Introduction
The rising demand for polyurethane products, mainly in the automotive, construction, and packaging sectors, are expected to drive the market over the forecast period. Polyurethane (PU) products in the form of rigid and flexible foam are widely used for a variety of comfort applications such as furniture, bedding, cushioning, packaging, and thermal insulation materials or automotive parts.1 Due to large production and simultaneous consumption, a significant volume of polyurethane foams (PUFs) waste is landfilled. Therefore, recycling of PUFs to dispose of foam wastes is important from both environmental and economic points of view.2,3 Different physical processing methods, such as mechanical grinding, melt-processing, and compression molding, are successfully applied to thermoset PUF polymers.3,4 But, these processes are unsuitable for PUFs recycling due to their cross-linked structure; therefore, chemical recycling of PUFs has recently become an interesting research topic and an efficient, suitable way for waste treatments.
Chemical recycling methods such as glycolysis5-7 and acidolysis8-10 have been successfully developed at the industrial and pilot scale to degrade the polyurethane chain to recover low molecular weight polyols, whereas hydrolysis,11 alcoholysis,12,13 and aminolysis14 are still under investigation at the laboratory scale. A German engineering company, along with the Dutch recycling company is building a new reactor plant for the chemical recycling of discarded PU mattresses to achieve European sustainability goals. The obtained recovered polyol using acidolysis has 25-30% lower costs than the market price of the original polyether polyol. In academia, several researchers have investigated the glycolysis process to resolve the disposal problem of waste PUFs to recover high-quality polyols like virgin ones.5-7,15 In glycolysis, the polyurethane chain is subjected to chemical degradation via successive transesterification reactions of glycols with urethane or urea bonds in the presence of catalysts. The degradation products are small molecules or polyols containing alcoholic hydroxyl groups, which can be further used as raw materials for the fabrication of new flexible, rigid, or semi-rigid polyurethane foams.16,17 Wang et al. used dipropylene glycol to recycle polyurethane materials from car waste.12 Beneš et al. demonstrated the glycolysis of flexible PUFs scrap using diethylene glycol and dipropylene glycol. The recovered polyol was replaced with virgin polyol (maximum up to 36 wt.%) to prepare rigid polyurethane foams. The regenerated foam showed finer cell structure, good thermal conductivity, and compressive strength than virgin foam.18 The recycling of polyether polyol and toluene diisocyanate (TDI) based flexible PUFs using different catalysts and solvents were investigated. The combination of ethylene glycol and diethanolamine (DEA) mixture provided rapid degradation and the lowest kinematic viscosity products.19 Later, the recycling of flexible PUFs from dumped car seating was performed with diethylene glycol (DEG) and potassium acetate (KAc) at 220°C temperature. The optimum reaction and conversion were attained at 150% DEG and 1% KAc concentration to the mass of PU foam at 90 min reaction time.20 Molero et al. obtained an excellent quality of recycled polyol when DEA was used as a Lewis base catalyst following the ‘‘split-phase’’ glycolysis process.21 Meanwhile, Nikje and the research group prepared new foams using a mixture of recycled (up to 60 wt.%) and pure polyols. The recovered polyol was obtained via glycolysis of rigid foams under microwave irradiation. The foam density and reactivity of the regenerated PU foam increased with recycled polyol amount in the polyol blend.22 Kraitape and Thongpin investigated the incorporation of commercially recycled polyol from 0 to 10 wt.% with a petro-based polyol to prepare flexible PUFs. The resulting flexible PUFs showed enhancement in the compressive and tensile properties in reference to original flexible PUFs, ascribed to the higher crosslinking density and urea present in the recycled polyol.23 Although a majority of the earlier studies on the glycolysis of polyurethane foam use some common depolymerizing agents (short-chain polyols or glycols). The use of long-chain polyols i.e. high molecular weight glycols, for recycling PU foam waste was thought of as a new approach to advance in this glycolysis world.
Therefore, the main objective of this work is to recycle waste flexible polyurethane foam (WFPF) from recycled cars via glycolysis using different molecular weight glycols. The use of precursor polyol (used to make virgin PU foam) for the degradation of foam waste makes this investigation novel. The influence of different glycolysis agents on the viscosity, conversion, recovered polyols phase (one or split-phase), and quality of the recycled polyols are discussed. Besides, the effects of catalyst concentration, reaction temperature, and time on the recovered glycolysis products are determined. Furthermore, the purified recovered polyol (RPS) was used for the preparation of new flexible PU foams, and the physical and comfort properties of the regenerated foams were further measured. From an environmental and economic point of view, the suitability of this research will be helpful in promoting the industrial method of waste polyurethane recycling.
Experimental
Polyurethane flexible foam scrap was provided by KPX Chemical Co. Ltd., Korea. Industrial grade polyols; GPX-600 (Mw: 600 Da), GPX-3000 (Mw: 3000 Da), and GPX-6000 (Mw: 6000 Da) were supplied by KPX Chemical Co. Ltd., Korea. Potassium hydroxide (KOH, ≥85%, pellets) was purchased from Sigma-Aldrich, United States. Ethyl alcohol (99.9%) was procured from Samchun Pure Chemical. Co. Ltd., Korea.
For the production of recovered PU foams, conventional petro-based polyol (GPX-6000, main polyol, and POP-6040, copolymer polyol), isocyanate (KI-2000), cell opener (GEX-3300), surfactant (silicone-based, L-3002 and L-5309), blowing agent (distilled water), blowing catalyst (ETF), gelling catalyst (Dabco 33LV), chain-extender (1,4-butylene glycol), and crosslinking agent (diethanolamine) were provided by KPX Chemical Co. Ltd., Korea.
The degradation of WFPF was carried out in a round-bottom flask equipped with a stirrer and refluxing condenser under a nitrogen atmosphere. GPX-600, GPX-3000, and GPX-6000 (high molecular weight polyols) were used as glycolysis agents, and potassium hydroxide (KOH) as a catalyst. The foam waste was reacted with the glycolysis agent in a 1:1, 1:1.5, and 1:2 mass ratios (PU foam: Glycols). KOH (1, 2, 3, and 4 wt.% of PU foam) was used as the catalyst for the reaction. The typical recipe used for the recycling study is shown in Table 1. At first, the glycolysis agent placed in the flask was preheated to 195°C, and then a calculated amount of scrap foam was added by means of a continuous feeder. The temperature was maintained at 195°C during the feeding and reaction process. The zero time for the reaction was selected when the foam feeding was finished and complete dissolution takes place. Later, the reaction mixtures were stirred at 195°C for 2.0 hr to obtain the glycolysis products. After 2.0 hr, the depolymerization products consisting of a liquid glycolysis mixture were cooled down to ambient temperature, mixed with ethyl alcohol solvent, and the solid residue was removed by filtration. The liquid filtrate was evaporated under reduced pressure to obtain viscous recycled polyol. A schematic for the production of the recycled polyol is shown in Figure 1. The influence of glycolysis agents, catalyst concentration, time, and temperature in the system on the yield and quality of the recovered polyol were also determined.
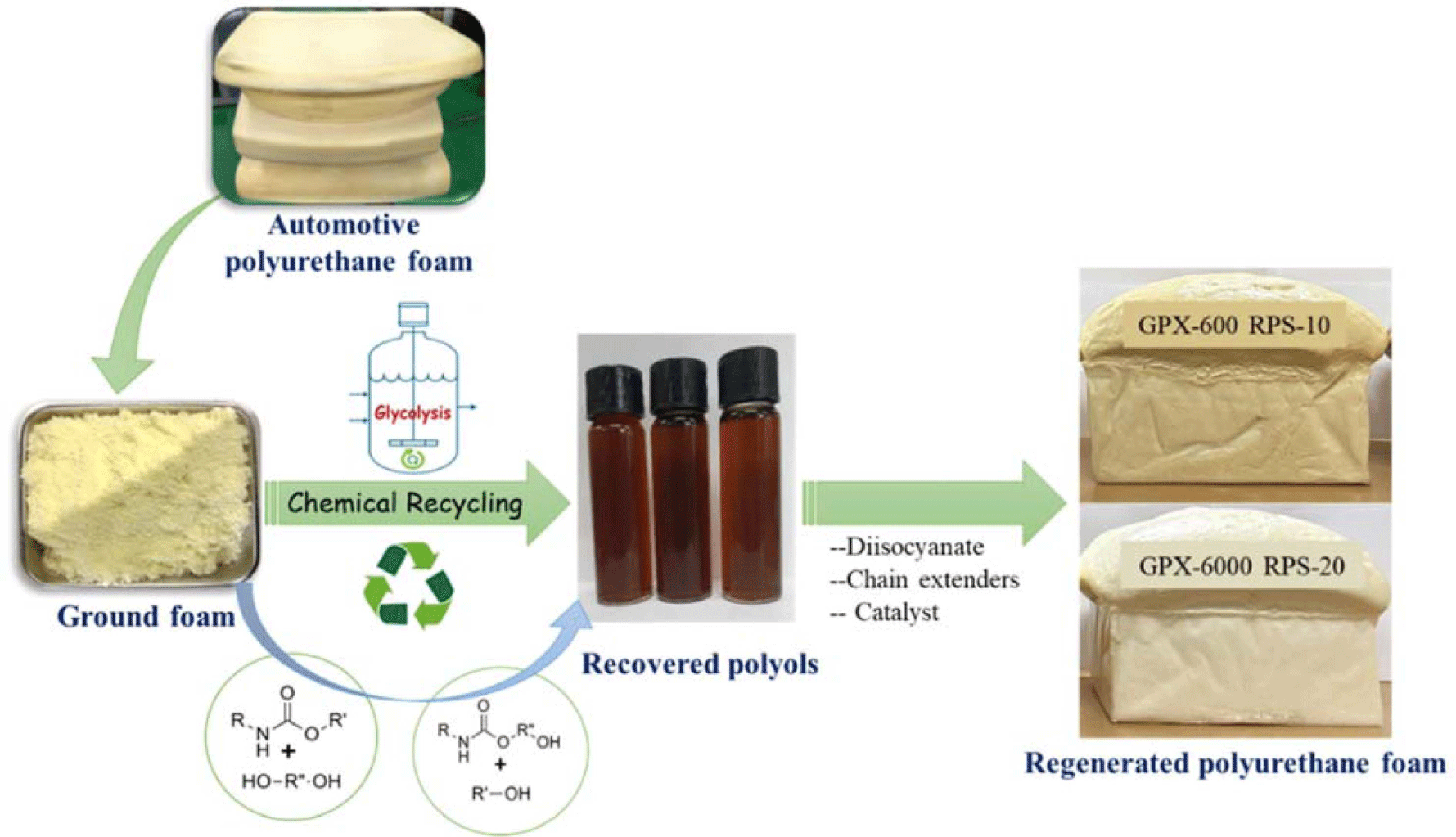
Flexible PUFs were prepared by a standard industrial procedure (Table 2) using variable amounts of purified recovered polyol, where 10 and 20 wt.% of virgin polyol were replaced by recycled polyol. First, a predetermined amount of virgin and recycled polyol was weighed and mixed in a 500 mL cup, to which catalysts, surfactant, and demineralized water were added. The mixture was homogenized with a mechanical stirrer for 15 sec at 1500 rpm. Then, an appropriate quantity of isocyanate was added to the polyol mixture, and the resulting solution was stirred for 5 sec at 3000 rpm. The mixture was quickly poured into a custom-made open plastic mold (250 × 250 × 100 mm3) and cured at ambient temperature. The test specimens of specific dimensions were cut for the physicomechanical property analysis.
The formation of glycolysis products was confirmed by Fourier Transform Infrared Spectroscopy (FT-IR) using a Thermoscientific NICOLET iS5 spectrometer. A total of 32 scans (resolution 4 cm-1) in the spectral range of 600 to 4000 cm-1 were used for all samples.
The viscosity of the recovered and virgin polyol was measured using a cone plate Brookfield Ametek DV3T viscometer at ambient temperature (25°C).
The morphology of the prepared PU foams was observed by a scanning electron microscope (Seron Technology, AIS 2300C) at an acceleration voltage of 20 kV. The foam samples were cut with a razor blade perpendicular to the foam rise direction and mounted on aluminum stubs with carbon tape, and then sputtered with gold coating before observation. The average cell diameter or pore size of the foams was obtained using ImageJ software from the cross-sectional surfaces.
The thermal degradation characteristics of the recovered PU foams were studied using a Q50 TA instruments thermogravimetric analyzer. The samples were heated from 30°C to 600°C at a heating rate of 20°C/min under N2 atmospheric conditions (50 ml/min).
The seating comfort properties of the virgin and regenerated PUFs were investigated through compressive behavior by analyzing compression force deflection (CFD) curves. The CFD test was performed using a Tensometer 2000, Myungjitech universal tensile tester with a crosshead speed of 50 mm/min at ambient temperature according to ASTM D3574. A circle flat indenter was pressed against the foam samples, and the dimensions of the samples were cut to 50 mm (l) × 50 mm (w) × 25 mm (h). The test is carried out by compressing the regenerated foams to 75% deformation and releasing the force to return to the initial state. After two successive cycles, the third data were used to compute the hardness, sag factor, and hysteresis loss of the foam material. The force value corresponding to 25% compression load represents the hardness of the foam. The sag factor or supporting property of foam material was determined from 65% and 25% load values, as obtained from CFD curves. Hysteresis loss is evaluated by calculating the amount of energy absorbed and released by the foam material during the compressive test. The equations for hysteresis loss and sag factor are given:
Where the x % CFD value denotes the force value at x % compression.
Results and Discussion
The degradation of polyurethane wastes was carried out with different industrial-grade molecular weights (from low to high) polyols. After the degradation experiment was complete, the reaction mixture was rapidly cooled, and sulfuric acid solution (9.5%) was added for neutralization purposes. To minimize the pyrolysis and avoid byproduct formation, glycolysis was carried out at 195°C. The recovered polyol was extracted with ethyl alcohol solvent, followed by vacuum filtration. The glycolysis of waste foam resulted in a single or two-phase mixture formation at the end of the reaction with respect to different glycolysis agents.
In order to investigate the influence of glycols in the system, KOH was selected as the catalyst due to its suitable catalytic activity. Initially, the degradation reactions of scrap PU foams were carried out by varying the amount of catalyst (KOH), and the mass ratio of glycolysis agent to PU foam added. At first, the low molecular weight glycol (GPX-600, Mw = 600 g/mol) was used as a glycolysis agent, and the optimized reaction condition was selected for the entire degradation study. The amount of PU foam waste was kept constant throughout the recycling study. The obtained products give two-phase immiscible liquid layers. Figure 2(a) and 2(b) show the conversion percentage with a varying catalyst amount and mass ratio of glycolysis agent to PU foam. It is observed that, regardless of the amount of GPX-600, the higher the content of the catalyst, the higher the conversion. However, the conversion is relatively higher when the GPX-600 weighs 7.5 g compared to other mass ratios. The catalyst concentration was kept lowest considering the moderate dissolution time affecting the strong enhancement of degradation and subsequent secondary reactions. Moreover, the effect of reaction time on the degradation of waste PU foams showed maximum conversion at 2 hr, and there is no significant change after that (Figure 2(c)).
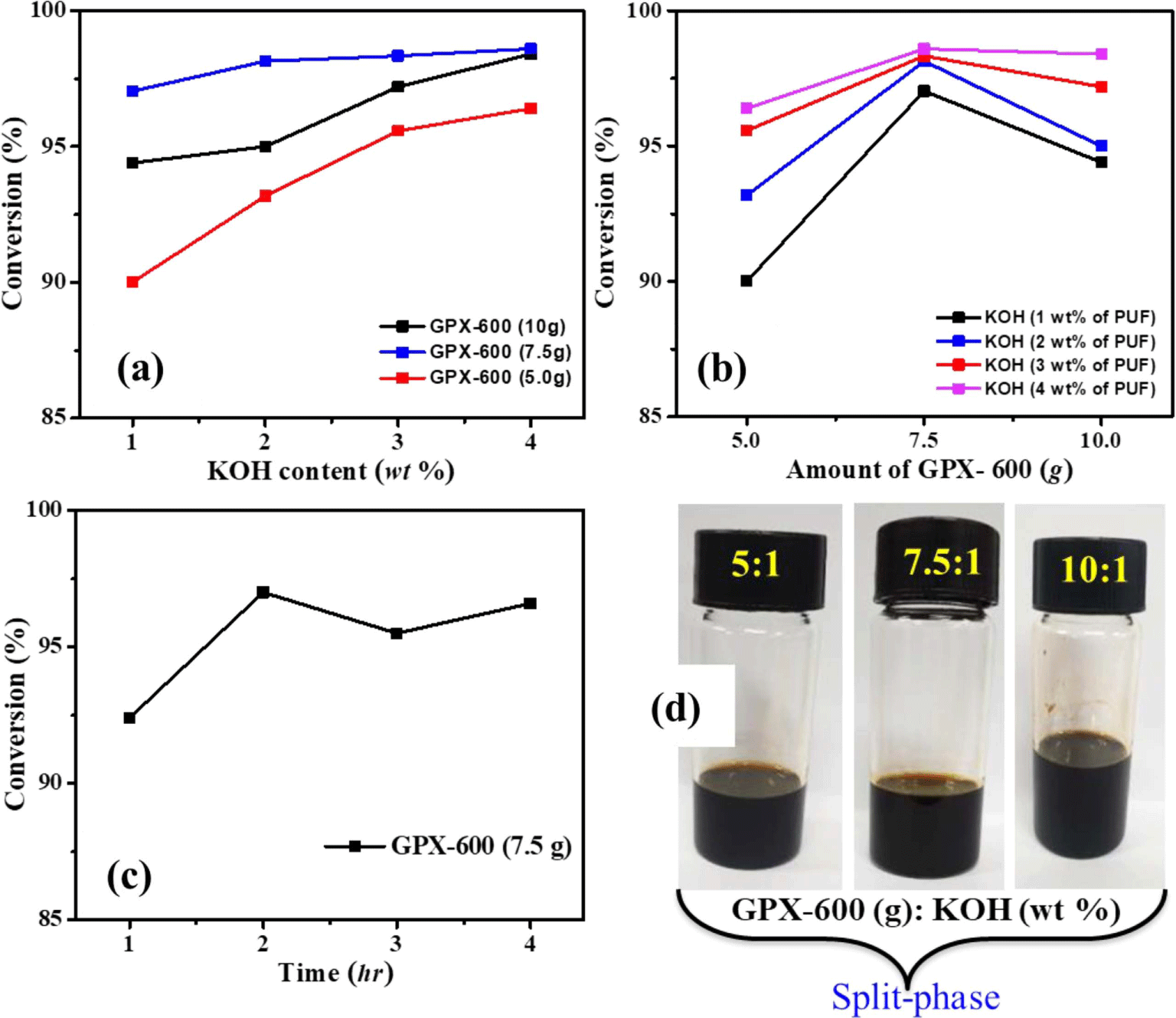
In this typical experimental investigation, high molecular weight glycols (GPX-3000, Mw: 3000 g/mol) and (GPX-6000, Mw: 6000 g/mol) were used as the depolymerizing agent with the aim of producing single-phase recovered polyols. Although the glycolysis product distribution between single and double phases was fairly similar for different glycols, the chemical properties and quality of the recovered polyol phase depend on the glycolysis agent. The variation in conversion with the content of glycols was investigated.
From Figure 3, it is evident that the conversion increases as the content of the depolymerizer increases. When the amount of GPX-6000 in the reaction mixture was increased to 50 and 100 g (i.e., PUF/Glycols weight ratios of 1:10 and 1:20, respectively), the extent of glycolysis of the hard segments also increases. Whereas, with increasing glycolysis temperature and time at a particular content of glycolysis agent i.e. using 50 g GPX-6000, there is no significant improvement in the extent of degradation. The recovered polyols are obtained as a homogenous one-phase product in every case. The formation of single-phase recovered products provides added advantages to eliminate the high cost of separation and purification from an economic and industrial point of view.
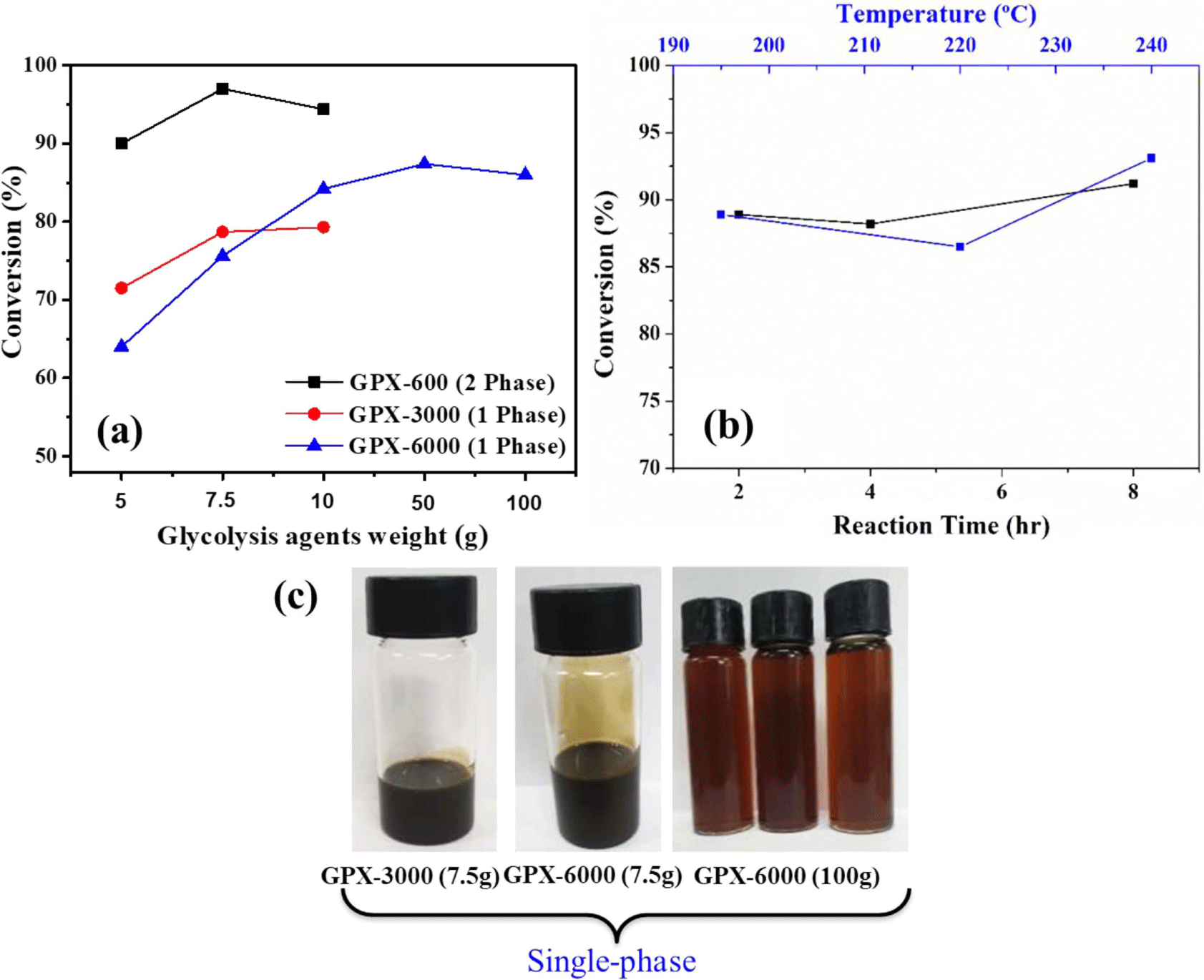
The viscosity is an important property of fluid for analyzing the flow behavior of the polyols and their suitability for polyurethane foam preparation. Figure 4 shows the effect of different glycolysis agents on the viscosity of the recovered polyols obtained under optimal conditions (195°C, 2 hr, and 1 wt.% of KOH). The viscosity of the virgin polyols was lower compared to the recovered polyols in every case. Worth noting is that the viscosity is observed maximum at a particular content of glycolysis agents i.e., 5 g in all the recovered polyols. With the increase in solvent concentration, a continuous decrease in viscosity was observed. This is thought to be due to the increased glycolysis conversion with the content of the depolymerizer. At higher concentrations of glycols, the residue content was low, which in turn affected the viscosity of the recovered polyols to lower values. The viscosity values of the recycled polyols obtained at different recycling conditions are shown in Table 3.
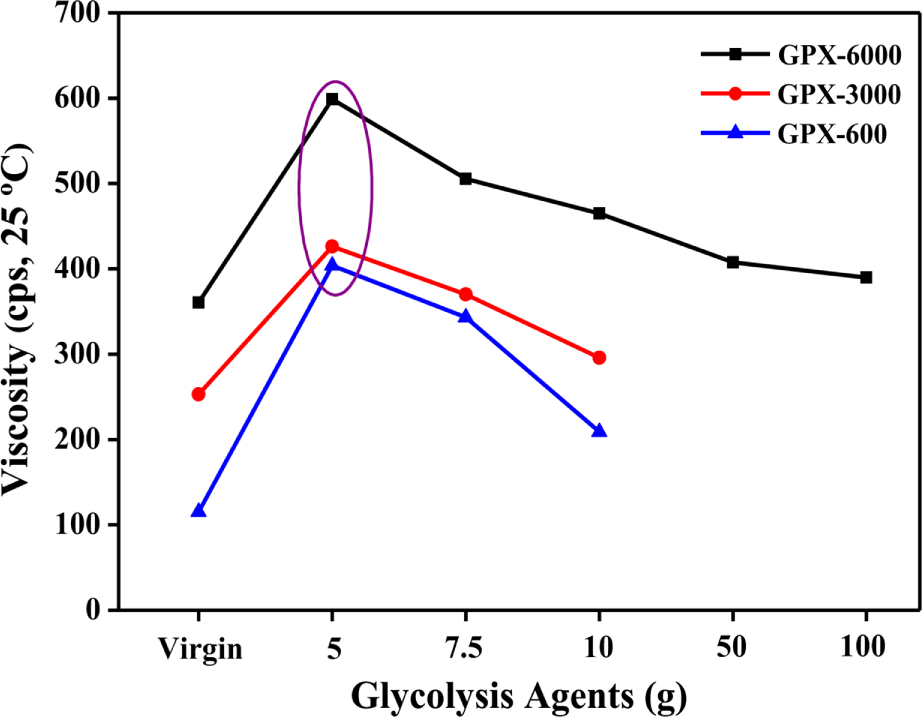
The ATR FTIR technique was used to investigate the functional groups of the virgin polyols and obtained recovered polyols to provide an update about the successful glycolysis of polyurethane. Figure 5 shows the normalized spectra of the recovered polyols obtained from foam waste at different reaction conditions. The recovered polyols prepared with the corresponding glycolysis agent’s weight percent are designated as RPS-5, RPS-7.5, RPS-10, and others. The spectra display a broad band around 3400 cm-1, typically arising from the -OH stretching vibration. The -CH stretching vibrations peak appears at 2970 and 2885 cm-1 respectively. After glycolysis, the appearance of characteristic absorption peaks at 1625 and 1515 cm-1 corresponds to the bending vibrations of the -NH group in the primary amines and amide bands, respectively. The absorption bands at 1454 and 1373 cm-1 appear for the bending vibrations of -CH2 moiety in the polyol chain. The increase in the intensity of the sharp band around 1085 cm-1 in the recovered polyols is due to the C-O stretching vibrations. Additionally, notice should be made that the -NH peak intensities at 1625 and 1515 cm-1 decrease in the recovered polyols with increasing GPX-6000 content as a glycolysis agent (Figure 5(c)). These amine byproducts and other impurities are undesirable and can adversely affect the polyurethane foaming process from the recovered polyol. Therefore, it can be concluded that under the action of glycolysis agents and catalysts, waste PU foams are successfully degraded into small molecular polyols with much structural similarity to virgin polyols and hence can be considered as a substituent for the preparation of recovered polyurethanes.
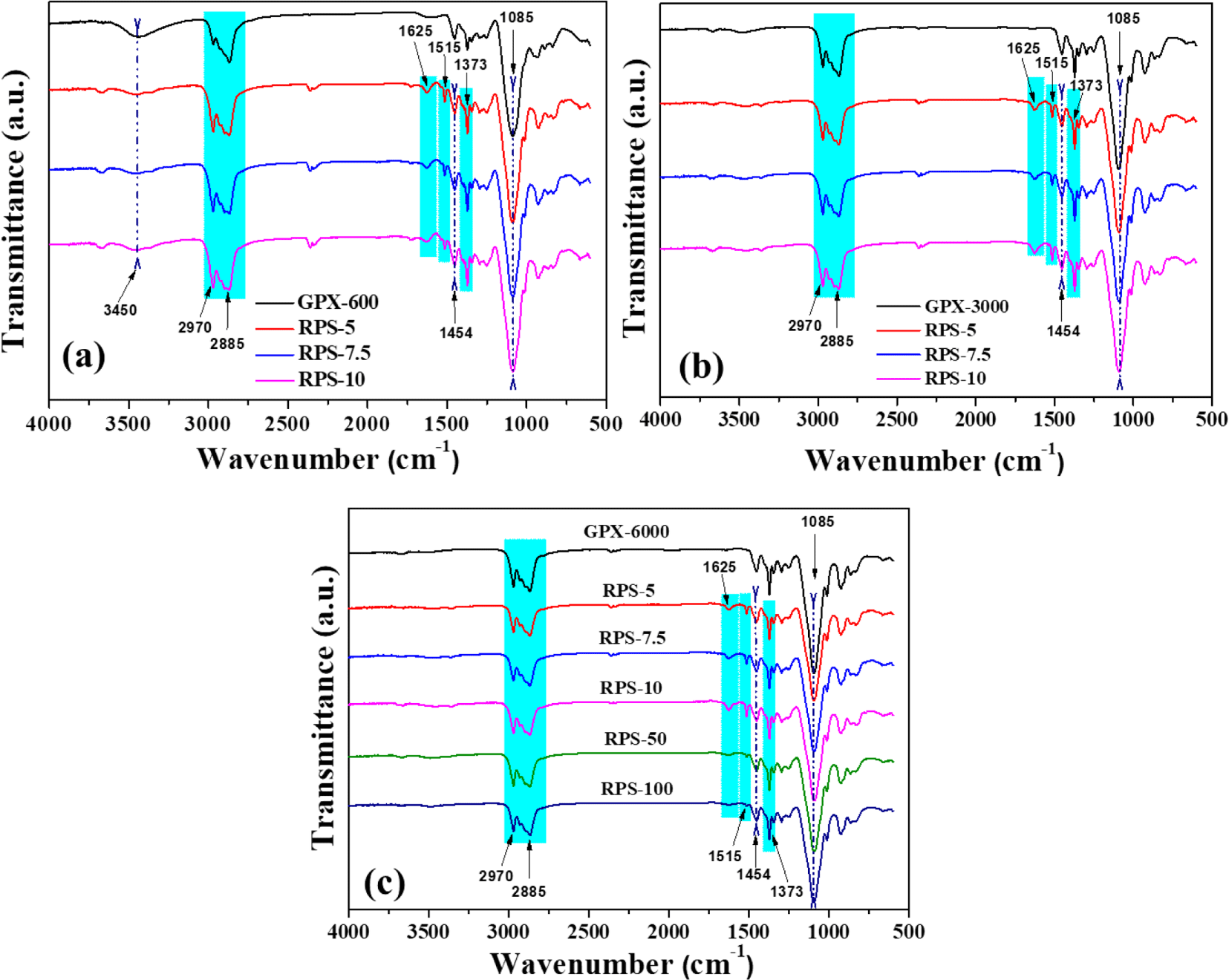
The recovered polyol was applied for the preparation of flexible foams, and the morphology and physicomechanical properties of the resulting foams were evaluated. It was visually observed that the regenerated foams became darker in color with increasing the bio-polyol amount. The images of the respective foams based on the recovered polyols are shown in Figure 6. The height of the resulting recovered foams was observed similar to that of reference foam, which suggests good reactivity and satisfactory foaming properties. In addition, the densities of recovered foams were found similar to that of virgin polyol foam.
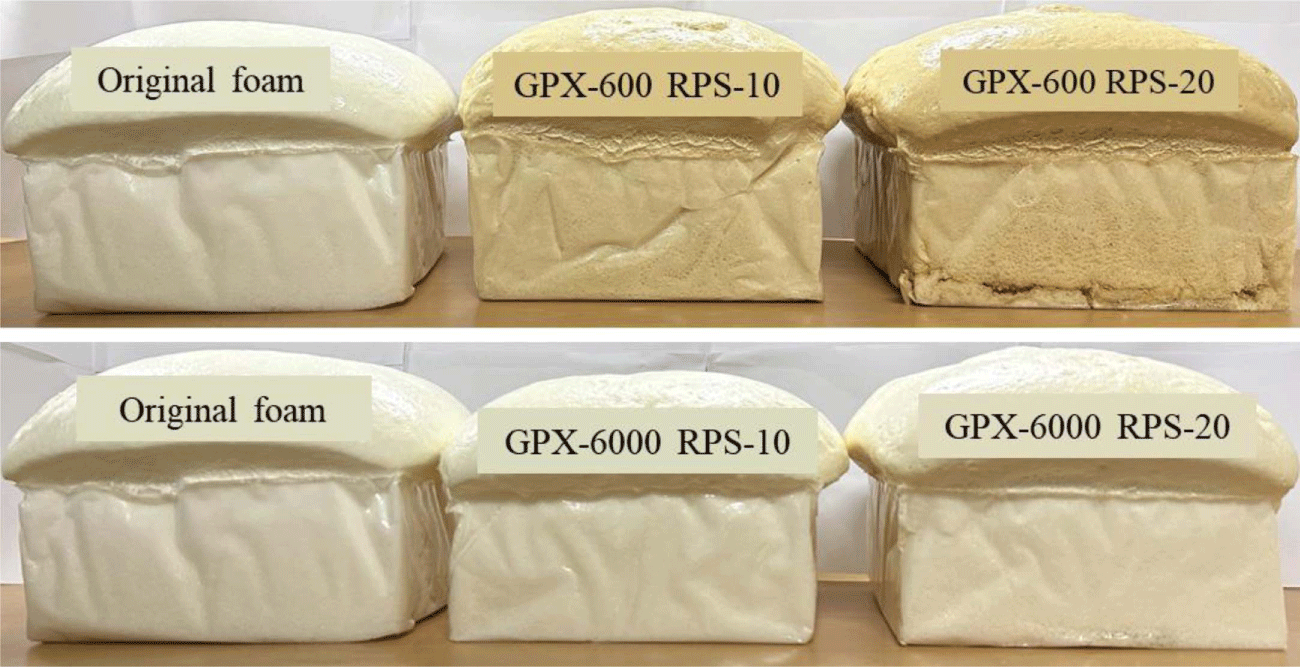
Figure 7 displays the SEM images of the different regenerated PU foam cross-sections with varying recovered polyol contents. The typical cellular structure is observed clearly in every case. The cell diameter is observed higher for GPX-600 RPS and 10% GPX-6000 RPS foam compared to the original foam, whereas the cell size is similar for higher recovered polyol content i.e. 20% GPX-6000 RPS. The original polyol foam shows an average cell size of 0.54 mm, whereas 10% GPX-600 and 20% GPX-600 recovered polyol foams present an average cell size of 0.63 mm and 0.73 mm, respectively.
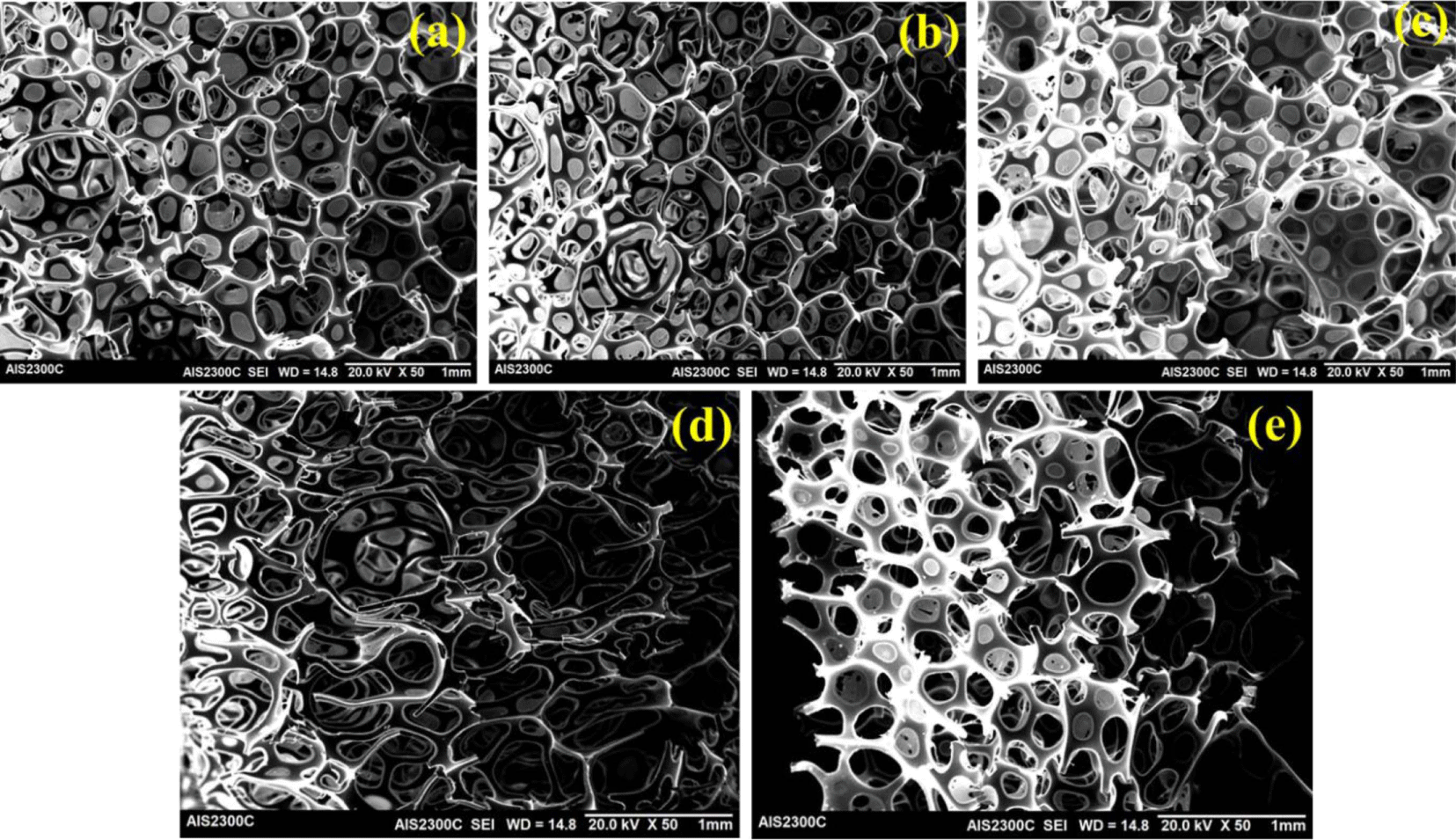
The average cell size was observed to decrease with 20% GPX-6000 recovered PU foam (0.51 mm), probably due to the higher viscosity and fast reactivity of the RPs restricting the bubble formation and coalescence during the foaming. In contrast, while using 10% GPX-6000 (average cell size of 0.92 mm) recovered polyol for PU foam, the phenomenon is the opposite. In fact, it is noticeable and well-reported that the higher viscosity of recycled polyol provides more heterogeneous and non-uniform cell morphology in PU foams.
Figure 8 shows the corresponding thermal degradation curves of the original foam and regenerated foams using recovered polyols. The thermal degradation of PUFs is characterized by the degradation of the hard segments followed by the degradation of the soft segments. It is clear from the figure that the decomposition of recovered foams followed a two-step degradation peak. The initial degradation starts around 250°C involving the dissociation of urethane bonds and biuret, followed by the decomposition of amines, polyether chains, and other components around 350°C in the later stages. Although there are no significant differences in the thermal stability, the results reveal that the recovered polyurethane foams are equally thermally stable compared to the virgin counterparts.
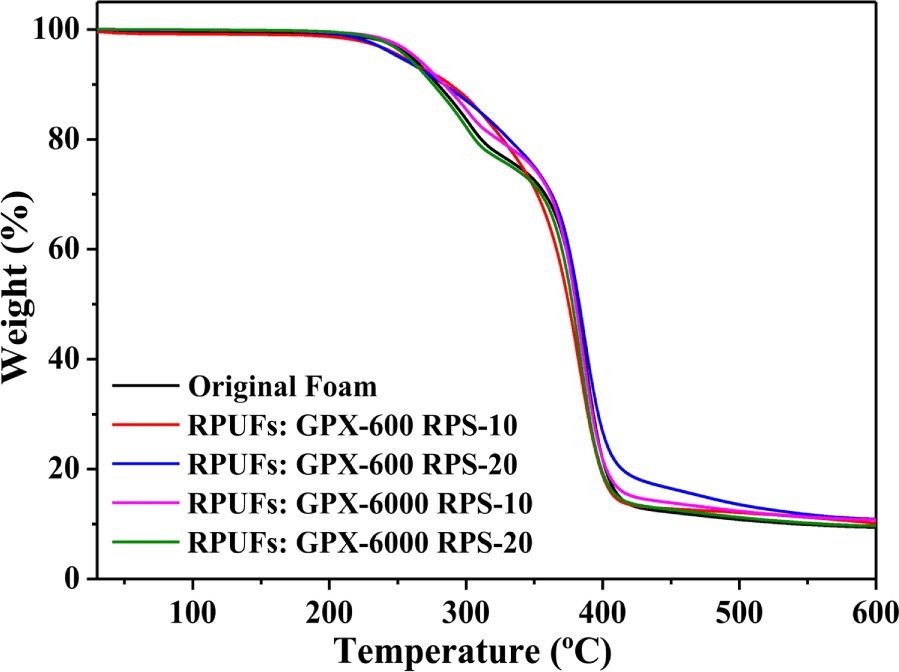
The most common test for evaluating seating comfort in the short term is the compression force deflection (CFD) method. The CFD test determines the load-bearing characteristics of a seat material (foam) at a given deflection.24 Several properties, such as the initial hardness factor (IHF), and sag or support factor (SF), were obtained from the CFD curve to explain the short-term seating comfort in a static state. Also, hysteresis loss with reference to the resilience properties of seat cushions is an important factor in assessing comfort qualities was measured.
Figure 9(a)-(c) shows the hardness, sag factor, and hysteresis loss (%) behavior of the regenerated polyurethane foams. 25% CFD value (obtained from the corresponding CFD plot) represents the hardness of the material. From Figure 9(a), it can be observed that recovered foams using GPX-6000 RPS exhibited lower hardness than the original foam, whereas foams prepared using GPX-600 RPS showed increased hardness compared to the original foam. This is in agreement with the overall glycolysis conversion using both GPX-600 and GPX-6000, which in turn results in the higher amine content affecting the hardness properties. Also, the use of base polyol i.e. GPX-6000 for original foam and recovered foam (using GPX-6000 RPS) preparation maintains good compatibility, resulting in similar hardness values.
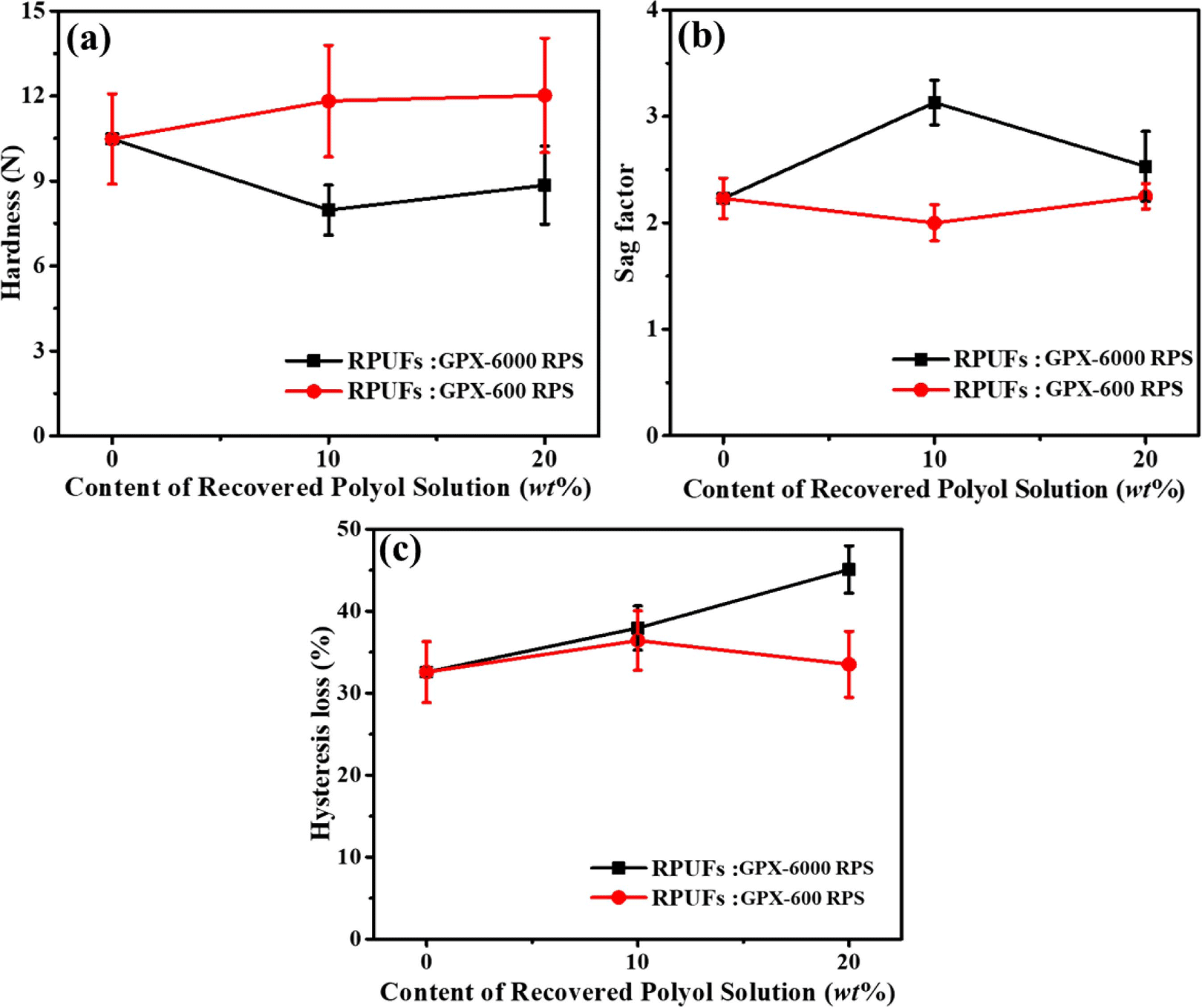
The Sag Factor (SF) of a foam material defines the supporting property or ability to support the load. The SF values of original and recovered foams are compared and presented in Figure 9(b). The recovered foam using GPX-6000 RPS exhibited improved SF values compared to the original foam, indicating a good supporting property. The decrease in hardness of the GPX-6000 RPS foam had an influence on the increased supporting comfort, i.e. high SF values. The SF values of original and regenerated foams using GPX-600 RPS were obtained as similar. A sag factor value of higher than 2.8 is required for good comfort, as reported in earlier reported work.25
In addition, hysteresis loss relates to the resiliency of foam and mainly contributes to the comfort property of PU foam products. The average hysteresis loss was observed in the range of 32 to 42%. From the hysteresis loss curves (Figure 9(c)), the resilience property of GPX-6000 RPS regenerated foam decreases. The hysteresis loss values showed comparable resilience behavior for the original and regenerated foams using GPX-600 RPS.
Conclusions
In summary, the recycling of post-consumer automotive polyurethane foam waste via glycolysis using different industrial-grade polyols was demonstrated in this study. The degradation study of the waste flexible polyurethane foams using virgin polymeric polyol (used to prepare original PU foam) has been accomplished for the first time. The effects of glycolysis agents, catalyst concentration, and reaction times on the recovered polyol properties were investigated. It has been observed that, regardless of the content of glycolytic agents, the higher the content of the catalyst, the higher the conversion. The catalyst concentration at 1.0 wt.% was found to be the best glycolysis condition. Interestingly, with the increase in the molecular weight of glycolysis agents (Mw: 600 to 6000 g/mol) the recycling process resulted in split-phase to single-phase recovered polyol products. The FTIR spectra of recovered polyols were similar to the original polyols. Compared to virgin polyols, the recovered polyol shows higher viscosity due to the presence of higher molecular weight moieties and secondary byproducts. Furthermore, after proper treatment of recovered polyol, flexible polyurethane foams were prepared by mixing conventional virgin and recovered polyol on a laboratory fume hood. The regenerated polyurethane foams (RPUFs) derived from recovered polyol (replacing up to 20% virgin polyol) showed good thermal degradation properties and cellular size morphology. The presence of amine byproducts in the recovered polyol slightly affects the foaming properties of the RPUFs to that of reference foam. The short-term seating comfort properties of RPUFs by compression force deflection (CFD) test showed comparable hardness, hysteresis loss, and supporting property i.e. sag factor, compared to virgin foam. In this sense, the glycolysis of waste foams to produce polyols exemplifies the suitability of this recycling method, and the effective use of these recovered polyols to regenerate foam materials can be achieved further.