Introduction
Asphalt is commonly known as the residue left over from the oil-refining process.1 However, it is one of the most widely used building materials worldwide owing to its useful properties, including high flexibility, adhesiveness, and waterproofness, making it ideal for road paving, rooftops, and waterproofing sheets.2-4 The annual global consumption of asphalt is estimated to exceed 100 million tons.5 However, asphalt loses its physical properties, such as adhesiveness and flexibility, outside a certain temperature range, so it cannot always be used alone. To use asphalt as a building material, this temperature range needs to be expanded,6 where elastomer materials such as styrene-butadiene-styrene (SBS) copolymers and natural rubber (NR) can be used as modifiers to improve asphalt’s physical properties such that it can maintain its adhesion and flexibility.7,8 However, SBS copolymers and NR exhibit various drawbacks when used as asphalt modifiers. The SBS copolymer is an elastomer synthesized from petroleum, so the market supply is unstable owing to the decrease in global crude oil reserves.9 In addition, when added as an asphalt modifier, SBS copolymer must be processed at temperatures of 180°C10 or higher, which is energy consuming and raises safety issues. NR is treated as a latex, in which polymer particles are dispersed in water, and when added as an asphalt modifier, the moisture within the latex evaporates rapidly in high-temperature asphalt, significantly reducing processing safety. Compared with SBS copolymer, the non-uniform molecular weight and the low modifiability of NR may reduce the quality of the asphalt products. Therefore, SBS copolymer, which is free from the risk of moisture evaporation, is most commonly used, but it is added at a temperature higher than the asphalt processing temperature and requires a long time to disperse owing to its solid form. Research is currently being conducted on the use of liquid rubber as an asphalt modifier. Liquid rubber imparts fluidity and flexibility to asphalt,11 can be easily mixed at low temperatures compared with existing rubber modifiers, and does not require high processing temperatures during the addition process, which can reduce energy consumption. Liquid rubber also improves the physical properties of asphalt owing to its uniform dispersion. These characteristics increase the productivity and safety of road pavement and building materials. To address the problems surrounding existing rubber modifiers, we synthesized epoxidized natural rubber (ENR) through an epoxy reaction, using hydrogen peroxide and formic acid from NR that is unaffected by the oil market. ENR possesses high polarity due to epoxy groups, providing exceptional air impermeability, resistance to oils and organic solvents, superior wet road grip performance, and excellent tensile and fatigue properties.41 Furthermore, liquid epoxidized natural rubber (LENR) with high fluidity was synthesized through a depolymerization reaction involving the partial ring-opening of epoxy groups using sodium nitrite. We designed LENR through synthesis, combining the advantages of epoxy functionality and liquid characteristics. The LENR could be applied at temperatures lower than 170-200°C, the range in which existing rubber modifiers are added. We synthesized a rubber modifier that improves the physical properties of asphalt and used it to manufacture asphalt sheets. We also measured the physical properties—including the tensile, adhesion, and wet adhesion strengths—of these asphalt sheets to confirm the trend.
Experimental
The 60 wt% NR latex used in this study was purchased from Jungwoo Trading (Busan, Republic of Korea). The 60 wt% NR latex used in this study consists of 60 wt% natural rubber, 0.6 wt% ammonia, and 39.4 wt% water. NR latex (20 wt%) was prepared by mixing 330 g of 60 wt% NR latex and 670 g of distilled water. Hydrogen peroxide (34.5 wt%) and formic acid (85 wt%) were purchased from Samchun Chemicals (Seoul, Republic of Korea) and used as received. To prepare a 33 wt% aqueous sodium nitrite solution, 33.5 g of sodium nitrite (98.5 wt%, Samchun Chemicals (Seoul, Republic of Korea)) was dissolved in 76.5 g of distilled water. Sodium dodecyl sulfate, used as a coagulant stabilizer for NR latex, was purchased from Daejung Chemicals (Siheung, Republic of Korea) and dissolved in 90 g of distilled water and 10 g of sodium dodecyl sulfate to prepare a 10 wt% solution. The asphalt used in the production of the sheets was provided by RAVI Co., Ltd. (Eumseong, Republic of Korea), and used as received. The asphalt sheet fluid is composed of 65-70% asphalt, 13-20% calcium carbonate, and 3-10% poly(ethylene terephthalate). The concrete used to produce the blocks for measuring the adhesion and wet adhesion strengths was purchased from DO Paint Co., Ltd (Daejeon, Republic of Korea).
In a 2000 mL round-bottomed flask, 330 g of 60 wt% NR latex was added to 670 g of distilled water to prepare 1000 g of 20 wt% NR latex. Afterwards, 100 g of 10 wt% sodium lauryl sulfate (SLS) was added. The two solutions were stirred sufficiently at room temperature, and the flask was immersed in an oil bath at 70°C. When the solution reached 70°C, hydrogen peroxide (34.5 wt%) and formic acid (85 wt%) were added using a dropper, and the epoxidation reaction was carried out at 70°C for 12 h while stirring. After the reaction was complete, an aqueous solution of sodium nitrite (33 wt%) was added using a dropper. The reduction reaction was carried out at 70°C for 12 h, and then 4000 mL of methanol was added to precipitate the products. The solids were washed thrice with 4000 mL of distilled water. The obtained products were dried in a vacuum oven for 24 h to obtain the final products (Figure 1). At 25°C, the synthesized LENR-1-5 were dark brown, sticky liquids. The ENRs in this study were synthesized using varying amounts of hydrogen peroxide and formic acid, as shown in Table 1, and are denoted as LENR-1-5, respectively, according to the amounts of hydrogen peroxide and formic acid added during the synthesis.
Asphalt sheets modified by LENR-1-5 (AS_LENR-1-5) were fabricated, and the changes in the properties of the asphalt sheets upon modification, including their tensile, adhesion, and wet adhesion strengths, were measured. The asphalt sheets shown in Figure 2 were fabricated by adding LENR-1-5 at different weight ratios (5, 10, 15, and 20 wt%) to asphalt heated to 160°C. Specimens AS_LENR-1-5 were injected into a silicone mold with a width of 150 mm, length of 250 mm, and thickness of 3 mm. The specimens were covered with release paper, cooled at room temperature for over 24 h, and then separated from the mold for use. Here, the addition ratio of LENR refers to the weight ratio of LENR to the asphalt sheet standard (100 wt%), which were manufactured at 5, 10, 15, and 20 wt%. The sheet was produced so as to prevent the formation of bubbles, which made accurate measurement of the tensile, adhesion, and wet adhesion strengths difficult. Subsequently, the asphalt sheet was processed, and its tensile, adhesion, and wet adhesion strengths were measured according to specifications.
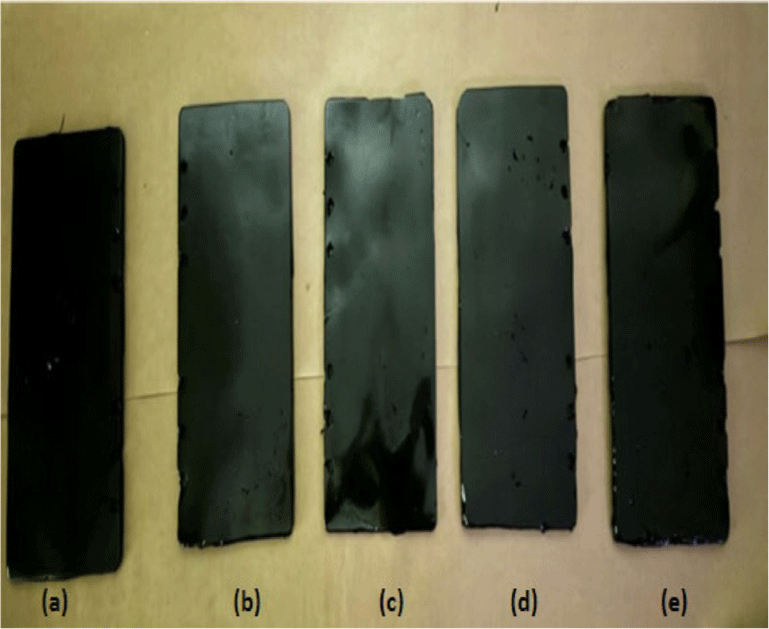
Fourier-transform infrared (FT-IR) spectroscopy was used to determine the molecular structure of the synthesized LENR-1-5. The specimens were analyzed using a NICOLET 380 FT-IR spectrometer (Thermo Fisher Scientific, USA) in the wavenumber range of 400-4000 cm-1. To quantitatively analyze the epoxy group contents of LENR-1-5, proton nuclear magnetic resonance (1H NMR) spectroscopy was used. The 1H NMR spectra were measured in ppm using CDCl3 as the solvent (MR400 DD2 spectrometer, Agilent, USA). Differential scanning calorimetry (DSC) was used to measure the glass transition temperature (Tg), which indicates the degree of fluidity of the synthesized LENR-1-5 with respect to temperature. The Tg values of LENR-1-5 were measured using a Q-10 differential scanning calorimeter (TA Instruments Inc., USA). Gel-permeation chromatography (GPC) was performed to confirm the molecular weights of LENR-1-5 synthesized with varying amounts of hydrogen peroxide and formic acid. The molecular weights of LENR-1-5 were measured using a Waters 2695 Alliance HPLC system. The viscosities of the LENR specimens were measured at 70°C for 10 s using an L4 spindle at 100 rpm (Viscolead One L, FUNGILAB, Spain). To measure the tensile strength, specimens were prepared by mixing LENR-1-5 based on the weight ratio of the asphalt sheet liquid at 5, 10, 15 and 20 wt%; pouring it into a 3 mm thick mold; and cooling it at room temperature for 24 h. The mold was used to prepare a dumbbell-shaped tensile strength test piece from an asphalt sheet. The tensile strength corresponded to the breaking of the test piece at a speed of 100 cm/min using a universal material testing machine (STM Co., Republic of Korea). Asphalt sheets are mainly used for rooftops and walls; therefore, to evaluate the adhesion performance and stability of the concrete towards moisture (such as rain), concrete cubes were prepared, asphalt sheets were attached, and the adhesion and wet adhesion strengths were measured using a universal material testing machine. To measure the adhesion strength, concrete cubes measuring 75 mm in width and 15 mm in height were made (Figure 3), and AS_LENR-1-5 were cut to have a width of 80 mm and height of 18 mm. The two sides of the specimens were attached and heated in an oven at 120°C for 30 min. Sufficient adhesion to the concrete blocks was ensured. After cooling to room temperature for 3 h, adhesion strength was measured when the asphalt sheet was completely detached from the concrete block using a universal material testing machine.
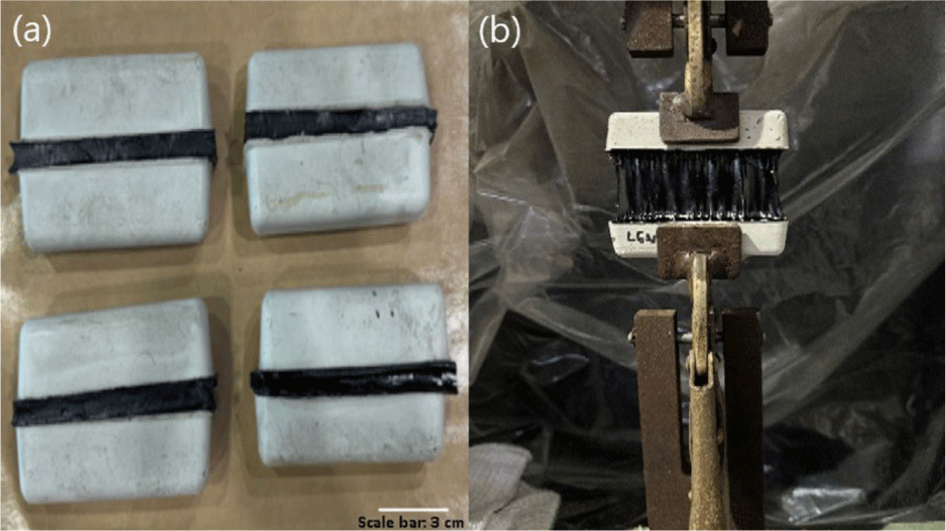
To measure the wet adhesion strength of the asphalt sheets, specimens were prepared in the same manner as in the adhesion strength test, and then they were stored in a water bath at 25°C for 3 h (Figure 4). The specimens were removed from the water bath immediately, and the wet adhesion strength was measured in the same manner as the adhesion strength while still sufficiently moist.
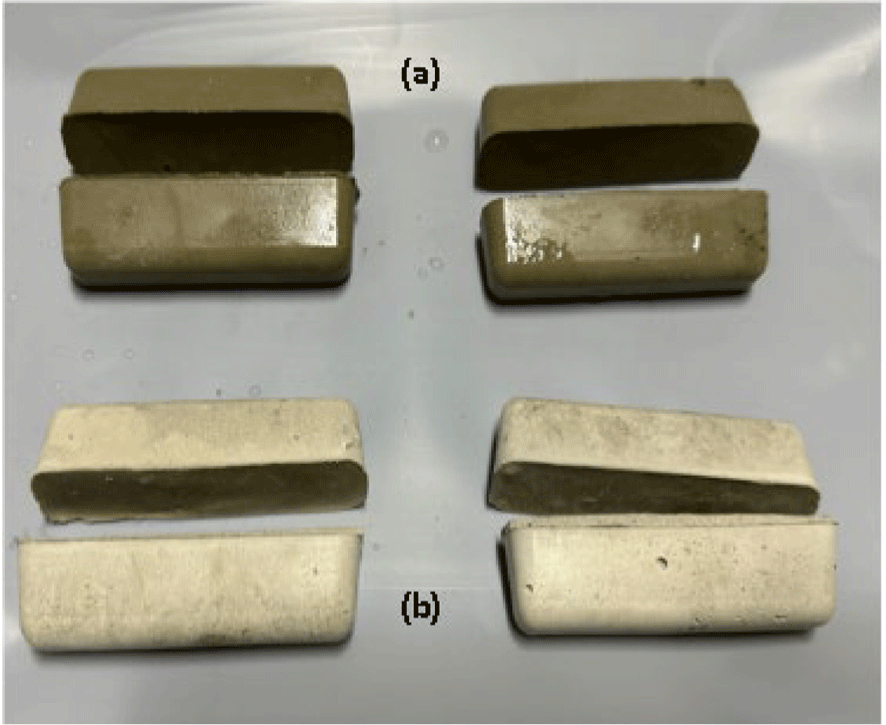
Results and Discussion
The structure of the LENR sample was confirmed using FT-IR spectroscopy. The FT-IR spectra and major peaks are shown in Figure 5, respectively. By comparing the peaks in the FT-IR spectra of LENR-1-5, we confirmed that the structures changed with the amounts of formic acid and hydrogen peroxide added during synthesis.
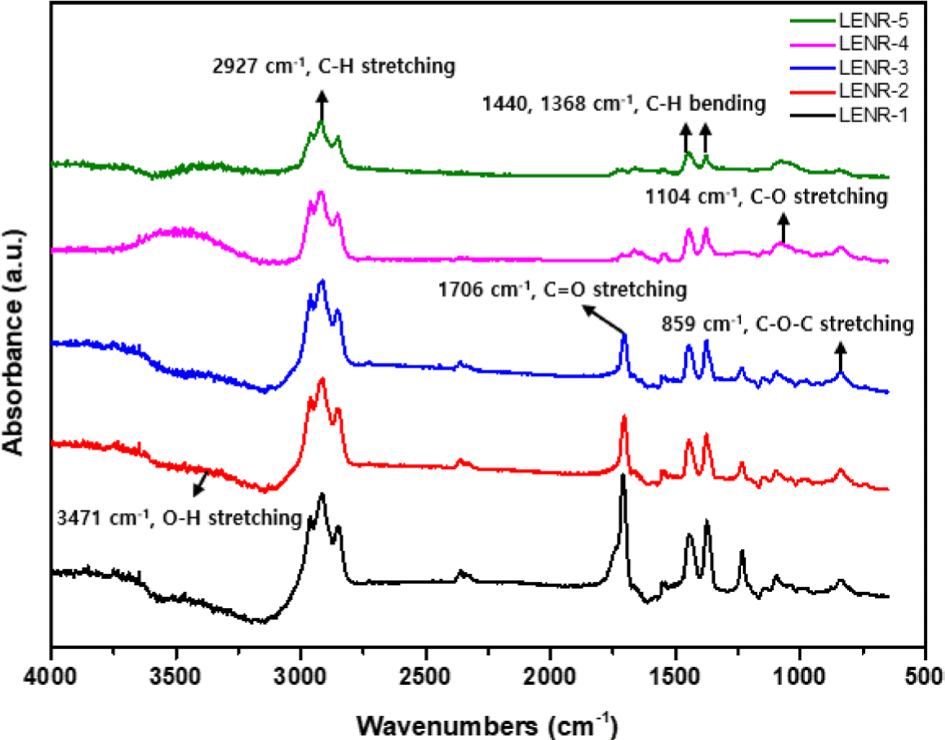
The C-H bending peaks of polyisoprene were observed at 1368 cm-1 and 1440 cm-1. The 1104 cm-1 peak corresponding to C-O stretching and the 859 cm-1 peak corresponding C-O-C stretching indicated an epoxy group structure, confirming that LENR-1-5 contain epoxy groups. In the spectra of LENR-1, 2, and 3, a peak appeared at 1706 cm-1, which corresponds to the C=O stretching vibration of the carbonyl group. In addition, in the spectra of LENR-4 and 5, a peak appeared at 3471 cm-1, which did not appear in the spectra of LENR-1, 2, and 3. This peak corresponds to the O-H stretching vibration of the hydroxyl group (-OH) (Figure 5). These spectral features indicate that LENR-1, 2, and 3, synthesized using less than 0.3 mol of formic acid (85 wt%) and 0.9 mol of hydrogen peroxide (34.5 wt%), possess carbonyl groups, while LENR-4 and 5, synthesized using more than 0.3 mol of formic acid (85 wt%) and 0.9 mol of hydrogen peroxide (34.5 wt%), possessed hydroxyl groups but no carbonyl groups.
These results may be due to the change in the pH of the NR caused by an increase in formic acid and hydrogen peroxide concentration. According to a previous study,16 when NR latex is depolymerized into a liquid state, different products are produced depending on the pH of the latex. In an alkaline medium with a pH of 9 or higher, hydrogen peroxide and sodium nitrite act as oxidizing agents that oxidize and decompose the NR molecular chains, and LENR with a carbonyl group at each molecular terminal is synthesized (Scheme 1).21 The mechanism shown in Scheme 2 is similar to the reaction pathway reported by Ravindran et al.22; at a pH of 6 or lower, NR was decomposed by OH radicals, producing LENR with a hydroxyl group at the terminus.


Figure 6 shows the 1H NMR spectra of LENR-1-5 synthesized using different amounts of hydrogen peroxide and formic acid. The chemical shifts in the 1H NMR spectra were measured in ppm using CDCl3 as the solvent. The signals at 1.65, 2.05, and 5.1 ppm correspond to the protons in the structural formula of NR, while those at 1.65, 2.05, and 5.1 ppm correspond to -CH3, -CH2-C=C, and -CH=CH-group protons, respectively. In addition, the peak at 2.7 ppm arises from the methine (-CH-) protons in the epoxy ring.
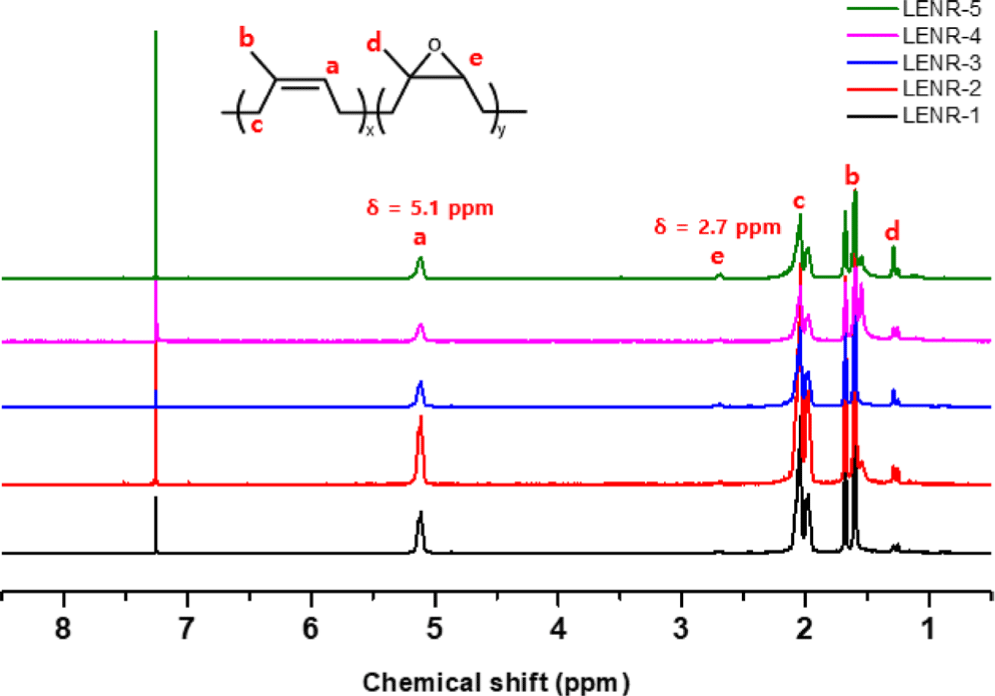
To confirm that the epoxy group content increases with the amount of hydrogen peroxide and formic acid added, we used the signal at δ = 2.7 ppm, which represents protons in the epoxy ring, and the signal at δ = 5.1 ppm, which corresponds to the protons in NR. The calculation is shown in Equation (1), and the results are given in Table 2.
As shown in Table 2, the epoxy group content varied with the amounts of hydrogen peroxide and formic acid used. The epoxy group content of LENR-1, synthesized using 0.45 mol hydrogen peroxide and 0.15 mol formic acid, was the lowest among the specimens (2.9%). As the amounts of hydrogen peroxide and formic acid increased, the epoxy group content gradually increased in proportion to the amount of hydrogen peroxide and formic acid used, to 3.8%, 7.4%, 9.9%, and 14.5% for LENR-2, 3, 4, and 5, respectively. The epoxy group content has been reported to increase as the pH of NR latex decreases during the epoxidation reaction.16 Our results show that the epoxy content increased as the amount of formic acid and hydrogen peroxide increased, and we assume that these two substances, which are acidic, lowered the pH of NR latex. These results are similar to those of previous studies.
The glass transition temperatures (Tg) of LENR-1-5 were measured and confirmed that the specimens were liquid rubbers that maintained fluidity at room temperature. The physical properties of rubber vary with temperature, and the Tg is the temperature at which rubber transforms from a hard solid into an elastic solid. Elasticity is an important property of rubber used as an asphalt modifier. In the case of asphalt mixtures incorporating rubber modifiers with high elasticity, physical properties such as adhesion performance and tensile strength tend to improve.23,24 Rubber, which is flexible and elastic at temperatures above its Tg, improves the shortcomings of asphalt, which is inelastic and brittle at room temperature. Because rubber hardens and loses elasticity at temperatures below its Tg, we expect that the lower the Tg, the better rubber’s modifying ability at room temperature. The Tg values of LENR-1-5, which were determined using DSC, are shown in Figure 7.
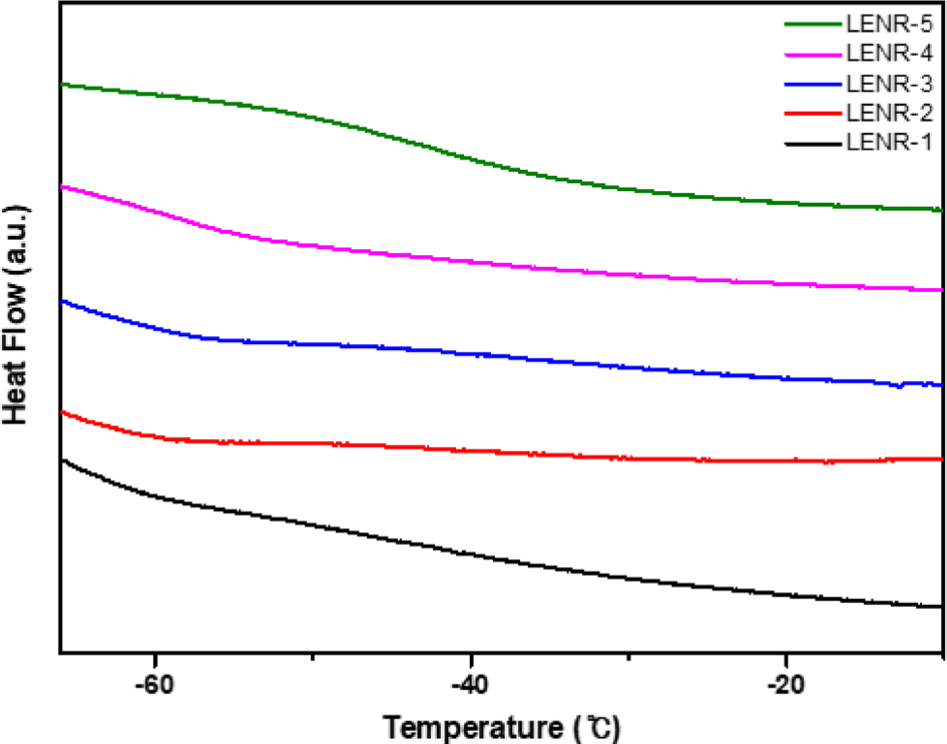
A study reported that rubber used as an asphalt modifier should have a Tg below -30°C to improve the low-temperature cracking of asphalt.25 The epoxidation reaction increases the Tg of NR. Normally, NR has a Tg below -65°C, and for epoxidized rubber synthesized from NR, the Tg increases to approximately -20°C, worsening its low-temperature characteristics26 and inhibiting its application as an asphalt modifier. LENR-1, 2, and 3 have Tg values of approximately -63 to 61°C, similar to that of NR; as the epoxy content increases, the Tg increases, and LENR-5 has a Tg of -43°C.
To determine the relationship between the epoxy group content and the molecular weights (MW) of LENR-1-5, which were synthesized via depolymerization using sodium nitrite after NR latex was epoxidized using formic acid and hydrogen peroxide, GPC MW measurements were performed. The epoxy rubber generated by the epoxidation reaction of NR was depolymerized using sodium nitrite to shorten each molecular chain, resulting in a decrease in MW. In the case of low-MW rubber, the molecular chain is short, so it generally has the advantages of good flexibility, processability, and improved dispersibility; however, the physical properties of low-MW polymers are compromised.27 The results of the GPC MW measurements for each LENR sample are shown in Table 3.
Liquid rubber | Epoxy contents (%) | Mw (×103) |
---|---|---|
LENR-1 | 2.91 | 11.2 |
LENR-2 | 3.84 | 13.2 |
LENR-3 | 7.4 | 13.5 |
LENR-4 | 9.9 | 107.7 |
LENR-5 | 14.5 | 113.4 |
NR, which is commonly used, has an MW of approximately 1.3 × 10628,29; the synthesized LENR samples had lower MW values than NR. The higher the epoxy content of the LENR, the higher the MW; LENR-5 had the highest epoxy content and MW. Therefore, the synthesized LENR-1-5 had lower MW values than NR, where the MW of the sample increased as the epoxy content increased.
Solid rubber modifiers, mainly used for asphalt modification, begin to disperse in asphalt at high temperatures (150-200°C).25 LENR is a fluid rubber modifier. To confirm that it can modify asphalt at lower temperatures than existing solid rubber modifiers, the viscosities of LENR-1-5 were measured at 70°C (Figure 8).
Viscosity varies with the amount of hydrogen peroxide and formic acid used in the synthesis of LENR. LENR-1, which was synthesized with the lowest amounts, correspondingly had the lowest viscosity, and LENR-5, which was synthesized with the highest amounts, had the highest viscosity. This may be related to the epoxy content and glass transition temperature during LENR synthesis. Hydrogen peroxide and formic acid induce the epoxidation of NR, where the epoxy content varies with the amounts used. According to previous 1H NMR and DSC results, the glass transition temperature increases as the epoxy content increases, which means that the interactions between the molecules of the rubber strengthen, and the fluidity may decrease.30,31 In addition, the lower the MW of the liquid rubber, the shorter the molecular chain, which increases flexibility, processability, and dispersibility.27 According to the GPC MW measurement results, the viscosity decreased as the MW of the LENR sample decreased, indicating that a liquid rubber sample with a lower MW should have higher dispersibility.
Tensile strength, which measures the stress until a sample piece breaks under a tensile load, is the most important factor in evaluating the physical properties of a material. The tensile strength depended on the epoxy group content of LENR and the LENR content used in the production of the asphalt sheets. Figure 9 shows the tensile strengths of the asphalt sheets (AS_LENR-1-5) manufactured by adding LENR-1-5 in different proportions.
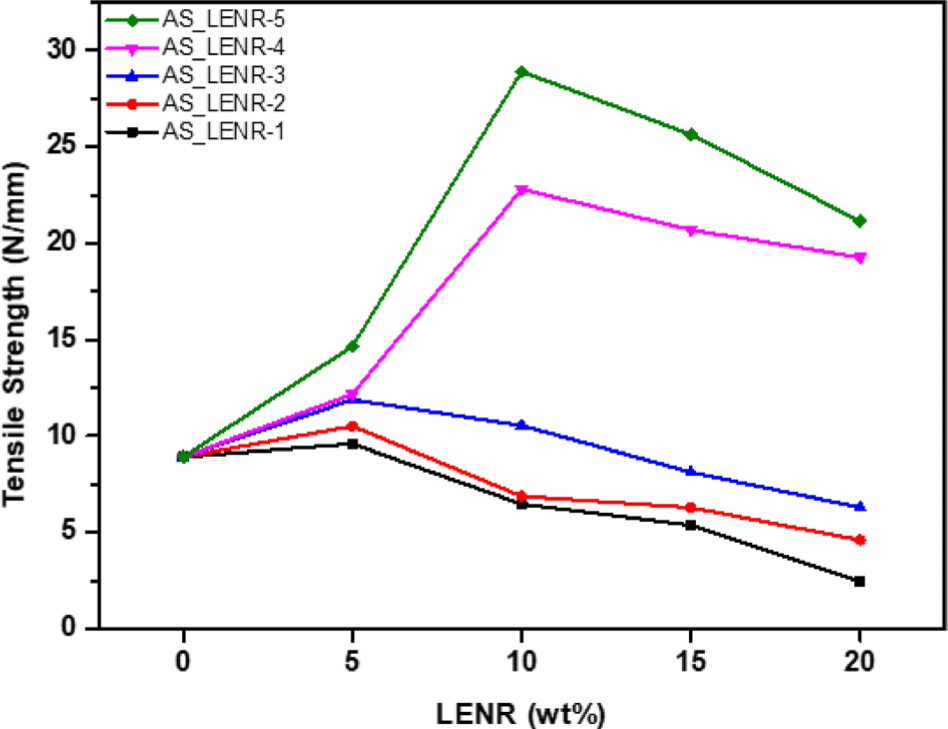
The tensile strength of all AS_LENR-1-5 was measured to be 8.92 N/mm at 0 wt%. For AS_LENR-1, as the LENR content increased by 5 wt% steps, the tensile strength values were observed to be 9.60 N/mm, 6.47 N/mm, 5.39 N/mm, and 2.45 N/mm, respectively. For AS_LENR-2, the tensile strength values were 10.52 N/mm, 6.89 N/mm, 6.30 N/ mm, and 4.61 N/mm, respectively, with 5 wt% step-by-step increased in LENR content. Similarly, AS_LENR-3 showed tensile strength values of 11.89 N/mm, 10.55 N/mm, 8.13 N/ mm, and 6.30 N/mm. For AS_LENR-4, the tensile strength values were 12.18 N/mm, 22.80 N/mm, 20.71 N/mm, and 19.27 N/mm. Lastly, for AS_LENR-5, the tensile strength values were recorded as 14.99 N/mm, 28.91 N/mm, 25.64 N/mm, and 21.14 N/mm, respectively. The tensile strengths of AS-LENR-1-3 increased up to 5 wt% of LENR-1-5 and then decreased when the LENR content exceeded 5 wt%. When 10 wt% or more LENR-1, 2, and 3 were added, the tensile strengths of AS-LENR-1-3 decreased compared with the modifier-free asphalt sheet solution. In addition, in the case of AS_LENR-4 and 5, the tensile strength increased when up to 10 wt% LENR-4 and 5 was added, and then decreased. However, for AS_LENR-4, 5, the tensile strength decreased when the LENR-4 and 5 contents ranged from 10 to 20 wt%, but the tensile strength was not lower than that of the modifier-free asphalt sheet solution. AS_LENR-5, to which LENR-5 containing 14.5% epoxy group content was added, had the highest tensile strength among all the content comparison groups, and AS_LENR-1, to which LENR-1 containing 2.91% epoxy group content was added, had the lowest tensile strength. These results indicate that adding polymers to asphalt improves its physical properties, such as elasticity, cohesion, rigidity, and adhesion.30 In the case of epoxy rubber, owing to its high Tg, the deformation resistance and strength of the asphalt sheet increase as Tg increases.32 Therefore, as the epoxy group content of LENR increased, the tensile strength increased. Adhesion strength generally refers to the strength of the force that causes two objects to stick together.33 In the case of asphalt sheets, which are mainly used in concrete materials for rooftops and walls, the adhesion strengths of the asphalt sheets (AS_LENR-1-5) manufactured by adding LENR-1-5 to concrete blocks were measured. In addition, because they are used as exterior concrete materials, they frequently come into contact with moisture, such as rain and snow. The wet adhesion strengths of AS_LENR-1-5, manufactured by adding LENR-1-5 to wet concrete blocks, were also measured. Figure 10 shows the adhesion strengths when the asphalt sheets and concrete blocks manufactured by adding LENR-1-5 were attached and completely removed. Figure 11 presents the wet adhesion strengths when the asphalt sheets and concrete blocks prepared by adding LENR-1-5 were attached and removed, respectively.
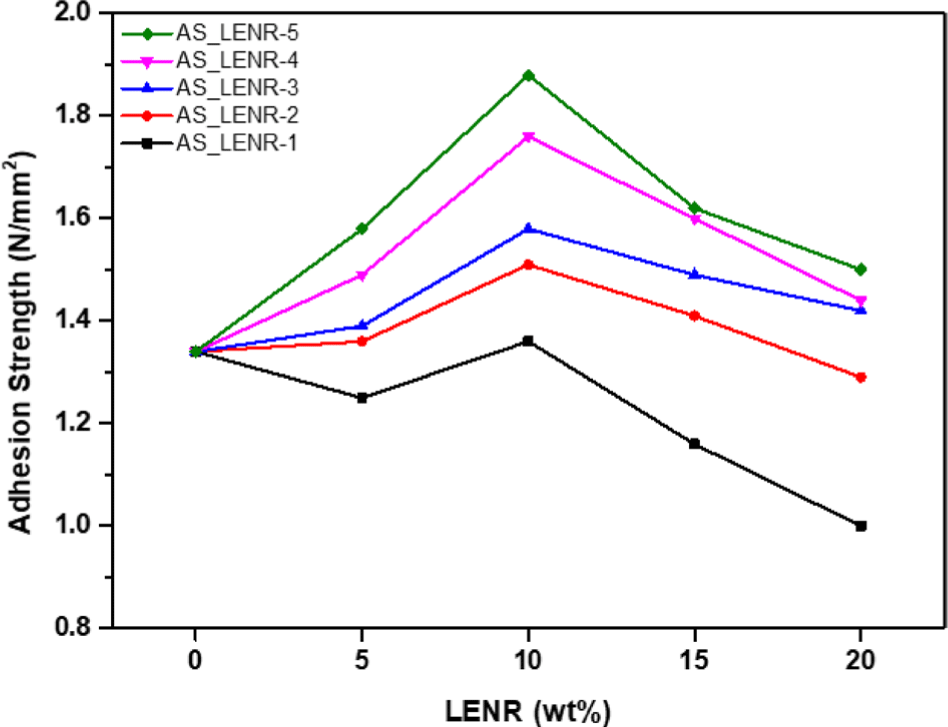
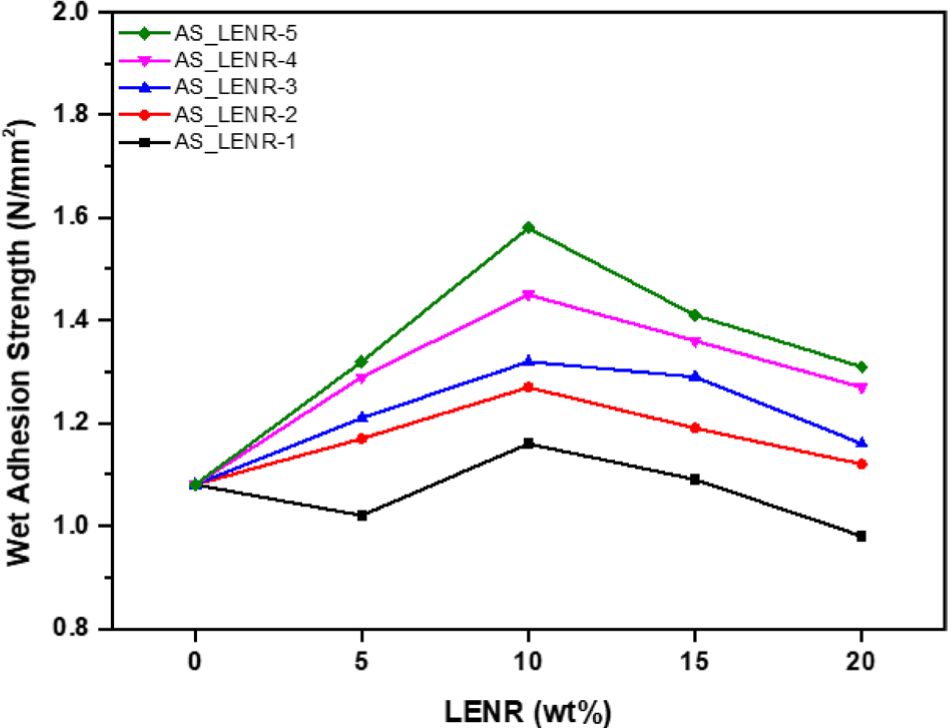
The adhesion strength of all AS_LENR-1-5 was measured to be 1.34 N/mm2 at 0 wt%. For AS_LENR-1, as the LENR content increased by 5 wt% steps, the tensile strength values were observed to be 1.25 N/mm2, 1.36 N/mm2, 1.16 N/mm2, and 1.00 N/mm2, respectively. For AS_LENR-2, the tensile strength values were 1.36 N/mm2, 1.51 N/mm2, 1.41 N/ mm2, and 1.29 N/mm2, respectively, with 5 wt% step-by-step increased in LENR content. Similarly, AS_LENR-3 showed tensile strength values of 1.39 N/mm2, 1.58 N/mm2, 1.49 N/ mm2, and 1.42 N/mm2. For AS_LENR-4, the tensile strength values were 1.49 N/mm2, 1.76 N/mm2, 1.60 N/mm2, and 1.44 N/mm2. Lastly, for AS_LENR-5, the tensile strength values were recorded as 1.58 N/mm2, 1.88 N/mm2, 1.62 N/mm2, and 1.50 N/mm2, respectively. AS_LENR-2-5, manufactured by adding LENR-1, had stronger adhesive strengths than the asphalt sheets without LENR-2-5; in particular, the highest adhesive strength was observed when the LENR content was 10 wt%. The adhesive strength gradually decreased from 15 wt%. In the case of AS_LENR-1, the highest adhesive strength was observed when the LENR-1 content was 10 wt%; otherwise, for all other LENR-1 contents, the same adhesive strength as the asphalt sheet without LENR-1 was observed.
The wet adhesion strength of all AS_LENR-1-5 was measured to be 1.08 N/mm2 at 0 wt%. For AS_LENR-1, as the LENR content increased by 5 wt% steps, the tensile strength values were observed to be 1.02 N/mm2, 1.16 N/ mm2, 1.09 N/mm2, and 0.98 N/mm2, respectively. For AS_ LENR-2, the tensile strength values were 1.17 N/mm2, 1.27 N/mm2, 1.19 N/mm2, and 1.12 N/mm2, respectively, with 5 wt% step-by-step increased in LENR content. Similarly, AS_LENR-3 showed tensile strength values of 1.21 N/mm2, 1.32 N/mm2, 1.29 N/mm2, and 1.16 N/mm2. For AS_LENR-4, the tensile strength values were 1.29 N/mm2, 1.45 N/mm2, 1.36 N/mm2, and 1.27 N/mm2. Lastly, for AS_LENR-5, the tensile strength values were recorded as 1.32 N/mm2, 1.58 N/mm2, 1.41 N/mm2, and 1.31 N/mm2, respectively. For AS_LENR-2-5, the wet adhesion strengths increased for all concentrations of LENR relative to the same containing 0 wt% LENR. However, the wet adhesion strength of AS_ LENR-1 decreased relative to the 0 wt% LENR sample for the other LENR-1 contents, except for 10 and 15 wt%. AS_LENR-1-5 showed the highest wet adhesion strengths at 10 wt% LENR addition and decreased again at contents exceeding 10 wt%. All the AS_LENR samples possessed the highest adhesion and wet adhesion strengths when the LENR content was 10 wt%. This is because when 7-9 wt% asphalt modifier is added, the resistance to permanent deformation and fatigue resistance of the asphalt mixture increases.34 In addition, epoxy rubber improves the physical properties of the mixture, such as adhesiveness and storage modulus,35-37 and it is known that asphalt modified by epoxidized NR has a higher viscosity and elasticity.38-40 The higher the epoxy group content of LENR-1-5, the higher the adhesion and wet adhesion strengths of the asphalt sheets, where the highest values were observed for the 10 wt% LENR samples.
Conclusions
In this study, LENR was synthesized and used as an asphalt modifier, and changes in the physical properties of asphalt sheets modified by LENR were evaluated. LENR was mixed at a temperature lower than the processing temperature of existing solid rubber modifiers, thereby improving the physical performance of the asphalt sheets. The tensile strength, adhesion strength, and wet adhesion strength of the asphalt sheets were found to improve as the epoxy group content increased, as observed from the enhanced physical properties of AS_LENR-1 to AS_LENR-5. Furthermore, when comparing the physical properties based on the variation in LENR content, the highest performance was achieved at an LENR content of 10 wt%. This suggests that using 10 wt% LENR is the most suitable for optimizing the physical properties of asphalt sheets. These results indicate that, compared with existing asphalt modifiers, LENR is better at improving the physical performance of asphalt sheets as well as the process efficiency. These results indicate that LENR can be applied in road pavements, building materials containing asphalt, and asphalt sheets. In future studies, the commercial application potential of LENR as an asphalt modifier will be investigated, along with research on various additives and addition ratios.