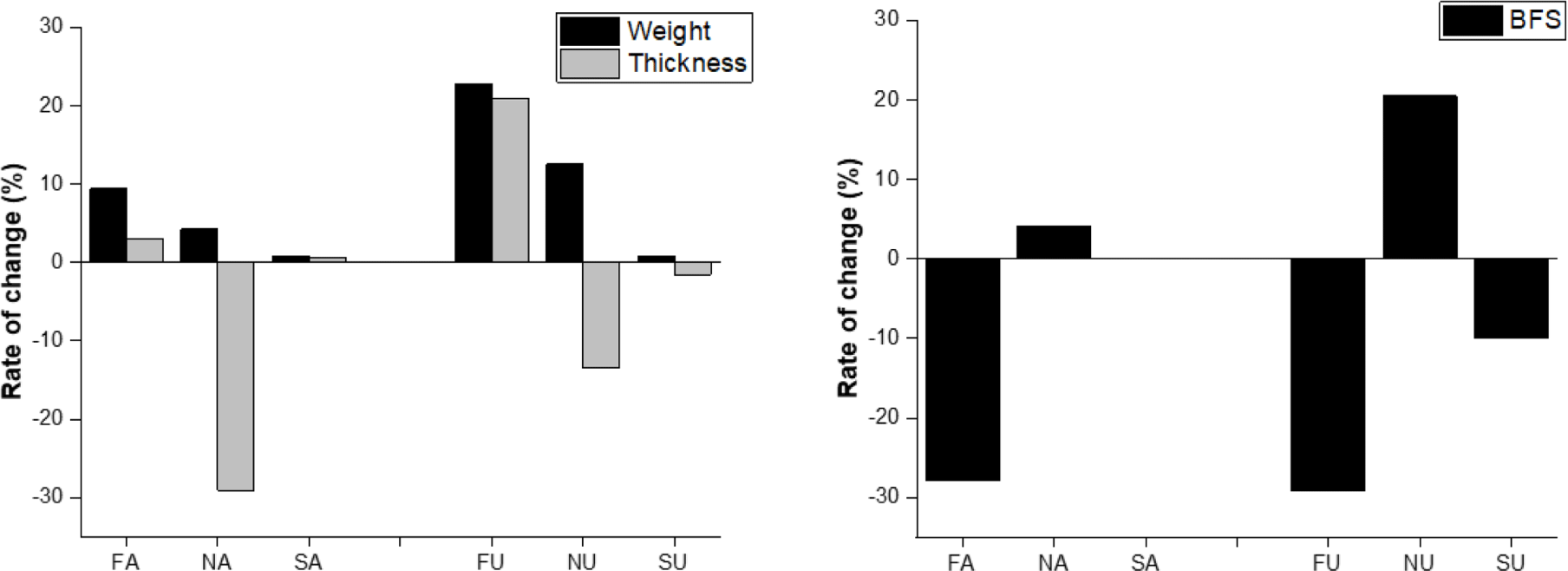
저속충격시험기를 이용하여 충격에 대한 저항성을 평가한 결과 필름으로 결합한 복합 방탄직물의 후면변형은 아라미드 직물 결합에서 27.9%, UHMWPE직물 결합에서 29.2% 감소하는 결과를 보였다. 폴리우레탄 필름으로 접착한 경우 바인더로 인해 직물이 뻣뻣해지며 저속충격에 대한 저항성이 커지는 것으로 볼 수 있으며 UHMWPE직물의 경우 직물표면의 바인더와 폴리우레탄 바인더가 결합하여 저항성이 더욱 커진 것으로 생각된다. 하지만 중량 및 두께가 최대 23%까지 증가하고 결합 이후 직물이 뻣뻣해지기 때문에 유연성을 필요로 하는 방탄소재로는 적합하지 않은 것으로 생각된다.
니들펀칭 방식으로 결합된 복합 방탄직물은 단순 적층시 보다 후면변형이 증가하였다. Figure 6은 각각의 방법으로 결합한 복합 방탄직물의 저속충격시험 이후 후면변형 형상으로 (a), (c)의 사진과 같이 후면변형 깊이가 낮고 폭이 넓은 것은 충격에 의한 파장이 충격지점으로부터 멀리 전달됨에 따른 결과이다. 반면 (b)에서는 후면의 부직포가 늘어나면서 탄환의 모양대로 밀고 들어간 형태를 확인할 수 있으며, 이는 충격이 넓은 면적으로 분산되지 못한 결과를 보여주고 있다. 이 결과는 단순 적층시 후면의 부직포가 일종의 완충재 역할을 함으로써 충격을 흡수하지만 니들펀칭으로 결합시 벌키한 부직포가 압축되어 완충의 효과를 가져오지 못함에 따른 것으로 판단된다. 또한 니들펀칭으로 결합력을 부여함과 동시에 니들에 의한 구성섬유의 파단이 일부 발생하여 충격 흡수 성능이 저하되는 것으로 볼 수 있다. 따라서 니들펀칭 결합방법에서는 펀칭 횟수나 니들의 형태에 따라 적절한 수준의 공정조건을 잡는 것이 중요하다고 할 수 있다.

스티칭 방법에서는 후면변형이 비슷하거나 10% 범위 내로만 증가하는 결과를 나타내어 중량 및 두께 증가대비 효과적인 결합방법으로 확인되었다. 따라서 두께 방향의 결합에서 스티칭 방법은 충격시 각 층간 분리에 많은 충격에너지를 분산하고 손상영역을 제한하며, 직물의 중량 및 두께, 유연성 등의 특성변화도 크지 않은 것으로 보아 방탄소재로의 적용가능성이 클 것으로 생각된다.
다음으로 중량 및 두께 증가대비 충격 저항 성능이 우수한 스티칭 방법에서 스티칭 패턴과 밀도 등의 영향을 확인하기 위한 실험을 실시하였다. Figure 7은 스티칭 패턴 및 밀도에 따른 중량 및 두께 변화량과 후면변형 변화량을 나타낸 그래프이다. 스티칭 밀도가 증가함에 따라 스티칭에 소요된 재봉실의 증가로 인해 중량이 증가하였다. 두께는 아라미드 복합 방탄직물의 경우 밀도가 비교적 높은 사선 스티칭(Stitching 4~5)와 다이아몬드 스티칭(Stitching 6~7)에서 두께가 대부분 큰 폭으로 감소하였다. 이는 적층되어 있던 직물들이 스치티로 인해 압축됨에 따른 것으로 볼 수 있다. 반면 UHMWPE 복합 방탄직물의 두께는 Stitching 1, 6을 제외하고 나머지는 모두 증가하였다. 이는 UHMWPE 직물이 뻣뻣해서 재봉시 각 층간에 공간이 형성됨에 따른 것으로 볼 수 있다.
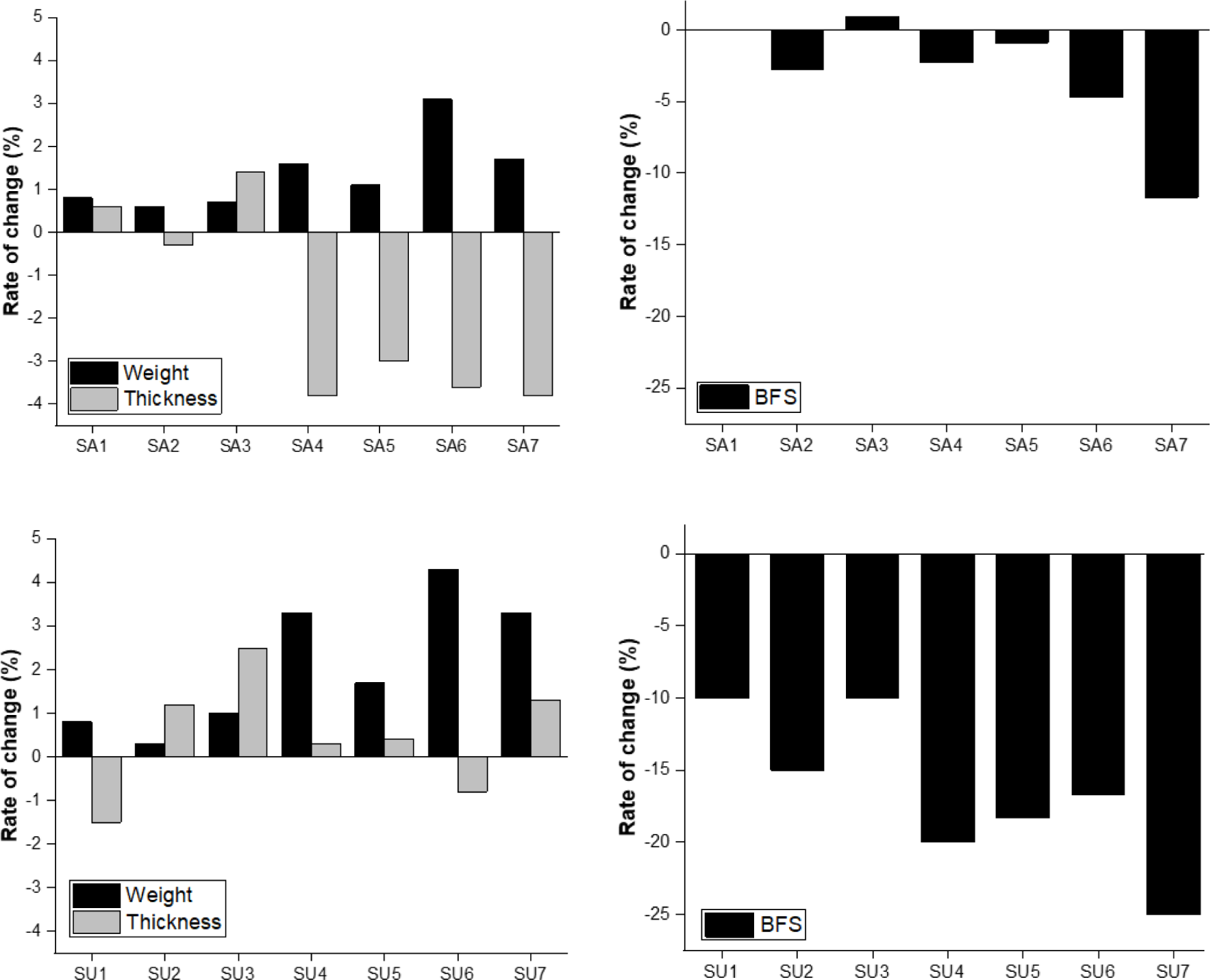
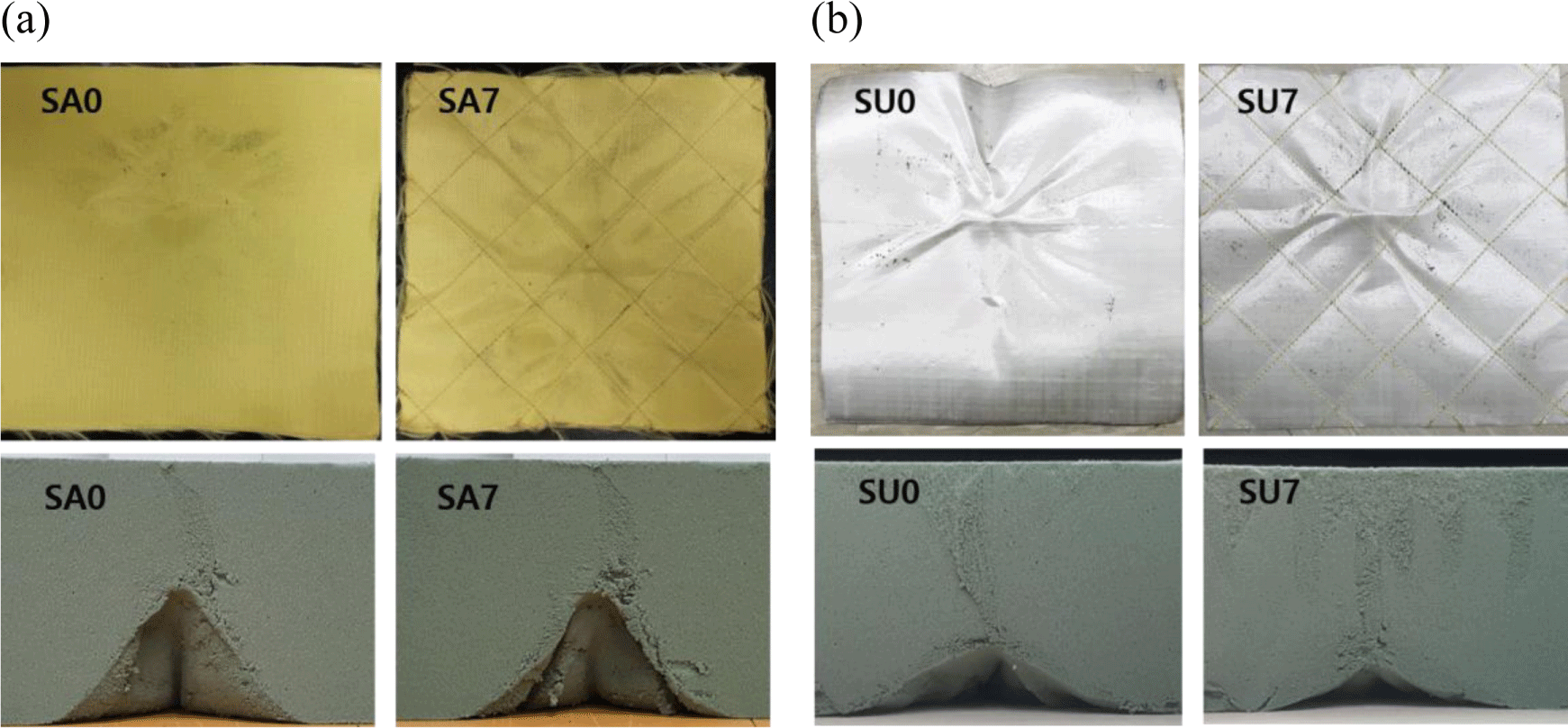
저속충격시험 결과 UHMWPE 복합 방탄직물의 후면변형 감소폭이 아라미드 복합 방탄직물에 비해 더욱 큰 결과를 나타내었다. 이는 직물 표면이 미끄러워 직물 층간의 slip이 상대적으로 많이 발생하는 UHMWPE 소재가 스티칭으로 결합됨으로써 충격시 층간 slip 및 층간분리를 억제함에 따라 충격에너지를 두께 방향으로도 효과적으로 전파함에 따른 결과인 것으로 판단된다. 사각 스티칭(Stitching 1~3)의 경우 각 모서리만 스티칭한 Stitching 2의 후면변형 감소가 컸으며, 사선 스티칭(Stitching 4~5)에서는 스티칭 밀도가 높아질수록 후면변형이 더 크게 감소하였다. 하지만 다이아몬드 스티칭 (Stitching 6~7)에서는 스티칭 밀도가 높아질수록 후면변형이 다시 증가하였다. 이는 과도한 스티칭 공정으로 인해 구성섬유의 손상이 증가하였기 때문으로 보여진다. 즉 조밀한 스티칭은 충격전파를 억제하여 충격을 고르게 분산하지 못할 뿐만 아니라 스티칭으로 인한 층간분리 억제 효과보다 섬유의 손상이 더 커지는 것으로 판단된다.
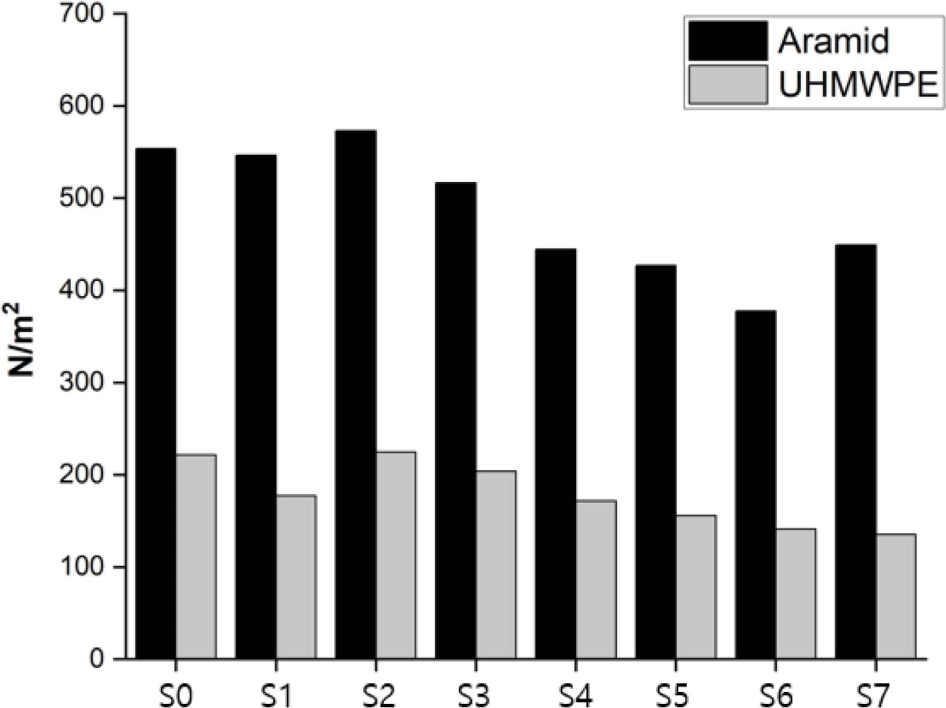
스티칭 패턴 및 밀도에 따른 충격 흡수 성능을 확인하기 위해 낙하충격시험을 실시하여 충격 이후의 후면의 에너지를 비교평가 하였다. 스티칭 밀도가 가장 높은 2.5 cm 다이아몬드 스티칭(S6)으로 결합된 복합 방탄직물이 가장 큰 에너지 흡수 능력을 나타내었다. 반면 모서리만 사각으로 스티칭한 시편의 경우(S2) 단순적층한 시편(S0)과 비교하였을 때 낙하 이후 에너지가 증가하였다. S2 시편의 경우 낙하충격 부분인 중앙부와 스티칭의 거리가 가장 멀고 스티칭 밀도가 가장 낮은 시편이며, S6은 가장 조밀한 스티칭으로 낙하충격 주위에 스티칭이 밀집해있다. 낙하하중 시험은 앞선 저속충격시험에 비해 충격체의 크기가 크고 충격 속도가 느리다. 따라서 충격이 직물의 fiber 방향과 층간 계면으로 천천히 전파되다가 스티칭 부분에서 스티칭 실에 의해 충격의 전달이 지연되거나 다른 층으로 쉽게 전파되기 때문에 더 큰 에너지를 흡수하고 있는 것으로 생각된다.
이와 같이 저속충격시험과 낙하충격시험의 결과를 비교해 보았을 때 충격체의 형상과 충격 속도에 따라 다른 결과를 확인 할 수 있었으며, 충격 조건에 따른 복합 방탄직물의 설계가 필요할 것으로 생각된다.
Conclusions
본 연구에서는 방탄 복합직물 구성시 두께 방향 보강을 위해 필름접착, 니들펀칭, 스티칭 방법으로 아라미드 및 UHMWPE 직물을 결합하고 저속충격시험 및 낙하충격시험을 실시하였다.
저속충격시험 결과 필름접착 방식으로 결합한 경우 충격에 대한 저항성이 가장 우수한 것으로 확인되었지만, 단순적층시 보다 증량의 증가가 크고 바인더로 인해 직물이 뻣뻣해지는 한계가 있었다. 니들펀칭 결합방식은 니들로 인해 섬유의 손상이 발생하여 오히려 후면변형이 증가하였으며, 스티칭 결합방식은 중량 및 두께는 유의한 차이를 보이지 않았으며 후면변형은 유사한 결과를 나타내었다.
스티칭 패턴과 밀도에 따른 성능을 확인한 결과 직물 표면이 매끄러운 UHMWPE 직물의 결합에서 직물 층간의 slip 및 분리를 효과적으로 억제함에 따라 후면변형이 큰 폭으로 감소하였다. 사각 스티칭 패턴에서는 각 모서리만 스티칭한 경우 후면변형이 가장 작았으며, 사선 스티칭 패턴에서는 스티칭 밀도가 높아질수록 후면변형이 감소하였다. 하지만 다이아몬드 스티칭 패턴에서는 스티칭 밀도가 높아질수록 후면변형이 다시 증가하였는데, 이는 과도한 스티칭으로 인해 층간분리 억제 효과보다 섬유의 손상이 더 커졌기 때문으로 생각된다.
또한 낙하충격시험에서는 스티칭 밀도가 가장 높은 2.5 cm의 다이아몬드 스티칭 결합이 가장 큰 충격에너지를 흡수하는 것으로 확인되었으며 각 직물의 특성 및 구성, 충격조건에 적합한 복합직물의 설계가 필요할 것으로 생각된다.